“If you think you have it all figured out, you’re not going fast enough.” — Mario Andretti
Over the years, automobile manufacturers have been challenged by the need for more power. In the early days, cars were powered by 6V batteries until the mid-1950s, when automotive systems evolved to 12V power supplies to meet the permanent need for more power. Not only did automobile manufacturers need to anticipate new power requirements for windows, steering systems, and seats, but more power was also critical for new high-voltage engines.
Recently, OEMs have been forced to rethink how to power vehicles again, spurred by CO2 emissions compliance. While OEMs are launching electric vehicles to meet these standards, there is currently no unified approach to powering the motor and all of the vehicle’s subsystems.
This shortfall is exacerbated by the dramatic increase in power requirements. Internal combustion engine vehicles typically require power supplies between 600W and 3kW. New electrified electric vehicles, hybrid vehicles, and plug-in hybrid vehicles (xEVs) require 3kW to more than 60kW, 5 to 20 times more power than before.
A 5- to 20-fold increase will put tremendous pressure on the size, weight, and complexity of the vehicle power delivery network (PDN). These demands will have a negative impact on energy efficiency, reliability, and even comfort and safety, as the increased size and weight will lead to compromises in vehicle features. If automakers continue to use traditional power supply methods, there will simply not be enough space to meet all electrical needs. To meet this challenge, they need to find a lightweight and compact solution that can not only mitigate the significant increase in power supply volume, but also has the flexibility to be reused across the entire product line.
In addition to the major technical challenges, OEMs are also putting pressure on themselves to commit to fully electrifying their products within the next 10 years (Figure 1), although the specifics of how to achieve this goal remain an open question. There is no clear path to standardization for electrification across the entire EV market. Therefore, while OEMs may share the same goals, the PDNs they design will differ significantly.
Figure 1: By 2030, battery electric vehicles (BEVs) will account for 45% of all xEVs
Accelerating the Electrification Momentum For
many years, electric vehicles accounted for less than 1% of global vehicle production. According to the Credit Suisse Global Automotive Center team, this proportion will soar from 11% in 2020 to 62% in 2030, with global vehicle sales reaching 63 million. Nearly half of these (29 million) are expected to be fully electrified.
Figure 2: OEMs have set aggressive targets for electrification of their product lines. These targets are the catalyst for building a world-class xEV platform.
What’s driving the explosive growth of electric vehicles? While emissions compliance and government incentives got the ball rolling, it’s consumer desire that’s creating the massive demand that’s enabled OEMs to move electric vehicles from the niche to the mainstream. These OEMs are now making bold promises. (Figure 2)
OEMs are now electrifying some of the most popular and sought-after vehicles. The GM Hummer, Ford's new Mach E (electric Mustang), and now the flagship F150 light truck (Lightning) are electrifying. These vehicles are attracting the public's attention because of their exciting performance gains and stylish designs.
These new vehicles, with better fast-charging technology and lower maintenance and repair costs, are the catalyst for consumer demand and increased adoption of electric vehicles. Consumers see the value, so the momentum is growing.
High-Stakes, High-Performance Electrification Challenges
The number of vehicle platforms, consumer options, different powertrain architectures, and choices of battery and charging configurations all add to the complexity of vehicle electrification that powertrain designers must address.
To optimize vehicle electrification, OEMs need to increase power levels, reduce power delivery network size and weight, and provide better thermal management and reusability. Traditional approaches to designing power systems must transition from complex custom discrete designs to smaller, more flexible, easier to use, and higher density modular solutions.
Accelerating the pace of electrification
To achieve aggressive electrification goals, OEMs must rethink their power supply architecture approaches. In addition to finding efficient solutions, accelerating and optimizing electrification must meet three major requirements.
1. Power density: Whether designing a fast sports car, a light truck or a family car, OEMs need to provide as much power as possible within a limited space. Cars require compact and efficient power solutions.
2. Flexibility/Scalability: There are many vehicles in each car series that use the same platform, so easy power expansion is very important when modifying the power of models such as sedans, minivans and SUVs that share the same platform.
3. Reusability: To achieve full vehicle electrification, OEMs need to be able to reuse power supply designs between different models to speed up the time to market.
