Recent progress in developing high-efficiency, low-consumption LEDs has made this lighting source a technical option in the design of automotive interior lighting systems. This article will introduce the specific details of the various driver structures and topologies used in automotive interior lighting LEDs and discuss thermal management issues.
LEDs are being used in many automotive lighting systems. LEDs are suitable for interior lighting because of their small size and high efficiency. Therefore, recent progress in the development of high-efficiency, low-consumption LEDs has made this lighting source a technical choice when designing automotive interior lighting systems. However, driving these devices to achieve optimal performance is an art.
LEDs require a specific operating current, a method and accuracy to adjust the LED forward current within a standard width range, a vehicle battery pack and charging system, and a series limiting resistor.
The innovative use of standard N-channel depletion transistors (JFETs) can achieve better results than using resistors when regulating the operating current of LEDs. JFETs can be regarded as voltage-controlled resistors. By simply adjusting the gate-source voltage, the source can provide a relatively stable current, which acts as a current source for the series LED. When the drain voltage is connected to an unregulated switching battery, a relatively stable current can be provided. Compared with standard resistors, the use of JFETs can provide higher efficiency.
LED interior lighting can be applied to: instrument panel backlight; console backlight; ceiling light; convenient light source; RGB tone light source.
Special attention should be paid to circuit topology, driver current requirements and thermal management. The circuit shown in Figure 1 is involved in almost all automotive LED light source applications. If the LED current is less than 100mA (most interior lighting applications are backlight or switch lighting, the current is generally 30mA), the resistor value can be calculated from the forward voltage (Vfwd) across the LED in series. When using a special supply voltage such as 13.5 V, the resistor value is determined as follows:
Vsupply - Vsw_bat - Vrpp -I_led*R1 - 2 Vfwd=0 V
Vsw_bat = 0 V
Vsupply = 13.5 V (typical)
Vrpp = 0.8 V
Vfwd = 3.5 V
I_led = 30mA
R1 = 13.5 - 0.8 - 2*(3.5) = 190 Ω/30
The method of adjusting the LED current by a dedicated resistor is well known, and the worst-case Vfwd voltage drop of the LED can be solved by selecting a resistor with a certain resistance range as compensation. However, the LED current changes when the supply voltage changes between 9V and 18V. Re-adjusting the formula under the same 190Ω resistor and 9V voltage, the I_led value becomes 6.3mA. Assuming all parameters remain unchanged, the I-led value is 53mA when the supply voltage rises to 18V.
Instrument panels usually need backlighting so that the driver can see the instrument panel and pointers clearly in low light conditions. First of all, the ability to adjust the brightness is the most important - it can provide a brightness adjustment ratio of 100:1. In addition, in order to facilitate the driver to understand the status of the car, some indicator lights also need backlighting, such as airbag inspection, power system status, fluid level, etc. In general, up to 30 LEDs can be used at the same time.
The LED connection in Figure 1 is extended to 6 parallel connections, and the transistor provides pulse width modulation (PWM) light adjustment function at the low voltage end. The previously calculated resistor value is used to adjust the forward current of the LED, so the total current is determined by the number of parallel branches of the LED under the condition of a given power supply voltage. Similarly, the supply voltage changes between 9V and 18V, and the LED current also changes accordingly. In practical applications, when the supply voltage is 9V, the LED must emit a high enough brightness so that the driver can correctly read the instrument panel reading. At 18V, the heating problem of the printed circuit board (PCB) will become prominent, which requires us to consider the worst-case situation caused by this. The LED conduction voltage used in the backlight depends on the color. The conduction voltage of red, orange, green and light yellow LEDs is 2.4V, and the blue and white LEDs can be as high as 3.8V. If the conduction voltage of the first two LEDs in the series connection is 2.4V, then congratulations, you can still connect another LED in series. In other words, if we use a standard white light in a group of LEDs, the number of LEDs on this branch is limited to two. If the battery polarity is reversed during vehicle maintenance, a reverse polarity voltage of up to -15V can be generated, and a reverse polarity protection diode is required. The reverse voltage rating of LEDs is generally -5V, so in the case of reverse polarity, we need a blocking diode to protect the LED.
