Manufacturers of cars, trucks, buses and motorcycles are rapidly electrifying their vehicles to improve the fuel efficiency of internal combustion engines and reduce carbon dioxide emissions. There are many electrification options, but most manufacturers are not choosing a full hybrid powertrain, but rather a 48-volt mild hybrid system. A mild hybrid system has a 48-volt battery in addition to the traditional 12-volt battery.
This can increase the amount of power by 4 times (P = V • I) for heavy loads such as catalytic converters. The 48V system can power the hybrid engine, improving vehicle performance while saving fuel and accelerating faster and more smoothly. The additional power can not only support the steering, braking and suspension systems, but also add new safety, entertainment and comfort features.
Introducing a 48-volt mild hybrid system, once designed, offers significant advantages. Overcoming the hesitation to modify the long-standing 12-volt power delivery network (PDN) may be the biggest challenge. Changing the power supply often requires new technology that must be extensively tested, and may require new suppliers who can deliver the power to the automotive industry’s high safety and quality standards.
But the data center industry is finding in its move to 48V PDN that the benefits far outweigh the conversion costs. For the automotive industry, 48V mild hybrid systems offer a path to quickly introduce new vehicles with lower emissions, longer range, and lower fuel consumption. In addition, it can provide exciting new design options for improving performance characteristics and reducing CO2 emissions.
How to maximize the 48V power delivery network
Adding a 48V battery to power heavier powertrain and chassis system loads provides engineers with a variety of options. There is now a choice to add systems that can handle 48V input directly, or to retain existing 12V electromechanical loads such as pumps, fans and motors without converting 48V to 12V through a regulated DC-DC converter. To manage change and risk, existing mild hybrid power delivery systems have gradually added 48V loads while still using large centralized multi-kilowatt 48V to 12V converters to provide 12V power to 12V loads throughout the vehicle. However, this centralized architecture not only does not fully exploit the benefits of the 48V PDN, but also does not take advantage of the advanced converter topologies, control systems and packaging that are now available.
Most of these centralized DC-DC converters (Figure 1) are bulky because they use an older, low-frequency switching PWM topology. In addition, they present a single point of failure for a number of critical powertrain systems.
Another architecture to consider is distributed power using modular power components (Figure 2). This power architecture uses smaller, lower-power 48-to-12V converters to distribute power throughout the vehicle close to the 12V loads. The simple power equations P = V • I and PLOSS = I2R illustrate why 48V distribution is more efficient than 12V.
For a given power level, a 48V system uses four times less current and 16 times less power than a 12V system. At one-quarter the current, cables and connectors can be smaller, lighter, and less expensive. In addition, a distributed power architecture has significant thermal management and power system redundancy advantages (Figure 4).
Advantages of modular components in distributed architecture
The modular approach to distributed power generation (Figure 5) is highly scalable.
The battery's 48V output is distributed to various high-power loads in the car, maximizing the benefits of lower current (4x) and lower power consumption (16x), resulting in a smaller, lighter PDN. Based on load power analysis of different distributed loads, a module can be designed and certified for appropriate power granularity and scalability for parallel arrays.
In this case, it is a 2kW module. As mentioned earlier, granularity and scalability are system-dependent. N+1 redundancy can also be achieved at a significantly reduced cost by using distributed modules instead of large centralized DC-DC converters. This approach still has advantages if the load power consumption changes during the vehicle development phase. Engineers can add or remove modules without modifying the entire completed custom power supply. Another design advantage is reduced development time because the modules are already approved and certified.
Implementing a distributed modular 48V architecture in higher voltage battery systems
Pure electric vehicles or high-performance hybrid vehicles can use high-voltage batteries because of the high power requirements of the powertrain and chassis systems. 48V SELV PDN still has significant advantages for OEMs, but now power system designers have the additional challenge of high-power 800V or 400V to 48V conversion.
Additionally, this high power DC-DC converter also requires isolation, but does not require regulation. One of the big advantages of a decentralized 48V to 12V converter arrangement is better regulation. The upstream high power converter can use a fixed ratio topology by using a regulated PoL converter. This is a huge advantage because a wide input to output voltage range of 16:1 or 8:1 is available for 800/48 and 400/48 respectively. Using a regulated converter in this range is not only very inefficient, but also creates a big problem for thermal management.
Decentralizing this high voltage isolated converter is difficult and expensive due to safety requirements when distributing 400V or 800V power. However, high power centralized fixed ratio converters can be designed using power modules instead of large “silver box” DC-DC converters.
