The modular parallel operation of inverter power supplies can greatly improve the flexibility of the system and break the limitation of inverter power levels. Users can combine the power of the system according to their needs. At the same time, it is easy to realize redundant design, so it has the advantages of high reliability and easy high power. The research on communication monitoring technology of parallel inverter power supplies is a problem that must be solved in the process of AC power supply system from traditional centralized power supply to distributed power supply and even intelligent power supply system power supply mode [1]. This paper introduces a parallel inverter power supply communication monitoring system based on CAN field bus. The system makes full use of the internal resources of TI's TMS320LF2407A DSP chip, obtains and analyzes the field control data from each parallel module through the CAN bus, responds to the strong real-time operation on the field, and realizes the scheduling and monitoring of the module work. It has the advantages of simple structure, convenient expansion and high reliability.
1 System composition
1.1 System network structure
The system composition is shown in Figure 1. The system consists of a monitoring host, a parallel power module and a CAN bus. The inverter power module is mainly composed of a PWM inverter, a DSP controller, signal sampling and load current sharing, and communication control. TMS320LF2407A (DSP) is selected as the control core. DSP controls the output PWM pulse according to the difference between the feedback voltage and current value and the set value, drives the inverter bridge power switch, and outputs a sinusoidal voltage with adjustable frequency, amplitude, and phase. The CAN controller embedded in the LF2407A receives commands from the CAN bus to control the parallel inverter power module.
The characteristic of this topology is that multiple network communication nodes share one transmission line, which not only has high channel utilization, but also has simple connection, low cost and high system reliability. Information transmission adopts CAN communication protocol and the transmission medium adopts twisted pair. If the anti-interference ability of the system needs to be further improved, photoelectric isolation and other measures can be added between the controller and the transmission medium.
1.2 Main hardware of the system
The hardware module circuit is shown in Figure 2. Since the LF2407A chip itself contains an embedded CAN controller, the hardware design is relatively simple, and only one transceiver SN65HVD232D is needed to realize the interface between this node and the bus.
SN65HVD232D is an interface chip for CAN protocol controller and physical bus of TI, which complies with ISO11898 standard. It provides differential transmission capability for the bus and differential reception capability for the CAN controller. A 120Ω matching resistor is added to the terminal to ensure the anti-interference capability and reliability of data communication.
2 Software Design
2.1 Baud rate setting programming
The transmission rate of the CAN bus is related to the maximum distance between two nodes. Table 1 shows the relationship between the maximum distance between any two nodes in the CAN bus system and the bit rate. The table also shows the values of the bit timer configuration registers BCR2 and BCR1 of the LF2407A. The setting of these values is related to the main clock frequency of the LF2407A. Generally, the bit rate can be calculated according to the following formula:
Baud rate = ICLK/[(BRP+1)×bitTime] (1)
Among them, ICLK is the DSP system frequency, and BRP is determined by the bit timer configuration register BCR2.
bitTime=(TSEG1+1)+(TSEG2+1)+1 (2)
TSEG1 and TSEG2 are determined by the bit timer configuration register BCR1.
2.2 Frame Structure Design
According to the CAN2.0 specification, the message transmitted on the CAN bus consists of 3 to 11 bytes, including 3 bytes of control bytes and 0 to 8 bytes of data bytes.
A valid CAN data frame consists of a frame start, arbitration field, control field, data field, check field, response field, and frame end. The CAN controller of TMS320LF2407A supports two different frame formats: standard frame and extended frame. The main difference between them is the different arbitration field formats. The arbitration field of the standard frame consists of an 11-bit identifier and a remote transmission request bit RTR; the arbitration field of the extended frame consists of a 29-bit identifier and a substitute remote request bit SRR bit, a flag bit, and a remote transmission request bit RTR, as shown in Figure 3.
The identifier is the name of the message and is first sent to the bus during the arbitration process. It is used in the receiver's acceptance judgment and in the arbitration process to determine access priority.
The remote transmission request bit (RTR) is used to determine whether to send a data frame or a remote frame. When RTR is high, the CAN controller sends a remote frame; when it is low, it sends a data frame.
The data length code (DLC) is used to determine the number of data bytes to be sent per frame, up to 8 bytes.
The control command indicates the meaning of this frame. The meaning of the control command word in this article is shown in Table 2.
2.3 Program flow design
Master-slave control is a relatively mature inverter parallel control method. This design adopts the master-slave control strategy to realize communication monitoring of the parallel inverter system.
If mailbox 3 is set as a non-broadcast mailbox, mailbox 2 is set as a non-broadcast mailbox, mailbox 4 is set as a broadcast mailbox, and mailbox 0 is set as a broadcast mailbox, the program flow charts for receiving and sending information are shown in Figures 4 and 5 respectively.
As can be seen from the flow chart, the entire communication system is mainly divided into a master node and multiple sub-nodes. Each sub-node will use mailbox 4 to regularly send a master request to the bus in the form of broadcast at a certain time interval to detect whether the master node is working properly. If it is working properly, the master node will send a response against the master request, and this response is also sent on the bus in the form of broadcast. Therefore, each node on the network will receive a master request and an anti-master request response. The function of mailbox 0 is to receive and distinguish these two types of information, and judge its own status to decide whether to use mailbox 4 to send an anti-master request. The main function of mailbox 2 is to receive the control information of the master node and notify mailbox 3 to send a response message.
Figure 5 shows the information sending process in detail. The program list of the CAN communication main part of this system written by DSP assembly instructions is as follows.
