Introduction
The coal feeder control system designed in this paper is mainly used in the coal pulverizing system of thermal power plants. It cooperates with the coal pulverizer equipment to undertake the task of quantitatively and evenly supplying coal to the system. It is an important auxiliary equipment of thermal power plants. This system can also be applied to the metering and conveying system of bulk materials in metallurgy, chemical industry and other departments, which is of great significance for saving energy, improving economic benefits and ensuring safety.
Figure 1 Self-tracking power supply circuit
Figure 2 4~20mA current generation circuit
Design of control system hardware
The control system mainly includes the detection of weighing sensor signals, the detection of digital speed sensor signals, the scanning of keyboard input signals, the display of LCD screen, and some alarm devices. Since this design has high requirements for the main controller, Samsung's low-power ARM processor S3C44B0x based on ARM7TDMI-S core is finally used as the main controller of the system.
The acquisition of weighing sensor signals is one of the most important factors affecting the control accuracy of this system. In this design, the sensor bridge is designed to be in the form of four strain gauges under force. At the same time, since the output signal of the strain gauge sensor is very small, the voltage of the bridge is required to be particularly stable, so this system uses a symmetrical power supply with positive and negative pressure self-tracking performance, as shown in Figure 1.
The sensor signal is first amplified and filtered, and then sent to the A/D controller. The S3C44B0x processor integrates an 8-way 10-bit A/D controller, a zero comparator and an internally generated comparison clock signal, and supports software-enabled sleep mode, so the sensor signal can be measured very accurately. And by using this processor, the system does not need to expand the A/D conversion chip, thus reducing the complexity of the system.
The speed sensor detects the speed of the belt. Since the speed of the motor rotation is generally different from the speed of the belt, there is a proportional coefficient. In order to ensure accuracy, this design uses a speed sensor alone. The pulse output of the speed sensor is proportional to the belt speed. By sending the speed signal of the belt and the weight signal of the weighing sensor to the microprocessor for processing, the actual flow rate in tons/hour is obtained. The
required coal feeding amount is input through the keyboard, the actual coal feeding amount and the required coal feeding amount are PID calculated, and the generated control signal is used to control the frequency converter, thereby controlling the speed of the motor. The frequency converter used in this system is Siemens MMV400. This frequency converter is set to 4~20mA current control. The controller compares the user's instructions and the on-site status feedback and sends 4~20mA current to the analog input port of the frequency converter. Then the frequency converter converts the input current signal into the corresponding frequency and outputs it to control the motor. The circuit that generates 4~20mA current is shown in Figure 2. [page]
The control data of the ARM processor is first sent to the D/A controller (TLC5615) through optoelectronic isolation, converted into a 0~2V voltage signal, and then passed through the V/I converter (AD694) to generate a 4~20mA current signal to accurately control the motor speed.
The LCD display screen displays the motor speed, required coal feed, actual coal feed, and belt speed. The S3C44B0x integrates an LCD controller that can transmit the data in the display cache to the external LCD drive circuit and support monochrome, 4 or 16-level grayscale LCD and 256-level color LCD. A large number of I/O ports are used as relay signal outputs. In addition, the S3C44B0x can also communicate with the host computer through the serial port RS-232.
Design of control system software
The coal feeder control system software uses the embedded real-time multi-tasking operating system mC/OS-II. It is a real-time multi-tasking operating system with open source code, portability, curability, scalability, and preemptiveness. Most of its source code is written in ANSI C, which is easy to port and runs stably and reliably. At present, it has been successfully ported on dozens of microprocessors and microcontrollers from 8 bits to 64 bits.
Porting of mC/OS-II on S3C44B0x The porting of
mC/OS-II mainly includes: declaring 3 macros (open interrupt, close interrupt and task switching); setting the growth direction of the stack; declaring 10 compiler-related data types; writing 6 operating system-related functions in C language (OS-CPU-CC task stack initialization and 5 hook functions); writing 4 processor-related functions in assembly language (OS-CPU.ASM). The
4 processor-related functions written in assembly language are as follows.
mC/OS-II needs to disable interrupts before accessing the critical interrupt of the code, and re-enable interrupts after the access. The operating system uses the two functions OS_ENTER_CRITICAL() and OS_EXIT_CRITICAL() to enable and disable interrupts.
In mC/OS-II, OS-STK-GROWTH is used to specify the growth direction of the stack. 0 means growth from low address to high address, and 1 means the opposite. However, the ADS compiler used only supports the growth from high address to low address, so OS-STK-GROWTH should be set to 1.
Then write 4 processor-related functions in assembly language and put them in the function OS-CPU.ASM, which completes the porting of the OS-CPU.ASM file. The upper-level task scheduling part does not require any changes. After completing the above work, mC/OS-II can run normally on the S3C44B0x processor.
