The high-torque permanent magnet synchronous motor direct drive eliminates the unfavorable factors such as low efficiency, frequent maintenance, noise and large rotational inertia caused by the mechanical structure because it removes the complex mechanical transmission mechanism. It has a series of outstanding advantages such as high efficiency, low vibration and noise, high precision, fast response, and convenient use and maintenance [1]. In recent years, with the development of power electronics technology, permanent magnet materials, motor design and manufacturing technology, sensor technology, control theory, etc., high-torque permanent magnet synchronous motors have been more and more widely used in high-performance systems such as CNC machine tools, mining machinery, and port machinery [2-3].
The AC motor control system widely uses single-chip microcomputer, DSP and FPGA as the core of the control system. STM32 is a new 32-bit flash microcontroller based on the ARM Cortex-M3 core. It uses the high-performance, high-code density Thumb-2 instruction set and tightly coupled nested vector interrupt controller, has a rich peripheral interface, and has the advantages of high performance, low cost and low power consumption [4]. This paper designs a high-performance, low-cost control system for a high-torque permanent magnet synchronous motor drive system for port machinery using the STM32 + IPM hardware architecture.
1. Vector Control Principle of High Torque Permanent Magnet Synchronous Motor
Ignoring the core saturation, eddy current and hysteresis loss of the motor, and ignoring the influence of leakage flux, the voltage, flux linkage and torque equations of the large torque permanent magnet synchronous motor are respectively:
ψd, ψq, ud, uq, id, iq, Ld, Lq are the flux, voltage, current and inductance of the d and q axes of the permanent magnet synchronous motor respectively, Rs is the armature winding resistance, ωr is the rotor angular velocity, ψf is the flux generated by the permanent magnet that interlinks with the rotor, Te is the electromagnetic torque, and Pn is the number of motor pole pairs.
According to formula (3), control id = 0 to make the stator current vector located on the q axis. At this time, the torque Te and iq are linearly related, realizing the decoupling control of the electromagnetic torque. As shown in Figure 1, the permanent magnet synchronous motor in this paper adopts speed and current dual closed-loop control. In the figure, ω* is the given speed command, ω is the speed feedback, the speed error is input into the speed controller, and the quadrature axis current command i*q is output. Through the current PI controller and coordinate transformation, the IPM switching signal is generated by SVPWM.
Figure 1 High torque permanent magnet synchronous motor control principle block diagram
2 System Design
Figure 2 shows the block diagram of the system structure. This paper uses STM32F103VCH6 main control chip and PM800HSA120 intelligent power module as the core of the system. The hardware control system mainly includes: processor module; detection module, mainly including Hall current detection and resolver interface circuit; main circuit, mainly composed of rectification, soft start, filtering, braking circuit, and PM800HSA120 and its drive, protection, and absorption circuits; switching power supply and other modules, mainly composed of multi-channel DC/DC conversion, DC bus voltage protection, temperature detection protection and other circuits.
Figure 2 High torque permanent magnet synchronous motor hardware system structure block diagram
2.1 Hardware system design
2.1.1 Processor module
STM32F103VCH6 is a new 32-bit flash microcontroller based on ARM's Cortex-M3 core. It has a three-stage pipeline and branch prediction function, and a maximum operating frequency of 72 MHz, which can meet the processing speed and real-time requirements of this system. It has two high-performance 12-bit 16-channel A/D converters, two 16-bit embedded dead-zone control 6-PWM timers designed specifically for motor drive, and a variety of peripherals and interfaces such as SPI and USB 2.0 are integrated on the chip [5]. As shown in Figure 2, this system makes full use of the on-chip resources of STM32, using it to receive and process feedback signals such as current and position, receive and process various error protection signals, and execute motor control algorithms. [page]
2.1.2 Detection module
The detection module mainly includes current detection circuit and position detection circuit. The current detection adopts Lime current type Hall sensor.
LT308-S7 has the advantages of strong anti-interference ability, high sensitivity, good linearity, and small temperature drift. In order to reduce the detection error when the current is weak, this paper designs a current detection circuit with adjustable gain as shown in Figure 3. The current signal output by the sensor is converted into a voltage signal Vi after being sampled by a precision resistor. After passing through a voltage follower circuit, a three-stage amplifier circuit, and a Schottky diode clamp circuit, the output voltage Vo (Vo = 3nVi / 20 + 1. 5, n is the amplification factor) is sent to the A/D module of STM32 for processing. Among them, the switch chip DG403 is controlled by STM32 to adjust the gain of the current detection circuit. A large gain is selected for a small current, and vice versa for a large current. Since the rated current of a high-torque motor can reach 232 A, if the gain of the detection circuit is not adjustable, the amplification gain of the detection circuit is relatively small when the current is weak, and the current detection accuracy will be reduced. The use of a gain-adjustable detection circuit can increase the gain when the current is weak, thereby reducing the detection error and improving the resolution of current detection.
