Recommendations for general troubleshooting
Under accidental conditions, even if the technology used is not advanced, the quietness of the system may still be acceptable. However, the physical properties of the noise will eventually come into play and may occur unexpectedly. If we understand the actual workings of ground systems and interfaces and the mechanisms by which noise couples into signals, then identifying and solving problems is simple and logical.
Perhaps the most important aspect of troubleshooting is how you recognize the problem. Without a systematic approach, eliminating noise problems can be difficult, time-consuming and labor-intensive. For example, don't fall into the trap of turning a blind eye to problems because you're used to dealing with them in a certain way. Things that "might not go wrong" are exactly where the problems are. What's more, problems that disappear on their own will reappear on their own.
Don't replace components right away. The reason is this: If we collect enough clues and analyze as much information as possible between hands-on replacement components, many problems will reveal themselves.
Ask questions like: Has it ever worked fine? Under what conditions does noise occur? What other symptoms appeared at the same time?
Be careful to use the device itself to find clues. Control operations of equipment and making some simple logical judgments may provide very valuable clues. For example, if the noise is not affected by changing the volume or channel selection, it would logically follow that the noise enters the signal path after the control. If the noise can be eliminated by turning down the volume or selecting another station, then the noise must have entered the signal path before the station was selected.
Take good notes, you may waste a lot of time here just by remembering.
Draw a block diagram of the system, showing all signal interconnecting cables, including digital and RF cables, indicating their approximate lengths, and labeling balanced inputs or outputs. Generally speaking, a stereo pair can be represented as a single line. Pay attention to equipment that uses a 3-prong power outlet for grounding, and pay attention to ground connections such as cable TV or DSS panels.
The system should be analyzed from back to front. As a general guideline, unless clues have been found that suggest starting at another starting point, analyze from the input to the power amplifier (for audio systems) or from the input to the monitor (for video systems) and work backwards. Test the interface down to the signal source. A simple-to-construct test adapter or simulator allows the system to self-test and pinpoint the entry point of noise or interference. By temporarily adding the simulator directly to the interface, precise information about the nature of the problem is reproduced.
Found the problem of unbalanced interface
For unbalanced audio interfaces, simulator testing specifically identifies the following issues:
![]() |
Figure 1: Simulator of unbalanced interface. |
Emulators are wired using standard connectors as shown in Figure 1. They do not carry signals, so they must be clearly labeled so they are not inadvertently permanently installed into the system. Be extremely careful not to damage the speakers or headphones.
four step testing method
Each signal interface is tested using the following four-step method. Multiple cables in the same chassis (e.g. stereo pairs) are to be tested simultaneously:
![]() |
|
Is the output quiet?
No—The problem is either in chassis B or in the downstream stage;
Yes - go to the next step;
![]() |
|
Is the output quiet?
No - there is a "single pin connection problem" inside chassis B, which can be confirmed by the "Hummer" buzzer test.
Yes - go to the next step;
![]() |
|
Is the output quiet?
No—Noise is being induced into the cable, relocate the cable to avoid the interfering field;
Yes - go to the next step;
Is the output quiet?
No - the problem is common impedance coupling and an isolator needs to be installed in the signal path;
Yes—The noise is coming from the output of Chassis A. Perform the test sequence on the next upstream interface. Repeat as necessary until the problem is found.
Found issues with balanced interfaces
For balanced interfaces, testing specifically identifies the following issues:
![]() |
Figure 2: Simulator of balanced interface. |
The emulators are wired using the standard connectors shown in the figure. They do not carry signals, so they must be clearly labeled so they are not inadvertently permanently installed into the system. Be extremely careful not to damage the speakers or headphones.
Each signal interface is tested using the following four-step method. Multiple cables in the same chassis (e.g. stereo pairs) are to be tested simultaneously:
![]() |
|
Is the output quiet?
No—The problem is either in chassis B or in the downstream stage;
Yes - go to the next step;
![]() |
|
Is the output quiet?
No - there is a "single pin connection problem" inside Chassis B, which can be confirmed by Hummer testing.
Yes - go to the next step;
![]() |
|
Is the output quiet?
No—Noise is being induced into the cable, relocate the cable to avoid the interfering field;
Yes - go to the next step;
![]() |
|
Is the output quiet?
