0 Introduction
With the development of modern industry, the requirements for air environment in the production process are getting higher and higher. In order to meet the needs of human comfort and process flow, the temperature, humidity, cleanliness and flow rate of the air should be adjusted in a certain space during production. In chemical fiber plants, the system that provides air conditioning for the process flow is called process air conditioning. At present, most domestic textile plants adopt air heat and humidity treatment methods with spray surface cooling. Air treatment equipment mostly adopts large combined air conditioners, and the air conditioning system adopts a dual-fan air conditioning system with a fixed air volume throughout the year. This method is due to the high heat generation of process equipment in the workshop, and the process flow has relatively strict temperature and humidity accuracy requirements for air conditioning air supply parameters. The air conditioning system required in the production line should be able to provide a very large supply and return air volume. This will cause the fan to consume a lot of energy (about 25% of the air conditioning refrigeration energy consumption). Therefore, reducing the energy consumption of the fan is of great significance to the energy saving work of the entire chemical fiber plant.
1 Structure and working principle of chemical fiber combined air conditioning
1.1 Structure of chemical fiber combined air conditioning
The structure of chemical fiber combined air conditioning is shown in Figure 1. The system consists of air valve actuator, temperature and humidity sensor, differential pressure switch, differential pressure transmitter, three-way cold water valve and actuator, steam two-way valve, frequency converter and PLC.
The basic task of the air conditioning system is to keep the air in the workshop at a certain temperature and humidity, discharge the excess heat and moisture from the workshop, and replenish it in time when the heat and moisture are insufficient. In order to complete this task, so that the regulated temperature and humidity can approach the set temperature and humidity values according to the curves of isothermal humidification, adiabatic humidification, cooling and humidification, this paper gives the design scheme of the air conditioning control system composed of air system, water system and steam system.
1.2 Working principle of chemical fiber combined air conditioner
The fresh air window is mainly used to introduce fresh air from the outside. In order to save energy, the return air window is sometimes used to introduce part of the workshop return air. The fresh air window and the return air window are generally equipped with adjustable dampers to control the air intake and the fresh/return air ratio. The fresh/return air is usually mixed by the blower and sent to the spray chamber. The spray chamber has forward spray, reverse spray and multiple rows of nozzles. Deep well water and circulating water are sprayed out through nozzles to produce fine water drops, and then the air is sprayed back through the circulating water to complete the adiabatic humidification process, and the cooling and humidification process can be completed through the forward spray of deep well water. After the air is treated with water, the regulating valve can be controlled, and the air can be isothermally humidified with steam, or the air can be isohumidified with a heater. Using the spray chamber to treat the air can make the relative humidity of the air relatively stable, which is conducive to the regulation and control of the relative humidity of the workshop air, thereby meeting the high requirements of the textile process for the relative humidity of the air. At the same time, using water to treat the air can also play a role in cleaning the air, which is conducive to reducing the dust concentration of the workshop air. In addition, the use of heaters can achieve rapid heating in winter.
2 System hardware design
The hardware design of this system mainly consists of two parts: the control system and the motor system. The hardware structure block diagram of the control system is shown in Figure 2.
2.1 Control scheme
This design adopts DDC direct digital control, which can collect analog quantities such as temperature, humidity, pressure and their parameters at various points on the site in real time, and can also modify various set values and various parameters. At the same time, it can realize automatic opening and closing and automatic adjustment of related valves and frequency converters to achieve the purpose of controlling constant temperature, constant humidity and constant pressure, and has manual and automatic switching functions. In
addition, even if the automatic control loop fails, the system can switch to manual mode to continue to adjust the parameters normally.
2.2 Execution device
The execution device is the actuator that completes all actions. It can complete all actions of chemical fiber air conditioners, including the start and stop of fans, the start and stop of water pumps, and the control of air valves. In the control process of chemical fiber combined air conditioners, the controller can send signals to the fan and water pump. When the air valve receives the signal, it can control the air chamber. In the control process, the chemical fiber air conditioner will automatically or manually control the temperature and humidity of the workshop according to the instructions issued by the controller. The execution control can be carried out according to the controller or the touch screen. This system is equipped with a touch screen human-machine interface.
2.3 Sensor
(1) Temperature sensor
This design uses the JCJ100F temperature transmitter. JCJ100F temperature transmitter contains high-precision linear amplifier circuit and uses high-precision components, so it has the advantages of high sensitivity, good stability, high accuracy and long service life.
