Technological progress has greatly increased the electronic content in modern cars, and the development of electronic technology has made cars safer, smarter, more comfortable, more environmentally friendly and more energy-efficient. The development of the two complements each other and brings out the best in each other, providing great convenience for people's lives. However, at the same time, the reliability of electronic components has also become an important factor in ensuring car safety, especially products used in the increasingly popular advanced driver assistance systems (ADAS), which will have a profound impact on car safety.
At present, the penetration rate of new ADAS cars in my country is less than 4%, which is far behind that of developed countries. With the introduction of relevant policies, the domestic ADAS market will grow rapidly. According to forecasts, the scale of China's ADAS market will reach 96.3 billion yuan in 2020, with an average annual compound growth rate of 52%, far exceeding the international market.
Harsh environments challenge electronic components
Automobiles are harsh environments with wide temperature ranges (instant heating and cooling), mechanical vibration, noise, gas pollution, potential risks of transient voltage, high current, etc. These are the important factors that affect the functional stability, reliability and driving experience of modern automobiles.
Car heat is not only in the engine compartment
With the multifunctionalization of automobiles for the purpose of autonomous driving in recent years, such as the continuous development of ADAS, which is the focus of research and development at this stage, the mechatronics of various electronic control units (ECUs) has been continuously improved. More and more electronic devices are installed in automobiles, and the reliability of electronic components has an increasing impact on the overall reliability of automobiles. Especially in automotive applications with rapid temperature changes and high mechanical strength (stress), durable electronic components are needed to meet higher requirements. In addition, while achieving high performance, it is also necessary to meet the miniaturization requirements to solve space constraints.
Facing challenges head-on, capacitors show their talents
The development of electric vehicles has greatly increased the use of multilayer ceramic capacitors ( MLCCs ). Traditional cars use about 2,400 pieces, while new energy vehicles such as Tesla use around 8,000 pieces. The average ADAS usage per vehicle has reached 2,000-3,000 pieces.
In order to meet the higher level of reliability and robustness requirements of self-driving car components, capacitors are constantly improving in terms of advanced functionality, ease of use, and physical substitution. Traditional MLCCs have adopted some new technologies, while tantalum polymer capacitors are trying to replace them; supercapacitors are also making efforts in the ADAS application market.
MLCC technology innovation
ADAS is becoming more and more important in improving driving safety, and more and more ICs support this function. In order to suppress noise, more smooth decoupling MLCCs are needed. From the perspective of space-saving design, the demand for miniaturized, high-capacitance MLCCs will continue to increase.
MLCCs related to automotive safety devices ADAS/AD ECU
MLCC has the characteristics of small size, large specific capacity, long life, high reliability, and suitable for surface mounting, but it is inevitable that some failures will occur in cars with harsh environments. In order to meet the requirements of automotive grade, TDK developed a high-reliability product, resin electrode type (Soft Termination, also called flexible terminal electrode) MLCC, which can solve the problems of bending cracks and solder cracks and ensure the reliability of applications.
Generally, the main cause of component flex cracks is the bending stress of the substrate, including solder stress caused by the amount of solder, stress during substrate segmentation, and stress during manufacturing. When the component body cracks, "short-circuit mode" or "open-circuit mode" failure may occur.
The main causes and processes of bending
In automotive applications, substrate bending stress and thermal shock can cause expansion or contraction of the capacitor solder joint. The Cu (copper) base layer of the common MLCC terminal electrode is plated with Ni (nickel) and Sn (tin). The resin electrode product is a structure in which a conductive resin layer is added to the Cu and Ni plating layers. This structure has a certain degree of flexibility and can absorb the stress generated, which can improve the reliability of the connection compared to ordinary electrode products.
Differences in terminals between standard electrode MLCC and resin electrode products
The resin layer can absorb the stress caused by the expansion and contraction of the solder joint due to thermal shock and the substrate bending stress, thereby preventing cracks in the component body.
According to reports, TDK's MLCC resin electrode products have more than twice the bending resistance in the substrate bending resistance (limit bending) test compared to ordinary electrode products. The test showed that when cracks occurred in the ceramic component of ordinary electrode products, although the nickel plating layer of the conductive resin electrode product began to peel off from the conductive resin layer, no cracks occurred, thus confirming that the resin electrode product can suppress cracks.