No - The problem is shield current induced noise (SCIN), use a different type of cable or take steps to reduce shield current.
Yes—The noise originates from the output of Chassis A, and the test sequence is performed on the next upstream interface.
![]() |
Figure 3: Three chassis with internal pinout issues. |
![]() |
Figure 4: A "Hummer" used to test shields. |
"Pin single connection problem" and "Hummer"
The "single-pin problem," coined by Neil Muncy, refers to the phenomenon of common impedance coupling that has been inadvertently engineered into a significant number of products. As Neil says, "Balanced design gets a bad rap because of this, and it's a reputation it doesn't deserve. It's really the novelty issue. Balanced wire interconnects were originally expected to ensure noiseless system performance, but, in fact, they Often this is not done." This problem effectively converts the shield connection into a very low impedance signal input, as shown in Figure 3, where shield current is allowed to flow through internal wires or circuit board traces shared by sensitive amplifier circuits. Any small voltage drop that occurs is amplified and appears at the output of the device. When this problem exists in a system, it may interact with other noise coupling mechanisms, making troubleshooting difficult. It may affect unbalanced audio, video and data interfaces. Fortunately: simple testing can expose problems. The "Hummer" test method was proposed by John Windt. The circuit of this simple device is shown in the figure below. It forces a current of about 50mA to flow through a potentially troublesome shield connection in the device under test. In a properly designed device, this can cause additional noise at the device output. When the clip is shorted, the 12V transformer supplies approximately 50mA. Optional LEDs and an IN4001 diode simply show that a connection has been made and current is indeed flowing.
Using the "Hummer" test
1. Disconnect the input and output cables (except the output under test) and all chassis connections (such as rack mounting) from the device under test;
2. Add power to the device under test;
3. Measure (and if possible, listen to) the output of the device under test. The only noise should be white noise or "hiss." Experiment with various control settings to familiarize yourself with the noise characteristics of the device under test without a Hummer connected.
![]() |
Figure 5: Pattern generator. |
![]() |
Figure 6: Video simulator. |
4. Connect one pin of the Hummer to the chassis of the device under test and touch the other pin to the shield contact of each output or output connector. If the device under test is designed correctly, there will be no hum or changes in the noise floor in the output.
5. Test other possible trouble paths, such as from the input shield contact to the output shield contact or from the protective ground pin of the power cord to the chassis. In some devices, the single pin of the XLR connector doesn't necessarily have to be connected directly to ground - hopefully this is just on the input side. In this case, the "Hummer" LED may not glow, and that's right.
Found a problem with the video interface
This is a simple difference from the troubleshooting steps for audio systems. Because many - if not most - monitors display a blue screen when there is no video signal, this test utilizes a portable video source to keep the display functioning. If you do a lot of video processing, you may want to use a video pattern generator similar to the B&K Precision Model 1211E shown in Figure 6. It is important that the generator is battery powered and not grounded. You will also need a test adapter or "emulator" connection as shown in Figure 5. Utilizes RCA and BNC connectors to easily fit it into a small cast aluminum box. By temporarily placing testers and generators at strategic locations in the system, precise information about the nature of the problem can be exposed. The cable between the tester and chassis B should be as short as possible—much shorter than the cable under test.
To test starting from the monitor input and working backwards to the signal source, each signal interface must be tested using the following four steps:
![]() |
|
Are the distractions gone?
No—The problem is either with Chassis B or downstream. Connect the cable again and perform the test on the next downstream interface.
Yes—Go to the next step.
![]() |
|
Are the distractions gone?
No—The problem may be due to common impedance coupling within Chassis B or to devices further downstream. If the inputs are different (i.e. the shield is not directly connected to ground), then the problem may be due to exceeding the common-mode voltage limit. If the problem is not in Chassis B, connect the cable again and start the test procedure on the next downstream interface.
Yes—Go to the next step.
![]() |
|
Are the distractions gone?
No—The interference is being induced by the cable itself due to the strong AC magnetic field near the cable. Reroute cables to avoid strong magnetic fields. Such magnetic fields include high-current power lines, power transformers, and CRT monitors. Electric field coupling is also possible, but is extremely rare in video systems unless the shield itself is destroyed or disconnected.
Yes—Go to the next step.
![]() |
|
Are the distractions gone?
