introduce
The STM32F103ZET6 has a 12-bit ADC, which is a successive approximation analog-to-digital converter.
12bits ADC represents the conversion accuracy of ADC. When there is an input reference voltage, ADC inputs the analog signal through the signal line, samples the analog signal, and then stores the sampled digital signal in the data register for software reading (CPU or DMA mode). The stored data is converted according to 12bits after comparison with the reference voltage.
ADC input range: Vref- ≤ Vin ≤ Vref+
ADC Clock
The ADC input clock ADCCLK cannot exceed 14MHz (specified in the Datasheet). It is generated by dividing PCLK2.
Conversion Mode
It supports single conversion and continuous conversion. As the name implies, single conversion only performs one conversion and then writes the value to the data register. Continuous conversion performs ADC operation uninterruptedly and writes the value to the data register.
Channel Description
The ADC has two groups of channels: a regular channel group and an injected channel group.
Rule channel group: equivalent to your normal running program.
Injection channel group: It is equivalent to an interrupt. When your program is running normally, the interrupt can interrupt your execution. Similarly, the conversion of the injection channel can interrupt the conversion of the rule channel. After the injection channel is converted, the rule channel can continue to convert.
In other words, the injection channel can interrupt the regular ADC data conversion currently in progress. For the time being, just understand it as the concept of priority.
● Regular channel group: consists of up to 16 conversions. The regular channels and their conversion order are selected in the ADC_SQRx registers. The total number of conversions in the regular group should be written to the L[3:0] bits of the ADC_SQR1 register.
● Injection channel group: consists of up to 4 conversions. The injection channels and their conversion order are selected in the ADC_JSQR register. The total number of conversions in the injection group should be written to the L[1:0] bits of the ADC_JSQR register.
That is to say, in the regular channel group, 16 analog signals are supported to be input simultaneously, and the analog signals of these channels are sampled to digital signals, and the same is true for the injection channel.
Interrupt Description
● If a regular channel is converted:
─ The conversion data is stored in the 16-bit ADC_DR register
─ The EOC (end of conversion) flag is set
─ If EOCIE is set, an interrupt is generated.
● If an injection channel is converted:
─ The conversion data is stored in the 16-bit ADC_DRJ1 register
─ The JEOC (JEOC End of Conversion) flag is set
─ If the JEOCIE bit is set, an interrupt is generated.
Interrupt Events | Event Flags | Enable control bit |
Rule group conversion completed | EOC | EOCIE |
Injection group conversion completed | J.E.O.C. | JEOTIC |
The analog watchdog status bit is set | AWD | AWDIE |
Channel Scan
This mode is used to scan a group of analog channels.
The scan mode can be selected by setting the SCAN bit in the ADC_CR1 register. Once this bit is set, the ADC scans all channels selected by the ADC_SQRX register (for regular channels) or ADC_JSQR (for injected channels). A single conversion is performed on each channel of each group. At the end of each conversion, the next channel of the same group is automatically converted. If the CONT bit is set, the conversion does not stop on the last channel of the selected group, but continues again from the first channel of the selected group.
If the DMA bit is set, the DMA controller transfers the converted data of the regular group channels to the SRAM after each EOC. The converted data of the injected channels are always stored in the ADC_JDRx register.
calibration
The ADC has a built-in self-calibration mode. Calibration can significantly reduce the accuracy errors caused by variations in the internal capacitor bank. During calibration, an error correction code (digital value) is calculated on each capacitor and this code is used to eliminate the errors introduced on each capacitor in subsequent conversions.
It is recommended to perform a calibration after each power-up.
Before starting calibration, the ADC must be powered off (ADON='0') for at least two ADC clock cycles.
sampling time
The conversion time of ADC is not only related to the ADC clock, but also to the sampling time. ADC uses several ADC_CLK cycles to sample the input voltage. The number of sampling cycles can be changed by the SMP[2:0] bits in the ADC_SMPR1 and ADC_SMPR2 registers. Each channel can be sampled at different times.
The conversion time of ADC is calculated as: Tconv = sampling time + 12.5 cycles
For example: When ADCCLK = 14MHz, the sampling time is 1.5 cycles, Tconv = 1.5 + 12.5 = 14 cycles = 1μs
Environment Description
In the reference voltage, Vref- on the board is directly connected to GND, and Vref+ is connected to Vcc 3.3V.
