1. Overview of Watchdog Timer
The purpose of the watchdog timer and PWM timing function is different. Its characteristics are that it requires different receiving signals (some external watchdog chips) or resetting the counter to keep the count value not 0. Once no signal is received for some time, or the count value is 0, the watchdog will send a reset signal to reset the system or generate an interrupt.
The function of the watchdog is to reset the system within a certain time interval after the microprocessor enters an error state due to interference. Therefore, the watchdog is an effective measure to ensure the long-term, reliable and stable operation of the system. Currently, most embedded chips have integrated watchdog timers to improve the reliability of system operation.
The watchdog of the 4412 processor is used to reset the processor when the system is disturbed by a fault. It can also be used as a general 16-bit timer to request an interrupt operation. The watchdog timer generates a reset signal of 128 PCLK cycles. The main features are as follows.
1) General purpose interrupt mode 16-bit timer.
2) When the counter is reduced to 0 (overflow occurs), a reset signal of 128 PCLK cycles is generated.
The functional block diagram of the watchdog timer is as follows:
The watchdog module includes a pre-scale factor amplifier, a divide-by-four frequency divider, and a 16-bit counter. The watchdog clock signal source comes from PCLK. In order to obtain a wide range of watchdog signals, PCLK is first pre-scaled and then divided by the divider. The pre-scale factor and the divider value can be determined by the watchdog control register (WTCON). The pre-scale factor ranges from 0 to 255, and the divider ratio can be 16, 32, 64, or 128. The calculation of the watchdog timer clock period is as follows:
Where Prescaler value is the value of the prescaler amplifier; Divison_factor is the divide-by-four ratio, which can be 16, 32, 64, or 128.
Once the watchdog timer is enabled, the value of the watchdog timer data register (WTDAT) cannot be automatically loaded into the watchdog timer (WTCNT). Therefore, an initial value must be written to the watchdog counter (WTCNT) before the watchdog is started. When the 4412 is debugged with embedded ICE, the reset function of the watchdog timer is not enabled. The watchdog timer can determine whether the current CPU is in the debug state from the CPU core signal. If the watchdog timer determines that the current mode is the debug mode, even if the watchdog generates an overflow signal, it still does not generate a reset signal.
2. Watchdog timer related timers
1. Watchdog timer control register (WTCON)
The contents of the WTCON register include: whether the user starts the watchdog timer, the selection of 4 frequency division ratios, whether interrupts are allowed, whether reset operations are allowed, etc.
If the user wants to use the watchdog timer as a general timer, the interrupt should be enabled and the watchdog timer reset should be disabled.
WTCON is described as follows:
2. Watchdog Timer Data Register (WTDAT)
WTDAT is used to specify the timeout period. After the watchdog disables the reset function and turns on the interrupt enable, the watchdog timer is now a normal timer and is used in the same way as a normal timer. When the reset function is used, the system will reset when the value of WTCNT decreases to 0, so the value of WTCNT cannot be loaded into the watchdog count register (WTCNT). The initial value after reset is 0x8000. WTDAT is described as follows:
3. Watchdog count register (WTCNT)
WTCNT contains the current count value of the counter when the watchdog timer is working. WTCNT is described as follows:
3. Programming of Watchdog Timer
1. Watchdog software programming process
Because the watchdog is an operation to reset or interrupt the system, no peripheral hardware circuit is required. To realize the watchdog function, you only need to operate the watchdog register group, that is, the watchdog control register (WTCON), watchdog data register (WTDAT), and watchdog count register (WTCNT).
The general process is as follows:
1) Set the watchdog interrupt operation, including global interrupt and watchdog interrupt enable and definition of watchdog interrupt vector. If only reset operation is performed, this step does not need to be set.
2) Setting of the watchdog control register (WTCON), including setting the pre-division ratio factor, the division value of the divider, interrupt enable and reset enable, etc.
3) Setting of the watchdog data register (WTDAT) and the watchdog count register (WTCNT).
4) Start the watchdog timer.