There is a way to adjust the brightness of LEDs by controlling the voltage at the low voltage end of the circuit. The host can control the LEDs through bias resistors, transistors or digital transistors (such as the MMUN2211 series) as a simple interface. The transistor has integrated Rb and Rbe resistors, so using a logic level signal is sufficient to drive a basic emitter circuit. By using such a transistor and controlling the duty cycle of PWM at a single frequency, a wide brightness adjustment range can be provided for the LEDs in the circuit.
Not only LED driving, but also many circuit applications require low-cost solid-state current regulators. Therefore, a solid-state current regulator should include the following factors: low cost; maintain current stability in a wide range of on-state voltage; small voltage drop when running at low on-state voltage; power limitation when the on-state voltage is too high; provide an ideal two-terminal current source for parallel applications; provide high-frequency PWM control for LED brightness adjustment; have anti-magnetization characteristics for directly introduced RF energy; and have a high level of electrostatic anti-interference ability.
Replacing the 190 ohm resistor in the circuit of Figure 1 with a depletion-type N-channel field effect transistor will result in the circuit shown in Figure 3. Simply shorting the gate and source, and biasing the drain and source with a voltage above 1 V, can generate an LED drive current. It is worth mentioning that in the process of using JFET instead of resistor to adjust the LED forward current, when the drain-source voltage increases (battery voltage changes), the current can still remain relatively stable. Figure 4 shows the steady-state current characteristics of JFET. Within the normal working range of the supply voltage, this characteristic can be deeply understood by measuring the JFET's volt-ampere characteristic curve.
As shown in Figure 4, the JFET volt-ampere characteristic curve is first in the linear region, where the current through the JFET increases linearly as the voltage drop between the drain and source increases. The voltage range in this region is relatively narrow (greater than the LED forward voltage drop and less than 1.5V). We can compare the difference in the LED current in Figure 1 and Figure 3 under the same 9V power supply input. In the circuit of Figure 1, the reverse polarity diode voltage drop is 0.8V, leaving a 1.2V voltage for the 190 ohm resistor, and the LED current is 6.3 mA. In the circuit of Figure 3, the JFET voltage drop is 1.2V, which makes the LED current become 21mA. Therefore, we can see that under lower line voltage conditions, the LED current provided by the JFET bias method is about 3.5 times that of the power supply method in Figure 1. This is similar to the control of the sag voltage in a linear regulator. This lower dropout voltage characteristic can provide a larger current and lighting brightness for the LED when the car battery is low.
The next region in Figure 4 is the constant current region, which has a voltage range of 1.5 V (LED on voltage) to about 6 V (Vbattery is 9.2 V to 14.5 V). This constant current region defines the size of the JFET saturation drain current Idss. By shorting the gate to the source, Idss in this region becomes a constant current source current, and this constant current value can be selected as needed.
In Figure 1, the LED current is determined by a voltage value (13.5 V). If this voltage value does not change, the LED current will also be constant. But what happens if this voltage value changes? There is more than one supply voltage bias point in the JFET constant current region. Immediately after the linear region, as the voltage drop of the JFET increases, the JFET drain current basically enters a pinch-off state, and the rate of change of the current also decreases suddenly (the instantaneous slope or admittance of the current curve decreases). Therefore, the JFET can provide a fairly reliable constant current over a wide range of battery voltage changes (9.5 V to 14.5 V).
Compared with resistors, using the constant current region of JFET to generate constant current can achieve better results. The on-state voltage of the LED manufactured for a single bias current follows a normal distribution. When the power supply voltage is 13.5 V, in order to keep the output current at 30mA, the voltage drop caused by the deviation of the LED on-state voltage must be solved. At this time, if you want to use the LED normally according to the circuit in Figure 1, you may need to insert a large number of resistors to compensate for the different forward voltages of different LEDs in the circuit. It seems that buying LEDs that cover all on-state voltage ranges (classified according to different on-state voltages) will help reduce costs, but ironically, this forces users to stock an equal number of resistors with different resistance values. As an alternative, if the circuit shown in Figure 5C is used, the constant current source or JFET will be able to ignore the on-state voltage of the LED and directly provide a stable current of a certain value.
