1 Overall design
The remote robot control system consists of three parts: robot intelligent control module, robot monitoring module, and remote control module. Its working process is that the remote PC sends control commands to the robot controller, the processor receives the command from the remote end and sends it to the controller, and the controller controls the robot movement; the robot monitoring system captures the live image through the video camera, transmits it to the remote end, and displays the live image on the remote PC. Its overall structure block diagram is shown in Figure 1.
(1) Robot intelligent control module: This part is the core of the system. It adopts embedded system design, can automatically run and process data, and manage and control the robot monitoring module through RS485 bus. The controller uses GPRS module to realize the communication between the robot intelligent control module and the external network, so that users can remotely control the robot intelligent control module through SMS and the Internet. At the same time, the controller also provides users with a human-machine interface through keyboard and display screen, which is convenient for users to realize local control.
(2) Robot monitoring module: The robot monitoring module controls each drive unit by forming several small control systems through single-chip microcomputers, and forms a network of these small control systems through a unified control bus, which is connected to the robot intelligent control module and controlled by the robot intelligent control module.
2 System Hardware Design
2.1 Hardware System Structure
This paper selects Samsung's S3C4480 chip as the central control module of the controller, which is responsible for communicating with GPRS communication module, robot monitoring module, data storage, keyboard, display screen and other modules as well as data collection and processing of the system. It is mainly divided into two parts: robot intelligent control module and robot monitoring module.
2.2 Hardware Design of Robot Intelligent Control Module
The circuit design part of the controller is mainly divided into the following modules:
(1) Peripheral circuit module of ARM processor S3C4480: including power management, keyboard, display screen and data and program storage devices such as SDRAM and Flash.
(2) GPRS communication module and its peripheral circuit design: GPRS module is used to realize data transmission between remote users and control terminals. This paper selects Siemens' MC35I module. Its peripheral circuit design mainly completes the circuit design of the power supply part of the MC35 module, data transmission, module startup and shutdown and working mode indication.
(3) Serial port expansion: GPRS modem dial-up Internet access requires the processor to provide it with a complete 9-wire serial port, while S3C4480 only provides a 3-wire serial port. Therefore, this paper expands the complete 9-wire serial port expansion by connecting an external dual-channel universal asynchronous receiver and transmitter STl6C2550.
(4) RS485 converter: Through TI's RS485 interface chip 75LBC184, the conversion between the TTL level and RS485 level of the S3C4480 (microcontroller) serial port is realized. The input impedance of this chip is twice the standard input impedance of RS485 (≥24kΩ), so 64 nodes can be connected on the bus.
2.2.1 Design of peripheral circuits of ARM processor
2.2.1.1 Use of development board resources
The development board provides a wealth of external resources. In addition to the necessary configurations such as power supply, clock source, reset circuit, etc., some resources used by the system are briefly introduced below:
External memory configuration: 2M Bytes Flash, 8M Bytes SDRAM, providing storage space for the storage and operation of system data, programs and operating system kernel.
Extended network port: 10M network port, RTL8019AS, this part is used to download the operating system kernel and application programs from the PC.
LCD interface (with LCD display): 320X240, STN, 16 levels of grayscale, maximum 640×480256 colors.
Keyboard: The keyboard and LCD interface are used to provide users with a local controlled human-computer interaction interface.
Serial port: Two standard RS232 interfaces. Used to connect to a PC and debug the system through a hyperterminal.
JTAG interface: Use a JTAG emulator to perform online simulation through the JTAG boundary scan port. Currently, there are two standards for JTAG, namely a 14-pin interface and a 20-pin interface. The development board uses a standard 14-pin JTAG interface, supports ARM7 series processors, supports STD, parallel port connections, and supports network debugging functions.
2.2.1.2 Allocation of system memory
[page]
S3C4480 supports big/little end selection of data storage (selected by external pins); has 8 memory banks, each memory bank can reach 32MB, totaling up to 256MB; the access size of all memory banks can be changed (8-bit/16-bit/32-bit); among the 8 memory banks, Bank0~Bank5 can support ROM, SDRAM; Bank6 and Bank7 can support ROM, SRAM and SDRAM, etc.; the starting address of 7 memory banks is fixed, and the starting address of 1 memory bank is variable.
