I. Introduction
Robotics research is the most complex and challenging subject in the field of automation. It integrates multiple disciplines such as mechanics, electronics, computers, materials, sensors, and control technology, and is a concentrated embodiment of multidisciplinary high-tech achievements. The research on humanoid walking robot technology is at the forefront of robot research, and it represents a country's high-tech development level to a certain extent. Motion control system is the core of robot control technology and one of the key technologies in the field of robot research. It plays a pivotal role in robot control. Therefore, all research institutions regard the research on robot motion control system as their primary task.
Coordinated movements, certain intelligence, and the ability to achieve wireless real-time walking have become the main themes of today's robot development. With the continuous development of modern high technology represented by electronic computers and digital electronic technology, especially the widespread application of high-speed digital signal processors represented by DSP and large-scale programmable logic devices (represented by CPLD and FPGA), robot motion control systems have also developed from the previous single structure and simple functions to structured, standardized, modular and highly integrated directions. The use of open architecture has become an inevitable trend in the development of this technology. The author of this article has designed a multifunctional distributed humanoid robot motion control system in response to this trend.
2. Control objects and requirements
We take the new generation of humanoid walking robot newly developed by the Robotics Teaching and Research Section of the School of Mechanical and Electrical Engineering and Automation of the National University of Defense Technology as the research object (its appearance is shown in Figure 1). The robot is about 1.55m high and weighs about 65kg. It is powered by batteries and does not require an external power supply or control signal line. It can walk without cables and can also complete some basic movements of human legs, hands and head. It has initially possessed the appearance characteristics of humans. This new humanoid robot has a total of 36 degrees of freedom (as shown in Figure 2), including 12 upper limbs, 12 lower limbs, 2 heads, and 10 hands; each joint of the lower limbs has a position sensor, and the foot has a multi-dimensional force/torque sensor; it has a visual sensor, voice control system and wireless remote control module; the entire control system. The power supply is integrated on the robot body. In order to make it truly "humanoid", the control system must be able to complete a variety of functions including motion control and planning, visual perception processing, speech recognition and other environmental perception. Among them, motion control is the key to the entire control system, and it must be able to meet the following requirements:
(1) High system integration, small size, light weight, high power, high efficiency and airborne.
(2) The connection between each module is simple, which is easy to install and maintain.
(3) The controller should have good dynamic response and following characteristics, steady-state error and static error correction.
(4) The system is integrated on the robot body, which has strong electromagnetic interference and must have strong anti-interference capabilities.
(5) Data exchange between various parts must be real-time, effective, accurate and reliable.
3. Dynamic control system design
According to the above requirements, we designed a new control structure based on CAN field bus. The whole control system adopts the method of centralized management and decentralized control, and is divided into three layers according to the structure and function of the control system: organization layer, coordination layer, and execution layer. Among them, the organization layer consists of a workstation outside the robot body, which is mainly responsible for realizing human-computer interaction, wireless communication, voice, vision, and macro instruction generation, which belongs to the category of intelligent control and will not be discussed in depth in this article; the coordination layer and execution layer are integrated on the robot body to complete specific control tasks, which belongs to the category of physical control and is a control system in our usual sense. Its specific structure is shown in Figure 3.
(1) Main control computer module
The main control computer is required to be small in size and fast in computing speed. It is usually a small-board industrial control computer equipped with a liquid crystal display and a self-made special function keyboard. It mainly completes online motion planning, action-level motion control, voice interactive control, visual guidance control, and human-computer interaction. It receives information from local sensors, generates task planning data for joint axis systems in real time according to certain control algorithms and task requirements, and sends it to each underlying motion controller through a data transmission bus.
(2) Communication module
The main control computer and each controller use CAN bus for communication. CAN (Controller Area Network) bus is the most widely used field bus and the only field bus with international standards so far. Compared with general communication buses, its data communication has outstanding reliability, real-time performance and flexibility. Its main features are:
(1) The CAN bus is a multi-master bus, and any node on the network can send data to other nodes at any time.
(2) Nodes on the CAN bus can be divided into different priorities through identifiers to meet different real-time requirements.
(3) The CAN bus uses non-destructive bus arbitration technology, and low-priority nodes do not affect the transmission of high-priority nodes.
(4) The communication rate of CAN bus nodes within 40m can reach up to 1MBPS.
(5) The number of nodes on the CAN bus can reach 110 in the standard frame format and is almost unlimited in the extended frame format.
(6) The message adopts a short frame format, with a short transmission time and an extremely low error rate.
(7) The CAN bus communication medium can be twisted pair, which has a flexible structure and is easy to connect.
