With the continuous development of new energy vehicles, large factories have gradually begun to use transport vehicles driven by power batteries. The batteries commonly used in electric vehicles are lead-acid batteries, lithium batteries, nickel-metal hydride batteries, etc. The battery is an object that integrates high energy, so its use and safety management are particularly important. At present, electric vehicles lack equipment that can reflect the battery status in real time, intuitively, and online. The early damage caused by untimely maintenance, poor storage, and excessive discharge of the battery has brought certain losses to the company. The battery management system can solve this problem. Therefore, it is of great value and significance to study a system that can monitor the working condition of the battery in real time.
The battery management system designed by the reference lacks data transmission function, which makes its application have certain limitations. The battery management system designed by the reference is based on DSP as the control core, which has a high cost and high power consumption of the system operation, and has great limitations.
In view of the above shortcomings, a design scheme based on the single-chip microcomputer CC430F5137 as the control core is adopted. The CC430F5137 integrates the CC1101 radio transceiver, which can realize the wireless transmission function of 100-200 m, and the CCA30F5137 has the low power consumption characteristics of the MSP430 series microcontroller. The above advantages make up for the defects of the current battery management system and meet the requirements of current applications.
1 Battery Management System Operation Principle
This system is installed in electric vehicles and can monitor the battery status in real time. When the battery car is charging, the system can transmit the charging data to the charging center through the wireless module and automatically manage the charging and discharging. In this way, the charging center can understand the charging status in real time, and the charging center does not need to connect other lines to the car, which reduces the trouble of building lines and improves work efficiency; when the car is using the battery normally, the system will monitor the battery power consumption in real time, notify the driver in time when the remaining power is insufficient, and send the alarm to the charging center through the wireless module to inform that charging is needed.
The block diagram of the battery management system is shown in Figure 1. This system uses CC430F5137 as the control core; the battery charge and discharge control circuit mainly manages the charge and discharge of the battery. The charge and discharge current of high-power batteries is large, and the charge and discharge control circuit is required to protect the battery from damage; the battery detection circuit mainly detects the battery charge and discharge voltage, charge and discharge current and battery temperature; the LCD display circuit is used to display battery voltage, temperature, power and other parameters to provide a reference for users; the CC1101 radio module is used to send the collected battery data to the charging center via radio so that the charging center can manage it in real time.
2 Hardware design of battery management system
The battery management system includes current detection module, voltage detection module, temperature detection module and data transmission module.
2.1 Design of current and voltage detection module
In this system, the microcontroller needs to detect the overall voltage of the battery pack and the voltage of a single battery. There are currently two detection methods: one is to use a Hall voltage sensor to convert the measured voltage, and then sample it through an A/D conversion element; the other is to use precision resistors to build a resistor divider circuit, and then use an A/D conversion element for sampling. The second method is more suitable for conditions with a relatively fixed voltage range. If there is a large voltage or a large voltage range, the first method is more suitable. This system uses the first detection method.
2.1.1 Selection of analog sampling chip
This system uses the AD7656 analog-to-digital conversion chip to collect analog signals. AD7656 is a highly integrated, 16-bit successive approximation ADC with 6 channels simultaneously sampled using an innovative semiconductor manufacturing process (iCMOS). Its throughput is as high as 250 ksps, and it can sample 6 channels simultaneously; it supports parallel, serial and daisy chain interface modes; it can be seamlessly connected to high-speed serial ports such as SPI and QSPI of the processor; it has a wide bandwidth input, and the signal-to-noise ratio (SNR) is 86.5 dB when the input frequency is 50 kHz; when the power supply voltage is 5 V and the sampling rate is 250 ksps, the power consumption is 140mW. As shown in Figure 2, AD7656 has two power input terminals, namely the analog voltage input terminal AVCC and the digital voltage input terminal DVCC. When AD7656 converts 6 channels of data at the same time, a standard input power supply is required to achieve high precision requirements, so the decoupling of AVCC is very important. A magnetic bead is added to the output end of the power supply in this system to provide a better power supply. In the grounding design of the circuit, the DGND and AGND of AD7656 need to be grounded separately to avoid mutual influence. In this system, the positive power supply voltage VDD is +12 V, the supply voltages of the logic power supply VDRIVE, the digital power supply DVCC, and the analog power supply AVCC are all +5 V, and the supply voltage of the negative power supply VSS is -12 V. The RANGE port is grounded, that is, the input range of ±10 V is selected; W/B grounding indicates 16-bit parallel output; AD7656 STBY is connected to VDRIVE to select normal mode; SER/PAR port is grounded to select parallel interface; WR/REFEN/DIS is connected to VDRIVE to select internal reference.