The Flash in the development board uses SST39VFl60, 1M×16 bits, as a program memory mainly used to replace ROM, and can also store some important data when necessary. The SDRAM chip in the development board uses HY57V641620, 4M×16bit, with a storage capacity of 8MB. Use SDRAM as system memory.
2.2.2 GPRS module MC35 and its peripheral circuit design
2 2.2.1 MC35 module
MC35 is a new generation of wireless communication GPRS module launched by Siemens. It mainly consists of six parts: GSM baseband processor, GSM radio frequency module, power supply module (ASIC), flash memory, ZIF connector, and antenna interface.
2.2.2.2 MC35 peripheral circuit design
(1) MC35I power supply circuit
The module requires a single power supply to provide a voltage of 3.3V to 4.87 (the standard input is 4.27) and a current of 2A. This paper selects LM2576ADJ as the power supply for the module. The chip is a step-down switching voltage regulator with a voltage input range of 10~40V. It uses 12V (obtained through a 220V to 12V transformer) as input and an output of 1.5V. The circuit design of the power supply part is shown in Figure 2.
(2) Startup and shutdown circuits
The startup circuit consists of an open-drain transistor and a power-on reset circuit. This paper uses program control to implement it. Its circuit diagram is shown in Figure 3, and its simplified circuit is shown in Figure 4.
The first method is manual control. The circuit is shown in Figure 3. It is mainly used for the separate debugging of the MC35I module. When S1 is pressed, the base of Q3 is high, Q3 is turned on, and the voltage of the IGT pin is pulled down, which turns off the module.
The shutdown circuit gives the pin a low level greater than 3.5s through the transistor, which can turn off the GPRS module. The circuit design is similar to Figure 3.
2.2.2.3 Data communication circuit
In terms of electrical characteristics, the serial port of the MC35 module uses the ITU-TV.24 protocol, which is not compatible with the RS232 level. Therefore, level conversion is required. In this system, we use the MAX3238 level conversion chip from TI. The data communication circuit design is shown in Figure 5.
2.2.2.4 SIM card circuit
MC35I also provides 6 SIM card circuit interfaces. The circuit connection diagram of the SIM card reader is shown in Figure 6:
2. 2.3 Serial port expansion module
In order to realize the remote control of the home intelligent controller, it is necessary to dial up to the Internet through GPRS modem MC35. This design uses AT's STl6C2550 to complete the serial port expansion. The circuit connection diagram of STl6C2550 and ARM processor is shown in Figure 7.
In addition, the serial port output of STl6C2550 is TTL level, and MAX3238 is used here to convert the level into the RS232 level of the serial port.
2.2.4 RS485 interface circuit
The home intelligent controller designed in this system uses RS485 bus for home internal network wiring. Since neither the ARM processor 4480 nor the single-chip microcomputer (AT89C52 of Atmel Company selected in this article) provides a ready-made RS485 bus interface, it is necessary to select a conversion chip to realize the interface conversion. This system uses the Yili RS485 interface chip 75LBCl84 produced by TI.
2.2.4.1 RS485 interface circuit design
The serial port outputs of 4480 and single-chip microcomputer are both TTL level, so the connection circuits of 4480 and single-chip microcomputer and 75LBCl84 are consistent, and the circuit diagram is shown in Figure 8.
2.3 Robot monitoring module
The robot monitoring system integrates multiple functions such as robot motion control and video camera on-site shooting. This paper implements the robot drive unit module and other motor device drive unit modules in the robot monitoring module. Each module is composed of a single-chip microcomputer as a controller, and is connected to the RS485 bus through the single-chip microcomputer to form a monitoring network, and is ultimately controlled by the robot intelligent controller.
2.3.1 Infrared robot drive unit control module
The infrared robot drive unit control module is mainly used to control robots containing infrared receiving chips.
[page]
2.3.1.1 Design of infrared transmitting circuit
The infrared transmitting device used in the infrared transmitting circuit is the plastic-encapsulated TSAL6200 infrared transmitting diode. The width and interval of the infrared pulse train are controlled by the time interval of the high and low levels output by the single-chip microcomputer through the I/O port. The modulation circuit is a controllable oscillator composed of two monostable triggers U2A and U2B cascaded from 74LSl23. The circuit diagram is shown in Figure 9.
2.3.1.2 Infrared receiving circuit design
Infrared receiving uses }tS0038B infrared receiver, and the circuit design is shown in Figure 10.
