With the continuous development of the power industry, there are many types of relay protection testers currently used in China. However, since the performance of the relay protection tester itself directly affects the value of the relay protection device, the working performance and stability of the tester are particularly important. Although DL/T*-1997 "Technical Conditions for Relay Protection Microcomputer Test Devices" puts forward clear requirements for relay protection test devices and stipulates regular inspection cycles and inspection items, there are no relevant inspection procedures or specifications, and there are no ready-made inspection devices. This has brought certain difficulties to the acceptance and weekly inspection of relay protection testers. Therefore, such a data acquisition device is needed to accurately collect various data of the relay protection tester so that the host computer can analyze the data and calibrate the relay protection tester.
1. System design
The data acquisition device designed in this paper is specially used for the data collection of relay protection test instruments. The design uses DSP as the core controller of the data acquisition device. The overall structure of the system hardware is shown in Figure 1. The system consists of voltage and current sampling circuits, signal amplification, low-pass filtering, synchronous signal acquisition and recognition, DC sampling, analog/digital conversion circuits, and communication module circuits.
In this scheme, the data selector uses the AD7502 chip produced by AD. The AD7502 chip is a dual four-to-one data selector, so two A/D converters are required for cyclic sampling. The analog/digital conversion chip uses the 16-bit parallel high-speed converter ADS8515 launched by TI. The main control chip uses TI's digital signal processor TMS320F2812. TMS320F2812 is a 32-bit fixed-point high-speed digital processor with a maximum operating frequency of 150 MHz. The chip adopts an improved Harvard structure and has six independent parallel data and address buses on the chip, which greatly improves the data throughput of the system. The combination of 32-bit accumulator, 16-bit hardware multiplier and input and output data shift registers can quickly complete complex numerical operations. Therefore, the calculation speed of TMS320F2812 is very high, which can meet the online real-time requirements of the system.
When communicating with the host computer, this solution uses USB bus technology based on various factors. The USB interface chip is ISP1581 from Philips. ISP1581 is a cost-effective USB 2.0 interface chip launched by Philips. It fully complies with the USB 2.0 specification and supports 7 IN endpoints, 7 OUT endpoints and one fixed control IN/OUT endpoint. ISP1581 supports the self-test working mode of USB 2.0 and the return working mode of USB 1.1, and can operate normally under high-speed or full-speed conditions. ISP1581 integrates a serial interface engine (SIE), PIE, 8 KB FIFO memory, data transceiver, PLL's 12 MHz crystal oscillator and 3.3 V voltage regulator. The communication between ISP1581 and the external microcontroller is mainly achieved through a high-speed universal parallel interface. It has two modes of connection with the microcontroller: disconnect bus mode and general processor working mode. In the disconnected bus mode, AD[7:0] is a multiplexed 8-bit address/data bus, and DATA[15:0] is a separate DMA data bus; in the general processor working mode, AD[7:0] is a separate 8-bit address line, and DATA[15:0] is a 16-bit controller data bus. At this time, DMA will be multiplexed to the data bus of the DATA[15:0] controller. In the hardware design of this device, the circuit is designed as a general processor mode.
2 System Hardware Design
2.1 Voltage and current sampling circuit design
This system collects three-phase voltage, three-phase current and two voltage and current signals of the neutral line. The sampling circuits of voltage and current are similar. The voltage uses a voltage transformer and the current uses a current transformer. The voltage and current sampling circuits are composed of the operational amplifier OPA2277. The voltage acquisition circuit is shown in Figure 2. In Figure 2, T1 is a voltage transformer. The signal from the voltage transformer is processed by OPA2277 and then sent to the S1 input pin of the data selector AD7502. The other 7 voltage and current signals are sent to the other 7 input pins of AD7502 respectively.
2.2 Design of program-controlled filter circuit
The data selector AD7502 is used as the analog switch for four voltage and four current signals in the system. The filter circuit is implemented by OPA2277, and the circuit schematic is shown in Figure 3. Among them, A0 and A1 of AD7502 are connected to GPIOB4 and GPIOB5 of DSP general I/O port, and EN pin is connected to high level. GPIOB4 and GPIOB5 output different values to control the connection of different channels of AD7502, so that 8 signals are sent to two A/D converters in turn.
