In order to cope with climate change and reduce travel pressure, the country has introduced a series of policies, including the implementation of the "National VI" emission standard, which is called the "strictest" emission standard in history. In fact, since the implementation of the "National VI" standard, many car owners have said that exhaust emissions have been reduced by half, but the power of the car has also been significantly reduced compared to before, and even fuel consumption has increased. It is imperative to reduce automobile emissions and fuel consumption. To achieve this goal, one way is to adopt hybrid power, that is, to add an electric motor driven by a second battery to the drive train of a gasoline or diesel vehicle.
传统的电子化采用一个高压电池,电压通常在 300~400 V 之间的,耦合至高性能电动机。这些“全混合动力”汽车可显著提高燃油效率,但也会大大增加成本和车身重量。而“插电式”混合动力汽车,即电池通过交流电源插座充电,也具有类似的缺点。
An alternative is the “mild hybrid electric vehicle” (MHEV), which uses a small 48 V battery to drive an electric motor, allowing for faster acceleration and greater low-end torque while still improving fuel economy and with only modest increases in cost and complexity. The benefits of mild hybrid systems are so popular with consumers that IHS Markit analysts predict that 48 V mild hybrids will account for nearly 50% of hybrid vehicle sales by 2025. The lower cost of 48 V systems also makes them attractive to automakers.
The addition of a 48 V Li-ion battery means that MHEVs are dual voltage vehicles, which creates unique design challenges, primarily in managing the battery charge and discharge cycles while maintaining system efficiency. In this article, we will discuss these challenges and explore the benefits that power converters can gain from using automotive power modules and new wide bandgap transistors based on wide bandgap technology.
48 V Architecture
The most basic hybrid system (see the image below) includes a battery, an integrated starter generator (ISG), a 48 V to 12 V converter, and one or more 48 V loads, just like a stable system. Because 48 V mild hybrid systems retain a 12 V battery and multiple 12 V loads, these systems will continue to use a dual voltage architecture for the foreseeable future.
48 V mild hybrid system
The ISG is responsible for the vehicle's power supply, vehicle launch and energy recovery during braking.
The 12 V battery portion of the system remains the same except that there is no 12 V alternator. Since there is no 12 V power generator in the ICE, a bidirectional converter is required to convert power between the 48 V system and the 12 V system.
MHEV bidirectional converter operation mode
The bidirectional converter has multiple operating modes. During vehicle startup, the ISG is powered by the 48 V Li-Ion battery. If the 48 V battery is low or does not provide enough power (e.g. due to low temperatures), the converter will operate in boost mode, using the 12 V battery to provide additional starting current. Normally, the engine start/stop function will be inhibited until all systems have reached normal operating temperature, at which point the vehicle will begin a normal restart.
When the vehicle has reached normal temperature and is being driven, but no additional acceleration is required, the converter will operate in buck mode to charge the 12 V battery from the 48 V battery and power the 12 V loads. When additional power is required, the converter will switch again to boost mode to provide supplemental power to the ICE, reducing fuel consumption and overall emissions.
Converter Topology
48 V to 12 V converters typically have a wide power range of (1~3) kW. To maintain high efficiency in this range, multi-level interleaved buck-boost converters are the most popular choice.
The buck topology provides the voltage step-down, in this case from 48 V to 12 V, while the boost topology provides the opposite power conversion. The synchronous topology keeps the power switch fully on most of the time in both modes, increasing the overall efficiency of the converter.
A multiphase interleaved design connects several identical converter phases in parallel (see the image below, "Bidirectional Converter - Single Phase" for a single-phase example) to act as a single high-power converter. Under heavy load conditions, all phases operate, but during light loads, a battery disconnect switch can be used to turn off some loads, reducing losses and increasing efficiency. Each phase produces an output current at a slightly different phase angle, reducing ripple on the output capacitors. Using interleaved converters instead of a single large converter means that each phase has a smaller current, reducing stress on the power switches, conductors, and inductors (see the image below, "Multiphase Buck-Boost Converter in Configuration").
