In the study of bionic propulsion mechanism, accurate measurement of fish tail fin flapping parameters is of great significance for the study of fish bionic propulsion mechanism and engineering application; however, most researchers currently use the observation method of analyzing images taken by high-speed cameras to obtain parameters. This method is limited by the environment and equipment, and the results are less accurate. This design is a micro-inertial measurement device for biological motion based on MEMS devices. The device is used to achieve accurate measurement of the SPC-III robot fish tail fin flapping parameters, laying the foundation for the first domestic live fish tail fin flapping parameter measurement experiment using MEMS devices, and providing support for the design theory of robot fish bionic propulsion.
1 Design requirements and system structure
According to the biological characteristics of living fish and the characteristics of the experiment itself, the micro-inertial measurement unit should meet the following design requirements: small size, light weight, low power consumption, high acquisition frequency and acquisition accuracy, and good waterproof sealing performance. In order to achieve these requirements, the hardware of the micro-inertial measurement unit consists of two parts: ① microprocessor unit; ② micro-inertial sensor unit. The microprocessor unit mainly includes a microprocessor, an A/D conversion chip and Flash. As the core unit, the microprocessor connects to the A/D conversion chip through the SPI1 port to complete data acquisition, connects to the Flash through the SPIO port to complete data storage, and communicates with the host computer through the serial port. The micro-inertial sensor unit is composed of a MEMS accelerometer and a MEMS gyroscope to complete the task of collecting the original information of acceleration and angular velocity. After the collected original information is processed by A/D conversion, it is written into the Flash chip for storage, or sent directly to the host computer through the serial port for processing. The schematic diagram of the system principle is shown in Figure 1.
2 Microprocessor Unit
2.1 LPC2129 Processor
This device requires the microprocessor to have certain processing capabilities and low power consumption and small size, so Philips' LPC2129 is selected. LPC2129 is based on a 16/32-bit ARM7TDMI-SCPU that supports real-time simulation and tracing, and has 16 KB on-chip SRAM and 256KB embedded high-speed on-chip Flash memory. LPC2129 has a smaller LQFP64 package, extremely low power consumption, multiple 32-bit timers, 4-channel 10-bit ADC, 9 external interrupts, and up to 46 GPIOs.
[page]
In the software design of LPC2129, the commonly used uC/OS-II or uClinux operating system on ARM is not used, but a foreground and background timing interrupt structure is used. This foreground and background timing interrupt structure is more suitable for control systems with high real-time requirements, which can ensure that the control loop delay is within a designed range, and the priority relationship between each module is very clear, which is more convenient to use.
2.2 A/D conversion acquisition chip ADS1256
The A/D conversion chip uses the 24-bit serial analog/digital converter ADS1256 from TI of the United States. It can provide up to 23 bits of noise-free accuracy and a data rate of up to 30 ksps. ADS1256 uses a four-wire SPI communication method and is connected to the SPI1 interface of LPC2129, which allows flexible and convenient communication.
ADS1256 adopts a multi-channel cyclic acquisition mode. After the data preparation signal DRDY prompts that data can be extracted, the current acquisition channel is first changed to the next acquisition channel, a new acquisition conversion is started, and then the data in the A/D conversion register is immediately extracted (the data at this time is actually the data converted in the previous round). This method can realize the acquisition and conversion of new data while extracting data, which is a highly efficient working method.
2.3 Flash chip AT45DB041B
Flash1 uses Atmel's programmable serial access chip AT45DB041B. The main storage unit is divided into 2048 pages, each page is 264 bytes, and has two 264-byte static random access memories as data buffers.
AT45DB04lB is connected to the SPI0 interface of LPC2129. The collected data is first written into the buffer 2 of Flash, and then the data in the buffer is written into the main memory page of Flash for preservation, pending offline data analysis and processing.
3 Micro Inertial Sensor Unit
The MEMS sensor unit of the micro inertial measurement device is composed of a micromechanical gyroscope and a micro accelerometer, which can accurately measure one axial angular velocity information and one axial acceleration information of the carrier.
