To understand the similarities and differences between MCU and PLC, we must first clarify what is MCU and what is PLC. In this regard, it may be helpful for us to briefly review the development history of computers. According to the original definition of computer experts, the computer system consists of five parts: control unit (CU), arithmetic operation unit (ALU), memory, input device (Input), and output device (Output). The CU or ALU of early computers (transistor or integrated circuit, excluding vacuum tubes) consisted of one or more circuit boards. The CU and ALU were separate. With the improvement of integration, the CU and ALU were combined to form a central processing unit (CPU). Then, the CPU was integrated into a single integrated circuit to produce an MPU or MCU, and MPUs such as Intel4004, 8008, 8080, 8085, 8086, 8088, and Z80 appeared. Since then, the development of MPU has produced two branches. One branch is developing towards high performance, high speed and large capacity. Typical chips include Intel8086, 286, 386, 486, 586, P2, P3, P4, etc., with speeds ranging from 4.7MHz to the current 3.2GHz. The other branch is developing towards multi-functions, integrating all memory (ROM, PROM, EPROM, EEPROM, FLASH ROM, SRAM, etc.) and input/output interfaces (Timer/Counter, PWM, ADC/DAC, UART, IIC, SPI, RTC, PCA, FPGA, etc.) into an integrated circuit to become SOC (System On a Chip). In my humble opinion, this is the single-chip computer widely used today, referred to as a single-chip microcomputer. This branch can be said to be of various varieties, with bit widths ranging from 8 bits to 32 bits, pin counts ranging from 6 to hundreds, operating frequencies ranging from tens of KHz to hundreds of MHz, and architectures including both CISC and RISC, which are countless. Commonly used ones include MCS-51 series, MCS-96 series, PIC series, AVR series, ARM7/9 series, TMS320 series, MSP430 series, many MOTOROLA microcontrollers, etc.
So far, we can divide the development of computer core processors into three stages: board-level CPU, chip-level MPU and SOC.
What is PLC? The full name of PLC is Programmable Logic Controller. When it was first introduced into China, it was referred to as PC. Later, IBM-PC was widely used, and PC became synonymous with personal computer, and then it was changed to PLC. PLC also has another meaning, Power Line Carrier.
PLC is a product, but this product is a bit special. Before the control program is downloaded, it does not have any control function, that is, PLC without application program is useless. PLC is actually a general control platform designed for industrial environment. It must be secondary developed to achieve the final control purpose. Therefore, it also needs the cooperation of program editing/debugging software.
PLC is an intelligent product. What solution does its core controller adopt? The board-level CPU is definitely not an option. The MPU also needs several integrated circuits. For example, the Z80 MPU requires the Z80MPU, PIO, CTC, SIO, EPROM, SRAM, etc. These integrated circuits are installed on a circuit board. This is the early single-board computer. This solution is too large and not suitable for modern requirements. It can be seen that the core controller of the PLC is the most suitable to use a single-chip microcomputer.
From this we can conclude:
1. PLC is a product built on a single-chip microcomputer, which is an integrated circuit. The two are not comparable.
2. Single-chip microcomputers can form a variety of application systems, from micro, small to medium and large. PLC is a special case of a single-chip microcomputer application system.
3. PLCs from different manufacturers have the same working principle, similar functions and indicators, a certain degree of interchangeability, guaranteed quality, and programming software is moving towards standardization. This is the basis for PLC to be widely used. The single-chip microcomputer application system is like the Eight Immortals crossing the sea, each showing its magical powers, with a wide range of functions and uneven quality. It is difficult to learn, use and maintain.
Finally, from an engineering perspective, let's talk about the selection of PLC and single-chip microcomputer systems;
1. For single projects or projects with very few repetitions, the use of PLC solutions is a wise and quick way, with a high success rate, good reliability, and less trouble, but the cost is relatively high.
2. For large-volume supporting projects, the use of single-chip microcomputer systems has the advantages of low cost and high efficiency, but this requires considerable R&D strength and industry experience to make the system run stably and sustainably. The best method is to embed the functions of PLC into the single-chip microcomputer system, which can greatly simplify the development time of the single-chip microcomputer system, ensure performance, and ensure efficiency.
The difference between PLC and MCU.
Seeing netizens discussing the difference between PLC and MCU, I would like to say a few words: PLC is actually a ready-made single-chip computer (MCU has a wide range) system.
You can think of PLC ladder diagram as a programming language like assembly and other computer languages, but the scope of use is different! And the usual practice is to convert your ladder diagram into C or assembly language (determined by the CPU used by PLC), and then use the assembly or C compilation system to compile it into machine code! PLC runs only machine code. Ladder diagram is just to make it easier for users to use.
Similarly, MCS-51 MCU can also be used for PLC production, but 8-bit CPU is not suitable for some advanced applications such as: A large number of operations (including floating-point operations), embedded systems (UCOS can now be ported to MCS-51), etc., are just a little bit beyond our ability. An industrial system used by our company is made using MCS-51 microcontrollers, but with the addition of DSP, it can already meet our requirements (our equipment is slow and mainly logic control, but the number of points is not small, 128 points of I/O!!), and it also uses ladder diagram programming. We convert our ladder diagram into C51 and then use KEIL's C51 for compilation. Have you noticed that different models of PLCs will use different CPUs!!
