With the widespread application of integrated circuits and embedded computers in automobiles, the number of electronic controllers in modern automobiles is increasing. Common ones include electronic fuel injection devices of engines, anti-lock brake devices (ABS), airbag devices, electric door and window devices, active suspension, etc. Although the increase of electronic control systems has improved the power, economy and comfort of cars, the increased complex circuits have also reduced the reliability of cars and increased the difficulty of maintenance. From the perspective of wiring, most traditional electronic gas systems use a single point-to-point communication method, with little connection between each other, which will inevitably lead to a large wiring system. Therefore, a new concept, the CAN local area network of electronic controllers on cars, has come into being. In order to enable parts produced by different manufacturers to work in coordination on the same car, standards must be formulated. According to relevant ISO standards, the topology of CAN is a bus, so it is called a CAN bus. The CAN bus is designed as a microcontroller communication in the automotive environment, exchanging information between various electronic control devices ECN on the vehicle, and exchanging information between various electronic control devices ECN on the vehicle to form an automotive electronic control network.
Controller Area Network (CAN) is a multi-master serial communication bus. The basic design specifications require high bit rate, high electromagnetic interference resistance, and the ability to detect any errors. The application of CAN in automobiles has many industry standards or international standards, such as ISO11992 and ISO11783 of the International Organization for Standardization (ISO) and SAE J1939 of the Society of Automotive Engineers. CAN bus has been included in the design of automobiles as a standard device.
Introduction to CAN bus
CAN communication protocol specifies 4 different frame formats, namely data frame, remote frame, error frame and overload frame. Communication coordination is based on the following basic rules: bus access, arbitration, encoding/decoding, error marking and overload marking. CAN complies with the OSI model. According to the OSI benchmark model, there are only three layers: physical layer, data link layer and request layer, but the application layer still needs to be defined by the user. As a serial communication network that effectively supports distributed control or real-time control, the CAN bus has applications ranging from high-speed networks to low-cost multi-line networks. For example, the bit rate of CAN in applications such as engine control components, ABS, and anti-skid systems in automobiles can be as high as 1Mbps. At the same time, it can be used cheaply in electrical systems of transportation vehicles, such as electrical windows, light beams, seat adjustments, etc., to replace the required hardware connections. Its transmission medium is twisted pair, the communication rate can reach up to 1Mbps/40m, the direct transmission distance can reach up to 10km/5kbps, and the number of connected devices can reach up to 110. CAN is a multi-master working mode with flexible communication mode. It does not require node information such as station address, and adopts non-destructive bus arbitration technology to meet real-time requirements. In addition, CAN uses a short frame structure to transmit signals, with short transmission time and strong anti-interference ability.
The main differences between the CAN bus and other communication protocols are two aspects: First, the message transmission does not contain the target address. It is based on the whole network broadcast. Each receiving station filters the message according to the identifier reflecting the nature of the data in the message. Its characteristics are online and offline, plug-and-play, and multi-station reception; the other aspect is that it particularly strengthens data security to meet the needs of control systems and other systems with higher data requirements.
In the design of modern cars, CAN bus has become a trend in building car networks; and as a car network that is directly connected to each ECU inside the car and is responsible for the transmission of commands, the sending and sharing of data, its reliability and stability are closely related to the performance of the whole vehicle. The design and development of this paper is based on a simulation platform built under experimental conditions, and the communication between nodes is carried out through peer-to-peer CAN communication nodes. The experiment shows that its operating performance is stable and reliable, but its practical application still needs further research and improvement, and the communication processing capability, error correction and fault tolerance of the program need to be further improved.
Previous article:Discussing the embedded design of VxWorks to realize automatic sending of MMS
Next article:Application of LPC21XX Series Microcontroller Based on ARM7 in BAS
Recommended ReadingLatest update time:2024-11-16 16:32
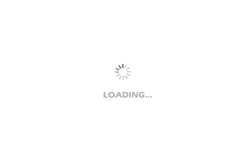
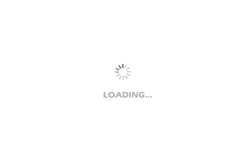
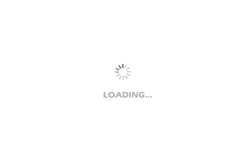
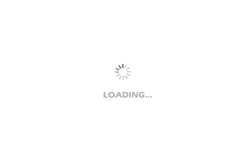
Professor at Beihang University, dedicated to promoting microcontrollers and embedded systems for over 20 years.
- Innolux's intelligent steer-by-wire solution makes cars smarter and safer
- 8051 MCU - Parity Check
- How to efficiently balance the sensitivity of tactile sensing interfaces
- What should I do if the servo motor shakes? What causes the servo motor to shake quickly?
- 【Brushless Motor】Analysis of three-phase BLDC motor and sharing of two popular development boards
- Midea Industrial Technology's subsidiaries Clou Electronics and Hekang New Energy jointly appeared at the Munich Battery Energy Storage Exhibition and Solar Energy Exhibition
- Guoxin Sichen | Application of ferroelectric memory PB85RS2MC in power battery management, with a capacity of 2M
- Analysis of common faults of frequency converter
- In a head-on competition with Qualcomm, what kind of cockpit products has Intel come up with?
- Dalian Rongke's all-vanadium liquid flow battery energy storage equipment industrialization project has entered the sprint stage before production
- Allegro MicroSystems Introduces Advanced Magnetic and Inductive Position Sensing Solutions at Electronica 2024
- Car key in the left hand, liveness detection radar in the right hand, UWB is imperative for cars!
- After a decade of rapid development, domestic CIS has entered the market
- Aegis Dagger Battery + Thor EM-i Super Hybrid, Geely New Energy has thrown out two "king bombs"
- A brief discussion on functional safety - fault, error, and failure
- In the smart car 2.0 cycle, these core industry chains are facing major opportunities!
- The United States and Japan are developing new batteries. CATL faces challenges? How should China's new energy battery industry respond?
- Murata launches high-precision 6-axis inertial sensor for automobiles
- Ford patents pre-charge alarm to help save costs and respond to emergencies
- New real-time microcontroller system from Texas Instruments enables smarter processing in automotive and industrial applications
- In fact, Valentine's Day 20200214 was cancelled
- This problem occurs when setting up the stm8 environment. What is the reason? Thank you
- dsp28335 data space
- [Xianji HPM6750 Review 8] Detailed description of the small twists and turns encountered by SPI peripherals
- MSP430 MCU Development Record (16)
- I posted a thread about icebabycool. He didn't answer the question but laughed at me instead of showing my low IQ. Please punish this kind of rogue behavior severely.
- Help with POE design issues
- [Voice and vision module based on ESP32S3] Material unpacking—ESP32S3 BOX
- PCBA intelligent detection fixture, one-click generation of test reports
- How to choose the right inductor in a switching power supply