1 BOOT mode selection
When we use the BOOT program of TMS320VC5410, we need to set the DSP to the microcomputer working mode (sample MP/MC=0 after hardware reset). When the boot program in the chip is executed and the DSP is reset, the program starts to execute the program from FF80H of the internal ROM. At FF80H, there is a jump instruction to turn to the masked BOOT program in the ROM, so that the internal BOOT program starts to run. This boot program is first initialized. Initialization work includes disabling interrupts (INTM=1), mapping the internal dual access block/single access block to the program/data space (OVLY=0), and setting 7 wait states for both the program and data spaces.
There are 5 modes for TMS320VC5410 program boot:
(1) HPI mode, which is a host interface mode. The host interrupts the DSP by writing to the host control register (HPIC), and the DSP interrupts the host through the host interrupt signal

(2) Parallel I/O port BOOT mode (supports 8 bits and 16 bits).
(3) Serial port mode (standard/TDM/BSP) (supports 8 bits
and 16 bits). There are 8 serial port boot modes. The boot mode is determined by the two formats of word length 8 bits and 16 bits and the setting of CLKX/FSX pins. When using 8-bit sub-length, the following control bits need to be set:
· Receive reset signal RRST;
· Transmit mode bit TXM;
· Clock mode bit MCM (make CLKX driven by the on-chip clock source);
· Frame synchronization mode bit FSM (frame synchronization pulse signal must be applied externally to FSR pin);
· Format bit FO (select 8-bit data transmission mode). (4) External parallel mode (supports 8 bits and 16 bits). (5) WARM BOOT, that is, hot boot mode, can control the transmission entry address, and can also be used after the device is hot reset or the program code has been transferred to the on-chip or off-chip memory (such as DMA) by other means. In WARM boot mode, the SRC or ADDR field in the BRS word specifies the upper 6 bits of the entry address.
This article mainly discusses the 8-bit/16-bit parallel I/O port boot mode.
The I/O port boot mode provides a method for asynchronously transferring program code from the I/O port address space 0h to the internal or external program memory. Figure 1 is the program flow chart.
From the flowchart in Figure 1, we can see that by setting the content of the FFFFH address in the data area reasonably, making it an effective parallel boot, we can realize our parallel I/O BOOT mode.
2 Design the content of the FFFFH address to make it an effective parallel boot data

3 Set the content of 08000h to realize the boot function
We can get the data we need to fill in according to Figure 2.

According to Table 1, we can fill in the words that meet the requirements.

To get the information of the filled-in words, you need to generate a table. Before generating this table, you need to make a batch file. The batch file is as follows:
(1) First compile and generate the ".out" file; (
2) Open UltraEdit-32 batch editing software;
(3) Use the hex command to edit.
The hex command format is as follows:
myfile. out/* Input COFF file name. -e 0x0000/* Program start address. -a/* ASCII output format. -boot/* Boot all program units. -bootorg PARALLEL/* Create PARALLEL BOOT boot. -memwidth 16/* 16-bit EPROM. -o myfile. hex/* Output file name. Here is a small program to show the specific operation process (the program starts at 0x2000): hex500 test1. out-e 0x2000-boot-bootorgPARALLEL-memwidth 16-romwidth 16-o test1.hex In this way, a table can be generated, as shown in Table 2. The underlined ones in Table 2 represent the starting address of each Section, and the framed ones are the length of this Section (note that when we fill in this table, we should add 1 to the length of the Section, which is the experience gained after application), and the last four 0s of the last Section indicate the end. From the above, we can use the parallel BOOT mode.




→参考文献CH(开始)
2 Ren Lixiang, Ma Shufen, Li Fanghui (eds.) Principles and Applications of TMS320C5400 Series DSPs. Beijing: Electronic Industry Press, 2000, 7
3 Peng Qicong (ed.) TMS320C54X Practical Tutorial. Chengdu: University of Electronic Science and Technology Press, 2000, 1
Previous article:Research on H4001 non-contact IC card reading program
Next article:Design of photoelectric micro-loss blood glucose monitoring system based on MSP430
Recommended ReadingLatest update time:2024-11-16 16:54
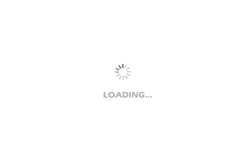
Professor at Beihang University, dedicated to promoting microcontrollers and embedded systems for over 20 years.
- Innolux's intelligent steer-by-wire solution makes cars smarter and safer
- 8051 MCU - Parity Check
- How to efficiently balance the sensitivity of tactile sensing interfaces
- What should I do if the servo motor shakes? What causes the servo motor to shake quickly?
- 【Brushless Motor】Analysis of three-phase BLDC motor and sharing of two popular development boards
- Midea Industrial Technology's subsidiaries Clou Electronics and Hekang New Energy jointly appeared at the Munich Battery Energy Storage Exhibition and Solar Energy Exhibition
- Guoxin Sichen | Application of ferroelectric memory PB85RS2MC in power battery management, with a capacity of 2M
- Analysis of common faults of frequency converter
- In a head-on competition with Qualcomm, what kind of cockpit products has Intel come up with?
- Dalian Rongke's all-vanadium liquid flow battery energy storage equipment industrialization project has entered the sprint stage before production
- Allegro MicroSystems Introduces Advanced Magnetic and Inductive Position Sensing Solutions at Electronica 2024
- Car key in the left hand, liveness detection radar in the right hand, UWB is imperative for cars!
- After a decade of rapid development, domestic CIS has entered the market
- Aegis Dagger Battery + Thor EM-i Super Hybrid, Geely New Energy has thrown out two "king bombs"
- A brief discussion on functional safety - fault, error, and failure
- In the smart car 2.0 cycle, these core industry chains are facing major opportunities!
- The United States and Japan are developing new batteries. CATL faces challenges? How should China's new energy battery industry respond?
- Murata launches high-precision 6-axis inertial sensor for automobiles
- Ford patents pre-charge alarm to help save costs and respond to emergencies
- New real-time microcontroller system from Texas Instruments enables smarter processing in automotive and industrial applications
- Pingtouge RVB2601 Review: Connecting to Alibaba Cloud IoT Platform
- MSP430F5529 IO port pin interrupt study notes
- Circuit-level electrostatic protection design techniques and ESD protection methods
- [ESK32-360 Review] +TFT screen display function and expansion (3)
- Can the 7805 and 1117-5 power supplies be used within ±0.05?
- CC3200 Kit OURS-SDK-WFB_Exploration 4——FreeRTOS Run
- The microcontroller outputs PWM wave to control the load supply voltage 0-12V adjustable
- 【Insights】If you don’t plant flowers in your heart, weeds will grow
- I would like to ask which manufacturers produce unipolar TMR tunneling effect switches. I only found MDT, and Magne does not have unipolar ones.
- Altium16.1 manufacturing output IPC-2581 and odb++ formats are not working