1 Introduction
In medicine, for lumbar diseases such as lumbar disc herniation, physical traction is usually used as a conservative treatment method. Portable and adjustable traction devices can be operated by patients themselves. They are simple and easy to use, suitable for small and medium-sized hospitals and more suitable for long-term rehabilitation at home. The existing portable and adjustable traction devices produced domestically include manual bracket traction and mechanical traction. These traction devices are manually controlled and monitored. The operation is laborious and cannot last for a long time. It is not intuitive. The adjustment is difficult. The traction force generated by the traction device is difficult to maintain accurately. There is no automatic monitoring device, which brings many inconveniences to patients and medical staff. This requires the use of an electromechanical physiotherapy automation system. For this reason, this paper designs a new type of lumbar traction device. It uses the AT89C5l single-chip microcomputer as the microprocessor, cooperates with other auxiliary circuits and is tractioned by a DC motor. Thereby achieving physical therapy for lumbar spine disease. Its single-chip microcomputer control system can ensure the accurate quantification of traction treatment actions, and the traction force and traction time required for traction treatment can be adjusted. It can be precisely controlled and displayed in real time, and the entire traction process is completed automatically.
2 Hardware Implementation of Lumbar Traction Device
The main tasks of the instrument are: keyboard key detection, display of operation setting information and running status, detection and control of pulling force signals, relay control and drive of traction motor, etc. Traction force monitoring and control is the main research goal of this system and the fundamental guarantee of the stability and reliability of this system. According to the requirements of this system, AT89C51 single-chip microcomputer is used as the main control chip. A pulling load sensor is used to detect the traction force value.
2.1 Overall hardware design
Figure 1 shows the hardware composition of the lumbar traction instrument system. The system uses AT89C51 as the main control MCU, which mainly includes the traction force acquisition and detection unit circuit, the traction motor adjustment control circuit, the keyboard control and LED display unit circuit, the system power supply circuit, the alarm circuit and the traction device. The analog signal output by the tension sensor is processed by the signal conditioning circuit, sent to the AID converter to convert it into a digital quantity and then sent to the AT89C51. The single-chip microcomputer makes a judgment based on the traction force and traction time set by the user, generates the pulse signal required to drive the traction motor, and adjusts the control motor and traction device. As a result, the instrument is in three states when working: traction operation, traction holding and traction relaxation. And the monitoring and display of traction force and traction time are realized.
Figure 1 Overall block diagram of the tractor hardware circuit system
2.2 Partial Hardware Circuit Principle
The lumbar traction device uses the AT89C51 single-chip microcomputer as the system control unit, and uses its control capability to realize real-time detection of traction force and monitor the traction force through the LED digital display unit, and realize the drive control of the motor. The conventional unit circuits of the single-chip microcomputer system, such as keyboard design, external memory expansion, and the design and implementation of analog-to-digital conversion interface circuits, are introduced in detail in many example development materials and will not be introduced here. This article aims to use the single-chip microcomputer to realize the development idea of the new application case of the lumbar traction device. The following mainly analyzes the design and implementation of the peripheral measurement and motor control interface circuit.
2.2.1 Principle of traction force collection and detection
The traction force acquisition detection uses a pull-type load sensor as the detection sensor, and the traction force value is obtained by amplification, AID converter conversion and sending to the single-chip microcomputer for counting. The traction device converts the tension on the sensor into a voltage value proportional to it. The strain resistance element of the sensor is shown in Figure 2. The initial resistance of the four strain gauges is equal, and differential cloth and full bridge wiring are used. Because when the sensor is subjected to force, the resistance change direction of the strain resistors Rl and R2 is the same, and the resistance change direction of R3 and R4 is the same. By using differential cloth and full bridge wiring. The voltage value converted by the force on the sensor can be accurately output. After the differential pressure output of the sensor is amplified by the amplifiers OP07 and TL062, the output is sent to the AID converter for data sampling and processing. OP07 is a low drift differential amplifier. We use it as the first stage of amplification. It can accurately amplify the input from the sensor as small as 10μV, and well suppress the interference of common-mode signals; for the second stage amplification, we use a dual-channel operational amplifier TL062, and use the first channel to form a voltage follower to reduce noise and buffer in this circuit. Therefore, the signal output by OP07 passes through this circuit and enters the second channel in a proportional and stable manner. The output of OP07 is amplified by the second channel, and the positive input of the second channel is connected according to Figure 3. By adjusting RW, the positive input of TL062 can be adjusted to set the output zero point, so that the output signal of the analog part is within the linear working range of the A/D converter.