Solder cracks in electronic components are caused by the soldering process during manufacturing and harsh usage conditions. The main reason is that in the environment of repeated temperature changes in automobiles, the difference in thermal expansion coefficients between the component electrode and the substrate causes thermal stress to be applied to the solder joint. At the same time, for environmental considerations, lead-free solder is used in automotive electronic components. From the perspective of temperature management and solder composition, the risk of solder cracks is higher than that of conventional eutectic solder.
The main cause of solder cracks
Generally, the bonding strength decreases after thermal shock. After 3000 thermal cycles (-55 to 125°C) shock test, the bonding strength of ordinary electrode MLCC decreased by about 90%, while the resin electrode product only decreased by about 50%. The excellent thermal shock resistance of resin electrode products was confirmed by thermal shock test data.
MLCC Thermal Shock Test Data
TDK believes that in places with large temperature changes such as automobile engine compartments or other heat source equipment, the electronic components used will cause solder cracks due to component body cracks and stress at the junction with the substrate, which may cause component detachment, short circuits, and open circuit failures. The use of resin electrode products can prevent cracks caused by substrate warping, bending, and thermal shock without changing the occupied space, and can also suppress external stress, thereby improving the connection reliability of the ADAS system.
In September, TDK began mass production of new automotive-grade CGA series resin electrode MLCC products, achieving larger capacitance, with the 2012 specification capacitance being 22μF and the 3216 specification capacitance being 47μF.
Tantalum polymer capacitors take over the market
As cars become increasingly populated with electronic components and increasingly compacted with space to house them, some companies have been exploring opportunities to shrink automotive-grade capacitors to save board space.
Wilmer Companioni, senior technical marketing manager at Kemet, believes that automotive applications are special, and the stability and capacitance accuracy of MLCCs correspond to the dielectric materials used. The main reason for their failure is the presence of various microscopic defects such as cracks, holes, and delamination on the outside or inside of the MLCC. These defects will directly affect the electrical performance and reliability of the MLCC, and ultimately affect the function of the ADAS system.
So, is there a reliable and compact product that can replace the MLCC on the market? Yes, tantalum polymer capacitors (Ta Polymer) provide automotive designers with a new potential solution that helps achieve board space saving, no piezoelectric noise and miniaturization solutions.
He said that since 2015, Kemet has launched a tantalum polymer SMD product portfolio, opening up opportunities for automotive component miniaturization and reducing overall solution costs, and challenging the MLCC supply chain.
At the beginning of 2018, the MLCC supply chain showed some loosening, and some customers were looking for alternative solutions to MLCC. In order to verify the feasible technology, Kemet conducted a lot of research. It was found that engineers can use tantalum polymer capacitors when the capacitance range is between 1uF and 1mF and below 75V.
Capacitance and voltage of different capacitor technologies
However, the conversion process from MLCC to tantalum polymer SMD components is not a “one-to-one” process and several considerations need to be followed. Mechanical and dimensional characteristics are the first parameters to be verified.
Parameters to consider when converting MLCC to Tantalum Polymer SMD
To determine whether MLCC and tantalum polymer capacitors can be directly replaced, a size comparison must be made: MLCC EIA codes 0805 and 1206 can be directly replaced using P-2012 and A-3216 sizes. Although the replacement is not direct, the larger MLCC EIA codes 1210 and 2220 can also be replaced by B3528 and D7343.
MLCC vs. Tantalum Polymer Size Comparison
In order to determine what solution is suitable, it is necessary to compare electrical characteristics. MLCC technology is characterized by capacitance drop effect, temperature drop effect and final life aging effect. On the other hand, MLCC technology has very low leakage current and insulation resistance ranges from 100 to 1000MΩ; the DCL (leakage current) indicator of tantalum polymer capacitors is defined as 0.1×C×V μA (C: rated capacitance in μF; V: rated voltage in V).
Previous article:What are the unavoidable points behind the rapid growth of electric vehicles?
