The requirements for low power MCUs vary depending on the application and how the MCU is used in the application. For example, in a battery-powered thermostat application, low power is primarily defined by the lowest power mode in which the device can drive an LCD display, in which case reducing power consumption will extend the life of the battery. In other low power applications, such as electric meters, low power refers to the operating current consumed by the system during operation. The third category of systems are those that need to keep time regardless of whether the main power supply to the system is present. An electric meter during a power outage is an example of a third category system. Because the requirements of various applications vary, MCUs with more flexible power modes allow designers to further customize system operation.
In the past, the operating modes of the MCU were used for device operation; idle and doze modes reduced or eliminated CPU switching power while allowing peripherals to operate; and sleep modes allowed limited peripherals to operate at the lowest power. As today's advanced MCUs move to more advanced silicon processes that minimize system cost and reduce operating current, some new low power modes are being added to increase the flexibility of the MCU. We will explore some of the new low-power modes found in today’s advanced MCUs by looking at their use in a variety of applications.
We will compare various power modes implemented in different applications using the Battery Life Estimator (BLE) software tool and 16-bit MCUs. Microchip’s BLE is a free software tool that allows designers to estimate the battery life of a system and determine which of the available operating modes is best for their application. The PIC24FJ128GA310 MCU family offers some of the new low-power modes, and its LCD display driver works well in some of the following examples.
Multiple Applications Require Low-Power MCUs
Thermostats have become more complex, with more information to display and multiple regions to cover. As a result, large amounts of on-chip flash program memory are often required to store complex menus in multiple languages.
Generally speaking, advanced processes are required to produce large memory MCUs at competitive prices. As semiconductor processes advance, the trend is for transistors to have less operating current and more leakage current. The increase in leakage current is most evident in the current specifications of low-power modes such as sleep mode. Sleep current on advanced MCUs is typically in the 3 to 5µA range, and most of the time a typical thermostat application is just driving a segmented LCD display. Segmented LCD displays are often driven in sleep mode, which allows certain peripherals (in this case, the LCD driver) to run while the CPU and most peripherals are powered down. Thermostats must be woken up periodically and put into operating mode to read the temperature, update the display, and perhaps signal the furnace, fan, or air conditioning unit to turn on. However, more than 99% of the time, only sleep mode is needed. Since a lot of time is spent in sleep mode, improving sleep current can significantly increase the battery life of the system.
New Low-Power Modes
In order to enable MCUs with sub-µA power modes, many vendors have introduced new low-power deep sleep modes. Typical deep sleep currents are in the 10 to 50nA range, and these devices can add 400nA when running the real-time clock calendar (RTCC). Extremely low currents are achieved by shutting down the entire device and only retaining a small amount of memory, the real-time clock, and perhaps a watchdog timer. However, these deep sleep modes do not allow peripherals to run or retain data RAM on the device. When the device wakes up from deep sleep, if the RAM contents are lost, the device needs to perform a restart routine before resuming program execution.
New low-power modes, such as low-voltage sleep mode, retain the device’s data RAM at a typical base current of 330nA and allow additional low-power peripherals to run. This low-voltage sleep mode retains the device’s RAM and reduces sleep current by reducing the device’s on-chip regulator output. By reducing the supply voltage to the device’s logic and limiting the active peripherals, the MCU’s sleep current can be reduced from 3.7µA to 330nA. In this type of MCU sleep mode, peripherals such as LCD drivers, timers, and RTCCs can still run with minimal current addition. The device resumes operating from low-voltage sleep mode in less than half the time it takes to wake up from deep sleep. The device then begins execution from the next instruction rather than starting from the restart sequence that is normally required to wake up from deep sleep mode.

Figure 1: Battery Life Estimator Tool Main Screen
As shown in Figure 1, the main screen of the Battery Life Estimator Tool displays the MCU and its operating voltage, battery, and operating mode. The estimated battery life for the thermostat model is 11 years and 88 days. [page]
In addition, the BLE tool models the amount of time the MCU will spend in each operating mode and the amount of power it will consume in each mode. Figure 1 shows the BLE output display where you can set several key parameters of the system to get the lifetime estimate and average system current. First, select the operating voltage for the MCU and the system. This allows the Battery Life Estimator to obtain the appropriate specifications. Then select the battery or battery pair—in this case, 2 AAA alkaline batteries. You can also select the expected system operating voltage and operating temperature to obtain the specifications that best fit the battery life estimation model. Finally, define the operating modes that will be used in the system. For our thermostat, two modes will be used.
