1 Introduction
Thyristor, also known as silicon controlled rectifier, is the most widely used high-power conversion device in industrial applications. Thyristor mainly adopts phase-shift trigger control in rectifier occasions such as sintering furnaces and arc furnaces, that is, the output is controlled by adjusting the phase of the thyristor conduction moment. Traditional thyristor triggers use analog control circuits, which cannot overcome their inherent shortcomings. Compared with analog control circuits, the main advantages of digital control circuits are stable output waveforms and high reliability, but their disadvantages are that the circuit is relatively complex and the control accuracy is not high when the phase-shift trigger angle is large. With the development of single-chip microcomputer technology, the advantages of control circuits composed of single-chip microcomputers are more obvious. In addition to having the same advantages as digital trigger circuits, it is also because its phase-shift trigger angle is calculated by software, the trigger circuit structure is simple, the control is flexible, the temperature drift is small, the control accuracy can be compensated by software, and the phase-shift range can be adjusted arbitrarily. It has been widely recognized by the industry. Taking the three-phase bridge fully controlled rectifier circuit as an example, the design of the hardware circuit of the thyristor trigger composed of a single-chip microcomputer and the method of realizing phase-shift trigger pulse control by software are introduced.
2. Composition of MCU trigger
The thyristor trigger controlled by the single-chip microcomputer is mainly composed of four parts: synchronization signal detection, CPU hardware circuit, reset circuit and trigger pulse drive circuit, as shown in Figure 1. The CPU obtains the trigger signal through the detection circuit, and implements the predetermined program flow through programming according to the requirements of the circuit to be controlled. The trigger pulse signal is output through the single-chip microcomputer I/O terminal within the corresponding time period. The reset circuit can ensure the safe and reliable operation of the system.
3 Control principle of phase-shift trigger pulse
Phase control requires that the natural commutation point of the converter circuit be used as a reference, and after a certain phase delay, a trigger signal is output to turn on the thyristor. In practical applications, the natural commutation point is given by a synchronization signal, and then synchronization is achieved in the CPU by the method of synchronous voltage zero-crossing detection, and the CPU control software completes the phase shift calculation and outputs the trigger pulse according to the phase shift requirement.
Figure 2 is a three-phase bridge fully controlled rectifier circuit. The timing of the trigger pulse signal output can also be determined by the single chip microcomputer according to the synchronization signal level. When the single chip microcomputer detects the A phase synchronization signal, the output pulse timing usually adopts the phase shift trigger pulse method, that is, a synchronization voltage signal and a timer are used to complete the calculation of the trigger pulse. This is feasible when the three-phase circuit is symmetrical. Because the three phases are completely symmetrical, each phase is 120° apart from each other, the circuit commutates every 60°, and the commutation timing is known in advance. This method uses less single chip microcomputer resources, only one synchronization signal is required, the circuit is relatively simple, but the software design workload is slightly larger.
[page]
Because only one synchronous input signal is used, the trigger pulse delay of all thyristors is based on it. In order to ensure the accuracy of the trigger pulse delay phase, a timer is used to measure the cycle of the synchronous voltage signal, and the time corresponding to the electrical angle of 60° and 120° is calculated from it. Since the trigger circuit of the three-phase bridge full-controlled rectifier circuit must trigger and turn on a thyristor every 60°, that is, a trigger pulse signal must be output every 60°, so the first trigger pulse signal as a reference must be adjusted to less than 60° to ensure that the trigger pulse is not missed. When the A-phase synchronous voltage signal is used as a reference, when the single-chip microcomputer detects the positive jump of the A-phase synchronous voltage signal, the timer is started. When the timer overflows, the first trigger pulse signal is output. After that, the calculated cycle determines that a trigger pulse is output every 60° until the single-chip microcomputer detects the positive jump of the A-phase synchronous signal again. This cycle ends and the next cycle begins. It should be noted that the time from the single-chip microcomputer detecting the positive jump of the synchronous voltage to the output of the first trigger pulse signal must be adjusted to less than or equal to 60° electrical angle time, otherwise the trigger pulse will be missed. The time of the first trigger pulse relative to the positive jump of the synchronization signal can be adjusted according to the trigger timing of the three-phase bridge full-controlled rectifier circuit, as shown in Figure 3. In Figure 3, α1 is the trigger delay angle, (α2-α1) and (α4-α3) are both trigger narrow pulse widths of 60°, α0 is a standard cycle of the synchronization pulse signal of 360°; g0 represents the synchronization pulse signal, gl, g2, g3, g4, g5, and g6 represent VT1, VT2, VT3, VT4, VT5, and VT6 trigger pulse signals respectively; 0 represents a low level, and 1 represents a high level
According to the timing requirements of the thyristor conduction in the three-phase bridge fully controlled rectifier circuit, the output trigger pulse is divided into three cases:
(1) When the phase-shift trigger delay angle α≤60°, the first pulse output based on the A-phase synchronization signal and the delay angle time should be the trigger signal of the A-phase VT1 thyristor. The trigger delay time and the timing of the trigger pulse do not need to be adjusted. After that, the trigger signals of the VT2, VT3, VT4, VT5, and VT6 thyristors are output in sequence every 60°.
