O Introduction
Clothing is an important part of people's lives. In addition to appearance factors such as style, color, and gloss, comfort is also an important part of clothing functionality. The so-called clothing comfort refers to the performance of clothing that meets the requirements of the human body and eliminates any uncomfortable factors after the human body is dressed. Clothing pressure can be divided into two types: vertical pressure formed by the weight of the clothing itself and restraint pressure caused by the clothing tightly wrapped around the body.
Traditional clothing pressure comfort test methods mainly include: fluid pressure method, resistance method, and plaster method. Among them, the method of using a fluid mercury pressure gauge or a hydraulic press to measure clothing pressure is simple and direct, but the accuracy is low, especially dynamic measurement is quite difficult; the resistance measurement method is to insert a resistance strain gauge sensor into the clothing, and the strain gauge is deformed due to clothing pressure, resulting in a change in resistance value, thereby converting the pressure change into a changing voltage signal, and the clothing pressure test result is obtained by measuring the changing voltage value. This method has high test accuracy and stable results, but it is easily affected by external conditions, and it is difficult to measure clothing pressure dynamically; the plaster method is mainly realized through model detection. This method can measure the natural pressure value close to that when wearing clothes, but it cannot perform clothing pressure tests during continuous movements, and the plaster model is difficult to make. The above various test methods are limited by time and space, and it is difficult to adapt to the needs of different test conditions, and the accuracy of the test data is not high, and there is no data storage function.
In view of the defects of traditional testing methods, this system uses AVR low-power, high-performance single-chip microcomputer as the core CPU, selects the new Flexiforce sensor developed by Tekscan Company of the United States to measure clothing pressure, and designs it into a portable clothing pressure testing system that can perform dynamic and static measurements and has data storage functions.
1 System composition
The functional modules of this system mainly include: parameter detection module, data display module, storage module, real-time clock module, PC communication module and control module. The clothing pressure detection adopts a multi-point test method, that is, multiple pressure sensors are connected to the test module. After each sensor completes a data test, its data is sent to the core CPU, and then the main chip performs calculations on the data, and stores the data in the memory according to certain rules, and displays the data on the LCD screen in real time. After the test is completed, the data in the memory can be read into the PC through the serial port for analysis and storage. The control module mainly completes the setting of system functions. The system structure is shown in Figure 1.
2 Functional module design
2.1 Microprocessor
The microprocessor of this system adopts ATmegal6L from the AVR series of high-performance and low-power microcontrollers, which integrates timers, ADC, on-chip clock, USART, SPI, TWI, and 21 interrupt sources. The power consumption of ATmegal6L at 1 MHz, 3V, and 25℃ is 1.1 mA in normal mode, 0.35 mA in idle mode, and less than μA in power-down mode. The AVR microcontroller adopts a large fast access register group, a fast monotonic instruction system, and a single-stage pipeline technology, which enables its processing speed to reach 1 MIPS/MHz. The internal programmable FLASH is 16 KB, and the number of erase and write times can reach 10,000 times. AVR integrates 8-channel 10-bit successive approximation ADC. The ADC is connected to an 8-channel analog multiplexer and can
sample 8 single-ended input voltages from port A. The device also supports 16 differential voltage input combinations and has programmable gain stage control function. Its powerful data processing capability and highly integrated core fully meet the design requirements of the system.
2.2 Clothing pressure detection module
This system uses the new Flexiforce sensor developed by Tekscan in the United States to measure clothing pressure. Compared with the sensors used in traditional clothing pressure testing systems, the Flexiforce sensor is as thin as paper and has strong flexibility. It can measure the pressure between almost all contact surfaces. It has better characteristics in terms of linearity, hysteresis, drift and temperature sensitivity. According to the clothing pressure value to be measured, the Flexiforce A201 pressure sensor with a pressure range of 0 to 1 lb (4.4 N) is selected. The Flexiforce A201 pressure sensor consists of two layers of film, each of which is covered with a silver conductor and coated with a layer of special pressure-sensitive semiconductor material. The two films are pressed together to form a sensor. The silver conductor extends from the sensing point to the connection end of the sensor. The sensor point of Flexiforce A201 acts as a resistor in the circuit. When an external force acts on the sensing point, the resistance of the sensor point changes proportionally with the external force. When the sensor is not subjected to force, the resistance of the sensing point is the largest. The greater the pressure, the smaller the resistance of the sensing point.