3 System software design
The system software design is mainly divided into three parts: software design of the home system module; RS485 communication protocol design and software design of the communication between the home intelligent controller and the home system; software design of the home intelligent controller. Among them, the software design of the home intelligent controller is the core of the system software design. The software design of this part uses the embedded μClinux operating system as the development platform, which is responsible for data collection and data processing of the home system, and can communicate with remote users to realize remote control, which is the key to realizing the intelligent management of the home system. The system software structure block diagram is shown in Figure 11.
4 Conclusion
This device can be used to control the robot monitoring system, and can also realize remote monitoring of the robot through text messages and other means.
Previous article:Embedded System Design Based on ARM
Next article:C-computer based on ARM and sliding fingerprint sensor
Recommended ReadingLatest update time:2024-11-16 22:32
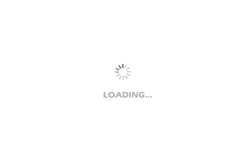
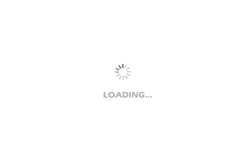
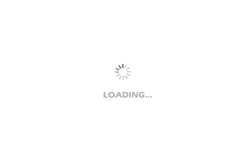
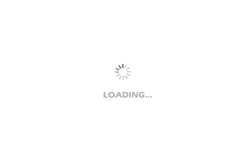
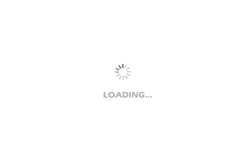
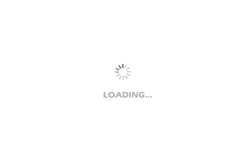
- Popular Resources
- Popular amplifiers
Professor at Beihang University, dedicated to promoting microcontrollers and embedded systems for over 20 years.
- Innolux's intelligent steer-by-wire solution makes cars smarter and safer
- 8051 MCU - Parity Check
- How to efficiently balance the sensitivity of tactile sensing interfaces
- What should I do if the servo motor shakes? What causes the servo motor to shake quickly?
- 【Brushless Motor】Analysis of three-phase BLDC motor and sharing of two popular development boards
- Midea Industrial Technology's subsidiaries Clou Electronics and Hekang New Energy jointly appeared at the Munich Battery Energy Storage Exhibition and Solar Energy Exhibition
- Guoxin Sichen | Application of ferroelectric memory PB85RS2MC in power battery management, with a capacity of 2M
- Analysis of common faults of frequency converter
- In a head-on competition with Qualcomm, what kind of cockpit products has Intel come up with?
- Dalian Rongke's all-vanadium liquid flow battery energy storage equipment industrialization project has entered the sprint stage before production
- Allegro MicroSystems Introduces Advanced Magnetic and Inductive Position Sensing Solutions at Electronica 2024
- Car key in the left hand, liveness detection radar in the right hand, UWB is imperative for cars!
- After a decade of rapid development, domestic CIS has entered the market
- Aegis Dagger Battery + Thor EM-i Super Hybrid, Geely New Energy has thrown out two "king bombs"
- A brief discussion on functional safety - fault, error, and failure
- In the smart car 2.0 cycle, these core industry chains are facing major opportunities!
- The United States and Japan are developing new batteries. CATL faces challenges? How should China's new energy battery industry respond?
- Murata launches high-precision 6-axis inertial sensor for automobiles
- Ford patents pre-charge alarm to help save costs and respond to emergencies
- New real-time microcontroller system from Texas Instruments enables smarter processing in automotive and industrial applications
- GD32L233C-START Evaluation——06.LPUART+DMA+MCU Sleep Wake-up——Comprehensive Test 1
- PCB engineers all know the design skills, you will lose a lot if you don’t read it!
- Understanding of some parameters in DCDC chip?
- [Zero-knowledge ESP8266 tutorial] Quick Start 14-Three IOs control 8 LED lights
- LTE Cat 1 STM32 4G EC200S
- Single-ended to balanced conversion, the actual situation is so different from the simulation, why?
- [NXP Rapid IoT Review] + Preliminary Study on Power Consumption of Some Devices
- Embedded Linux Learning Route Planning
- Today is the summer solstice. I heard that those who went out at noon had no shadow.
- Panta STM32H750 Part 6 (Using timer synchronization to generate a specified number of PWM pulses)