(2) When the phase-shift trigger delay angle is 60°<α≤120°, in order to ensure that the trigger pulse is not missed, the timing of the trigger delay angle should be adjusted within 60°, that is, minus a 60° time. At the same time, the timing of the output trigger pulse should also be adjusted. At this time, the first output trigger pulse signal should be the trigger signal of the B phase, VT6 thyristor, and then the trigger signals of VT1, VT2, VT3, VT4, and VT5 thyristors are output in sequence every 60°.
(3) When the phase-shift trigger delay angle α>120°, in order to adjust the timing of the trigger delay angle within 60° to ensure that the trigger pulse is not missed, it is necessary to subtract 120° and adjust the trigger pulse timing accordingly. At this time, the first output trigger pulse signal should be the trigger signal of the C-phase VT5 thyristor, and then the trigger signals of VT1, VT2, VT3, and VT4 thyristors are output in sequence every 60°.
4 Trigger Hardware Composition
Figure 4 shows the hardware circuit diagram of the phase-shift trigger pulse control controlled by the single-chip microcomputer. The single-chip microcomputer uses AT89C2051, which belongs to the MCS-51 series of small single-chip microcomputers with a total of 20 pins and 2 KB memory. The input of the synchronization signal passes through the resistor R1, which plays the role of current limiting and protection. The sinusoidal synchronization signal is clipped by the two clamping diodes VD1 and VD2 that limit the input voltage of the comparator, and then sent to the input end of the comparator LM339. The output of LM339 is a square wave with a 180° phase angle that is the same as the power supply phase. When the synchronization detection signal jumps positively, it is reversed and interrupted to provide synchronization instructions to the INT0 (pin 6) of the single-chip microcomputer. On the surface, it seems to be an external interrupt signal input, but in fact it is to measure the width of the pulse, which is determined by the time the signal arrives. Using this comparison circuit, whether the input synchronization voltage signal is high or low, the output signal of LM339 can accurately reflect the zero-crossing point of the synchronization input signal. R2 and C3 filter the output signal to avoid fluctuations in the output signal. Since AT89C2051 is an 8-bit single-chip microcomputer, the internal calculation of the trigger is 8-bit digital quantity. The trigger delay angle range is 0°~180°, and the control accuracy is 0.7°. Although the control accuracy is limited by the number of internal calculation bits, it is sufficient to meet general control requirements.
P1.2~P1.7 (pins 14~19) of the Pl port of AT89C2051 are used to output the trigger pulse signals of the three-phase bridge full-controlled rectifier circuits VT1~VT6 respectively. The 6-way pulse signal is inverted and amplified by 741504 to drive the power amplifier TD62004. The output of the device is connected to the primary winding of the pulse transformer. In order to make the reset more reliable, an advanced dedicated power-on reset device X25045 is used. The device has a programmable timer and adopts an SPI bus structure. The function of the timer watchdog is to ensure that within the set time, if the system program is dead and cannot access the chip select terminal of X25045 regularly, X25045 will be able to reset the system. This improves the reliability of the system and provides an independent protection system for the microcontroller. Other ports such as P1.0~P1.1 (pins 12 and 13) of the P1 port can be used as overvoltage and overcurrent indications, and P3.4~P3.5 (pins 8 and 9) of the P3 port can be used as overvoltage and overcurrent input terminals. The remaining ports of the P3 port can collect the voltage negative feedback signal from the rectifier end and perform digital PI adjustment after A/D conversion to form a voltage negative feedback closed-loop control to ensure the stability of the rectifier output voltage.