The output signal of the pressure sensor is in the millivolt level, and the detected signal needs to be amplified before it can be input to the CPU port. The amplifier circuit of the Flexiforce sensor is shown in Figure 2, RF=R1+RF1, Vout=-V0(RF+RS1). Among them, RF1 is a variable resistor, and its resistance change corresponds to the change of the external force applied to the sensor. This circuit uses the MC34071 amplifier. The sensor passes through the amplifier, and the output voltage value is Vout. After the corresponding relationship between the calibrated pressure and voltage, the measured clothing pressure value can be obtained.
This system uses 8 Flexiforce A201 pressure sensors, which are directly connected to the PA port of ATmega16L in parallel.
2.3 Data storage module
The system designs a data storage module. Since the space occupied by the system for storing data is not very large, the memory uses the AT24C256 chip produced by Atmel, which is a 256 KB data storage device and uses the I2C bus communication method to exchange data with the main CPU.
In order to facilitate better reading of data after testing, a certain storage mode is used to save the data in AT24C256. Therefore, when designing the software, the data transmission protocol is adopted: first transmit the detection channel number, then transmit the test time, and finally transmit the pressure value. The specific transmission format is shown in Figure 3.
The ATmegal6L microcontroller has an I2C communication module integrated inside. Its external port is multiplexed with the PC0 and PC1 ports. When using this port, you only need to connect a pull-up resistor to each of the two transmission buses. The I2C communication chip can be directly connected to this port.
2.4 Display module
This system uses SMGl2864 liquid crystal, which is small in size, light in weight, low in power consumption, and high in display quality. It can display 4 channels of collected data at the same time, and a circular display method can be used for 8 channels of data. The displayed data are channel number and pressure data. If the display data is not needed, the function key can be used to turn off the display.
The connection between SMG12864 LCD and ATmegal6L is very simple. The data port is directly connected to the PD port, and the function control terminal is connected to the PB port.
2.5 Serial port module, real-time clock module and function module
The serial port module mainly realizes the communication between the PC and the detection system. The PC can read the data in AT24C256 through the serial port. The system uses the MAX232 serial port communication conversion chip of Maxim.
This system uses the DS1302 real-time clock chip launched by the American DALLAS company. It uses a three-wire serial interface and integrates a programmable calendar clock and 31 bytes of static RAM. The DS1302 clock can automatically compensate for leap years. The DS1302 chip itself also has the function of trickle charging the backup battery, which can effectively extend the service life of the backup battery.
The DS1302 is powered by the system power supply when the system is working normally, and by a dedicated button battery when the system is not working.
The system sets 3 function keys to complete the system time configuration and auxiliary function selection. These auxiliary functions are mainly: one function key is used to display only the time when the system does not need to detect the comfort pressure of clothing. At this time, it can be used as a real-time clock. When a pressure test experiment is required, press this function key to enter the system pressure detection mode.
After the system starts, the whole system is initialized first, and then the function key is tested. If the function key is pressed, the system starts the A/D conversion and stores the detected data in a certain data format in AT24C256. At the same time, the detected data is displayed on the SMG12864 LCD screen in a loop. After the data test is completed, if there is no pressure data detection, the A/D conversion module is turned off, and the data storage port is closed, so the system enters the dormant state.
3 Implementation of pressure comfort detection algorithm
The collected data from the pressure sensor must be processed to obtain a specific and readable clothing comfort pressure value. First, the clothing pressure sensor converts the collected pressure value into an analog voltage value, then converts it into a standard voltage value through A/D, and after the MCU calculates the data, it converts it into a clothing comfort pressure value.
The specific algorithm is as follows:
The actual voltage value calculation formula of ATmegal6L A/D conversion is:
Where: ADC is the result value corresponding to the A/D conversion of the analog voltage value output by the pressure sensor; Vin is the analog voltage value output by the pressure sensor; VREF is the A/D conversion reference voltage value. In order to improve the accuracy, the internal A/D conversion reference voltage of ATmegal6L is selected as 2.56V.
Take G as the actual voltage value obtained by standard A/D conversion after loading the pressure sensor with a 100g weight, then:
Where: F is the clothing pressure, unit: g.
4 Test experiment
After the design of this system is completed, its stability and reliability are tested by testing the change of pressure at a point on the shoulder of the human body after wearing the clothes. The test curve is shown in Figure 4: the pressure change is relatively stable after the initial wearing of the clothes (0~12min); the clothing pressure also changes with time after the arm movement (12~18 min); the pressure value returns to the initial value when the arm stops moving (18~23 min).