The hardware connection diagram of CC430F5137 and AD7656 is shown in Figure 2. The 16 I/O ports of CC430F5137's P0 port are used as parallel data ports and are connected to the parallel data ports DB0~DB15 of AD7656; the P1.0 port is connected to the BUSY of AD7656 to detect whether the conversion is completed; the P1.1 port is connected to the three ports CONVST A, CONVST B and CONVST C, as the 6-way A/D simultaneous sampling start control port of AD7656; the P1.2 port is connected to the read signal /RD of AD7656 as the read data control port; the P1.3 port is connected to the /CS end of AD7656 as the chip select control port; the P1.4 port is connected to the RESET end of AD7656 as the restart control port of AD7656. [page]
2.1.2 Design
of current detection module The current detection module uses a Hall current sensor with a measurement range of 0 to 100 A. The current signal is reduced by 1:1000 and converted into a voltage signal on the precision sampling resistor. As shown in Figure 3, the wire flowing through the current to be measured is inserted into the gap of the sensor. At this time, the current output at the M end is a signal reduced in proportion to the current to be measured. After the current signal flows through the sampling resistor, a voltage drop is formed at both ends of the resistor. Since one end of the resistor is grounded, the other end of the resistor is V. That is, the converted voltage signal. The current range of the current sensor output is 0 to 100 mA, so the size of the sampling resistor determines the output voltage range. According to the input voltage requirements of the AD7656 analog conversion chip and the conversion ratio of the current sensor, the resistance value of the sampling resistor R is selected as 100 Ω, and the voltage of the output signal is within 0 to 10 V, which meets the input voltage requirements of the A/D conversion chip.
2.1.3 Design of voltage detection module
The voltage detection module adopts the measurement method of Hall voltage sensor plus A/D converter. As shown in Figure 4, the voltage detection module adopts Hall voltage sensor. Its measurement range is 0-200 V, and the rated input current of the voltage sensor is 0-10 mA. Therefore, before connecting the battery voltage to the Hall voltage sensor, a current limiting resistor R1 needs to be connected in series before the voltage sensor is connected. According to the input voltage range, the resistance value of R1 is selected as 20 kΩ. The accuracy of the resistor must be high enough, because the accuracy of resistor R1 will directly affect the accuracy of the input voltage, and then affect the accuracy of the entire voltage measurement. As shown in Figure 4, the output terminal M of the voltage sensor outputs a current signal with a range of 0 to 25 mA, but the input signal of the A/D converter is required to be a voltage signal, so the current signal output by the voltage sensor needs to be converted into a voltage signal. A resistor R2 is connected in series between the output terminal M of the voltage sensor and the ground, so that the current output by the output terminal M acts on the resistor R2 to obtain a voltage signal. According to the requirements of the A/D converter for the input voltage signal range, the resistance value of R2 is selected to be 400Ω.
2.2 Design of temperature detection module
During the charging and discharging process of the battery, part of the internal energy will be released in the form of heat energy. If the temperature of a single battery is too high, it will affect the life of the battery and even cause the battery to explode. Batteries will show different physical properties at different temperatures. Measuring the temperature of the battery and using and maintaining the battery according to its inherent performance indicators is a very important link for extending the battery life and achieving the best use of the battery. Considering the low power consumption requirements and cost constraints of the equipment, Maxim's DS18B20 digital temperature sensor was selected in this system for temperature measurement. DS18B20 is a high-speed, high-precision temperature sensor. When installing the temperature sensor, it needs to be as close to the battery as possible. The power supply voltage of DS18B20 is 3 V; the measurement range is -55~+125℃; the measurement accuracy is 0.5℃. The temperature acquisition circuit diagram is shown in Figure 5. The power supply voltage of DS18B20 is 3 V. The P1.5 port of the microcontroller CC430F51 37 is connected to the DQ port of DS18B20 to control DS18B20.