Division and scheduling of system tasks
The tasks in the embedded real-time system are different from the subroutine modules in the front-end and back-end systems. Generally, a task corresponds to an independent main program, which can call subroutines and use various system resources such as interrupts. The task division of embedded systems is to divide the things to be processed in the system into relatively independent task modules, establish tasks one by one in sequence, and assign different priorities. In the main program, what needs to be done is to establish the tasks of these modules, and then execute the task with the highest priority in the ready task queue each time. According to the characteristics of this control system, the tasks can be divided as follows: keyboard scanning, sensor signal detection, motor speed
slowdown, motor speed increase, and LCD display tasks.
The task scheduling of mC/OS-II is based on priority, so different priorities must be assigned to each task, among which 0, 1, 2, 3, OS_LOWEST_PRIO-3, OS_LOWEST_PRIO-2, OS_LOWEST_PRIO-1, OS_LOWEST_PRIO, these priorities are used by the system, so they must be retained. According to the
real-time requirements and importance of each task, the priorities of the above tasks are assigned as follows: 12, 6, 7, 8 and 13, etc. The lower the task priority number, the higher the priority.
When the coal feeder control system is started, if everything is normal, the coal delivery task will be carried out. During operation, if the sensor signal detects that the amount of coal fed is too much, a signal is sent to the motor slowing task, otherwise, a signal is sent to the motor acceleration task. In addition, when there are some faults or dangers, a signal is sent to the shutdown task. In short, in the control system, signals and messages are continuously transmitted, so that each task is continuously switched and operated, so that the entire system can work normally and continuously.
Conclusion
Based on the introduction of the structure of the coal feeder, this paper introduces the hardware principle and software design of its control system. After multiple on-site commissioning and operation, this control system can well complete the coal feeding task of the power plant.
References:
[1]. S3C44B0x datasheet http://www.dzsc.com/datasheet/S3C44B0x_589522.html.
[2]. ARM7TDMI-S datasheet http://www.dzsc.com/datasheet/ARM7TDMI-S_1231795.html.
[3 ]. RS-232 datasheet http://www.dzsc.com/datasheet/RS-232_584855.html.
Previous article:Digital Home Media Center System Designed with IXP Network Processor
Next article:Hardware Design of Frequency Hopping Radio Central Control Unit and Frequency Hopping Unit
Recommended ReadingLatest update time:2024-11-16 16:37
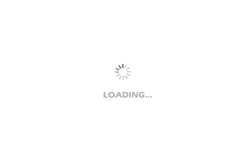
Professor at Beihang University, dedicated to promoting microcontrollers and embedded systems for over 20 years.
- Innolux's intelligent steer-by-wire solution makes cars smarter and safer
- 8051 MCU - Parity Check
- How to efficiently balance the sensitivity of tactile sensing interfaces
- What should I do if the servo motor shakes? What causes the servo motor to shake quickly?
- 【Brushless Motor】Analysis of three-phase BLDC motor and sharing of two popular development boards
- Midea Industrial Technology's subsidiaries Clou Electronics and Hekang New Energy jointly appeared at the Munich Battery Energy Storage Exhibition and Solar Energy Exhibition
- Guoxin Sichen | Application of ferroelectric memory PB85RS2MC in power battery management, with a capacity of 2M
- Analysis of common faults of frequency converter
- In a head-on competition with Qualcomm, what kind of cockpit products has Intel come up with?
- Dalian Rongke's all-vanadium liquid flow battery energy storage equipment industrialization project has entered the sprint stage before production
- Allegro MicroSystems Introduces Advanced Magnetic and Inductive Position Sensing Solutions at Electronica 2024
- Car key in the left hand, liveness detection radar in the right hand, UWB is imperative for cars!
- After a decade of rapid development, domestic CIS has entered the market
- Aegis Dagger Battery + Thor EM-i Super Hybrid, Geely New Energy has thrown out two "king bombs"
- A brief discussion on functional safety - fault, error, and failure
- In the smart car 2.0 cycle, these core industry chains are facing major opportunities!
- The United States and Japan are developing new batteries. CATL faces challenges? How should China's new energy battery industry respond?
- Murata launches high-precision 6-axis inertial sensor for automobiles
- Ford patents pre-charge alarm to help save costs and respond to emergencies
- New real-time microcontroller system from Texas Instruments enables smarter processing in automotive and industrial applications
- Download the free NI white paper "Overcoming the Challenges of Production Test for Complex Devices Under Test"
- DSP Basics--Fixed-point Decimal Operations
- Small Cell Networks and the Evolution of 5G
- A very down-to-earth question: How do capacitors absorb ESD?
- C Language Core Technology (Original Book 2nd Edition)
- Do you know the chip manufacturer of this Bluetooth module?
- ADS1.2 Issues
- Limited-time free download | NI white paper: "Three Visions of the O-RAN Alliance"
- Disassembly of isolator
- Which domestic motor drive company do you think is the most promising?