In the temperature measurement and control system, thermocouples or thermistors can be used to collect temperature, and then the preamplifier circuit converts the detected tiny signal into a signal that can be converted by ADC. At the same time, A/D conversion is performed after cold end temperature compensation, so that the analog temperature signal can be digitized.
After the digital signal is handed over to the CPU for processing, the CPU can control the return air valve, exhaust valve, fresh air valve, supply air valve and inlet and return water valve according to the data of the temperature sensor, thereby completing the function of automatically adjusting the air temperature.
(2) Humidity sensor
IH3605 humidity sensor is a capacitive integrated humidity sensor, which can make the capacitive humidity sensor and conditioning circuit together on a ceramic substrate. Water vapor in the air can pass through the protective polyester layer and then through the porous platinum layer into the dielectric layer to change the dielectric constant of the dielectric, thereby changing the capacitance. In this way, the capacitance change can be converted into a DC voltage output through the capacitance/frequency and frequency/voltage conversion circuits.
Since the output voltage of IH3605 is high and the linearity is good, it can be directly connected to the A/D converter without amplification and nonlinear correction to complete the conversion from analog to digital. In addition, it can also be directly used as the signal source of the electronic trigger switch to start the compressor.
2.4 Controller
This chemical fiber combined air conditioning control system uses Siemens programmable controller PLCS7-200 as the controller. The S7-200 series programmable controller can meet a variety of automation control needs. Since this design requires an expansion module, and CPU222 can only have two expansion interfaces, models above CPU222 can have 7 expansion modules. Since there are too many input points for CPU226, the CPU model selected after comprehensive consideration is CPU224. At the same time, EM222 is selected as the expansion output module. The analog input detection module on site uses EM231-RTD, and Pt100 is selected as the temperature sensor.
The external function of the programmable controller is mainly to realize the detection and control of industrial equipment or production processes through the external wiring of various interface modules. Therefore, through various input/output interface modules, the programmable controller can detect the required process information and transmit the processing results to the external process, thereby driving various actuators to realize the control of the industrial production process. Since the signal levels in actual production are diverse, and the levels required by external actuators are also diverse, but the CPU of the programmable controller can only process standard levels, the conversion of this signal level should be realized through the I/O interface. In order to adapt to various process signals, there should be corresponding multiple I/O interface modules in the design.
2.5 Design of control circuit
The entire circuit of this system consists of three parts, namely the return air system, the ambient air system and the side blowing air system. According to the current temperature and humidity, the above three parts have different operating modes. Due to limited space, the circuit part of the return air system is mainly introduced below.
The control circuit of the return air system in this system is shown in Figure 3. In the figure, when the circuit breaker QF1 is closed, the inverter is powered, the normally open contacts of the inverter are closed, and the return fan is powered; when the circuit breaker QF04 is closed, the lighting lamp is on; when the short circuit breaker QF01 is closed, the power indicator light is on, the fan runs, and the indicator light of the fan running is on.
3 System software design
The software flow chart of this system is shown in Figure 4. As can be seen from the figure, when the system is running, the program should be initialized first, then the set parameter values (wind pressure, fresh air, return air, environment, side blowing, mixed air, temperature and humidity) should be input, and then the workshop should be sampled. After the sampling is completed, the sampled value is compared with the set parameter value, and then the new value obtained by the system after the comparison is used to automatically execute the corresponding function, thereby completing a job. After that, the system will start to operate in a cycle according to the sampling. If necessary, it can also be controlled by manual control and manual intervention control.
4 Conclusion
This paper gives a design method for controlling the temperature and humidity of the chemical fiber plant workshop. The method has two control modes: manual and automatic. And its electrical principle and control circuit wiring design are neat and beautiful, the human-computer dialogue interface is friendly, the functions are complete, and the operation is simple. In addition, after actual use, the software of this system runs normally and without defects. It can control the indoor temperature of the workshop at 25℃±2℃ and the relative humidity between 50% and 70%, thus fully meeting the needs of human comfort and process flow, and also improving the output and quality of products.
