Since the servo system serves many purposes, such as computer CD drive control, radar tracking system, feed tracking system, etc., the requirements for the servo system are also different. The technical requirements for the servo system in engineering are very specific and can be summarized into the following aspects:
⒈ Requirements for the steady-state performance of the system;
⒉ Requirements for the dynamic performance of the servo system;
3. Requirements for system working environment conditions;
⒋ Requirements on system manufacturing cost, operating economy, degree of standardization, energy conditions, etc.
Although the requirements of servo systems vary due to the different moving parts, detection parts and mechanical structures of the service objects, the common point of all servo systems is to drive the controlled objects to perform mechanical movements according to the specified rules. From the perspective of automatic control theory, servo control systems generally include five parts: controller, controlled object, execution link, detection link and comparison link.
The block diagram of the servo system composition is shown in Figure 1.1.
Servo system composition (from top to bottom)
Controller: PLC, inverter, motion control card and other control devices, also called host computer;
The controller adjusts the control quantity according to the difference between the given value of the numerical control system and the actual operating value detected by the feedback device.
Servo drive: communicates between the host computer and the servo motor, and its function is similar to that of a frequency converter on an ordinary AC motor.
The power drive device is the main circuit of the system. On the one hand, it applies the electric energy in the power grid to the motor according to the size of the control quantity to adjust the size of the motor torque. On the other hand, it converts the constant voltage and frequency power supply of the power grid into the AC or DC power required by the motor according to the requirements of the motor.
Servo motor: an actuator that receives control signals from the driver;
The electric motor drives the machine to operate according to the power supply.
Mechanical equipment: convert the circular motion of the servo motor (or the linear motion of the linear motor) into the required motion form;
Various sensors and relays: detect various signals in industrial control environments and send them to the host computer or driver as the judgment standard for certain actions.
A servo system is an automatic control system that uses a certain component (such as a joystick) to make the system state reach or approach a predetermined value, and can compare the desired state (required value) with the actual state, and adjust the control component according to the difference between them (sometimes the rate of change of the difference).
Main Function
1. Use low-power command signals to control high-power loads;
2. In the absence of mechanical connection, the input shaft controls the output shaft located far away to achieve long-distance synchronous transmission;
3. Make the output mechanical displacement accurately track the electrical signal, such as recording and indicating instruments.
Previous article:A Prequel to China's Commercial Spaceflight
Next article:Differences between the three control modes of servo control
Recommended ReadingLatest update time:2024-11-16 11:27
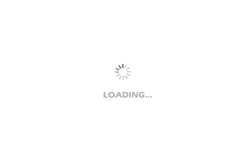
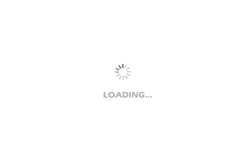
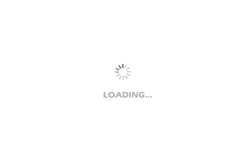
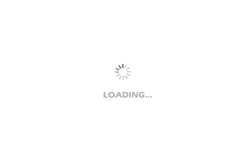
- Popular Resources
- Popular amplifiers
- Huawei's Strategic Department Director Gai Gang: The cumulative installed base of open source Euler operating system exceeds 10 million sets
- Analysis of the application of several common contact parts in high-voltage connectors of new energy vehicles
- Wiring harness durability test and contact voltage drop test method
- Sn-doped CuO nanostructure-based ethanol gas sensor for real-time drunk driving detection in vehicles
- Design considerations for automotive battery wiring harness
- Do you know all the various motors commonly used in automotive electronics?
- What are the functions of the Internet of Vehicles? What are the uses and benefits of the Internet of Vehicles?
- Power Inverter - A critical safety system for electric vehicles
- Analysis of the information security mechanism of AUTOSAR, the automotive embedded software framework
Professor at Beihang University, dedicated to promoting microcontrollers and embedded systems for over 20 years.
- Innolux's intelligent steer-by-wire solution makes cars smarter and safer
- 8051 MCU - Parity Check
- How to efficiently balance the sensitivity of tactile sensing interfaces
- What should I do if the servo motor shakes? What causes the servo motor to shake quickly?
- 【Brushless Motor】Analysis of three-phase BLDC motor and sharing of two popular development boards
- Midea Industrial Technology's subsidiaries Clou Electronics and Hekang New Energy jointly appeared at the Munich Battery Energy Storage Exhibition and Solar Energy Exhibition
- Guoxin Sichen | Application of ferroelectric memory PB85RS2MC in power battery management, with a capacity of 2M
- Analysis of common faults of frequency converter
- In a head-on competition with Qualcomm, what kind of cockpit products has Intel come up with?
- Dalian Rongke's all-vanadium liquid flow battery energy storage equipment industrialization project has entered the sprint stage before production
- Allegro MicroSystems Introduces Advanced Magnetic and Inductive Position Sensing Solutions at Electronica 2024
- Car key in the left hand, liveness detection radar in the right hand, UWB is imperative for cars!
- After a decade of rapid development, domestic CIS has entered the market
- Aegis Dagger Battery + Thor EM-i Super Hybrid, Geely New Energy has thrown out two "king bombs"
- A brief discussion on functional safety - fault, error, and failure
- In the smart car 2.0 cycle, these core industry chains are facing major opportunities!
- The United States and Japan are developing new batteries. CATL faces challenges? How should China's new energy battery industry respond?
- Murata launches high-precision 6-axis inertial sensor for automobiles
- Ford patents pre-charge alarm to help save costs and respond to emergencies
- New real-time microcontroller system from Texas Instruments enables smarter processing in automotive and industrial applications
- The Linux driver LCD screen is distorted or not bright at all. Where should I start debugging?
- Introduction to Intelligent Agents
- Traditional silicon components, silicon carbide (SiC) and gallium nitride (GaN)
- Collection of popular embedded system downloads
- What are the modulation methods of variable frequency power supply?
- This week's highlights
- 3.3V powered half-duplex RS-485 transceiver
- Passive Device Wireless Charging Solution Coil Testing
- DSP System Design-Technical Issues
- 【BLE 5.3 wireless MCU CH582】3. Non-blocking lighting