The above characteristics of CAN bus make it very suitable for robot control. In view of this, this paper selects CAN bus as the communication tool for robot control system. The specific connection method is: the main control computer is connected to the bus through the CAN bus interface card, and each motion controller is also connected to the bus through the bus transceiver, and the number can be increased or decreased according to the actual situation. Since CAN bus only uses two wires for communication, the complexity of system wiring is greatly reduced, and the reliability of the system is enhanced.
(3) Execution layer module
The execution layer is at the bottom of the entire control system and is composed of different types of controllers. It is mainly used to control the specific execution process of each motion joint axis system. Since the motors of each motion joint are of different models and carry different weights, the requirements for control accuracy are also different. We have designed different motion controllers for them.
①Open-loop DSP motion controller
The head and upper limbs are light in weight, so open-loop DSP motion controllers are used to control the joints of the head and upper limbs. These controllers do not require sampling and feedback, but directly receive control commands from the main control computer, and then generate corresponding execution commands to each joint axis system to make it rotate to the corresponding angle.
②Open-loop MCU motion controller
The volume and mass of each joint of the hand are very small, so an open-loop MCU motion controller is used for control. These controllers use MCS-51 microcontrollers as processors and can be directly embedded in the palm. They receive control commands from the host computer and use their IO pins to generate the required multi-channel pulse control signals to control the movement of each joint of the hand.
③ Closed-loop DSP motion controller
All the axis systems of the legs are composed of DC reduction drive motors with zero position detection. Encoder and potentiometer feedback and multi-dimensional force/torque sensors have complex structures. The control is difficult. The precision requirement is also high, so a closed-loop DSP motion controller is used. This part is the key to the entire control system and the focus of our research.
(4) Control system flow
The specific process of the entire control system is as follows: the system starts running and completes the initialization work; the main control computer sends control commands to the bottom-level controller according to the plan and calculation. After receiving the command, the bottom-level controller combines the information fed back by each sensor, generates corresponding execution commands through a certain control algorithm and sends them to each joint execution axis system, and uploads the operation status of the bottom-level axis system to the main control computer. The main control computer generates new commands based on the new situation and sends them to each controller, and repeats this process. This is actually two closed-loop feedback processes. The bottom-level controller performs small-loop feedback between the sensor and each joint axis system, and the main control computer performs large-loop feedback between each controller and each joint axis system. This can make the robot more "intelligent" and better perform offline real-time control.
The main control computer sends 200 sets of data to the bottom-level controller every second, and the bottom-level controller feeds back the same amount of data to the main control computer. The maximum communication rate of the CAN bus can reach several thousand frames per second, which can fully meet the control requirements.
4. Detailed design of controller
The closed-loop DSP controller that controls the lower limbs is the core of the entire control system. It bears the load weight of the entire robot, has a large output power, and requires high control accuracy. Therefore, its performance is directly related to the realization of robot movement. We specially designed a closed-loop DSP controller based on dual position sensors, and its structure is shown in Figure 4.
The DSP main processor uses the TMS320LF2407A chip of TI, which is a high-end product in the TI family C2000 series and is very suitable for industrial control. Its two event managers are particularly powerful and are completely designed for motor control. They can use multiple PWM pulse channels to directly generate the required PWM pulse control signals; its CAN bus module can directly communicate with the main control computer without adding a CAN bus controller; the external watchdog can monitor the controller voltage; the external memory stores the necessary parameters required for the control algorithm.
The dual position sensor of the controller consists of a voltage output sensor and a photoelectric encoder sensor. Among them, the voltage sensor converts the position information of the shaft system into a voltage signal, which is amplified by the amplifier circuit and then converted into a digital signal by a special A/D converter and sent to the DSP main processor. Instead of using the A/D converter that comes with TMS320LF2407A, a special A/D conversion chip is used. This is to improve the conversion accuracy, because the maximum conversion voltage that the A/D converter of TMS320LF2407A can accept is only 3.3V, and the voltage after power amplification is far beyond this range, so a special A/D conversion chip is used. Although this part of the circuit increases the complexity of the controller, it can greatly improve the conversion accuracy, so it is very worthwhile. The encoder sensor converts the position information of the shaft system into a pulse signal, which is isolated by the photoelectric isolation device and sent to a special pulse counter. The information after counting is sent to the DSP main processor. The pulse counter uses the popular CPLD device today. Its powerful function is of great help to improve the performance of the controller. At the same time, it can also be used as a decoding circuit to provide decoding function for the main processor.
The main processor generates the corresponding PWM pulse control signal after analyzing and calculating the received sensor signal, and sends it to the bottom axis system to control the operation of the axis system after photoelectric isolation and power amplification. The use of dual sensors can greatly improve the accuracy of feedback. The two signals can be considered at the same time, or one can be the main one and the other can provide supplement and reference.
The main processor communicates with the main control computer through the CAN bus, receives commands from the main control computer and feeds back the underlying information to the main control computer to achieve a higher level of feedback control. The main processor is connected to the bus through a CAN bus transceiver. To improve accuracy, optoelectronic isolation is required in the middle.