[page]
2.3 Data transmission module design The data transmission module consists of the CC1101radio module integrated inside the CC430F5137 microcontroller . The CC430F5137 microcontroller is a combination of TI's MSP430F5xx series MCU and a low-power RF transceiver, which can achieve extremely low current consumption. In addition, it uses battery-powered wireless network applications and can work for more than 10 years without maintenance. The advanced functionality contained in the micro-package can also provide core power for innovative RF sensor networks to report data to a central collection point. The CC430F5137 is a 16-bit ultra-low power MCU with 16 KB flash memory, CC1101 radio and 2 KB RAM. The supply voltage range is 1.8 to 3.6V, the normal operating mode consumes 160μA/MHz, and the LPM_3 consumes 2.0μA.
The CC1101 radio transceiver is integrated in the CCA30F5137 microcontroller. In order to improve the stability of data transmission, the RF frequency of the radio is set to 915 MHz, the channel spacing is 100 kHz, the data transmission rate is 38.4 kbps, the maximum transmission power can reach -109 dBm, and the transmission distance can reach 200 m. In the case of a long distance, a high-power antenna can be connected externally to increase the transmission distance. The transmission power can be adjusted according to the transmission distance to minimize power consumption. The RF radio hardware circuit of CC430F5137 is shown in Figure 6. The power supply voltage of CC430F5137 is +3.3 V, and the external frequency is a quartz crystal oscillator of 26 MHz. Among them, RF_N and RF_P are the receiving and transmitting pins of the RF radio transceiver. The two pins are connected to an external antenna to increase the transmission distance.
3 Power battery management system software design
The software design of the power battery management system includes the design of the SoC power detection subroutine, the system program when the battery is in normal use, and the system program when the battery is charging. The following is a detailed introduction to these parts.
3.1 SoC power detection subroutine
In the battery management system, the commonly used SoC calculation methods include Coulomb calculation method, open circuit voltage method, impedance measurement method, comprehensive table lookup method, etc. Considering the low power consumption characteristics and cost of the system, this system adopts the comprehensive table lookup method. The remaining capacity SoC of the battery is closely related to the battery voltage, current, temperature and other parameters. A related table is set according to the inherent characteristics of the battery, and the remaining power value of the battery can be calculated according to the battery voltage, current, temperature and other parameters. The remaining power detection program flow is shown in Figure 7. After the system is initialized, it starts to detect the battery voltage, current, and temperature parameters, and then calculates the remaining power of the battery according to the listed related tables, and displays the calculated data on the display screen. At the same time, this data is transmitted to the charging center through the wireless module. If the remaining power is insufficient, the system will trigger the alarm device to inform the personnel that the power is insufficient.
3.2 System Programming for Normal Battery Use
When the battery is in normal use, CC430F5137 will detect various parameters of the battery in real time, including voltage, current, temperature, etc. The remaining battery power can be calculated according to the table lookup method. If the battery power is insufficient, the system will prompt the user to inform the user of the insufficient power and send the insufficient power information to the charging center through the RF radio module integrated in CCA30F5137. If the output current of the battery is large and exceeds the inherent indicators of the battery, the system will also issue an alarm to inform the user of special conditions and promptly check and replace the battery.
The system program flow when the battery is in normal use is shown in Figure 8. First, the system will detect the relevant parameters of the battery, calculate the power, and display the relevant information of the battery. If an alarm occurs, the system will promptly notify the user and the charging center.
3.3 System program design when the battery is charging
Because the voltage and current of the battery input need to change continuously at different stages of battery charging, the system will detect the input voltage, current, temperature and other parameters of the battery in real time during the charging process, and then calculate the battery power according to the table lookup method, and send the power information to the charging center through RF radio. In this way, the charging center continuously controls the charging voltage and charging current according to the real-time parameters of the battery to better charge.
The system program flow is shown in Figure 9.
After the system is initialized, it will continuously detect the relevant parameters of the battery, and then send the relevant information of the battery to the charging center, and at the same time determine whether it is fully charged. If it is fully charged, it will notify the personnel that the battery is fully charged.
Conclusion
This paper designs a power battery management system based on the CC430F5137 microcontroller. This system can monitor the use of the battery in real time and feedback the real-time data of the battery to the user in a timely manner. The system runs stably and reliably, and has good application prospects.