Table 1 shows the corresponding relationship between the DG403 control signal and the gain amplification factor of the current detection circuit.
Table 1 DG403 control signal and gain amplification factor correspondence table
Considering the strong vibration and impact of port machinery [6], this paper uses the resolver YS210XFDW9574A for position detection. Its decoding circuit is shown in Figure 4. The AD2S99 chip is used to provide the excitation signal for the resolver, and the AD2S90 chip is used as the resolver/digital converter (RDC). The AD2S90 communicates with the control chip STM32 in synchronous serial mode (SPI). The frequency of the excitation signal source of the AD2S99 can be set through the SEL1, SEL2, and FBIAS pins. Here, the excitation frequency is set to 10 KHz. The output signal SYNREF generated by the internal processing of the AD2S99 is connected to the REF pin of the AD2S90, which can compensate for the phase deviation from the primary side to the secondary side of the resolver and ensure its conversion accuracy.
Figure 3 Current detection circuit
Figure 4: Resolver decoding circuit
Figure 5 shows the rotary transformer excitation conditioning circuit. The rotary transformer excitation signal is provided by AD2S99. The excitation conditioning circuit amplifies and filters the excitation signal. The external power supply of the excitation conditioning circuit adopts ± 15 V dual power supply to ensure the circuit static operating point zero adjustment; Ci1 is a coupling capacitor, which blocks DC and passes AC; Cf1 is used for phase compensation; NPN and PNP transistors form a push-pull circuit to eliminate crossover distortion.
Figure 5: Rotary transformer excitation conditioning circuit
2.1.3 Main circuit
The rectifier circuit of the main circuit uses the DD600N12 rectifier module; the soft start circuit uses the CM600HU-24F IGBT power switch to replace the relay to improve the system reliability. When the capacitor bank is charged to 80% of the rated voltage of the busbar, the IGBT is connected to the circuit; 16 6800 μF electrolytic capacitors are selected for the filter circuit; the CM400HU-24F IGBT is selected as the switching element for the brake circuit. Considering the interference, heat dissipation and economy of high-current power devices, the inverter circuit scheme of the 6-unit IPM module PM800HSA120 is selected. PM800HSA120 has an integrated drive and protection circuit, with overvoltage, undervoltage and temperature protection functions, a rated current of 800 A, a reverse bias voltage of 1200 V, and an operating frequency of up to 20 kHz. In order to further improve the anti-interference and reliability of the IPM, this paper strengthens the design of its drive circuit and protection circuit and performs some additional processing. As shown in Figure 6, the IPM drive signal is differentially processed, and the six-way drive signal sent by the control chip STM32 is converted into 12-way signals using a differential drive chip, and then restored to 6-way drive signals using a differential receiving chip on the IPM drive board, and then sent to the IPM after being isolated and driven by a high-speed optical coupler, as shown in Figure 7, to suppress common-mode interference signals and enhance the anti-interference performance of the IPM drive signal. Figure 7 (a) shows the isolated drive circuit of the W phase; the three-phase upper bridge arm is powered by an isolated power supply, and the three-phase lower bridge arm is powered by a 15 V power supply. Figure 7 (b) shows the W phase upper bridge arm isolated power supply circuit.
The fault signal processing circuit of IPM is shown in Figure 8. The error signal is first isolated and filtered by an optical coupler, and then passes through an inverting Schmitt trigger. On the one hand, the voltage signal is reversed, and on the other hand, the error signal is waveform-shaped, which has a certain inhibitory effect on the interference signal. Finally, the processed IPM error signal is input into the control chip STM32 for corresponding processing. [page]
Figure 8 IPM error signal processing circuit
Since the switching frequency of IPM is high and there is parasitic inductance in the power circuit, a high surge voltage will be generated during the IPM switching process, causing impact on the device and affecting the performance and service life of the device. For this reason, an IPM buffer circuit as shown in Figure 9 is designed to reduce the voltage and current spikes during the IPM opening and closing process, thereby reducing the switching loss of the device and protecting the safe operation of the device. Among them, the ultra-fast recovery diode RM25HG-24S is selected as the buffer diode, which has a withstand voltage of 1200 V and a maximum reverse recovery time of 300 ns; considering the driving current frequency of this system and the performance of the IPM itself, the IPM operating frequency is selected as 8 KHz, and the DC bus parasitic inductance is taken as 50 nH. According to calculations and experiments, the buffer capacitor Cs = 3 μF and the buffer resistor Rs = 12 Ω are finally selected.