2.3 Design of A/D conversion circuit and DSP interface circuit
The A/D converter is the core device in the analog/digital conversion circuit and plays an important role in the entire measurement system. If the number of bits of the analog/digital converter is low, it will cause a large measurement error. This device uses the A/D chip ADS8515 of Texas Instruments (TI) as the analog/digital converter. The ADS8515 is a 16-bit parallel A/D converter with a sampling rate of 250 KSPS and an input voltage range of ±10 V. The ADS8515 belongs to the successive approximation register type (SAR type for short) A/D converter. This type of converter outputs a digital signal by comparing the input analog signal with the comparator successively. It is the most widely used type of converter at present. The SAR type A/D converter has relatively low power consumption and a relatively small size. In addition, the A/D usually has a sample-and-hold device inside, which can maintain the sampling voltage until the conversion is completed, and its conversion rate is very fast. The interface circuit of ADS8515 and DSP is shown in Figure 4.
Since the I/O voltage of TMS320F2812 is 3.3 V, while the ADC is 5 V, the level conversion chip 74LVC245 is needed to realize the isolation function. The control of ADS8515 is realized by querying the chip select signal CS, the start signal R/C and the status signal BUSY. BUSY, CS, R/C are connected to the interrupt signal pin XINT1 of DSP and the general I/O interface GPIOB0 and GPIOB1 respectively. In order to ensure the synchronous sampling of the dual DSPs and prevent the crosstalk of the two DSP data during data output, the chip select signal CS and the start signal R/C of the other DSP are connected to the general I/O interface GPIOB2 and GPIOB3 of DSP respectively. In this way, the synchronous sampling of the dual DSPs can be ensured, and the data in the two A/Ds can be read in sequence.
2.4 Synchronous signal acquisition and recognition circuit design
In order to realize the AC synchronous sampling of the A/D converter, the design circuit of this scheme is shown in Figure 5. The scheme uses multiple OPA2277 and comparator MAX998 to form a signal acquisition and recognition circuit, thereby overcoming the frequency leakage error caused by non-integer cycle sampling and realizing strict synchronous sampling and equal interval sampling. In Figure 5, K3C is a relay, which is used as a switch to switch on and off the selected AC voltage signal and AC current signal. OPA2277 forms an amplification and filtering circuit. The role of diodes D2 and D3 is to protect the comparator MAX998 to prevent the voltage from being too large and breaking down the MAX998.
2.5 DSP System Design
The DSP system is mainly composed of DSP chip, power supply circuit, clock circuit, simulation and test circuit. Since the power supply system of TMS320F2812 has both 3.3 V digital and analog power supply and 1.8 V digital power supply, the safety and reliability of the power supply are the fundamental guarantee for the operation of the system, so it is necessary to convert the commonly used 5 V power supply into 3.3 V and 1.8 V power supply. This design uses TI's TPS767D318 as the power supply chip. This chip is specially designed for DSP applications and can provide 3.3 V and 1.8 V two-way voltage output, each of which can provide a maximum current of 1 A. TPS767D318 also has a voltage monitoring function. The design of the power supply circuit is shown in Figure 6. In addition, each power supply and ground pin of the DSP cannot be left floating, and the digital and analog grounds must be designed separately.
Since the system is sensitive to timing requirements, the clock circuit of this system uses an external active crystal oscillator with a working voltage of 3.3 V. The active crystal oscillator has better signal quality than the passive crystal oscillator, is more stable, and has a relatively simple connection method. The usual usage is: one pin is suspended, two pins are grounded, three pins are connected to output, and four pins are connected to voltage.
When hardware emulation is performed on the DSP system, the data memory, program memory and control registers inside the DSP can be monitored online through the JTAG boundary scan interface, and the program can be downloaded to the DSP chip for hardware emulation in the TMS320F2812 development environment CCS. The schematic diagram of the JTAG interface is shown in Figure 7.
2.6 Communication module design
At present, data acquisition systems mostly use ISA, EISA or PCI cards to complete data transmission. These methods have the disadvantages of difficult development and debugging, troublesome installation, poor versatility and portability, etc. In addition, the number of slots, addresses, and terminal resources on the PC are limited, resulting in poor scalability of this method. At present, the widely used USB bus interface has the advantages of easy installation, high bandwidth, and easy expansion, and has become the mainstream of computer interfaces. This paper selects a dedicated USB interface chip to complete the data transmission between DSP and PC. The USB 2.0 chip uses Philips' ISP1581. The connection circuit diagram of ISP1581 and TMS320F2812 is shown in Figure 8. When ISP1581 is powered on, the interface is set through BUS_CONF, MODE0, and MODE1. In this design, BUS CONF is connected to a high level through a resistor. ISP1581 works in general processor mode, AD[0~7] is an 8-bit address bus, and DATA[0~15] is an independent data bus. MODE0 is set to 1, so the read and write selection signal is of 8051 type. XCS0AND1 of TMS320F2812 is used as the chip select signal of ISP1581. The RREF pin is grounded through a 12 kΩ precision resistor to provide accurate mirror current. The RPU pin is pulled up through a 1.5 kΩ resistor.