Figure 2 Internal structure of the sensor
Figure 3 Traction force acquisition detection circuit
2.2.2 Principle of traction control
The control mechanism used in traction control is composed of a motor, a traction wheel, a ratchet relay, etc. It is a small electric traction system. Figure 4 shows the mechanism diagram of the electric traction part. We use the motor to drive the roller (called the traction wheel) to rotate through the transmission method. The rotation of the roller drives the traction belt wrapped around it to generate traction. In order to achieve the purpose of traction of the traction object. In the figure, the ratchet and the traction wheel are directly connected to the main shaft of the motor. Usually, in the electric traction system using the motor as the power for traction, the motor is controlled by a certain automatic control method. In this device, we also use a single-chip microcomputer and relay control method to realize the control of the motor. In order to maintain the traction force, the control system uses a ratchet relay to achieve it, that is, the ratchet relay is turned off, so that the ratchet cannot rotate. At this time, the pulling force output by the motor is in a maintained state. When the input set intermittent traction time is reached, the ratchet relay is turned on, the ratchet is loosened, the ratchet rotates freely, the traction motor is in a relaxed state, and the traction force is cancelled. When the input set intermittent relaxation time is reached, the ratchet relay is turned on and the motor is started to enter the traction operation state. The control circuit of the motor and relay is shown in Figure 5. The motor start and stop control signal comes from pin P1.3, and the relay on and off control signal comes from pin P1.6.
Figure 4: Electric traction mechanism diagram
3 Software Design
In this software design, the system control program consists of the main program, interrupt service program and other subprograms. The modular programming technology is used in the design. According to the functions of the system, the entire program is divided into the following modules according to the functions completed by each module: main program, interrupt service subprogram, motor traction operation subprogram, function setting subprogram, display subprogram, data processing submodule and traction time analysis subprogram. The system program flow is shown in Figure 6. The system functions are realized in the form of interrupts.

Figure 5 Motor and relay drive circuit
Figure 6 Flow chart of the lumbar traction system
The main program is initialized first, allowing all interrupts to be opened. The timer interrupt is also opened. The main program waits for and responds to interrupts at any time. In the case of no interrupt, the detection program is run to detect whether the system enters the function setting or the traction motor operation processing state. When a timer interrupt is generated, the program jumps to the timer interrupt service subroutine. The keyboard scanning, data acquisition, display and traction time analysis subroutines are run. When the interrupt subroutine is finished, it returns to the main program call.
3.1 Main program design
The main software program is the monitoring program of the system. It mainly completes the initialization, controls the flow of the program, calls subroutines and other functions. Its flow chart is shown in Figure 6. After power-on reset, the program starts to execute. The first is the initialization work, which includes:
·A/D sampling result, BCD conversion result, tension setting value, these storage units’ initial value settings;
· The initial values of the 10-second generator counter, timed on counter, timed off counter, total traction time counter, and timed on preset value, timed off preset value, and total traction time preset value are not set:
Setting the interrupt counter value, adjusting it can change the interrupt response time:
· Set each bit 00H~07H in the 20H unit to 0. Set the motor control port P1.3 to 1 (indicating the motor is off), 17H to 1 (indicating the timed off state), and 0DH to 1 (setting the waiting light to light up):
Timer 0 interrupt service initialization: timer working mode and its initial value setting
Next, check the bit address 00H to determine whether the motor is on. If yes (00H=1), execute the corresponding function of the motor traction operation processing program. If no (00H=0), go to the next step. Check the bit address 01H to determine whether the function key on the keyboard is pressed. If yes (01H=1), execute the corresponding function of the program parameter setting processing. If no (01H=0), return to the detection of whether the motor is on. The main program is executed in a loop.
The flow of the main program is relatively simple, and all the functions that need to be completed are implemented by subroutines.
4 Conclusion
The innovation of the author of this article is to design a lumbar traction device that can accurately control the traction force and traction time and can display them in real time. The traction process can be completed automatically, and the patient can make appropriate adjustments by himself during the treatment process. Because the system has simple hardware, low cost, high integration, good stability, convenient debugging, strong anti-interference ability, and can realize automatic control of traction force, it has certain practical value, but it still needs to be improved before it can be put into practical use. In order to truly promote the application of intelligent lumbar traction devices, new devices need to be used to make the circuit more compact. Certain technical measures should be taken to improve the mechanical structure design of the traction device, strengthen the reliability of the instrument, and increase the traction force detection in the traction force maintenance stage. When there is a deviation from the set value, the traction system can be controlled to automatically compensate. This is a problem worth exploring.