Figure 9 IPM buffer circuit
2.2 System software design
The system software is mainly composed of the main program and the interrupt service program. The main program completes the initialization of various software and hardware, motor initial position detection and motor start-up, etc. The interrupt service program includes the PWM interrupt subroutine and the external interrupt protection subroutine. The PWM interrupt subroutine is the core of the control system, which mainly completes the acquisition and processing of rotor current and speed, PID adjustment, calculation and selection of voltage vector, PWM generation, etc. The external interrupt subroutine mainly includes bus voltage over-voltage, under-voltage protection, startup protection and temperature protection. When the IPM has an error signal, the STM32 controls the TIM1_BKIN signal of the advanced control timer to prohibit PWM output to ensure the safety of the system. Figure 10 is the flow chart of the PWM interrupt service program.
Figure 10 PWM interrupt service routine
3 Experimental Results
As shown in Figure 11, the STM32 control board and IPM driver board of the permanent magnet synchronous motor control system designed in this paper are real objects. Unit and system experiments were carried out on a high-torque permanent magnet synchronous motor with a rated power of 132 kW, a rated current of 232 A, and an input voltage of 380 V. Figure 12 shows the PWM waveform of the upper and lower bridge arms of the W phase, and the test PWM frequency is 8 KHz (cycle 125 μs); Figure 13 shows the current waveform of the W phase when the motor is running at no load, indicating that the software and hardware modules of the control system can operate effectively.
Figure 11 Control circuit
4 Conclusion
This paper proposes a control system for a large-torque permanent magnet synchronous motor based on STM32. The STM32 processor module, gain-adjustable current detection circuit, resolver interface circuit, IPM drive protection circuit, etc. are designed. The vector control method is used to realize the speed and torque control of the permanent magnet synchronous motor, and experimental verification is carried out, providing a stable, reliable and cost-effective solution for the drive control of large-torque permanent magnet synchronous motors.
Previous article:Design and implementation of car remote anti-theft system based on STM32F
Next article:Design and implementation of CMMB intelligent network monitoring system
Recommended ReadingLatest update time:2024-11-16 14:30
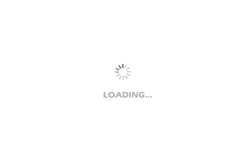
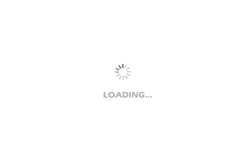
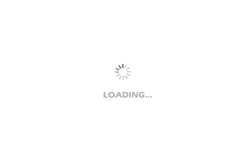
- Popular Resources
- Popular amplifiers
Professor at Beihang University, dedicated to promoting microcontrollers and embedded systems for over 20 years.
- Innolux's intelligent steer-by-wire solution makes cars smarter and safer
- 8051 MCU - Parity Check
- How to efficiently balance the sensitivity of tactile sensing interfaces
- What should I do if the servo motor shakes? What causes the servo motor to shake quickly?
- 【Brushless Motor】Analysis of three-phase BLDC motor and sharing of two popular development boards
- Midea Industrial Technology's subsidiaries Clou Electronics and Hekang New Energy jointly appeared at the Munich Battery Energy Storage Exhibition and Solar Energy Exhibition
- Guoxin Sichen | Application of ferroelectric memory PB85RS2MC in power battery management, with a capacity of 2M
- Analysis of common faults of frequency converter
- In a head-on competition with Qualcomm, what kind of cockpit products has Intel come up with?
- Dalian Rongke's all-vanadium liquid flow battery energy storage equipment industrialization project has entered the sprint stage before production
- Allegro MicroSystems Introduces Advanced Magnetic and Inductive Position Sensing Solutions at Electronica 2024
- Car key in the left hand, liveness detection radar in the right hand, UWB is imperative for cars!
- After a decade of rapid development, domestic CIS has entered the market
- Aegis Dagger Battery + Thor EM-i Super Hybrid, Geely New Energy has thrown out two "king bombs"
- A brief discussion on functional safety - fault, error, and failure
- In the smart car 2.0 cycle, these core industry chains are facing major opportunities!
- The United States and Japan are developing new batteries. CATL faces challenges? How should China's new energy battery industry respond?
- Murata launches high-precision 6-axis inertial sensor for automobiles
- Ford patents pre-charge alarm to help save costs and respond to emergencies
- New real-time microcontroller system from Texas Instruments enables smarter processing in automotive and industrial applications