Reference address:Design of control system for chemical fiber combined air conditioner
With the development of modern industry, the requirements for air environment in the production process are getting higher and higher. In order to meet the needs of human comfort and process flow, the temperature, humidity, cleanliness and flow rate of the air should be adjusted in a certain space during production. In chemical fiber plants, the system that provides air conditioning for the process flow is called process air conditioning. At present, most domestic textile plants adopt air heat and humidity treatment methods with spray surface cooling. Air treatment equipment mostly adopts large combined air conditioners, and the air conditioning system adopts a dual-fan air conditioning system with a fixed air volume throughout the year. This method is due to the high heat generation of process equipment in the workshop, and the process flow has relatively strict temperature and humidity accuracy requirements for air conditioning air supply parameters. The air conditioning system required in the production line should be able to provide a very large supply and return air volume. This will cause the fan to consume a lot of energy (about 25% of the air conditioning refrigeration energy consumption). Therefore, reducing the energy consumption of the fan is of great significance to the energy saving work of the entire chemical fiber plant.
1 Structure and working principle of chemical fiber combined air conditioning
1.1 Structure of chemical fiber combined air conditioning
The structure of chemical fiber combined air conditioning is shown in Figure 1. The system consists of air valve actuator, temperature and humidity sensor, differential pressure switch, differential pressure transmitter, three-way cold water valve and actuator, steam two-way valve, frequency converter and PLC.
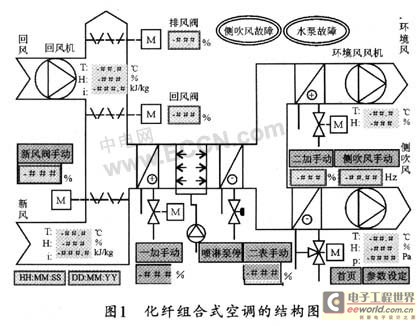
The basic task of the air conditioning system is to keep the air in the workshop at a certain temperature and humidity, discharge the excess heat and moisture from the workshop, and replenish it in time when the heat and moisture are insufficient. In order to complete this task, so that the regulated temperature and humidity can approach the set temperature and humidity values according to the curves of isothermal humidification, adiabatic humidification, cooling and humidification, this paper gives the design scheme of the air conditioning control system composed of air system, water system and steam system.
1.2 Working principle of chemical fiber combined air conditioner
The fresh air window is mainly used to introduce fresh air from the outside. In order to save energy, the return air window is sometimes used to introduce part of the workshop return air. The fresh air window and the return air window are generally equipped with adjustable dampers to control the air intake and the fresh/return air ratio. The fresh/return air is usually mixed by the blower and sent to the spray chamber. The spray chamber has forward spray, reverse spray and multiple rows of nozzles. Deep well water and circulating water are sprayed out through nozzles to produce fine water drops, and then the air is sprayed back through the circulating water to complete the adiabatic humidification process, and the cooling and humidification process can be completed through the forward spray of deep well water. After the air is treated with water, the regulating valve can be controlled, and the air can be isothermally humidified with steam, or the air can be isohumidified with a heater. Using the spray chamber to treat the air can make the relative humidity of the air relatively stable, which is conducive to the regulation and control of the relative humidity of the workshop air, thereby meeting the high requirements of the textile process for the relative humidity of the air. At the same time, using water to treat the air can also play a role in cleaning the air, which is conducive to reducing the dust concentration of the workshop air. In addition, the use of heaters can achieve rapid heating in winter.
2 System hardware design
The hardware design of this system mainly consists of two parts: the control system and the motor system. The hardware structure block diagram of the control system is shown in Figure 2.
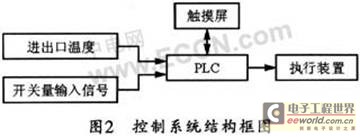
2.1 Control scheme
This design adopts DDC direct digital control, which can collect analog quantities such as temperature, humidity, pressure and their parameters at various points on the site in real time, and can also modify various set values and various parameters. At the same time, it can realize automatic opening and closing and automatic adjustment of related valves and frequency converters to achieve the purpose of controlling constant temperature, constant humidity and constant pressure, and has manual and automatic switching functions. In
addition, even if the automatic control loop fails, the system can switch to manual mode to continue to adjust the parameters normally.
2.2 Execution device
The execution device is the actuator that completes all actions. It can complete all actions of chemical fiber air conditioners, including the start and stop of fans, the start and stop of water pumps, and the control of air valves. In the control process of chemical fiber combined air conditioners, the controller can send signals to the fan and water pump. When the air valve receives the signal, it can control the air chamber. In the control process, the chemical fiber air conditioner will automatically or manually control the temperature and humidity of the workshop according to the instructions issued by the controller. The execution control can be carried out according to the controller or the touch screen. This system is equipped with a touch screen human-machine interface.