5 Conclusion
The experimental results show that the clothing pressure detection system can correctly test the clothing comfort pressure value. It is easy to use, powerful and has excellent performance. It is an ideal platform for clothing testing. It solves the difficulty of not being able to measure dynamic clothing pressure in traditional clothing pressure testing, and has data storage function. The device is small and can be carried around; it has low power consumption and is battery-powered. It can provide a reliable data foundation and basis for improving clothing pressure comfort in the future. Through objective measurement and research of pressure, it will contribute to the development of digital clothing pressure comfort research.
Previous article:Design of ISP1362OTG based on AVR microcontroller
Next article:Design of data acquisition system for laser scanning car body coordinate measurement
Recommended ReadingLatest update time:2024-11-16 16:39
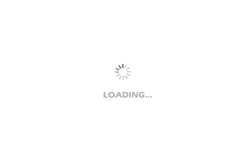
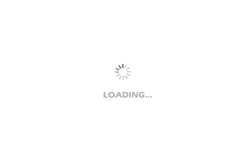
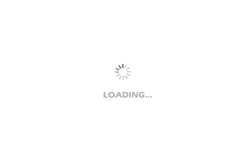
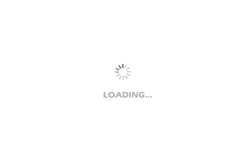
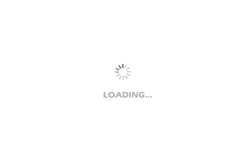
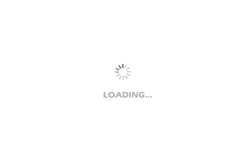
- Popular Resources
- Popular amplifiers
-
Principles and Applications of Single Chip Microcomputers 3rd Edition (Zhang Yigang)
-
Metronom Real-Time Operating System RTOS for AVR microcontrollers
-
Learn C language for AVR microcontrollers easily (with video tutorial) (Yan Yu, Li Jia, Qin Wenhai)
-
ATmega16 MCU C language programming classic example (Chen Zhongping)
Professor at Beihang University, dedicated to promoting microcontrollers and embedded systems for over 20 years.
- Innolux's intelligent steer-by-wire solution makes cars smarter and safer
- 8051 MCU - Parity Check
- How to efficiently balance the sensitivity of tactile sensing interfaces
- What should I do if the servo motor shakes? What causes the servo motor to shake quickly?
- 【Brushless Motor】Analysis of three-phase BLDC motor and sharing of two popular development boards
- Midea Industrial Technology's subsidiaries Clou Electronics and Hekang New Energy jointly appeared at the Munich Battery Energy Storage Exhibition and Solar Energy Exhibition
- Guoxin Sichen | Application of ferroelectric memory PB85RS2MC in power battery management, with a capacity of 2M
- Analysis of common faults of frequency converter
- In a head-on competition with Qualcomm, what kind of cockpit products has Intel come up with?
- Dalian Rongke's all-vanadium liquid flow battery energy storage equipment industrialization project has entered the sprint stage before production
- Allegro MicroSystems Introduces Advanced Magnetic and Inductive Position Sensing Solutions at Electronica 2024
- Car key in the left hand, liveness detection radar in the right hand, UWB is imperative for cars!
- After a decade of rapid development, domestic CIS has entered the market
- Aegis Dagger Battery + Thor EM-i Super Hybrid, Geely New Energy has thrown out two "king bombs"
- A brief discussion on functional safety - fault, error, and failure
- In the smart car 2.0 cycle, these core industry chains are facing major opportunities!
- The United States and Japan are developing new batteries. CATL faces challenges? How should China's new energy battery industry respond?
- Murata launches high-precision 6-axis inertial sensor for automobiles
- Ford patents pre-charge alarm to help save costs and respond to emergencies
- New real-time microcontroller system from Texas Instruments enables smarter processing in automotive and industrial applications
- It is easy to travel around the world on your own, travel around the world, live in Korea, live in Korea, travel to the world, travel to the world, move to the top 2.4mm + reach the destination...
- To: Test Engineers! More than 2000 connectors, download a complete 96-page catalog at once!
- Let’s take a look at the performance of this RISC-V MCU with a main frequency of 648M.
- C6455 CSL_EMIF Detailed Explanation
- Application of Single Pair Ethernet in Building Automation
- How to amplify a 3V signal 100 times? See how the ATA-4000 series high voltage power amplifier does it!
- What are the essential technologies for 5G smartphones?
- 【Want Talent】Beijing-3 embedded positions
- EEWORLD University Hall----Introduction to Digital Power Supply
- SPI interrupt and Main usage issues