3.1 ADXRS300 Single Angular Rate Gyroscope
ADXRS300 is an angular velocity sensor based on MEMS technology produced by Analog Devices, Inc. of the United States. ADXRS300 is powered by a +5V power supply, and the range of measuring yaw angular velocity is ±300rad/s, the sensitivity is 5mV/(rad·s-1), and the zero output voltage is 2.5V. The range, bandwidth and zero output voltage of the angular velocity can be set by external resistors and capacitors. It adopts BGA-32 packaging technology, the outer size is only 7mm×7mm×3mm, and the weight is only 0.5g. [page]
Assume that the measured angular velocity is αv, in units of (°)/s; the output voltage is Uo, in units of mV; the sensitivity K is 5mV/(°)·s-1, and the zero position output voltage is 2.5V, then there is the relationship:
3.2 ADXLl50 single-axis accelerometer
ADXL150 is a single-axis micro-accelerometer based on MEMS technology produced by Analog Devices, Inc. The main performance characteristics of ADXL150 are: zero-position output bias voltage is Us/2, measurement range is ±50g, sensitivity coefficient is 38mV/g, nonlinearity is 0.2%, zero acceleration drift is 0.2g; it can work with 4~6V power supply; power consumption is very low, and the static current is only 1.8~3.5mA.
Assume that the measured acceleration is av, in g; the output voltage is Uo, in mV; the sensitivity is K, in mV/g; the power supply voltage is Vs, in mV, then there is the relationship:
4 Measurement principles of speed, angle and displacement
After the angular velocity and acceleration information are integrated and calculated, the angle, velocity, displacement and other information can be obtained. Therefore, the device can measure various motion state information of the carrier based on the angular velocity and acceleration information of the carrier.
Assume that the sampling period is T, v(k) is the velocity at time kT, x(k) is the displacement at time kT, a(k) is the acceleration at time kT, and a(k) is the continuous true value of the acceleration. Then, the following integral formula for solving the velocity is obtained:
The area enclosed in the interval [kT, (k+1)T]. Knowing that the sampling values of acceleration at kT and (k+1)T are a(k) and a(k+1), the shape enclosed by acceleration a(t) in the time interval [kT, (k+1)T] can be approximated as a rectangle or trapezoid. The trapezoid is more accurate, as shown in Figure 2.
[page]
Therefore, the above formula can be approximated as:
It is known that the A/D sampling period is t, and at a certain time T1, the angular velocity of the carrier is w1, the linear acceleration is a1, and the linear velocity is v1. After a sampling period t, at the time T1+t, the angular velocity of the carrier is w2, the linear acceleration is a2, and the linear velocity is v2. In this sampling period t, the angle turned by the carrier is α, and the displacement of the carrier is s, then:
The angle, speed, displacement and other information of the carrier can be obtained through integral calculation.
5 Applications
5.1 System Integration
The micro inertial measurement device consists of a processor unit module and a sensor unit module. The two modules are connected through an inter-board bus and staggered to maximize the use of space and achieve the miniaturized size requirements. The device is powered by a 7.2V lithium battery. The final packaged device weighs only 25g.
The host computer data processing software was developed using NI's LabWindows/CVI software. The data processing software reads the speed information collected by the micro-inertial measurement device, generates speed/angle and displacement curves, and obtains the swing angle and amplitude values of the carrier.
5.2 Experiment on measuring the flapping parameters of SPC-III robot fish tail fin
The micro-inertial measurement device was used to measure the caudal fin flapping parameters of the SPC-III robot fish developed by the ITM Laboratory of the Robotics Institute of Beijing University of Aeronautics and Astronautics. The micro-inertial measurement device was installed at the caudal peduncle of the caudal fin of the robot fish, and the acquisition frequency of the measurement device was set to 1kHz. When the SPC-III robot fish flapped stably at a frequency of 1Hz, the collected data was processed by the host computer data processing software to obtain the caudal fin flapping parameters of the SPC-III robot fish: flapping frequency 1Hz, swing angle amplitude 41.70°, amplitude 97.368mm, maximum angular velocity 124.264(°)/s. The angular velocity curves are shown in Figures 3 and 4.
As shown in Table 1, the measured data is not much different from the theoretical design values. Possible causes of the error: the gyro and accelerometer have errors, including zero error and dynamic error; the robot fish tail fin flapping mechanism is not very precise and has deviations.
According to the estimation method of the caudal fin thrust of fish, it is estimated that the average thrust generated by the caudal fin of the SPC-III robotic fish when flapping at a frequency of 1 Hz is 10 N, as listed in Table 2.