Bidirectional Converter - Single Phase
Multiphase Buck-Boost Converter in Interleaved Configuration
The main blocks in this type of converter include the power disconnect switch, buck-boost half-bridge, current sensing stage, main inductor and load disconnect switch.
The synchronous buck-boost converter is actually two switching circuits combined into a single stage. The power switch controls the current flow in the main energy conversion element, the inductor. The inductor current is the main variable that needs to be controlled as it is critical to ensure excellent system accuracy.
The direction of the inductor current determines the source current direction, and therefore which battery receives the current. The system controller determines the current direction by generating the appropriate switching pattern (see the image below).
Basic Buck-Boost Conversion
Converter Design
The main circuit elements required are summarized in Table 1. Both the source disconnect stage and the load disconnect stage can use either discrete MOSFETs or integrated MOSFET power modules. The main purpose of these stages is to isolate the input and output of each interleaved stage from the other stages and the 48 V (source) and 12 V (load) batteries, respectively, using a back-to-back switch configuration. Since these MOSFETs operate at floating voltage potential, each device is controlled by a gate driver with high-side drive capabilities. The MOSFETs may need to remain conductive for a longer period of time and therefore must be able to conduct 100% of the time.
Table 1. Key functional blocks of buck-boost converter for dual-voltage MHEV system
The buck-boost stage is the heart of the converter and consists of two MOSFET devices in a half-bridge configuration connected to a power inductor. These MOSFETs must be controlled by high-side and low-side gate drivers that can be packaged separately or co-packaged into a dual driver IC. Alternatively, this stage can be implemented using a small automotive power module (APM) (see the image below).
Design based on automotive power modules
This integrated power module from ON Semiconductor features low thermal resistance, low internal resistance and improved EMI performance in a small AEC-compliant package. No power disconnect circuit is used in this implementation; for individual phase isolation, a load disconnect circuit can be used.
The main power inductor stores the energy for each converter phase and transfers it to either battery. The converter controller is responsible for controlling the two main switches that determine the direction of the current. For this stage to function properly, the current must be accurately measured to adjust the main inductor current appropriately. A shunt resistor based current sense amplifier is best used because of its very low error.
By using a high-precision shunt resistor, we can measure very small differential voltages, typically tens or hundreds of mV, while the shunt voltage itself can vary from 0 to 48 V relative to ground. This large difference means that the amplifier must amplify the small differential signal and provide a high common-mode voltage rejection ratio while being able to withstand transient voltages up to 80 V. Therefore, three amplifier specifications must be carefully selected:
● Common-mode voltage range (the wider the better);
● Input offset voltage (the smaller the better);
● Common mode rejection ratio (the higher the better).
In traditional op amps, the input voltage is limited to ±0.6 V from the supply rails, which greatly limits the common-mode voltage range. In recent years, dedicated current sensing amplifiers have provided a larger common-mode voltage range, up to 80 V. They also provide high precision, with offset voltages as low as 10 µV, enabling accurate and fast current monitoring systems.
Converter design using wide bandgap
As size and efficiency requirements continue to increase in automotive applications, wide bandgap (WBG) devices, such as those from ON Semiconductor, are emerging as an alternative to standard silicon devices. WBG devices can improve efficiency and reduce size while reducing overall system cost.
由于宽禁带器件可以显著降低开关损耗,因此使用宽禁带的降压转换器可实现数倍于典型硅功率晶体管的转换速度,从而最大限度地减少了频率范围内可能影响 AM 无线电接收的电磁干扰。此外,宽禁带晶体管不存在反向恢复损耗,因此不会在硬开关转换期间出现大电流尖峰和功率损耗。
Summarize
With the proliferation of new mild hybrid vehicles, more and more vehicles are equipped with 48 V battery subsystems, requiring the use of 48 V to 12 V converters. While many different converter topologies can be used, the bidirectional interleaved synchronous buck/boost converter is the most widely used due to its simplicity and high efficiency.