To model the time that the thermostat only displays the LCD screen, an operating mode called "Show LCD" is created. The "Show LCD" operating mode uses a low-voltage sleep mode to provide the lowest power mode for driving the LCD. The Battery Life Estimator tool models the device's operating cycle as 30 seconds, with 29.5 seconds spent in low voltage sleep mode. The second operating mode, Update Temperature and LCD, models the time required for the MCU to monitor temperature, update the LCD screen, and communicate with the HVAC unit.
To better appreciate the new low voltage sleep mode and how it is implemented in the BLE tool, the Add/Modify Mode screen can be viewed, as shown in Figure 2. In this screen, the designer can adjust the Duration setting, which is currently set to 29.5 seconds. Using the Additional System Current input box, the designer can add current consumption estimates for the MCU's peripheral circuits. In this case, a system current of 4µA is added to represent the current consumed by the LCD display, and an additional current of 1µA is added to represent the current required by the internal LCD bias resistors. Next, the power mode (low voltage sleep in this case) is selected, along with the desired peripherals. To provide an accurate system current model, the LCD driver, BOR, WDT, and RTCC have been selected. The MCU itself consumes 1.88 µA, which is added to our 5 µA system current to reach the 6.88 µA required for the system in low voltage sleep mode.

Figure 2: Battery Life Estimator Tool Mode Edit Screen The Battery Life Estimator Tool's Mode Edit screen allows designers to specify and name the conditions for each power mode used. The
BLE main screen shows that the device consumes an average current of 6.88uA in low-voltage sleep mode, and a little over 327uA when the device is in short-term active mode, so the total average current is less than 6.9uA. The estimated value of the system battery life is about 12 years, which is about 5 years longer than the shelf life of the battery. Figure 3 shows a similar analysis, but using sleep mode instead of low-voltage sleep mode. This analysis gives an average current of about 10.5uA, which reduces the battery life by three years. [page]

Figure 3: Battery Life Estimator Tool, battery life estimated based on sleep mode is three years less than battery life estimated based on standard sleep mode. At
the other extreme for the MCU are systems that spend most of their time in active mode, such as electric meters. Today’s electric meters are in only two states throughout their operating cycle. When powered on, they are in normal operating mode. In this “normal” operating mode, the MCU is active, constantly measuring voltage and current and calculating the power being supplied through the meter. The meter may also monitor for potential tampering, drive an LCD display, and possibly communicate with meter reading facilities.
When the meter is operating, it may appear that power is plentiful. In reality, power is a product provided by the meter manufacturer’s end customer, the utility. Utilities provide power to millions of customers, and even small power losses can be costly to the utility’s business. In practice, most meters must operate within the IEC-defined 10VA power budget. If possible line variations, component tolerances, and system design margins are taken into account, the final result is a system MCU current budget of about 10mA when using a capacitive power supply.
Some of today’s low-cost meters use 8-bit MCUs, and they often consume more than 10mA when running at full speed in active mode. Staying within the system power budget often requires designers to run the MCU at a lower frequency. Many current 16-bit MCUs utilize advanced process and design techniques to provide typical operating currents as low as 150µA/MHz and can run at full speed at 16MIPS while consuming no more than 6.9mA. The reduced operating current provides designers with two options: reduce the operating speed of the MCU to reduce system power consumption or add additional functionality while keeping the system power consumption within the allocated budget. Although
the meter spends the vast majority of its time in the active state, it is also an example of an application that takes advantage of one of the lowest power modes (Vbat). The Vbat function provides a dedicated pin that can provide a backup power source, such as an LTC battery or supercapacitor. If the system's main power source is lost (such as during a power outage), the RTCC's power automatically switches to the backup Vbat pin. RTCCs in meters are important during power outages as time-of-use billing becomes increasingly popular. When operating from Vbat, the RTCC allows the LTC battery to last for decades, providing virtually unlimited backup operating power. Using the Vbat function with an RTCC is not limited to meters. Many applications, including the thermostat mentioned above, can use RTCC to keep time during power outages or battery replacement. Vbat with a capacitor or battery can also help eliminate annoying flashes caused by power outages.