2. The specific code is as follows:
#include "exynos_4412.h"
#include "led.h"
#include "pwm.h"
void mydelay_ms(int time)
{
int i, j;
while(time--)
{
for (i = 0; i < 5; i++)
for (j = 0; j < 514; j++);
}
}
//*(volatile unsigned int *)(0x11000c20) = 0;
/*
* Bare metal code, different from the LINUX application layer, must add loop control
*/
void do_irq(void)
{
static int a = 1;
int irq_num;
irq_num = CPU0.ICCIAR&0x3ff; //Get the interrupt number
switch(irq_num)
{
case 57:
printf("in the irq_handlern");
EXT_INT41_PEND = EXT_INT41_PEND |((0x1 << 1)); // Clear GPIO interrupt flag
ICDICPR.ICDICPR1 = ICDICPR.ICDICPR1 | (0x1 << 25); // Clear GIC interrupt flag
break;
case 75:
printf("in the WDT interrupt!n");
WDT.WTCLRINT = 0;
ICDICPR.ICDICPR2 = ICDICPR.ICDICPR2 | (0x1 << 11); // Clear GIC interrupt flag
break;
}
CPU0.ICCEOIR = CPU0.ICCEOIR&(~(0x3ff))|irq_num; //Clear CPU interrupt flag
}
void wdt_init(void)
{
WDT.WTCON = (249 << 8) | (1 << 5) | (1 << 2)|(1 << 0);
WDT.WTDAT = 25000;
ICDDCR = 1; // Enable the distributor
ICDISER.ICDISER2 = ICDISER.ICDISER2 | (0x1 << 11); // Enable the corresponding interrupt to the distributor
ICDIPTR.ICDIPTR18 = ICDIPTR.ICDIPTR18 & (~(0xff << 24))|(0x1 << 24); //Select CPU interface
CPU0.ICCPMR = 255; //Interrupt mask priority
CPU0.ICCICR = 1; // Enable interrupt to CPU
}
int main (void)
{
wdt_init();
printf("hello reset!n");
while(1)
{
WDT.WTCNT = 25000;
mydelay_ms(100);
}
return 0;
}
Previous article:Exynos4412 bare metal development - RTC real-time clock unit
Next article:Exynos4412 bare metal development - UART
Recommended ReadingLatest update time:2024-11-16 17:41
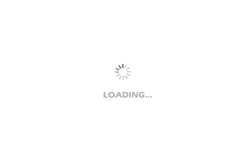
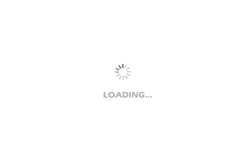
Professor at Beihang University, dedicated to promoting microcontrollers and embedded systems for over 20 years.
- Innolux's intelligent steer-by-wire solution makes cars smarter and safer
- 8051 MCU - Parity Check
- How to efficiently balance the sensitivity of tactile sensing interfaces
- What should I do if the servo motor shakes? What causes the servo motor to shake quickly?
- 【Brushless Motor】Analysis of three-phase BLDC motor and sharing of two popular development boards
- Midea Industrial Technology's subsidiaries Clou Electronics and Hekang New Energy jointly appeared at the Munich Battery Energy Storage Exhibition and Solar Energy Exhibition
- Guoxin Sichen | Application of ferroelectric memory PB85RS2MC in power battery management, with a capacity of 2M
- Analysis of common faults of frequency converter
- In a head-on competition with Qualcomm, what kind of cockpit products has Intel come up with?
- Dalian Rongke's all-vanadium liquid flow battery energy storage equipment industrialization project has entered the sprint stage before production
- Allegro MicroSystems Introduces Advanced Magnetic and Inductive Position Sensing Solutions at Electronica 2024
- Car key in the left hand, liveness detection radar in the right hand, UWB is imperative for cars!
- After a decade of rapid development, domestic CIS has entered the market
- Aegis Dagger Battery + Thor EM-i Super Hybrid, Geely New Energy has thrown out two "king bombs"
- A brief discussion on functional safety - fault, error, and failure
- In the smart car 2.0 cycle, these core industry chains are facing major opportunities!
- The United States and Japan are developing new batteries. CATL faces challenges? How should China's new energy battery industry respond?
- Murata launches high-precision 6-axis inertial sensor for automobiles
- Ford patents pre-charge alarm to help save costs and respond to emergencies
- New real-time microcontroller system from Texas Instruments enables smarter processing in automotive and industrial applications
- 4 discount spots left: STEVAL-SPIN3202 three-phase BLDC motor driver board
- [ART-Pi Evaluation] 4: ATT-Pi builds ModBus simulation environment in RTT Studio environment
- Common asynchronous circuit processing faults in IC design
- 【RPi PICO】Flashing light
- LED life issues
- How big is the driving capability of the DSP chip?
- Analysis and solution of temperature rise factors of CITIC Hua circuit board
- MSP430AFE235
- [RVB2601 Creative Application Development] Three-in-one OLED display for calendar, time, temperature and humidity
- GD32E103 eval board download error