LDP #DP_CAN
SPLK #0040H,TCR ; Mailbox 4 sends master request
LDP #DP_PF2
LAR AR7,#4H
LDP #DP_CAN
MAR *,AR4 ; Send times
LAR AR4,#0FFFFH
W_TA5: LDP #6
SBRK #01H
SAR AR4,30H
LACL 30H
BCND W_TA7,EQ
LDP #DP_CAN
BIT TCR,1 ; Wait for sending response
BCND W_TA5,NTC
SPLK #4000H,TCR
LDP #DP_CAN
MAR *,AR4 ; Send times
LAR AR4,#0FFFFH
W_TA7: LDP #DP_CAN
MAR*,AR4 ; Send times
LAR AR4,#0FFFFH
W_TA6: LDP #6
SBRK #01H
SAR AR4,30H
LACL 30H
BCND W_TA9, EQ; write mailbox content, configure parameters given
LDP #DP_USER
BIT CAN_FLAG1, BIT0; determine whether a response opposing the master node application is received
BCND W_TA6, NTC; if there is no objection, modify the ID1 and ID0 of mailbox 4. When it is 10, it means that this node is the master node
LDP #DP_USER
SPLK #00H, CAN_FLAG1
LDP #DP_CAN
SPLK #4000H, TCR; clear TA4 and MIF4
CALL LOOP11; mailbox 3 sends data
The use of fieldbus control technology can easily build a distributed inverter power local control network, so that the power system has the characteristics of a field network control system (FCS). This method not only inherits the advantages of a distributed control system (DCS), but also integrates digital communication and intelligent network control. The system introduced in this article not only makes the parallel connection of inverter power simple, but also provides stable and reliable data communication for each module, realizes the control functions of system parameter setting, static current sharing of parallel inverter power modules, and module competition, and the system structure is simple and reliable.
Previous article:Improvement of HDTV Image Quality Based on HQV Vida Processor
Next article:Detailed explanation of video transcoding technology and its implementation
Recommended ReadingLatest update time:2024-11-16 19:38
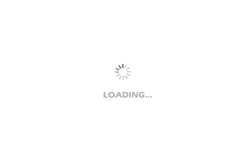
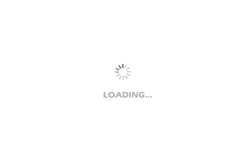
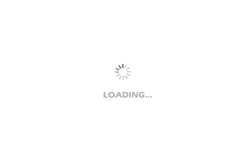
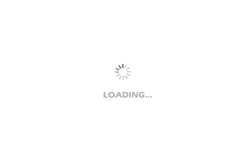
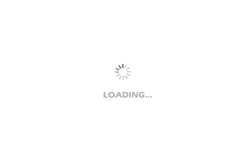
- Popular Resources
- Popular amplifiers
- Huawei's Strategic Department Director Gai Gang: The cumulative installed base of open source Euler operating system exceeds 10 million sets
- Analysis of the application of several common contact parts in high-voltage connectors of new energy vehicles
- Wiring harness durability test and contact voltage drop test method
- Sn-doped CuO nanostructure-based ethanol gas sensor for real-time drunk driving detection in vehicles
- Design considerations for automotive battery wiring harness
- Do you know all the various motors commonly used in automotive electronics?
- What are the functions of the Internet of Vehicles? What are the uses and benefits of the Internet of Vehicles?
- Power Inverter - A critical safety system for electric vehicles
- Analysis of the information security mechanism of AUTOSAR, the automotive embedded software framework
Professor at Beihang University, dedicated to promoting microcontrollers and embedded systems for over 20 years.
- Innolux's intelligent steer-by-wire solution makes cars smarter and safer
- 8051 MCU - Parity Check
- How to efficiently balance the sensitivity of tactile sensing interfaces
- What should I do if the servo motor shakes? What causes the servo motor to shake quickly?
- 【Brushless Motor】Analysis of three-phase BLDC motor and sharing of two popular development boards
- Midea Industrial Technology's subsidiaries Clou Electronics and Hekang New Energy jointly appeared at the Munich Battery Energy Storage Exhibition and Solar Energy Exhibition
- Guoxin Sichen | Application of ferroelectric memory PB85RS2MC in power battery management, with a capacity of 2M
- Analysis of common faults of frequency converter
- In a head-on competition with Qualcomm, what kind of cockpit products has Intel come up with?
- Dalian Rongke's all-vanadium liquid flow battery energy storage equipment industrialization project has entered the sprint stage before production
- Allegro MicroSystems Introduces Advanced Magnetic and Inductive Position Sensing Solutions at Electronica 2024
- Car key in the left hand, liveness detection radar in the right hand, UWB is imperative for cars!
- After a decade of rapid development, domestic CIS has entered the market
- Aegis Dagger Battery + Thor EM-i Super Hybrid, Geely New Energy has thrown out two "king bombs"
- A brief discussion on functional safety - fault, error, and failure
- In the smart car 2.0 cycle, these core industry chains are facing major opportunities!
- The United States and Japan are developing new batteries. CATL faces challenges? How should China's new energy battery industry respond?
- Murata launches high-precision 6-axis inertial sensor for automobiles
- Ford patents pre-charge alarm to help save costs and respond to emergencies
- New real-time microcontroller system from Texas Instruments enables smarter processing in automotive and industrial applications
- In PADS, VIA Stitch is gray
- test
- Please recommend IGBT
- TMS320F28377_SVPWM complete program
- Electronic Engineers from Entry to Mastery
- Will low power consumption of small UWB modules be an inevitable development in the future?
- 【AT-START-F425 Review】No.07 8x8 Dual Color Dot Matrix Screen Carousel
- The meaning of Mosfet's capacitance coer and cotr
- [ESK32-360 Review] + DHT22 and single bus detection of temperature and humidity
- [TI recommended course] #Zero-based entry: Hand-in-hand teaching you how to quickly develop MSP430? Project#