2.3 Sensor
(1) Temperature sensor
This design uses the JCJ100F temperature transmitter. JCJ100F temperature transmitter contains high-precision linear amplifier circuit and uses high-precision components, so it has the advantages of high sensitivity, good stability, high accuracy and long service life.
In the temperature measurement and control system, thermocouples or thermistors can be used to collect temperature, and then the preamplifier circuit converts the detected tiny signal into a signal that can be converted by ADC. At the same time, A/D conversion is performed after cold end temperature compensation, so that the analog temperature signal can be digitized.
After the digital signal is handed over to the CPU for processing, the CPU can control the return air valve, exhaust valve, fresh air valve, supply air valve and inlet and return water valve according to the data of the temperature sensor, thereby completing the function of automatically adjusting the air temperature.
(2) Humidity sensor
IH3605 humidity sensor is a capacitive integrated humidity sensor, which can make the capacitive humidity sensor and conditioning circuit together on a ceramic substrate. Water vapor in the air can pass through the protective polyester layer and then through the porous platinum layer into the dielectric layer to change the dielectric constant of the dielectric, thereby changing the capacitance. In this way, the capacitance change can be converted into a DC voltage output through the capacitance/frequency and frequency/voltage conversion circuits.
Since the output voltage of IH3605 is high and the linearity is good, it can be directly connected to the A/D converter without amplification and nonlinear correction to complete the conversion from analog to digital. In addition, it can also be directly used as the signal source of the electronic trigger switch to start the compressor.
2.4 Controller
This chemical fiber combined air conditioning control system uses Siemens programmable controller PLCS7-200 as the controller. The S7-200 series programmable controller can meet a variety of automation control needs. Since this design requires an expansion module, and CPU222 can only have two expansion interfaces, models above CPU222 can have 7 expansion modules. Since there are too many input points for CPU226, the CPU model selected after comprehensive consideration is CPU224. At the same time, EM222 is selected as the expansion output module. The analog input detection module on site uses EM231-RTD, and Pt100 is selected as the temperature sensor.
The external function of the programmable controller is mainly to realize the detection and control of industrial equipment or production processes through the external wiring of various interface modules. Therefore, through various input/output interface modules, the programmable controller can detect the required process information and transmit the processing results to the external process, thereby driving various actuators to realize the control of the industrial production process. Since the signal levels in actual production are diverse, and the levels required by external actuators are also diverse, but the CPU of the programmable controller can only process standard levels, the conversion of this signal level should be realized through the I/O interface. In order to adapt to various process signals, there should be corresponding multiple I/O interface modules in the design.
2.5 Design of control circuit
The entire circuit of this system consists of three parts, namely the return air system, the ambient air system and the side blowing air system. According to the current temperature and humidity, the above three parts have different operating modes. Due to limited space, the circuit part of the return air system is mainly introduced below.
The control circuit of the return air system in this system is shown in Figure 3. In the figure, when the circuit breaker QF1 is closed, the inverter is powered, the normally open contacts of the inverter are closed, and the return fan is powered; when the circuit breaker QF04 is closed, the lighting lamp is on; when the short circuit breaker QF01 is closed, the power indicator light is on, the fan runs, and the indicator light of the fan running is on.
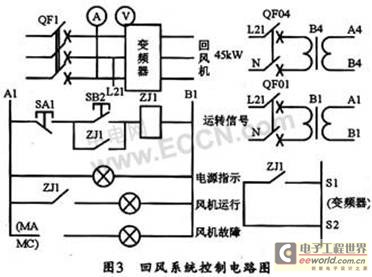
3 System software design
The software flow chart of this system is shown in Figure 4. As can be seen from the figure, when the system is running, the program should be initialized first, then the set parameter values (wind pressure, fresh air, return air, environment, side blowing, mixed air, temperature and humidity) should be input, and then the workshop should be sampled. After the sampling is completed, the sampled value is compared with the set parameter value, and then the new value obtained by the system after the comparison is used to automatically execute the corresponding function, thereby completing a job. After that, the system will start to operate in a cycle according to the sampling. If necessary, it can also be controlled by manual control and manual intervention control.