Power Density
The size and weight of the power electronics used in various xEV platforms are directly related to vehicle performance, energy efficiency, and battery range. In order to go further and faster, OEMs are actively reducing the size and weight of their power electronics and encouraging R&D teams to reduce vehicle weight.
Figure 3: Reducing the size and weight of the power delivery network is a key factor in the next generation of xEV platforms. For example, the 2.5kW Vicor BCM6135 can fit in the palm of your hand.
A small bus converter module (BCM6135) from Vicor with 98% efficiency weighs only 68 grams and can be easily combined with EMI filtering, smaller heat sink structure and housing to replace a 25 kg 48V battery. This not only frees up a lot of space and payload weight, but also saves 125 to 250 euros in weight reduction R&D costs. The high-density power module converts a 400 ~ 800V main battery to 48V in a small package of 61 × 35 × 7 mm, providing more than 2kW of power and a power density of more than 4.3kW/in3 (Figure 3)
Flexibility/Scalability
OEM designers standardize as many subsystems as possible that are integrated into the vehicle to save time, money and resources. However, each subsystem is slightly different as different levels of vehicle interior require different designs. As the electrification of the vehicle progresses, power system design teams are challenged with ever-changing power delivery requirements. The flexible, scalable, modular power system design approach provided by Vicor allows designers to implement standardized solutions across a variety of powertrains such as SUVs, vans or light trucks.
For example, a van might have a power requirement of 5kW, but powering a light truck with a short bar, trailer and plow, and alternator might require 10kW. Using the same platform and a little extra space, engineers can quickly add or remove pre-qualified components from the array to increase or decrease power.
In addition, the modular design can also realize distributed power architecture through 48V bus, providing higher flexibility. The power module can be arranged in a convenient location for local 48V/12V conversion, behind the storage box, near the trunk, or next to each wheel. Deploying modular solutions not only provides design flexibility, but also provides a better way to optimize power supply changes and manufacturing processes.
Figure 4 The impact of modularity is best illustrated by the fact that four high-power density modules can be combined in more than 300 different ways to support different power requirements and a large number of different types of loads.
One of the most common delays in the automotive development process is the approval of electronic components used in the car. Sometimes this process can take up to two to three years to get through before a single component can get the production part approval process. R
&D teams often look for ways to reuse existing components to save development and approval time, saving valuable resources.
例如,基于分立式 DC-DC 转换器设计的传统 PDN 可能由 200 多个体积庞大的组件组成,然而 Vicor 的先进技术则只提供单个高密度电源模块。对于工程设计团队来说,为了实现相同的功能,认证一个模块与认证 200 多款独立组件相比,省时下的时间是非常显著的。
In addition, Vicor’s modular approach allows engineers to implement approximately 300 power delivery combinations by using three or four different types of scalable building blocks. (Figure 4) This design approach can save hundreds of hours of time and resources overall, helping OEMs stay ahead in the race to electrification.
OEMs are facing
a huge challenge to not only cross the finish line of electrification, but also to complete the design of xEV fleets to provide long-term benefits. Adopting a modular approach to power system design can provide a competitive advantage in this important battle for market share. Innovation is needed now in the form of new architectures and topologies that not only provide the highest performance today, but can also be reused and reconfigured later.
Traditional power supply designs cannot provide this level of flexibility and ease of use. For OEMs to achieve their aggressive electrification goals, a modular approach is best used that not only delivers the highest performance at multiple critical levels, but also helps them meet the most complex xEV power needs.
Previous article:Analysis of China's new energy data in July & Shanghai's new energy vehicle registration remains high
Next article:Can Baidu, which has been holding its breath, regain its position in "smart transportation"?