The two-joint parallel mechanism tail fin thruster used in the SPC-III robotic fish can generate a thrust of tens of Newtons. The actual thrust is basically consistent with the estimated thrust, which preliminarily verifies the tail fin thrust estimation method based on the ideal thruster theory and momentum theorem. In the absence of water tunnel model tests and CFD hydrodynamic calculation simulations, this method can quickly and easily obtain an estimated value of the tail fin thrust, or inversely solve the motion parameters of the tail fin. This thrust estimation method has been successfully used in the design and experimental work of the SPC series robotic fish in the ITM Laboratory of Beihang University.
Conclusion
A micro-inertial measurement device based on MEMS devices can be used to accurately measure the flapping parameters of the SPC-III robot fish tail fin. The micro-inertial measurement device is small in size, light in weight, and low in power consumption. It can obtain the carrier's acceleration, angular velocity, speed, displacement, angle and other motion information, and can be applied to biological motion measurement, sports measurement, human health monitoring and other fields.
Previous article:Design of VGA Interface for ARM Embedded Platform
Next article:Design of LAN IP Phone Based on ARM
Recommended ReadingLatest update time:2024-11-16 17:46
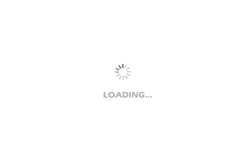
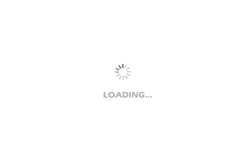
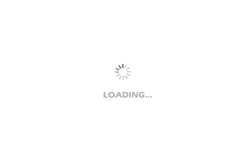
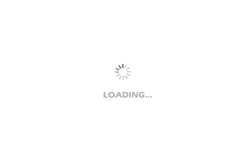
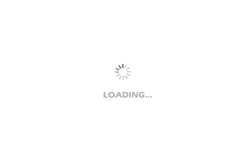
Professor at Beihang University, dedicated to promoting microcontrollers and embedded systems for over 20 years.
- Innolux's intelligent steer-by-wire solution makes cars smarter and safer
- 8051 MCU - Parity Check
- How to efficiently balance the sensitivity of tactile sensing interfaces
- What should I do if the servo motor shakes? What causes the servo motor to shake quickly?
- 【Brushless Motor】Analysis of three-phase BLDC motor and sharing of two popular development boards
- Midea Industrial Technology's subsidiaries Clou Electronics and Hekang New Energy jointly appeared at the Munich Battery Energy Storage Exhibition and Solar Energy Exhibition
- Guoxin Sichen | Application of ferroelectric memory PB85RS2MC in power battery management, with a capacity of 2M
- Analysis of common faults of frequency converter
- In a head-on competition with Qualcomm, what kind of cockpit products has Intel come up with?
- Dalian Rongke's all-vanadium liquid flow battery energy storage equipment industrialization project has entered the sprint stage before production
- Allegro MicroSystems Introduces Advanced Magnetic and Inductive Position Sensing Solutions at Electronica 2024
- Car key in the left hand, liveness detection radar in the right hand, UWB is imperative for cars!
- After a decade of rapid development, domestic CIS has entered the market
- Aegis Dagger Battery + Thor EM-i Super Hybrid, Geely New Energy has thrown out two "king bombs"
- A brief discussion on functional safety - fault, error, and failure
- In the smart car 2.0 cycle, these core industry chains are facing major opportunities!
- The United States and Japan are developing new batteries. CATL faces challenges? How should China's new energy battery industry respond?
- Murata launches high-precision 6-axis inertial sensor for automobiles
- Ford patents pre-charge alarm to help save costs and respond to emergencies
- New real-time microcontroller system from Texas Instruments enables smarter processing in automotive and industrial applications
- Use ST's new APP to instantly find the most suitable sensor
- [XMC4800 Relax EtherCAT Kit Review] + Getting started with DAVE, quickly build your own webserver
- [GD32L233C-START Review] + Guess which light will be on next time
- How to convert brd file to ad pcb file
- 【AT32WB415 Review】Serial communication test (including Bluetooth test)
- TI Voltage Reference (VREF) Application Design Tips and Tricks
- What happens if the input voltage of the window comparator is equal to the upper and lower limits?
- Banknote number recognition system based on ARM.pdf
- My knowledge of computers
- Sampling rate of MCU ADC