0 Introduction
In recent years, with the rapid development of China's economy and the rapid growth of the number of cars and drivers, the number of road traffic accidents has remained high, and the road traffic situation has become increasingly complex and worse. Mass deaths and injuries occur frequently, which has a great impact on people's life safety and family happiness. Therefore, it is particularly important to strengthen vehicle management. Traffic safety is mainly guaranteed by two aspects: one is that the vehicle has a good condition, and the other is the driver's standardized operation. Therefore, how to monitor and manage vehicles and standardize driver operations is an urgent problem that needs to be solved.
The car driving recorder, also known as the "car black box", is a digital electronic recording device that records and stores the vehicle's driving speed, time, mileage and other status information related to the vehicle's driving, and can output data through an interface. However, the driving recorder cannot transmit the vehicle's operating status to the monitoring center in real time, which belongs to post-event supervision, so it plays a limited role in preventing traffic safety accidents. The vehicle monitoring system based on GPS /GSM can obtain the vehicle's location, speed and other information in real time, providing an effective way for real-time monitoring of vehicles. However, GPS cannot obtain important vehicle condition information such as air pressure, water temperature, and speed, so the monitoring of the vehicle lacks comprehensiveness.
The vehicle monitoring management system based on CAN/GSM is developed for cars with CAN bus . The vehicle monitoring equipment of this system first obtains detailed vehicle condition information from the vehicle's CAN interface, and then communicates with the monitoring center based on China's most mature and widely used GSM mobile communication system to achieve comprehensive, dynamic, and real-time monitoring of the vehicle. Using the CAN bus , not only can comprehensive and detailed vehicle condition information be obtained, but also the system has strong scalability. For example, the GPS module can be connected to the bus as an intelligent node of CAN, so that the system has the ability to monitor the vehicle's location.
1 CAN bus technology
In order to realize the communication between the huge electronic control devices in modern cars and reduce the increasing signal lines, the bus must be used for information transmission. The CAN (Controller Area Network) bus is a relatively advanced and excellent field bus technology that is popular today. It is a serial data communication protocol developed by Bosch in Germany in the early 1980s to solve the data exchange between numerous control and test instruments in modern automobiles. It is a multi-master bus. The communication interface integrates the physical layer and data link layer functions of the CAN protocol and can perform frame processing on the communication data. CAN ensures the dynamic number of nodes in the network by encoding the communication data block, and enables different nodes to receive the same data at the same time. The data segment length is up to 8 bytes, which ensures the real-time nature of the communication; and the protocol uses CRC check to provide corresponding error handling functions to ensure the reliability of data communication. Since the CAN technical specification only includes the description of the physical layer and data link layer, and does not define the functions and implementation of the application layer, users can either use the open high-level protocol developed by the International CAN Bus User and Manufacturer Association or some other organizations, or flexibly implement their own application layer in the project. In more than ten years of application, CAN has been widely used in the interconnection of industrial process monitoring equipment with its extremely high reliability, real-time and flexibility. It has been supported by more than 100 internationally renowned companies such as Intel, Motorola, Philips, and Siemens, and is recognized as one of the most promising field buses. This system uses the above characteristics of the CAN bus to reduce the wiring harness in the car and solve the communication problem between many nodes.
2 Design of vehicle monitoring and management system
2.1 System design
This vehicle intelligent monitoring system uses CAN bus technology to collect various information of the vehicle, such as the start time, mileage, driving time, maximum speed and duration of each maximum speed of the vehicle, and stores the vehicle information 20 seconds before parking. Then use the existing GSM network to transmit the information to the monitoring center in the form of short messages to achieve real-time monitoring of the vehicle.
2.2 Hardware design
The main control chip of the vehicle monitoring equipment uses the 16-bit single-chip microcomputer MC9S12HZ developed by Freescale for automotive electronic applications . The main resources related to the vehicle monitoring equipment include: 32~256K Flash, 2~12K RAM and 1~2K EEPROM; 2 CAN controllers compatible with CAN2.0A and B with a rate of up to 1Mb/s; 2 full-duplex asynchronous serial communication interfaces; 32×4 segment LCD driver. The hardware connection diagram of the vehicle monitoring equipment composed of MC9S12HZ is shown in Figure 2. In terms of the interface with the CAN bus, we use the high-speed CAN transceiver TJAl050 of NXP. In order to improve the electrical EMC and ESD performance, the common mode choke L40 and ESD protection diode D39 are also added to the circuit . The GSM module uses a two-door TC35i, which is connected to the external controller through a 40-pin ZIF (Zero Insertion Force) interface. The monitoring system only uses the SMS service of the GSM network, so the main control chip and TC35i only need two pins, TXD and RXD. The main controller MC9S12HZ controls TC35i through AT commands. The microcontroller and TC35i communicate through the serial port. The automatic baud rate range supported by TC35i is 1200~230400B/s. We choose a baud rate of 9600B/s. According to the TC35i manual, its serial interface requires CMOS level, while MC9S12HZ is TTL level, so a level conversion circuit is required, as shown in Figure 2. The monitoring center consists of a PC and a TC35i module, and the level conversion between them is completed by the level conversion chip MAX232. 2.3 Software Design There are many vehicle operating parameters transmitted on the CAN bus, and the amount of data is large. However, the transmission speed of the SMS service of the GSM network is limited, so it is impossible to transmit all the information on the CAN bus back to the monitoring center. In fact, it is not necessary to monitor all vehicle operating parameters. It is enough to monitor some parameters that we are most concerned about and are most closely related to driving safety. For different parameters, the monitoring form is different. Some information needs to be monitored regularly, such as vehicle location information, while some information only needs to be sent when it exceeds the normal range, such as vehicle speed or rotation speed information. In addition, for different models, the parameters that need to be monitored are also different; or for the same parameter, under different circumstances, its monitoring form and monitoring range will also change. Therefore, it is required that the vehicle-mounted monitoring equipment can dynamically change the monitoring parameters and monitoring form.