Through the experimental test system, it is detected that the functions of sensors, control actuators, displays, alarms, etc. are normal and the performance meets the predetermined design requirements.
Previous article:Design of customizable human-computer interaction interface based on P89C51RD2
Next article:Micro Programmable Controller Based on AT89C51 Single Chip Microcomputer
Recommended ReadingLatest update time:2024-11-16 22:01
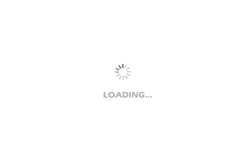
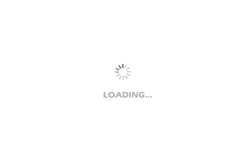
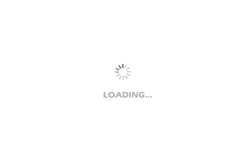
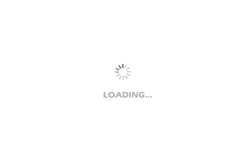
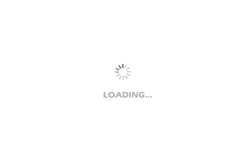
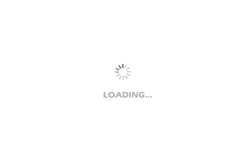
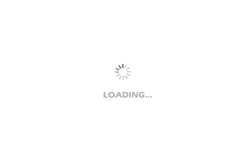
- Popular Resources
- Popular amplifiers
-
西门子S7-12001500 PLC SCL语言编程从入门到精通 (北岛李工)
-
Siemens Motion Control Technology and Engineering Applications (Tongxue, edited by Wu Xiaojun)
-
MCU C language programming and Proteus simulation technology (Xu Aijun)
-
100 Examples of Microcontroller C Language Applications (with CD-ROM, 3rd Edition) (Wang Huiliang, Wang Dongfeng, Dong Guanqiang)
Professor at Beihang University, dedicated to promoting microcontrollers and embedded systems for over 20 years.
- Innolux's intelligent steer-by-wire solution makes cars smarter and safer
- 8051 MCU - Parity Check
- How to efficiently balance the sensitivity of tactile sensing interfaces
- What should I do if the servo motor shakes? What causes the servo motor to shake quickly?
- 【Brushless Motor】Analysis of three-phase BLDC motor and sharing of two popular development boards
- Midea Industrial Technology's subsidiaries Clou Electronics and Hekang New Energy jointly appeared at the Munich Battery Energy Storage Exhibition and Solar Energy Exhibition
- Guoxin Sichen | Application of ferroelectric memory PB85RS2MC in power battery management, with a capacity of 2M
- Analysis of common faults of frequency converter
- In a head-on competition with Qualcomm, what kind of cockpit products has Intel come up with?
- Dalian Rongke's all-vanadium liquid flow battery energy storage equipment industrialization project has entered the sprint stage before production
- Allegro MicroSystems Introduces Advanced Magnetic and Inductive Position Sensing Solutions at Electronica 2024
- Car key in the left hand, liveness detection radar in the right hand, UWB is imperative for cars!
- After a decade of rapid development, domestic CIS has entered the market
- Aegis Dagger Battery + Thor EM-i Super Hybrid, Geely New Energy has thrown out two "king bombs"
- A brief discussion on functional safety - fault, error, and failure
- In the smart car 2.0 cycle, these core industry chains are facing major opportunities!
- The United States and Japan are developing new batteries. CATL faces challenges? How should China's new energy battery industry respond?
- Murata launches high-precision 6-axis inertial sensor for automobiles
- Ford patents pre-charge alarm to help save costs and respond to emergencies
- New real-time microcontroller system from Texas Instruments enables smarter processing in automotive and industrial applications
- The scariest camera in history! Even thieves would cry when they see it...
- Embedded SBC plays AI reasoning
- Popular must-read! Can't these 20 amplifier Q&A selections help you solve your problems?
- Fudan Micro FM1935 self-polling door lock development information
- Why are PCBs mostly green?
- 【TI Course】What is the resolution within 5 meters?
- Class AB amplifiers are replaced by Class D amplifiers
- Design of Internet Radio Based on RVB2601
- About MSP430 MCU serial communication data loss
- ccs5.5 printf console output cannot be displayed