No—Ground current couples through the common impedance of the cable shield. Install a suitable ground isolation device.
Yes—Interference is present at the output of Chassis A. Execute the test sequence on the interface between Chassis A and the upstream signal source.
By taking a systematic approach to diagnosing noise problems in your sound system, you can often locate and correct the problematic circuit or connection. With a systematic testing method and simple tools, you can directly and quickly find even the most elusive audio noise problems.
Previous article:Application of silicon spread spectrum oscillators in automotive electronics
Next article:Car Bluetooth hands-free solution based on CSR CVC-HF system
Recommended ReadingLatest update time:2024-11-16 16:53
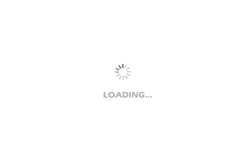
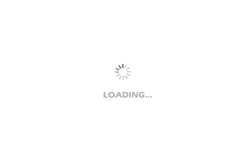
- Popular Resources
- Popular amplifiers
-
【Follow me Season 2 Episode 1】-Mission Code (Adafruit Circuit Playground Express Development Board)
-
Intelligent environmental perception technology for autonomous unmanned systems
-
A review of deep learning applications in traffic safety analysis
-
Dual Radar: A Dual 4D Radar Multimodal Dataset for Autonomous Driving
- Car key in the left hand, liveness detection radar in the right hand, UWB is imperative for cars!
- After a decade of rapid development, domestic CIS has entered the market
- Aegis Dagger Battery + Thor EM-i Super Hybrid, Geely New Energy has thrown out two "king bombs"
- A brief discussion on functional safety - fault, error, and failure
- In the smart car 2.0 cycle, these core industry chains are facing major opportunities!
- The United States and Japan are developing new batteries. CATL faces challenges? How should China's new energy battery industry respond?
- Murata launches high-precision 6-axis inertial sensor for automobiles
- Ford patents pre-charge alarm to help save costs and respond to emergencies
- New real-time microcontroller system from Texas Instruments enables smarter processing in automotive and industrial applications
- Innolux's intelligent steer-by-wire solution makes cars smarter and safer
- 8051 MCU - Parity Check
- How to efficiently balance the sensitivity of tactile sensing interfaces
- What should I do if the servo motor shakes? What causes the servo motor to shake quickly?
- 【Brushless Motor】Analysis of three-phase BLDC motor and sharing of two popular development boards
- Midea Industrial Technology's subsidiaries Clou Electronics and Hekang New Energy jointly appeared at the Munich Battery Energy Storage Exhibition and Solar Energy Exhibition
- Guoxin Sichen | Application of ferroelectric memory PB85RS2MC in power battery management, with a capacity of 2M
- Analysis of common faults of frequency converter
- In a head-on competition with Qualcomm, what kind of cockpit products has Intel come up with?
- Dalian Rongke's all-vanadium liquid flow battery energy storage equipment industrialization project has entered the sprint stage before production
- Allegro MicroSystems Introduces Advanced Magnetic and Inductive Position Sensing Solutions at Electronica 2024
- Car key in the left hand, liveness detection radar in the right hand, UWB is imperative for cars!
- After a decade of rapid development, domestic CIS has entered the market
- Aegis Dagger Battery + Thor EM-i Super Hybrid, Geely New Energy has thrown out two "king bombs"
- A brief discussion on functional safety - fault, error, and failure
- In the smart car 2.0 cycle, these core industry chains are facing major opportunities!
- The United States and Japan are developing new batteries. CATL faces challenges? How should China's new energy battery industry respond?
- Murata launches high-precision 6-axis inertial sensor for automobiles
- Ford patents pre-charge alarm to help save costs and respond to emergencies
- New real-time microcontroller system from Texas Instruments enables smarter processing in automotive and industrial applications
- Type-C interface display solution
- Is there any module similar to Yiweilian?
- How to choose the right operational amplifier
- How to use a switching boost chip to solder a circuit to achieve 5-24V output
- Here is a basic CAD shortcut key
- [GD32L233C-START Review] 1. Unboxing + Environment Setup
- Maxim Basic Analog IC APP download helps you innovate analog design!
- How is the internal low-pass filter of Bh1415 designed? How is the 150pf connected to pin 3 determined?
- Its automobile inner wheel difference safety warning system
- Motor drive