Previous article:Challenges and solutions for power electronics in hybrid vehicle systems
Next article:Cooling solutions for automotive motor drive power modules
Recommended ReadingLatest update time:2024-11-16 14:35
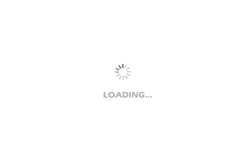
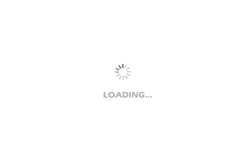
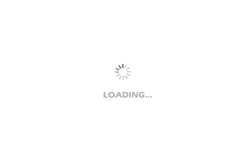
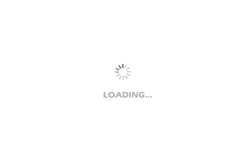
- Popular Resources
- Popular amplifiers
- Huawei's Strategic Department Director Gai Gang: The cumulative installed base of open source Euler operating system exceeds 10 million sets
- Analysis of the application of several common contact parts in high-voltage connectors of new energy vehicles
- Wiring harness durability test and contact voltage drop test method
- Sn-doped CuO nanostructure-based ethanol gas sensor for real-time drunk driving detection in vehicles
- Design considerations for automotive battery wiring harness
- Do you know all the various motors commonly used in automotive electronics?
- What are the functions of the Internet of Vehicles? What are the uses and benefits of the Internet of Vehicles?
- Power Inverter - A critical safety system for electric vehicles
- Analysis of the information security mechanism of AUTOSAR, the automotive embedded software framework
Professor at Beihang University, dedicated to promoting microcontrollers and embedded systems for over 20 years.
- Innolux's intelligent steer-by-wire solution makes cars smarter and safer
- 8051 MCU - Parity Check
- How to efficiently balance the sensitivity of tactile sensing interfaces
- What should I do if the servo motor shakes? What causes the servo motor to shake quickly?
- 【Brushless Motor】Analysis of three-phase BLDC motor and sharing of two popular development boards
- Midea Industrial Technology's subsidiaries Clou Electronics and Hekang New Energy jointly appeared at the Munich Battery Energy Storage Exhibition and Solar Energy Exhibition
- Guoxin Sichen | Application of ferroelectric memory PB85RS2MC in power battery management, with a capacity of 2M
- Analysis of common faults of frequency converter
- In a head-on competition with Qualcomm, what kind of cockpit products has Intel come up with?
- Dalian Rongke's all-vanadium liquid flow battery energy storage equipment industrialization project has entered the sprint stage before production
- Allegro MicroSystems Introduces Advanced Magnetic and Inductive Position Sensing Solutions at Electronica 2024
- Car key in the left hand, liveness detection radar in the right hand, UWB is imperative for cars!
- After a decade of rapid development, domestic CIS has entered the market
- Aegis Dagger Battery + Thor EM-i Super Hybrid, Geely New Energy has thrown out two "king bombs"
- A brief discussion on functional safety - fault, error, and failure
- In the smart car 2.0 cycle, these core industry chains are facing major opportunities!
- The United States and Japan are developing new batteries. CATL faces challenges? How should China's new energy battery industry respond?
- Murata launches high-precision 6-axis inertial sensor for automobiles
- Ford patents pre-charge alarm to help save costs and respond to emergencies
- New real-time microcontroller system from Texas Instruments enables smarter processing in automotive and industrial applications
- How to protect the microcontroller from read and write
- Has anyone used the SKY1311T card reader chip?
- The most powerful TI Bluetooth 5.0 solution CC2652R chip module
- [Help] What kind of software is this that can implement this host computer monitoring system?
- How to make the CLK of tms320c6678 SPI output 8 clock cycles each time
- What is the effect of connecting the SW pin of the switching power supply to the capacitor and resistor in series to GND?
- EEWORLD University ----TI LED Driver
- Doorbell program + circuit made by AVR microcontroller timer
- AR1021X series WiFi module selection reference and driver discussion in the field of wireless image transmission
- 2812 TxPR register write failure caused by TxCON highest bit