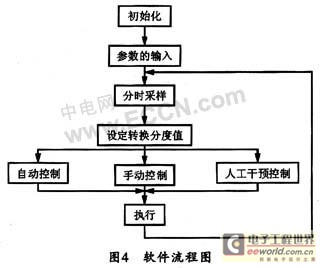
4 Conclusion
This paper gives a design method for controlling the temperature and humidity of the chemical fiber plant workshop. The method has two control modes: manual and automatic. And its electrical principle and control circuit wiring design are neat and beautiful, the human-computer dialogue interface is friendly, the functions are complete, and the operation is simple. In addition, after actual use, the software of this system runs normally and without defects. It can control the indoor temperature of the workshop at 25℃±2℃ and the relative humidity between 50% and 70%, thus fully meeting the needs of human comfort and process flow, and also improving the output and quality of products.
Previous article:Design of a non-chip mini speaker based on AU7845 single chip
Next article:Research on Power Control Algorithm of CDMA System Based on Matlab
- Popular Resources
- Popular amplifiers
Latest Industrial Control Articles
- Molex leverages SAP solutions to drive smart supply chain collaboration
- Pickering Launches New Future-Proof PXIe Single-Slot Controller for High-Performance Test and Measurement Applications
- CGD and Qorvo to jointly revolutionize motor control solutions
- Advanced gameplay, Harting takes your PCB board connection to a new level!
- Nidec Intelligent Motion is the first to launch an electric clutch ECU for two-wheeled vehicles
- Bosch and Tsinghua University renew cooperation agreement on artificial intelligence research to jointly promote the development of artificial intelligence in the industrial field
- GigaDevice unveils new MCU products, deeply unlocking industrial application scenarios with diversified products and solutions
- Advantech: Investing in Edge AI Innovation to Drive an Intelligent Future
- CGD and QORVO will revolutionize motor control solutions
MoreSelected Circuit Diagrams
MorePopular Articles
- Innolux's intelligent steer-by-wire solution makes cars smarter and safer
- 8051 MCU - Parity Check
- How to efficiently balance the sensitivity of tactile sensing interfaces
- What should I do if the servo motor shakes? What causes the servo motor to shake quickly?
- 【Brushless Motor】Analysis of three-phase BLDC motor and sharing of two popular development boards
- Midea Industrial Technology's subsidiaries Clou Electronics and Hekang New Energy jointly appeared at the Munich Battery Energy Storage Exhibition and Solar Energy Exhibition
- Guoxin Sichen | Application of ferroelectric memory PB85RS2MC in power battery management, with a capacity of 2M
- Analysis of common faults of frequency converter
- In a head-on competition with Qualcomm, what kind of cockpit products has Intel come up with?
- Dalian Rongke's all-vanadium liquid flow battery energy storage equipment industrialization project has entered the sprint stage before production
MoreDaily News
- Allegro MicroSystems Introduces Advanced Magnetic and Inductive Position Sensing Solutions at Electronica 2024
- Car key in the left hand, liveness detection radar in the right hand, UWB is imperative for cars!
- After a decade of rapid development, domestic CIS has entered the market
- Aegis Dagger Battery + Thor EM-i Super Hybrid, Geely New Energy has thrown out two "king bombs"
- A brief discussion on functional safety - fault, error, and failure
- In the smart car 2.0 cycle, these core industry chains are facing major opportunities!
- The United States and Japan are developing new batteries. CATL faces challenges? How should China's new energy battery industry respond?
- Murata launches high-precision 6-axis inertial sensor for automobiles
- Ford patents pre-charge alarm to help save costs and respond to emergencies
- New real-time microcontroller system from Texas Instruments enables smarter processing in automotive and industrial applications
Guess you like
- Qorvo 100 MHz Envelope Tracking Solution for 5G
- 【Beetle ESP32-C3】3. Adjust LED brightness with knob (potentiometer) (Arduino)
- China's first batch of autonomous driving unmanned commercial licenses issued! Do you dare to sit in an unmanned car? ?
- GDB debugging and DSP
- The IO pin of MSP430 is set as input, but it receives the output signal of the Hall sensor, and the chip-side signal does not switch.
- [Serial] [Starlight Lightning STM32F407 Development Board] Chapter 10 Serial Communication Experiment
- Where do errors in vector network analyzers come from?
- The relationship between serial port communication and interruption
- How to use a wiring harness tester to measure small resistance? Here's a method
- Those who don't know about RF MEMS, please take a look. This is what the technology is like.