3 Conclusion
A signal acquisition device for relay protection tester based on DSP technology is developed to verify whether the performance indicators of relay protection tester meet the design requirements. This paper focuses on the overall architecture of the data acquisition device, the hardware composition and circuit design of the data acquisition device based on DSP. The data acquisition device can accurately collect various data of the relay protection tester, laying a technical foundation for the verification device of the relay protection tester.
Previous article:Using MSGQ modules to simplify complex DSP applications
Next article:Design and implementation of a smart jamming platform based on FPGA/DSP
Recommended ReadingLatest update time:2024-11-16 22:50
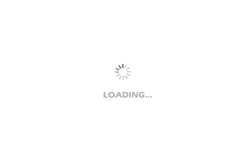
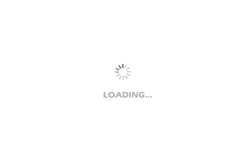
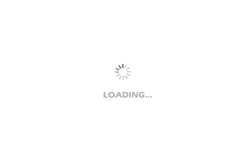
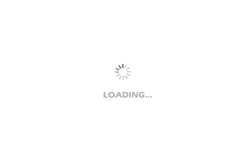
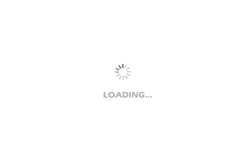
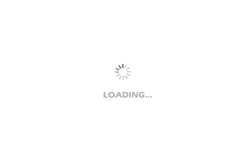
- Popular Resources
- Popular amplifiers
- Huawei's Strategic Department Director Gai Gang: The cumulative installed base of open source Euler operating system exceeds 10 million sets
- Analysis of the application of several common contact parts in high-voltage connectors of new energy vehicles
- Wiring harness durability test and contact voltage drop test method
- Sn-doped CuO nanostructure-based ethanol gas sensor for real-time drunk driving detection in vehicles
- Design considerations for automotive battery wiring harness
- Do you know all the various motors commonly used in automotive electronics?
- What are the functions of the Internet of Vehicles? What are the uses and benefits of the Internet of Vehicles?
- Power Inverter - A critical safety system for electric vehicles
- Analysis of the information security mechanism of AUTOSAR, the automotive embedded software framework
Professor at Beihang University, dedicated to promoting microcontrollers and embedded systems for over 20 years.
- Innolux's intelligent steer-by-wire solution makes cars smarter and safer
- 8051 MCU - Parity Check
- How to efficiently balance the sensitivity of tactile sensing interfaces
- What should I do if the servo motor shakes? What causes the servo motor to shake quickly?
- 【Brushless Motor】Analysis of three-phase BLDC motor and sharing of two popular development boards
- Midea Industrial Technology's subsidiaries Clou Electronics and Hekang New Energy jointly appeared at the Munich Battery Energy Storage Exhibition and Solar Energy Exhibition
- Guoxin Sichen | Application of ferroelectric memory PB85RS2MC in power battery management, with a capacity of 2M
- Analysis of common faults of frequency converter
- In a head-on competition with Qualcomm, what kind of cockpit products has Intel come up with?
- Dalian Rongke's all-vanadium liquid flow battery energy storage equipment industrialization project has entered the sprint stage before production
- Allegro MicroSystems Introduces Advanced Magnetic and Inductive Position Sensing Solutions at Electronica 2024
- Car key in the left hand, liveness detection radar in the right hand, UWB is imperative for cars!
- After a decade of rapid development, domestic CIS has entered the market
- Aegis Dagger Battery + Thor EM-i Super Hybrid, Geely New Energy has thrown out two "king bombs"
- A brief discussion on functional safety - fault, error, and failure
- In the smart car 2.0 cycle, these core industry chains are facing major opportunities!
- The United States and Japan are developing new batteries. CATL faces challenges? How should China's new energy battery industry respond?
- Murata launches high-precision 6-axis inertial sensor for automobiles
- Ford patents pre-charge alarm to help save costs and respond to emergencies
- New real-time microcontroller system from Texas Instruments enables smarter processing in automotive and industrial applications
- STM32F10x stepper motor encoder position control CANWeb source program
- MSP430F249_TimerA timer
- Synthesizable Verilog Syntax (Cambridge University, photocopy)
- [RVB2601 Creative Application Development] Short recording, playback and printing of recording data
- When the carrier data reaches the receiving end, how does the receiving end identify this information?
- SparkRoad Review (7) - FPGA Serial Port Test
- Disable AD auto-start JLink
- Seeking guidance - stc microcontroller remote upgrade program
- Problems with creating sheet symbols for multi-page schematics
- Zigbee Z-Stack 3.0.1 Modify channels using broadcasting