In an environment where power consumption is highly concerned, the development of low-power MCUs has led to extremely flexible general-purpose MCUs. Advances in process technology and design techniques have enabled 16-bit MCUs to operate at currents as low as 150uA/MHz. New low-power modes (such as low-voltage sleep and Vbat) add flexibility to the power management chain, allowing general-purpose MCUs to work in a wider range of applications. The end result is a powerful and adaptable MCU that enables customer-friendly, energy-efficient terminal applications.
Previous article:Application of single chip microcomputer in the analysis of arithmetic unit
Next article:The role of the capacitor next to the MCU crystal and the analysis of the oscillation circuit
Recommended ReadingLatest update time:2024-11-16 19:52
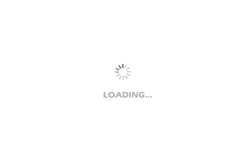
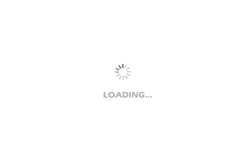
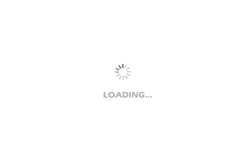
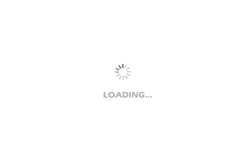
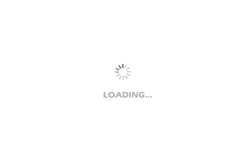
- Popular Resources
- Popular amplifiers
-
Wireless Sensor Network Technology and Applications (Edited by Mou Si, Yin Hong, and Su Xing)
-
Modern Electronic Technology Training Course (Edited by Yao Youfeng)
-
Modern arc welding power supply and its control
-
Small AC Servo Motor Control Circuit Design (by Masaru Ishijima; translated by Xue Liang and Zhu Jianjun, by Masaru Ishijima, Xue Liang, and Zhu Jianjun)
Professor at Beihang University, dedicated to promoting microcontrollers and embedded systems for over 20 years.
- Innolux's intelligent steer-by-wire solution makes cars smarter and safer
- 8051 MCU - Parity Check
- How to efficiently balance the sensitivity of tactile sensing interfaces
- What should I do if the servo motor shakes? What causes the servo motor to shake quickly?
- 【Brushless Motor】Analysis of three-phase BLDC motor and sharing of two popular development boards
- Midea Industrial Technology's subsidiaries Clou Electronics and Hekang New Energy jointly appeared at the Munich Battery Energy Storage Exhibition and Solar Energy Exhibition
- Guoxin Sichen | Application of ferroelectric memory PB85RS2MC in power battery management, with a capacity of 2M
- Analysis of common faults of frequency converter
- In a head-on competition with Qualcomm, what kind of cockpit products has Intel come up with?
- Dalian Rongke's all-vanadium liquid flow battery energy storage equipment industrialization project has entered the sprint stage before production
- Allegro MicroSystems Introduces Advanced Magnetic and Inductive Position Sensing Solutions at Electronica 2024
- Car key in the left hand, liveness detection radar in the right hand, UWB is imperative for cars!
- After a decade of rapid development, domestic CIS has entered the market
- Aegis Dagger Battery + Thor EM-i Super Hybrid, Geely New Energy has thrown out two "king bombs"
- A brief discussion on functional safety - fault, error, and failure
- In the smart car 2.0 cycle, these core industry chains are facing major opportunities!
- The United States and Japan are developing new batteries. CATL faces challenges? How should China's new energy battery industry respond?
- Murata launches high-precision 6-axis inertial sensor for automobiles
- Ford patents pre-charge alarm to help save costs and respond to emergencies
- New real-time microcontroller system from Texas Instruments enables smarter processing in automotive and industrial applications
- Research on WiMAX Network Application Scheme Based on IEEE 802.16e Technology
- ADI's "Basic Tutorial on Analog Electronic Devices" is available for free download!
- Asking for advice on tps65982
- What is the use of ceramic capacitors in parallel with DC motors?
- Last 3 days: Apply for free evaluation of Fudan Micro FM33LC046N Demo board
- Recommend several books on computer vision and image processing with OpenCV
- Sugar Glider ④ RSL10-SENSE-GEVK Playing with BHI160, step count, motion recognition? No need to process, get it directly!!
- How to solve this ESD problem
- STC12C5A60S2 MCU pattern water light (birds returning home) C program
- Goodbye 2019, hello 2020 Looking forward to the future