On the board, use voltage divider resistors for analog input, the resistor is adjustable, and use PC1 port for input
Configuration Process
The configuration process is divided into three stages:
● GPIO port configuration
● DMA configuration
● ADC configuration
GPIO port configuration
static void SK_ADC1GPIOInit(void) { GPIO_InitTypeDef stGpioInit; /* Enable ADC1 and GPIOC clock */ RCC_APB2PeriphClockCmd(RCC_APB2Periph_ADC1 | RCC_APB2Periph_GPIOC, ENABLE); /* Configure PC.01 as analog input */ stGpioInit.GPIO_Pin = GPIO_Pin_1; stGpioInit.GPIO_Mode = GPIO_Mode_AIN; GPIO_Init(GPIOC, &stGpioInit); }
DMA Configuration
DMA configuration uses DMA1 channel, so configure the relevant registers of DMA1:
1. Enable DMA1 clock
2. Reset DMA1
3. Configure the peripheral address and memory address for data transfer
4. Data transfer direction is peripherals --> memory
5. Data transfer size is 1 (half word, 16 bits)
6. Disable memory and peripheral address growth
7. Configure memory data and peripheral data width to 16 bits
8. Configure loop mode
9. Configure priority and disable mem2mem
static void SK_ADC1DMAInit(void)
{
DMA_InitTypeDef stDMA_Init;
/* Enable DMA clock */
RCC_AHBPeriphClockCmd(RCC_AHBPeriph_DMA1, ENABLE);
/* DMA channel1 configuration */
DMA_DeInit(DMA1_Channel1);
stDMA_Init.DMA_PeripheralBaseAddr = ADC1_DR_Address;
stDMA_Init.DMA_MemoryBaseAddr = (u32)&ADC_ConvertedValue;
stDMA_Init.DMA_DIR = DMA_DIR_PeripheralSRC;
stDMA_Init.DMA_BufferSize = 1;
stDMA_Init.DMA_PeripheralInc = DMA_PeripheralInc_Disable;
stDMA_Init.DMA_MemoryInc = DMA_MemoryInc_Disable;
stDMA_Init.DMA_PeripheralDataSize = DMA_PeripheralDataSize_HalfWord;
stDMA_Init.DMA_MemoryDataSize = DMA_MemoryDataSize_HalfWord;
stDMA_Init.DMA_Mode = DMA_Mode_Circular;
stDMA_Init.DMA_Priority = DMA_Priority_High;
stDMA_Init.DMA_M2M = DMA_M2M_Disable;
DMA_Init(DMA1_Channel1, &stDMA_Init);
/* Enable DMA channel1 */
DMA_Cmd(DMA1_Channel1, ENABLE);
}
ADC Configuration
Since the application scenario of the test is relatively simple and many usages are not used, it is not enabled during configuration:
For example, analog watchdog, injection conversion, dual ADC, etc. Here we only use the simplest single-channel ADC
The configuration process is as follows:
1. First, configure the ADC clock. Since the maximum supported clock frequency of the ADC is 14MHz, the system main frequency is 72MHz, and the frequency divided to PCLK2 is also 72MHz. The frequency divider of the ADC only supports the frequency division coefficients of 2/4/6/8. Temporarily set it to 8, that is, 72/8 = 9MHz.
2. Configure ADC to independent mode (configuration in dual mode selection)
3. Turn off SCAN mode (multi-channel ADC is used, single channel is not used temporarily)
4. Enable continuous conversion mode
5. Turn off external triggering and trigger independently by software
6. Right-align data
7. The number of conversion channels is 1 regular channel
Since the injection channel and external trigger are not used here, many registers are not configured.