The controller is directly installed in the body of the humanoid robot. Each controller can control 6 joint axis systems at the same time. Only two controllers are needed to realize the motion control of the entire lower limb.
5. Conclusion
On the basis of fully absorbing the high-tech achievements of relevant disciplines today, we have designed a humanoid robot motion control system with fast speed, strong stability, high integration, flexible structure and easy use. The entire motion control system can be directly embedded in the robot body so as to successfully complete the specified control tasks in actual operation. At the same time, the control system has a strong expansion function and can be easily transplanted to other similar control mechanisms. It is a multifunctional general control system with broad application prospects.
Previous article:Key issues of μC/OS-II running in DSP Flash memory
Next article:Design of Micro Digital Storage System Based on FPGA
Recommended ReadingLatest update time:2024-11-16 21:01
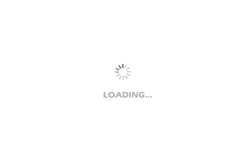
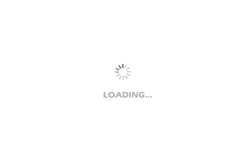
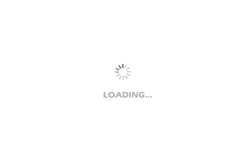
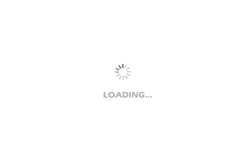
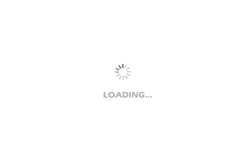
- Popular Resources
- Popular amplifiers
- Huawei's Strategic Department Director Gai Gang: The cumulative installed base of open source Euler operating system exceeds 10 million sets
- Analysis of the application of several common contact parts in high-voltage connectors of new energy vehicles
- Wiring harness durability test and contact voltage drop test method
- Sn-doped CuO nanostructure-based ethanol gas sensor for real-time drunk driving detection in vehicles
- Design considerations for automotive battery wiring harness
- Do you know all the various motors commonly used in automotive electronics?
- What are the functions of the Internet of Vehicles? What are the uses and benefits of the Internet of Vehicles?
- Power Inverter - A critical safety system for electric vehicles
- Analysis of the information security mechanism of AUTOSAR, the automotive embedded software framework
Professor at Beihang University, dedicated to promoting microcontrollers and embedded systems for over 20 years.
- Innolux's intelligent steer-by-wire solution makes cars smarter and safer
- 8051 MCU - Parity Check
- How to efficiently balance the sensitivity of tactile sensing interfaces
- What should I do if the servo motor shakes? What causes the servo motor to shake quickly?
- 【Brushless Motor】Analysis of three-phase BLDC motor and sharing of two popular development boards
- Midea Industrial Technology's subsidiaries Clou Electronics and Hekang New Energy jointly appeared at the Munich Battery Energy Storage Exhibition and Solar Energy Exhibition
- Guoxin Sichen | Application of ferroelectric memory PB85RS2MC in power battery management, with a capacity of 2M
- Analysis of common faults of frequency converter
- In a head-on competition with Qualcomm, what kind of cockpit products has Intel come up with?
- Dalian Rongke's all-vanadium liquid flow battery energy storage equipment industrialization project has entered the sprint stage before production
- Allegro MicroSystems Introduces Advanced Magnetic and Inductive Position Sensing Solutions at Electronica 2024
- Car key in the left hand, liveness detection radar in the right hand, UWB is imperative for cars!
- After a decade of rapid development, domestic CIS has entered the market
- Aegis Dagger Battery + Thor EM-i Super Hybrid, Geely New Energy has thrown out two "king bombs"
- A brief discussion on functional safety - fault, error, and failure
- In the smart car 2.0 cycle, these core industry chains are facing major opportunities!
- The United States and Japan are developing new batteries. CATL faces challenges? How should China's new energy battery industry respond?
- Murata launches high-precision 6-axis inertial sensor for automobiles
- Ford patents pre-charge alarm to help save costs and respond to emergencies
- New real-time microcontroller system from Texas Instruments enables smarter processing in automotive and industrial applications
- MicroPython 1.19 released
- [Sipeed LicheeRV 86 Panel Review] 3- Transplanting LVGL
- EEWORLD University ---- FreeRTOS on stm32 ST
- Read the white paper on Renesas Electronics' power module series and win double gifts: energy boost gift & 100% recommendation gift!
- Understanding common mode and differential mode
- 【McQueen Trial】Unboxing and microbit
- LLC or Flyback Topology? It all depends on the end-user requirements
- The basics of power management you must know
- STM32f767zi UART
- [Synopsys IP Resources] Complete Die-to-Die IP Solution: Use Cases and Requirements