Recommended ReadingLatest update time:2024-11-16 16:49
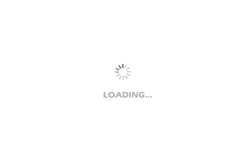
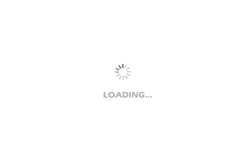
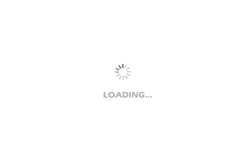
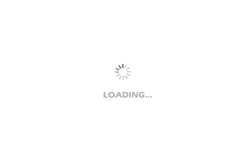
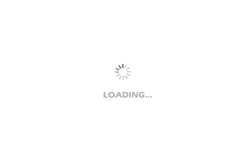
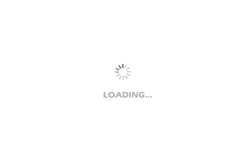
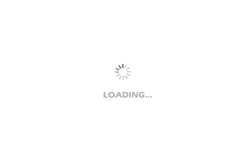
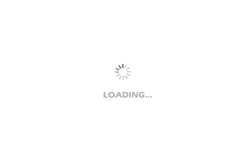
- Popular Resources
- Popular amplifiers
-
New Energy Vehicle Detection and Diagnosis Experiment (Edited by Mao Caiyun, Zhou Xien, and Long Jiwen)
-
Virtualization Technology Practice Guide - High-efficiency and low-cost solutions for small and medium-sized enterprises (Wang Chunhai)
-
Design of an adaptive constant on-time buck DC-DC converter with high efficiency and low power consumption
-
Research on design technology of high-efficiency step-up DC-DC converter with wide load range
- Huawei's Strategic Department Director Gai Gang: The cumulative installed base of open source Euler operating system exceeds 10 million sets
- Analysis of the application of several common contact parts in high-voltage connectors of new energy vehicles
- Wiring harness durability test and contact voltage drop test method
- Sn-doped CuO nanostructure-based ethanol gas sensor for real-time drunk driving detection in vehicles
- Design considerations for automotive battery wiring harness
- Do you know all the various motors commonly used in automotive electronics?
- What are the functions of the Internet of Vehicles? What are the uses and benefits of the Internet of Vehicles?
- Power Inverter - A critical safety system for electric vehicles
- Analysis of the information security mechanism of AUTOSAR, the automotive embedded software framework
Professor at Beihang University, dedicated to promoting microcontrollers and embedded systems for over 20 years.
- Innolux's intelligent steer-by-wire solution makes cars smarter and safer
- 8051 MCU - Parity Check
- How to efficiently balance the sensitivity of tactile sensing interfaces
- What should I do if the servo motor shakes? What causes the servo motor to shake quickly?
- 【Brushless Motor】Analysis of three-phase BLDC motor and sharing of two popular development boards
- Midea Industrial Technology's subsidiaries Clou Electronics and Hekang New Energy jointly appeared at the Munich Battery Energy Storage Exhibition and Solar Energy Exhibition
- Guoxin Sichen | Application of ferroelectric memory PB85RS2MC in power battery management, with a capacity of 2M
- Analysis of common faults of frequency converter
- In a head-on competition with Qualcomm, what kind of cockpit products has Intel come up with?
- Dalian Rongke's all-vanadium liquid flow battery energy storage equipment industrialization project has entered the sprint stage before production
- Allegro MicroSystems Introduces Advanced Magnetic and Inductive Position Sensing Solutions at Electronica 2024
- Car key in the left hand, liveness detection radar in the right hand, UWB is imperative for cars!
- After a decade of rapid development, domestic CIS has entered the market
- Aegis Dagger Battery + Thor EM-i Super Hybrid, Geely New Energy has thrown out two "king bombs"
- A brief discussion on functional safety - fault, error, and failure
- In the smart car 2.0 cycle, these core industry chains are facing major opportunities!
- The United States and Japan are developing new batteries. CATL faces challenges? How should China's new energy battery industry respond?
- Murata launches high-precision 6-axis inertial sensor for automobiles
- Ford patents pre-charge alarm to help save costs and respond to emergencies
- New real-time microcontroller system from Texas Instruments enables smarter processing in automotive and industrial applications
- How to quickly design a pulse oximeter? TI offers tips!
- Seek help from testing and packaging partners
- Summary: BearPi-Hongmeng-BearPi-HM Nano Review Summary
- "In-depth understanding of BootLoader", introducing the development theory, process and examples of BootLoader
- Weekly review information is here~
- Share an easy-to-understand msp430 microcontroller learning tutorial
- Simulation of a Microstrip Patch Antenna for 2.4 GHz Applications with Radiat...
- Analysis of DSP2407's frame pointer (FP) and stack pointer (SP)
- msp430 MCU rc522 radio frequency program and circuit diagram
- EEWORLD University Hall----FPGA Design Skills and Specifications