In order to realize dynamic monitoring of the vehicle, a monitoring list is established in the controller of the vehicle monitoring device. Each item in the list contains the parameter group number PGN, the position of the monitoring parameter in the PGN, the monitoring form, the monitoring time interval and the monitoring parameter range. The items in this parameter list can be dynamically added or deleted according to the command sent by the monitoring center, so as to realize dynamic monitoring of the vehicle. The
main program flow of the vehicle monitoring device software is shown in Figure 3. The serial communication transceiver program and the CAN bus listening program are placed in the interrupt program. When the corresponding command or data is received, the data is placed in the buffer and the corresponding flag bit is set. The main program performs the corresponding action by querying these flag bits. The main program first reads the default temporary control list stored in the on-chip EEPROM, and sets the CAN ID message identifier filter and mask register of MC9S12HZ according to the PGN in the monitoring list. The program can modify the monitoring parameter list according to the command, and decide whether to change the default temporary control list in the EEPROM according to the command. When the PGN to be monitored has new data, it is necessary to determine whether the data meets the sending conditions, including whether the timing interval has arrived, whether the monitoring variable value exceeds the normal range, etc. If the sending conditions are met, the PGN and its corresponding data are added to the sending list.
3 Conclusion
This system uses CAN bus technology to obtain various detailed information of the vehicle, and uses the GSM network to communicate with the monitoring system. It not only realizes the dynamic setting of vehicle monitoring parameters, but also makes it easy to expand the monitoring object by adding CAN intelligent nodes due to the adoption of CAN bus technology. This greatly improves the flexibility and comprehensiveness of the monitoring system. At the same time, the GSM short message service is used for data transmission, which is simple to connect, low cost and wide coverage.
Previous article:Briefly describe the design and implementation of wireless vehicle terminal player
Next article:Design of vehicle fault diagnosis instrument based on CAN bus
Recommended ReadingLatest update time:2024-11-16 17:32
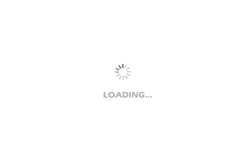
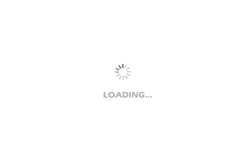
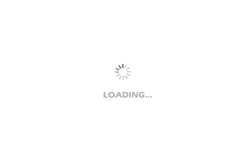
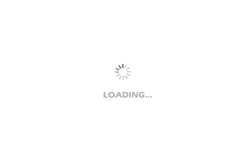
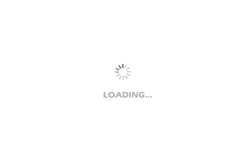
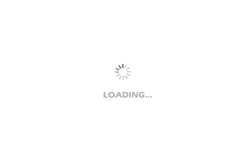
- Popular Resources
- Popular amplifiers
-
New Energy Vehicle Control System Inspection and Maintenance (Edited by Bao Pili)
-
Detailed explanation of big data technology system: principles, architecture and practice (Dong Xicheng)
-
Automotive CAN embedded intrusion detection system based on deep learning
-
Lightweight FPGA-based IDS-ECU architecture for automotive CAN networks
Professor at Beihang University, dedicated to promoting microcontrollers and embedded systems for over 20 years.
- Innolux's intelligent steer-by-wire solution makes cars smarter and safer
- 8051 MCU - Parity Check
- How to efficiently balance the sensitivity of tactile sensing interfaces
- What should I do if the servo motor shakes? What causes the servo motor to shake quickly?
- 【Brushless Motor】Analysis of three-phase BLDC motor and sharing of two popular development boards
- Midea Industrial Technology's subsidiaries Clou Electronics and Hekang New Energy jointly appeared at the Munich Battery Energy Storage Exhibition and Solar Energy Exhibition
- Guoxin Sichen | Application of ferroelectric memory PB85RS2MC in power battery management, with a capacity of 2M
- Analysis of common faults of frequency converter
- In a head-on competition with Qualcomm, what kind of cockpit products has Intel come up with?
- Dalian Rongke's all-vanadium liquid flow battery energy storage equipment industrialization project has entered the sprint stage before production
- Allegro MicroSystems Introduces Advanced Magnetic and Inductive Position Sensing Solutions at Electronica 2024
- Car key in the left hand, liveness detection radar in the right hand, UWB is imperative for cars!
- After a decade of rapid development, domestic CIS has entered the market
- Aegis Dagger Battery + Thor EM-i Super Hybrid, Geely New Energy has thrown out two "king bombs"
- A brief discussion on functional safety - fault, error, and failure
- In the smart car 2.0 cycle, these core industry chains are facing major opportunities!
- The United States and Japan are developing new batteries. CATL faces challenges? How should China's new energy battery industry respond?
- Murata launches high-precision 6-axis inertial sensor for automobiles
- Ford patents pre-charge alarm to help save costs and respond to emergencies
- New real-time microcontroller system from Texas Instruments enables smarter processing in automotive and industrial applications
- C2000 MCU-based multi-string LED lighting driver
- Key features and benefits of the TLV320ADC5140
- Summary of MSP430 clock settings and applications
- The probe must have an impact on the impedance test?
- Does anyone know how to drive the LCD screen on the GD32F450z_EVAL development board?
- What are the options for isolated DAC/ADC? APC & PAC chips
- Simple analysis of the difference between STM32 and 51
- A senior project used a digital tube, a three-pin inductor, and a three-pin capacitor.
- The role of parallel resistance on the capacitor of the integration circuit
- Practical sharing: The harm of Miller effect to MOSFET switching process