[page]
5 Design of Phase-Shift Trigger Pulse Control Software
The control software of the phase-shift trigger pulse can facilitate delay calculation. The software completes system initialization, input of initial values, calculation of electrical angle time and sends them to the timer, and realizes the processing of trigger delay angle through external interruption. Since all ports of AT89C2051 output high level during power-on reset, in order to ensure that all thyristors are not triggered by trigger signals during reset, low level should be used as the signal to effectively trigger the thyristor. The flow chart of the phase-shift trigger pulse control software is shown in Figure 5.
6 Conclusion
In the experiment, digital PI regulation is added to form a voltage negative feedback closed-loop control, which makes the output voltage run stably, improves the symmetry and stability of the trigger pulse, and the trigger delay angle can reach up to 180°, which improves the performance index of the trigger and the reliability of the converter. This design scheme realizes the single-chip microcomputer control of the thyristor trigger, embodies the characteristics of simple control circuit, easy adjustment and low CPU resource occupation, and is an ideal and easy-to-promote thyristor trigger control design scheme.
Previous article:Application of single chip microcomputer in the brightness adjustment system of full automatic CCFL film viewer
Next article:Portable electronic product analysis solution based on single chip microcomputer
Recommended ReadingLatest update time:2024-11-16 18:06
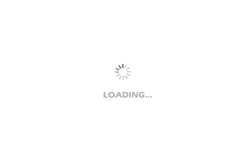
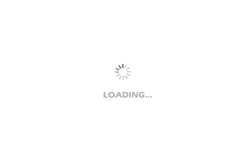
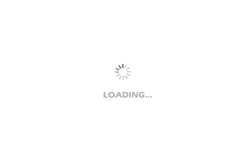
- Popular Resources
- Popular amplifiers
-
Wireless Sensor Network Technology and Applications (Edited by Mou Si, Yin Hong, and Su Xing)
-
Modern Electronic Technology Training Course (Edited by Yao Youfeng)
-
Modern arc welding power supply and its control
-
Small AC Servo Motor Control Circuit Design (by Masaru Ishijima; translated by Xue Liang and Zhu Jianjun, by Masaru Ishijima, Xue Liang, and Zhu Jianjun)
Professor at Beihang University, dedicated to promoting microcontrollers and embedded systems for over 20 years.
- Innolux's intelligent steer-by-wire solution makes cars smarter and safer
- 8051 MCU - Parity Check
- How to efficiently balance the sensitivity of tactile sensing interfaces
- What should I do if the servo motor shakes? What causes the servo motor to shake quickly?
- 【Brushless Motor】Analysis of three-phase BLDC motor and sharing of two popular development boards
- Midea Industrial Technology's subsidiaries Clou Electronics and Hekang New Energy jointly appeared at the Munich Battery Energy Storage Exhibition and Solar Energy Exhibition
- Guoxin Sichen | Application of ferroelectric memory PB85RS2MC in power battery management, with a capacity of 2M
- Analysis of common faults of frequency converter
- In a head-on competition with Qualcomm, what kind of cockpit products has Intel come up with?
- Dalian Rongke's all-vanadium liquid flow battery energy storage equipment industrialization project has entered the sprint stage before production
- Allegro MicroSystems Introduces Advanced Magnetic and Inductive Position Sensing Solutions at Electronica 2024
- Car key in the left hand, liveness detection radar in the right hand, UWB is imperative for cars!
- After a decade of rapid development, domestic CIS has entered the market
- Aegis Dagger Battery + Thor EM-i Super Hybrid, Geely New Energy has thrown out two "king bombs"
- A brief discussion on functional safety - fault, error, and failure
- In the smart car 2.0 cycle, these core industry chains are facing major opportunities!
- The United States and Japan are developing new batteries. CATL faces challenges? How should China's new energy battery industry respond?
- Murata launches high-precision 6-axis inertial sensor for automobiles
- Ford patents pre-charge alarm to help save costs and respond to emergencies
- New real-time microcontroller system from Texas Instruments enables smarter processing in automotive and industrial applications