The Industrial Internet of Things integrates various sensors and control units with perception and monitoring capabilities, Internet communications, intelligent analysis and other technologies into all aspects of the industrial production process, thereby greatly improving manufacturing efficiency, improving product quality, reducing product costs and resource consumption, and ultimately achieving intelligence.
PLC control system is an industrial control unit, which is used to replace relays, execute logic, timekeeping, counting and other sequential control functions. It is widely used in industrial systems because of its strong versatility, easy use, wide adaptability, high reliability, strong anti-interference ability and simple programming.
There is a big branch in the industrial Internet of Things, which is to integrate the PLC control system into the Internet of Things system. PLC is a traditional industrial control unit. The system communication only involves a workshop or factory area, and the data is exchanged within the local area network. To realize the PLC Internet of Things, the first thing is to be able to remotely exchange data with the PLC through the Internet. The current mainstream technology is to bridge the PLC and the Internet through the PLC remote monitoring module. There are still very few PLCs with built-in Internet communication.
The main function of the PLC remote monitoring module is to realize the conversion between the PLC's industrial communication protocol and the Internet's general protocol, to establish a real-time data interaction channel between the remote central control system and the PLC system. The central control system uses data processing technology to realize data analysis, storage, and feedback control of the front-end PLC system.
The core functions of the PLC remote monitoring module are as follows:
It is necessary to solve the protocol conversion and network communication of PLCs of various brands and models on site.
Solve the network node problem, so that the remote data processing system can be quickly and easily connected to the front-end PLC and maintain stable communication.
To realize these two functions, the PLC remote module manufacturers need to have a very in-depth study of the industrial control industry and master the protocols of various types of PLCs (Siemens, Mitsubishi, Omron, AB, Schneider, Beckhoff, Delta, Xinje, etc.), so that they can be used in different sites. In addition, the manufacturers need to have a deep technical foundation in protocol conversion and network communication. That is, both the industrial control and IT industries need to have a deep technical foundation.
The current mainstream technology for PLC remote modules is to transfer through cloud servers, which uses domain name identification technology. There is no need for a fixed IP. The register address of the PLC is mapped on the server through the network. The central control system accesses the cloud server, generally using the OPC protocol or the HTTPS protocol. In this way, the two sides can quickly form a network connection, and the PLC and network protocol conversions are automatically converted by the module. The front-end configuration engineers only need to understand the PLC protocol, and the back-end central control system engineers only need to understand the general OPC protocol or the HTTPS protocol. Engineers on both sides can work independently. A project can be implemented separately.
This type of PLC remote module has many additional functions, because the module uses variable mapping registers to extract data, so that variables can be called to do mobile phone APP, web page monitoring, realize mobile terminal monitoring function, and can also do SMS/WeChat alarm, telephone dial alarm.
There are some other remote modules on the market, such as VPN, which only forms a network transparent transmission channel. In this way, the software protocol of the central control room needs to support PLC, and there is no way to develop mobile APP and web monitoring. In this way, the central control system generally needs to use traditional automatic control software and configuration software. It is more troublesome to develop the central control system by yourself using C++, PHYSON, and JAVA. Because programmers generally do not know the industrial control protocol. The flexibility is relatively poor.