8. Configure the sampling time of Ch11 of ADC 1 and the number of channels for regular sampling
9. Enable DMA of ADC1
10. Turn on and wake up ADC1
11. Initialize the calibration register and calibrate ADC1
void SK_ADC1Init(void)
{
ADC_InitTypeDef stADC_Init;
RCC_APB2PeriphClockCmd(RCC_APB2Periph_ADC1, ENABLE);
/// Step 1 : Configure I/O Pin First
SK_ADC1GPIOInit();
/// Step 2 : Configure DMA
SK_ADC1DMAInit();
/// Step 3 : PCLK2 div in 8, ADC CLK => 9Mhz
RCC_ADCCLKConfig(RCC_PCLK2_Div8);
/// Step 4 : Configure Basic function of ADC1
stADC_Init.ADC_Mode = ADC_Mode_Independent;
stADC_Init.ADC_ScanConvMode = DISABLE;
stADC_Init.ADC_ContinuousConvMode = ENABLE;
stADC_Init.ADC_ExternalTrigConv = ADC_ExternalTrigConv_None;
stADC_Init.ADC_DataAlign = ADC_DataAlign_Right;
stADC_Init.ADC_NbrOfChannel = 1;
ADC_Init(ADC1, &stADC_Init);
/// Step 5 : Configure Ch11 sample rate
ADC_RegularChannelConfig(ADC1, ADC_Channel_11, 1, ADC_SampleTime_55Cycles5);
/// Step 6 : Enable ADC1 DMA
ADC_DMACmd(ADC1, ENABLE);
/// Step 7 : Enable ADC1
ADC_Cmd(ADC1, ENABLE);
/// Step 8 : Reset Calibration Register
ADC_ResetCalibration(ADC1);
while(ADC_GetResetCalibrationStatus(ADC1));
/// Step 9 : Start Calibration
ADC_StartCalibration(ADC1);
while(ADC_GetCalibrationStatus(ADC1));
/// Step 10 : Software trigger ADC1
ADC_SoftwareStartConvCmd(ADC1, ENABLE);
}
Finally, don't forget that 12-bit precision corresponds to a granularity of 4096, that is, if you divide the number into 4096 parts and convert it into voltage, it is:
(float)ADC_ConvertedValue/4096*3.3
Previous article:STM32F103ZET6 Clock (2) - Code
Next article:STM32F103ZET6 — EXTI
Recommended ReadingLatest update time:2024-11-23 11:46
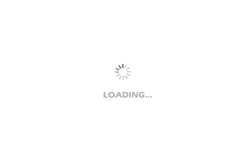
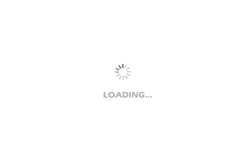
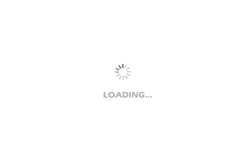
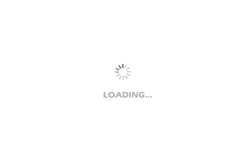
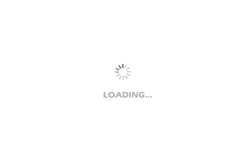
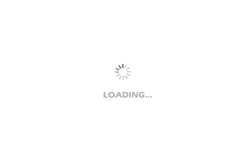
- Naxin Micro and Xinxian jointly launched the NS800RT series of real-time control MCUs
- How to learn embedded systems based on ARM platform
- Summary of jffs2_scan_eraseblock issues
- Application of SPCOMM Control in Serial Communication of Delphi7.0
- Using TComm component to realize serial communication in Delphi environment
- Bar chart code for embedded development practices
- Embedded Development Learning (10)
- Embedded Development Learning (8)
- Embedded Development Learning (6)
Professor at Beihang University, dedicated to promoting microcontrollers and embedded systems for over 20 years.
- Intel promotes AI with multi-dimensional efforts in technology, application, and ecology
- ChinaJoy Qualcomm Snapdragon Theme Pavilion takes you to experience the new changes in digital entertainment in the 5G era
- Infineon's latest generation IGBT technology platform enables precise control of speed and position
- Two test methods for LED lighting life
- Don't Let Lightning Induced Surges Scare You
- Application of brushless motor controller ML4425/4426
- Easy identification of LED power supply quality
- World's first integrated photovoltaic solar system completed in Israel
- Sliding window mean filter for avr microcontroller AD conversion
- What does call mean in the detailed explanation of ABB robot programming instructions?
- STMicroelectronics discloses its 2027-2028 financial model and path to achieve its 2030 goals
- 2024 China Automotive Charging and Battery Swapping Ecosystem Conference held in Taiyuan
- State-owned enterprises team up to invest in solid-state battery giant
- The evolution of electronic and electrical architecture is accelerating
- The first! National Automotive Chip Quality Inspection Center established
- BYD releases self-developed automotive chip using 4nm process, with a running score of up to 1.15 million
- GEODNET launches GEO-PULSE, a car GPS navigation device
- Should Chinese car companies develop their own high-computing chips?
- Infineon and Siemens combine embedded automotive software platform with microcontrollers to provide the necessary functions for next-generation SDVs
- Continental launches invisible biometric sensor display to monitor passengers' vital signs
- FPGA Design Process
- Power supply obstacles + power supply SBC selection and pitfalls
- Sharing of key points on the use of ADI passive components
- Four design considerations for telematics hardware in connected cars
- Method of Recognizing Telephone Signal Tone Using Single Chip Microcomputer
- Analysis of Single-Ended Forward Excitation Transformer
- Wide voltage input USB-C, 5V/3A output adapter reference design
- How much do you know about the CAN-FD protocol?
- When the machine is turned off, the LDO output is normally 3V. Why does the voltage reach 3.5V after the machine is turned on? What is the reason?
- 【Smart Sports Watch】3. Build Development Environment 2