Of course, you can also use microcontrollers to directly develop control systems, but the requirements for developers are quite high (not one The general level can be competent), the development cycle is long, and the cost is high (for some larger systems, you need to do experiments, and the printed circuit board will cost a considerable amount of money. You can say that you use simulators and experimental boards to develop, but I want to tell you that by doing so, you only verify the feasibility of hardware and software, which does not mean that it can be used in industrial control systems, because industrial control systems have very high requirements for anti-interference, stability first, not performance first, so your circuit board design must be constantly tested and improved). When you solve the above problems, you will find that you have made a PLC. Of course, if you need others to use it easily, you also need a set of software to use it. You don’t need to tell others your circuit (you can’t tell others). The above are some of my humble opinions. Please correct me if I’m wrong, but don’t hit me! Don’t scold me! I just want to discuss it with you!!!
Many people think that PLC is very mysterious. In fact, PLC is very simple. Its internal CPU is not as good as ordinary microcontrollers in other functions except for its fast speed. Usually PLC uses a 16-bit or 32-bit CPU with 1 or 2 serial channels to communicate with the outside world. There is only one timer inside. If you want to improve reliability, adding a watchdog timer is enough.
The key technology of PLC lies in the fact that it has a program that can interpret the ladder diagram language and an auxiliary communication program. The efficiency of the ladder diagram language interpretation program determines the performance of the PLC, and the communication program determines the difficulty of the PLC exchanging information with the outside world. For simple applications, it usually operates as an independent controller, without exchanging information with the outside world, and only needs to have a program that can interpret the ladder diagram language internally. In fact, the main work of designing a PLC is to develop a program that interprets the ladder diagram language.
Previous article:A problem that needs attention in the multiplication operation of MSP430G2333 lower computer
Next article:What is the precision of MCU AD
Recommended ReadingLatest update time:2024-11-16 13:01
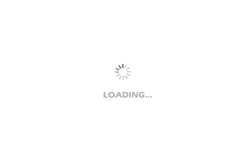
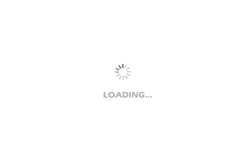
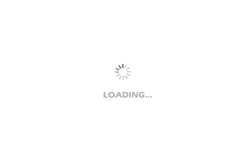
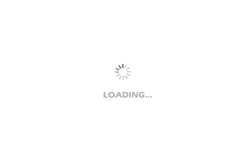
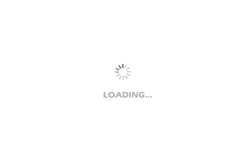
- Popular Resources
- Popular amplifiers
-
Wireless Sensor Network Technology and Applications (Edited by Mou Si, Yin Hong, and Su Xing)
-
Siemens PLC Programming Technology and Application Cases (Edited by Liu Zhenquan, Wang Hanzhi, Yang Kun, etc.)
-
Siemens PLC from Beginner to Mastery with Color Illustrations (Yang Rui)
-
Siemens PLC Project Tutorial
Professor at Beihang University, dedicated to promoting microcontrollers and embedded systems for over 20 years.
- Innolux's intelligent steer-by-wire solution makes cars smarter and safer
- 8051 MCU - Parity Check
- How to efficiently balance the sensitivity of tactile sensing interfaces
- What should I do if the servo motor shakes? What causes the servo motor to shake quickly?
- 【Brushless Motor】Analysis of three-phase BLDC motor and sharing of two popular development boards
- Midea Industrial Technology's subsidiaries Clou Electronics and Hekang New Energy jointly appeared at the Munich Battery Energy Storage Exhibition and Solar Energy Exhibition
- Guoxin Sichen | Application of ferroelectric memory PB85RS2MC in power battery management, with a capacity of 2M
- Analysis of common faults of frequency converter
- In a head-on competition with Qualcomm, what kind of cockpit products has Intel come up with?
- Dalian Rongke's all-vanadium liquid flow battery energy storage equipment industrialization project has entered the sprint stage before production
- Allegro MicroSystems Introduces Advanced Magnetic and Inductive Position Sensing Solutions at Electronica 2024
- Car key in the left hand, liveness detection radar in the right hand, UWB is imperative for cars!
- After a decade of rapid development, domestic CIS has entered the market
- Aegis Dagger Battery + Thor EM-i Super Hybrid, Geely New Energy has thrown out two "king bombs"
- A brief discussion on functional safety - fault, error, and failure
- In the smart car 2.0 cycle, these core industry chains are facing major opportunities!
- The United States and Japan are developing new batteries. CATL faces challenges? How should China's new energy battery industry respond?
- Murata launches high-precision 6-axis inertial sensor for automobiles
- Ford patents pre-charge alarm to help save costs and respond to emergencies
- New real-time microcontroller system from Texas Instruments enables smarter processing in automotive and industrial applications