The topology can also be designed with multiple interleaved phases, allowing high efficiency over a wide operating range. This is important because 12 V vehicle loads vary greatly over time, and even though the converter needs to be able to operate at maximum load conditions, it rarely remains at this load condition for long. When the load is light, the converter will turn off unnecessary interleaved phases to reduce losses and maintain high efficiency.
Previous article:A brief discussion on three technical routes of solid-state batteries
Next article:Panasonic announces development of cobalt-free electric vehicle batteries
Recommended ReadingLatest update time:2024-11-23 11:57
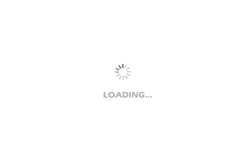
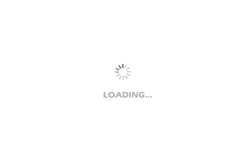
- Popular Resources
- Popular amplifiers
-
Siemens Motion Control Technology and Engineering Applications (Tongxue, edited by Wu Xiaojun)
-
Virtualization Technology Practice Guide - High-efficiency and low-cost solutions for small and medium-sized enterprises (Wang Chunhai)
-
Learning PLC is easy - PLC ladder diagram and statement table with pictures (Li Changjun, Zhou Hua)
-
Operational Amplifier Practical Reference Handbook (Edited by Liu Changsheng, Zhao Mingying, Liu Xu, etc.)
- 2024 China Automotive Charging and Battery Swapping Ecosystem Conference held in Taiyuan
- State-owned enterprises team up to invest in solid-state battery giant
- The evolution of electronic and electrical architecture is accelerating
- The first! National Automotive Chip Quality Inspection Center established
- BYD releases self-developed automotive chip using 4nm process, with a running score of up to 1.15 million
- GEODNET launches GEO-PULSE, a car GPS navigation device
- Should Chinese car companies develop their own high-computing chips?
- Infineon and Siemens combine embedded automotive software platform with microcontrollers to provide the necessary functions for next-generation SDVs
- Continental launches invisible biometric sensor display to monitor passengers' vital signs
- Intel promotes AI with multi-dimensional efforts in technology, application, and ecology
- ChinaJoy Qualcomm Snapdragon Theme Pavilion takes you to experience the new changes in digital entertainment in the 5G era
- Infineon's latest generation IGBT technology platform enables precise control of speed and position
- Two test methods for LED lighting life
- Don't Let Lightning Induced Surges Scare You
- Application of brushless motor controller ML4425/4426
- Easy identification of LED power supply quality
- World's first integrated photovoltaic solar system completed in Israel
- Sliding window mean filter for avr microcontroller AD conversion
- What does call mean in the detailed explanation of ABB robot programming instructions?
- STMicroelectronics discloses its 2027-2028 financial model and path to achieve its 2030 goals
- 2024 China Automotive Charging and Battery Swapping Ecosystem Conference held in Taiyuan
- State-owned enterprises team up to invest in solid-state battery giant
- The evolution of electronic and electrical architecture is accelerating
- The first! National Automotive Chip Quality Inspection Center established
- BYD releases self-developed automotive chip using 4nm process, with a running score of up to 1.15 million
- GEODNET launches GEO-PULSE, a car GPS navigation device
- Should Chinese car companies develop their own high-computing chips?
- Infineon and Siemens combine embedded automotive software platform with microcontrollers to provide the necessary functions for next-generation SDVs
- Continental launches invisible biometric sensor display to monitor passengers' vital signs
- DSP C6000 addressing mode
- Detailed explanation of third-order intermodulation distortion and testing
- [Mill Edge AI Computing Box FZ5 Review] First experience with "object detection"
- Schematic diagram of BLDC (PMSM) controller based on STM32103x
- 2.10 Relays, solid-state relays
- Raspberry Pi Pico Documentation
- 【Beetle ESP32-C3】Hardware Analysis
- Design Method of AC/DC PWM Flyback Converter
- Design of Accelerometer Temperature Control System Based on DSP
- Technology that Industrial Switches Don’t Know