Previous article:Overview of the four key points of motor drivers
Next article:Introduction to PWM drive of brushed DC motor using H-bridge circuit
Recommended ReadingLatest update time:2024-11-16 13:31
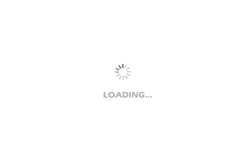
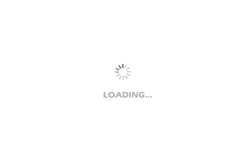
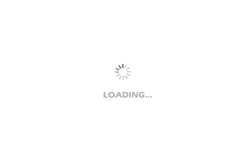
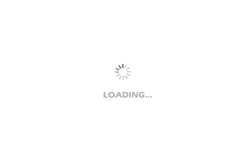
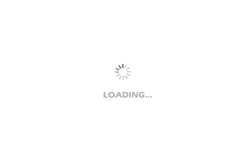
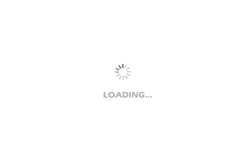
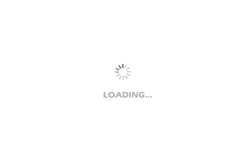
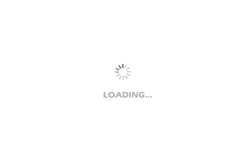
- Popular Resources
- Popular amplifiers
- Huawei's Strategic Department Director Gai Gang: The cumulative installed base of open source Euler operating system exceeds 10 million sets
- Analysis of the application of several common contact parts in high-voltage connectors of new energy vehicles
- Wiring harness durability test and contact voltage drop test method
- Sn-doped CuO nanostructure-based ethanol gas sensor for real-time drunk driving detection in vehicles
- Design considerations for automotive battery wiring harness
- Do you know all the various motors commonly used in automotive electronics?
- What are the functions of the Internet of Vehicles? What are the uses and benefits of the Internet of Vehicles?
- Power Inverter - A critical safety system for electric vehicles
- Analysis of the information security mechanism of AUTOSAR, the automotive embedded software framework
Professor at Beihang University, dedicated to promoting microcontrollers and embedded systems for over 20 years.
- Innolux's intelligent steer-by-wire solution makes cars smarter and safer
- 8051 MCU - Parity Check
- How to efficiently balance the sensitivity of tactile sensing interfaces
- What should I do if the servo motor shakes? What causes the servo motor to shake quickly?
- 【Brushless Motor】Analysis of three-phase BLDC motor and sharing of two popular development boards
- Midea Industrial Technology's subsidiaries Clou Electronics and Hekang New Energy jointly appeared at the Munich Battery Energy Storage Exhibition and Solar Energy Exhibition
- Guoxin Sichen | Application of ferroelectric memory PB85RS2MC in power battery management, with a capacity of 2M
- Analysis of common faults of frequency converter
- In a head-on competition with Qualcomm, what kind of cockpit products has Intel come up with?
- Dalian Rongke's all-vanadium liquid flow battery energy storage equipment industrialization project has entered the sprint stage before production
- Allegro MicroSystems Introduces Advanced Magnetic and Inductive Position Sensing Solutions at Electronica 2024
- Car key in the left hand, liveness detection radar in the right hand, UWB is imperative for cars!
- After a decade of rapid development, domestic CIS has entered the market
- Aegis Dagger Battery + Thor EM-i Super Hybrid, Geely New Energy has thrown out two "king bombs"
- A brief discussion on functional safety - fault, error, and failure
- In the smart car 2.0 cycle, these core industry chains are facing major opportunities!
- The United States and Japan are developing new batteries. CATL faces challenges? How should China's new energy battery industry respond?
- Murata launches high-precision 6-axis inertial sensor for automobiles
- Ford patents pre-charge alarm to help save costs and respond to emergencies
- New real-time microcontroller system from Texas Instruments enables smarter processing in automotive and industrial applications
- Award-winning live broadcast: Microchip&avnet series live broadcast second collection
- Redefining the retail experience: Four opportunities for RF technology
- Thank you for being here
- Tuya Sandwich Wi-Fi & BLE SoC NANO Main Control Board WBRU Zero Code Development IoT Fan
- #The best content of the "Interview with famous teachers" in the Electronics Competition#The third issue - Professor Li Yubai of the University of Electronic Science and Technology of China
- #idlemarket# MM32 development board exchange open source development board
- Forum Prize: Texas Instruments TI-36X Pro Scientific Calculator Disassembly and Analysis
- Why does Kalman filter need to do the prediction step?
- Misiqi's project cooperation based on ESP32 development board IOT Bluetooth WIFI
- Is this a circuit that can prevent the MCU from hanging?