Next article:Tesla's domestically produced standard version uses lithium iron phosphate batteries, which has been questioned by car owners
Recommended ReadingLatest update time:2024-11-17 03:06
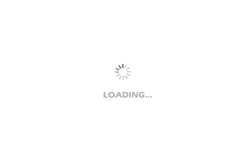
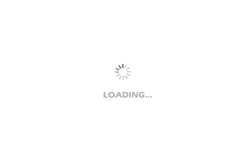
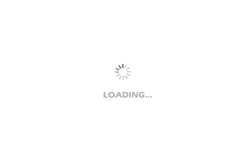
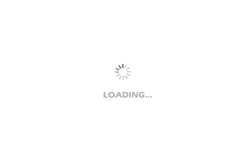
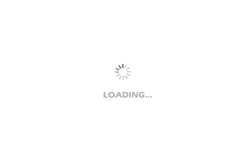
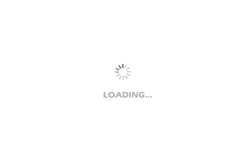
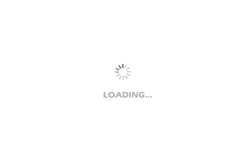
- Popular Resources
- Popular amplifiers
-
Modern Electronic Technology Training Course (Edited by Yao Youfeng)
-
Distributed robust Kalman filter fusion algorithm for ADAS system vision and millimeter wave radar
-
End-to-end learning of ADAS vehicle spacing and relative speed based on monocular camera
-
Improved SSD algorithm for real-time target vehicle detection in ADAS
- Huawei's Strategic Department Director Gai Gang: The cumulative installed base of open source Euler operating system exceeds 10 million sets
- Analysis of the application of several common contact parts in high-voltage connectors of new energy vehicles
- Wiring harness durability test and contact voltage drop test method
- Sn-doped CuO nanostructure-based ethanol gas sensor for real-time drunk driving detection in vehicles
- Design considerations for automotive battery wiring harness
- Do you know all the various motors commonly used in automotive electronics?
- What are the functions of the Internet of Vehicles? What are the uses and benefits of the Internet of Vehicles?
- Power Inverter - A critical safety system for electric vehicles
- Analysis of the information security mechanism of AUTOSAR, the automotive embedded software framework
Professor at Beihang University, dedicated to promoting microcontrollers and embedded systems for over 20 years.
- Innolux's intelligent steer-by-wire solution makes cars smarter and safer
- 8051 MCU - Parity Check
- How to efficiently balance the sensitivity of tactile sensing interfaces
- What should I do if the servo motor shakes? What causes the servo motor to shake quickly?
- 【Brushless Motor】Analysis of three-phase BLDC motor and sharing of two popular development boards
- Midea Industrial Technology's subsidiaries Clou Electronics and Hekang New Energy jointly appeared at the Munich Battery Energy Storage Exhibition and Solar Energy Exhibition
- Guoxin Sichen | Application of ferroelectric memory PB85RS2MC in power battery management, with a capacity of 2M
- Analysis of common faults of frequency converter
- In a head-on competition with Qualcomm, what kind of cockpit products has Intel come up with?
- Dalian Rongke's all-vanadium liquid flow battery energy storage equipment industrialization project has entered the sprint stage before production
- Allegro MicroSystems Introduces Advanced Magnetic and Inductive Position Sensing Solutions at Electronica 2024
- Car key in the left hand, liveness detection radar in the right hand, UWB is imperative for cars!
- After a decade of rapid development, domestic CIS has entered the market
- Aegis Dagger Battery + Thor EM-i Super Hybrid, Geely New Energy has thrown out two "king bombs"
- A brief discussion on functional safety - fault, error, and failure
- In the smart car 2.0 cycle, these core industry chains are facing major opportunities!
- Rambus Launches Industry's First HBM 4 Controller IP: What Are the Technical Details Behind It?
- The United States and Japan are developing new batteries. CATL faces challenges? How should China's new energy battery industry respond?
- Murata launches high-precision 6-axis inertial sensor for automobiles
- Ford patents pre-charge alarm to help save costs and respond to emergencies
- Nordic nRF52832 program download problem analysis
- The result of arctan calculation by IP core is not converted
- What is the GPIO number under Sys/class?
- Good thing to share: MobIR Air ultra-high cost-effective portable mobile thermal imager
- How to generate .lib file for atmel atudio and call it in other projects
- LPC1768 UCOSII is ported to IAR8.3 environment. There is no problem in compiling, but it is stuck when creating the first task function...
- This module can meet the "high current" required for 3C lithium battery pack testing. You should know about it?
- Please help me with this DCDC IC model, thank you very much
- Which technology is best? 5G or Wi-Fi 6
- Internet of Things For Dummies 2nd Edition