Power modules with appropriate granularity and scalability can be developed and then easily paralleled for a wide range of vehicles with different powertrain and chassis electrification requirements. In addition, Vicor fixed ratio bus converters (BCM®) are bidirectional, supporting a variety of energy regeneration schemes. BCMs use a sine amplitude converter (SAC™) high frequency soft switching topology to achieve efficiencies of more than 98%. They also have a power density of 2.6kW/in3, which can significantly reduce the size of centralized high voltage converters.
Vicor is a supplier to the automotive market, delivering innovative and state-of-the-art 48V solutions. A distributed, modular approach to automotive power architecture simplifies complex power delivery challenges, improving performance, productivity and time to market. Vicor is a leader in 48V power conversion, continuously innovating power architectures, power conversion topologies, control systems and packaging.
Previous article:Analog Devices and Hyundai Motor Company Collaborate to Deliver Industry's First All-Digital Road Noise Cancellation System
Next article:Waymo launches AI 'content search' tool to let self-driving cars quickly identify objects
Recommended ReadingLatest update time:2024-11-16 12:25
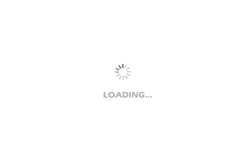
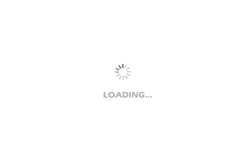
- Popular Resources
- Popular amplifiers
-
Siemens Motion Control Technology and Engineering Applications (Tongxue, edited by Wu Xiaojun)
-
Operational Amplifier Practical Reference Handbook (Edited by Liu Changsheng, Zhao Mingying, Liu Xu, etc.)
-
Detailed explanation of big data technology system: principles, architecture and practice (Dong Xicheng)
-
100 Examples of Microcontroller C Language Applications (with CD-ROM, 3rd Edition) (Wang Huiliang, Wang Dongfeng, Dong Guanqiang)
- Car key in the left hand, liveness detection radar in the right hand, UWB is imperative for cars!
- After a decade of rapid development, domestic CIS has entered the market
- Aegis Dagger Battery + Thor EM-i Super Hybrid, Geely New Energy has thrown out two "king bombs"
- A brief discussion on functional safety - fault, error, and failure
- In the smart car 2.0 cycle, these core industry chains are facing major opportunities!
- The United States and Japan are developing new batteries. CATL faces challenges? How should China's new energy battery industry respond?
- Murata launches high-precision 6-axis inertial sensor for automobiles
- Ford patents pre-charge alarm to help save costs and respond to emergencies
- New real-time microcontroller system from Texas Instruments enables smarter processing in automotive and industrial applications
- Innolux's intelligent steer-by-wire solution makes cars smarter and safer
- 8051 MCU - Parity Check
- How to efficiently balance the sensitivity of tactile sensing interfaces
- What should I do if the servo motor shakes? What causes the servo motor to shake quickly?
- 【Brushless Motor】Analysis of three-phase BLDC motor and sharing of two popular development boards
- Midea Industrial Technology's subsidiaries Clou Electronics and Hekang New Energy jointly appeared at the Munich Battery Energy Storage Exhibition and Solar Energy Exhibition
- Guoxin Sichen | Application of ferroelectric memory PB85RS2MC in power battery management, with a capacity of 2M
- Analysis of common faults of frequency converter
- In a head-on competition with Qualcomm, what kind of cockpit products has Intel come up with?
- Dalian Rongke's all-vanadium liquid flow battery energy storage equipment industrialization project has entered the sprint stage before production
- Allegro MicroSystems Introduces Advanced Magnetic and Inductive Position Sensing Solutions at Electronica 2024
- Car key in the left hand, liveness detection radar in the right hand, UWB is imperative for cars!
- After a decade of rapid development, domestic CIS has entered the market
- Aegis Dagger Battery + Thor EM-i Super Hybrid, Geely New Energy has thrown out two "king bombs"
- A brief discussion on functional safety - fault, error, and failure
- In the smart car 2.0 cycle, these core industry chains are facing major opportunities!
- The United States and Japan are developing new batteries. CATL faces challenges? How should China's new energy battery industry respond?
- Murata launches high-precision 6-axis inertial sensor for automobiles
- Ford patents pre-charge alarm to help save costs and respond to emergencies
- New real-time microcontroller system from Texas Instruments enables smarter processing in automotive and industrial applications
- I would like to ask you about the closed-loop control of the motor encoder
- How to protect privacy using Bluetooth
- Tesla Robot Optimus Prime Conference Uncut 4K HD First Episode
- O-RAN development trends, reference architecture, and interoperability testing
- Qorvo PAC series highly integrated motor control chips and applications
- Five skills required for RF test engineers
- 【GD32L233C-START Review】Display driver for color OLED screen
- Would you choose the popular outdoor power supply?
- Solution to severe static heating of wireless network card
- China's latest classification catalogue of medical devices (No. 104, 2017)