Previous article:A design scheme for the interface between fixed-point digital signal processor and single-chip microcomputer
Next article:Design of low-cost and high-precision A/D and D/A conversion based on single-chip microcomputer
Recommended ReadingLatest update time:2024-11-16 17:29
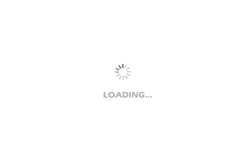
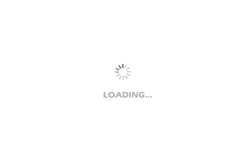
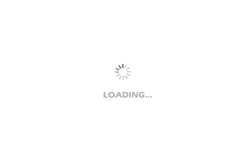
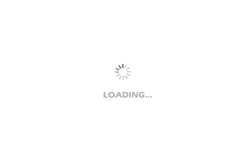
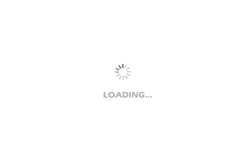
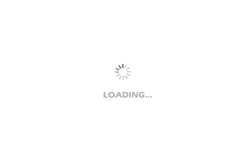
- Popular Resources
- Popular amplifiers
-
Research on collaborative energy-saving optimization control method for connected hybrid vehicle fleet
-
Research on image recognition for SoC deep learning algorithms_Yang Donghong
-
Implementing a perception system for autonomous vehicles using a detection and segmentation network on a SoC FPGA
-
Multi-port and shared memory architecture for high-performance ADAS SoCs
Professor at Beihang University, dedicated to promoting microcontrollers and embedded systems for over 20 years.
- Innolux's intelligent steer-by-wire solution makes cars smarter and safer
- 8051 MCU - Parity Check
- How to efficiently balance the sensitivity of tactile sensing interfaces
- What should I do if the servo motor shakes? What causes the servo motor to shake quickly?
- 【Brushless Motor】Analysis of three-phase BLDC motor and sharing of two popular development boards
- Midea Industrial Technology's subsidiaries Clou Electronics and Hekang New Energy jointly appeared at the Munich Battery Energy Storage Exhibition and Solar Energy Exhibition
- Guoxin Sichen | Application of ferroelectric memory PB85RS2MC in power battery management, with a capacity of 2M
- Analysis of common faults of frequency converter
- In a head-on competition with Qualcomm, what kind of cockpit products has Intel come up with?
- Dalian Rongke's all-vanadium liquid flow battery energy storage equipment industrialization project has entered the sprint stage before production
- Allegro MicroSystems Introduces Advanced Magnetic and Inductive Position Sensing Solutions at Electronica 2024
- Car key in the left hand, liveness detection radar in the right hand, UWB is imperative for cars!
- After a decade of rapid development, domestic CIS has entered the market
- Aegis Dagger Battery + Thor EM-i Super Hybrid, Geely New Energy has thrown out two "king bombs"
- A brief discussion on functional safety - fault, error, and failure
- In the smart car 2.0 cycle, these core industry chains are facing major opportunities!
- The United States and Japan are developing new batteries. CATL faces challenges? How should China's new energy battery industry respond?
- Murata launches high-precision 6-axis inertial sensor for automobiles
- Ford patents pre-charge alarm to help save costs and respond to emergencies
- New real-time microcontroller system from Texas Instruments enables smarter processing in automotive and industrial applications
- Share the disassembly of IPP-5002
- [Raspberry Pi Pico Review] --- Getting Started
- The 2019 STM32 National Tour Seminar is about to start. Register now to win three gifts
- Problems of overcurrent and overvoltage protection in voltage doubler rectifier circuit
- When installing 32-bit dependent libraries in 64-bit Ubuntu, "libc6:i386 (!= 2.19-0ubuntu6.6) but 2.19...
- Popular science information on the entire process of chip design and production
- [Rivet RVB2601 Creative Application Development] 1. Routine Experience - Music Player
- EEWORLD University Hall----Linux Kernel Analysis and Application Xi'an University of Posts and Telecommunications (Chen Lijun)
- DIY ImxRT1010 board, sharing hardware debugging experience
- Useful information sharing | Come and get the various "grounds" in the switching power supply