Introduction
The winding machine developed in this paper is horizontal, and the core mold is placed horizontally. During winding, the core mold rotates at a constant speed around its main axis, and the trolley motor drags the trolley to reciprocate along the axis of the core mold, driving the winding nozzle to complete the winding and placement of the fiber on the core mold at a certain winding angle to meet the technical requirements of the product.
Modular open CNC system has become the development direction of CNC technology today. The winding control system in this paper uses an embedded multi-task motion controller to realize the synchronous motion control of the main axis and the trolley and the winding logic control.
The development of an open winding machine numerical control system based on PC and TRIO motion controller is discussed. The control system structure of the FRP pipe winding machine is composed of a main shaft that drives the FRP pipe core mold to rotate, a trolley that arranges glass fiber on the core mold, and a resin and curing agent supply system. When the horizontal winding machine is winding, the core mold rotates at a constant speed around its main shaft, and the trolley motor drags the trolley to reciprocate longitudinally on the workbench, driving the winding nozzle to complete the winding and laying of the fiber layer on the core mold at a certain winding angle. The trolley motor should be accelerated and decelerated continuously according to the process requirements during reciprocating operation, and the load of the trolley and the main shaft changes with the change of the winding glue amount, which is easy to cause the relative position of the wire guide head and the core mold to change, resulting in linear abnormality and poor yarn overlap. The winding machine system is a nonlinear time-varying position synchronous follow-up control system with a large inertia change. Therefore, the position tracking control method based on electronic gears is adopted to ensure good yarn overlap. The electronic gear mode is actually a multi-axis linkage mode, and its motion effect is similar to the meshing motion of two mechanical gears. When the current axis works in the electronic gear mode, the electronic gear ratio needs to be set. The current axis will follow the active axis according to this speed ratio. The active axis can be in any motion mode. The displacement increment of the current axis is equal to the displacement increment of the active axis associated with it multiplied by the electronic gear ratio.
The structure of the winding machine control system
is shown in Figure 1. The host computer uses Taiwan Advantech 1PC610 chassis and PCA-6179 motherboard. It communicates with the MC206 motion controller of the British Wo Motion Technology Company through RS-232 serial port to form a powerful open motion control system. The industrial PC is responsible for the human-machine interface management, motion status display, remote monitoring and process file storage, and the motion controller is responsible for real-time motion control and logic control. The structure supports software upgrades and function expansions, and has upper and lower levels of openness. The
winding machine spindle motor is a 7.5 kW three-phase AC asynchronous motor driven by a Japanese Yaskawa ICI MR-G7A47P5 inverter. For the speed of the spindle motor, this system adopts a closed-loop control method with greater load resistance. The analog output of the motion controller axis 3 interface is used as the input signal of the inverter speed control. The analog voltage output value is set in the open-loop control state of the motion controller to realize the inverter speed control. A CWZ1X rotary encoder installed on the input shaft of the gearbox completes the detection of the spindle angle and speed. The inverter adopts the PG vector control mode. The PG-X2 speed card uses the encoder sampling signal as the inverter input to realize the speed closed-loop control, and as the speed and position signal input to the encoder interface 4 of the controller, realizing the function of completing the speed closed-loop control and the spindle angle position sampling by one encoder. The trolley adopts the Yaskawa SGMGH-44ACA61 servo motor to complete the precise positioning. It reciprocates along the axial direction of the glass fiber reinforced plastic tube and tracks the spindle movement with a certain response speed and accuracy according to the winding law. The axis 0 interface works in the servo mode to complete the closed-loop control of the trolley servo motor. The spindle encoder feedback is connected to the MC206 axis 4 interface as the input axis of the reference encoder, providing an encoder input for the synchronous movement of the trolley.
Software design
of winding machine control system The upper computer program of the winding machine control system is developed based on the Windows 2000 platform using Microsoft's VC++6.0 to complete the process file setting and management, remote monitoring and machine tool operation status display and other functions. The industrial computer and MC206 complete the process parameter download and machine tool status parameter upload and display through the serial port based on the MODBUS protocol.
The communication adopts a master-slave query mechanism. The system sets the industrial computer as the master station and MC206 as the slave station. Only when the master station issues a query can the slave station respond, and the slave station cannot actively send data. When working, the worker selects the model of the pipe to be wound and downloads the process file, and then enters the winding processing state. At this time, all motion and logic control are completed by the slave station, and the slave station only responds to the query of the master station and uploads the status data. Even if the industrial computer fails or crashes for some reason, it will not affect the winding processing of the current pipeline. Thereby improving the stability of the system and the real-time control.
The motion control program is compiled in Trio BASIC multi-tasking language. The motion control program can be downloaded to MC206 by running the MotionPerfect software on the PC and can be run offline. Trio BASIC language has three different types of storage variables: named variables, VR () variables and TABLE area variables. Named variables are local variables, which are only valid in the task in which they are defined.
Variables are global variables that can be shared by multiple tasks and can be used for communication between tasks; TABLE area is usually used to store CAM/command curves. This program is used to store process files for winding pipe models. The running user program is called a thread or task.
For complex multi-task programs, threads should be assigned priorities. The default servo cycle of the controller is 1ms, which is divided into three time slices internally. Each time slice is 1/3 ms. They are used to process servo functions, communications and common "housekeep" tasks internally. The remaining time in each time slice is used to run user programs. MC206 can run up to 7 user threads. Each thread is numbered from 1 to 7. The highest-numbered threads (threads 7 and 6) are assigned fixed time slices. They are called "fast tasks" and are mainly used for tasks with the following requirements: tasks that must be processed in each servo cycle; tasks with a large amount of calculations and processing; tasks whose program execution speed cannot be changed after the task is started. 5g-threads are called "slow tasks". They have a common priority, and the program execution speed will decrease as the number of tasks increases. Users can use instructions to start tasks to run at the specified priority.
In the host computer software Motion Performance, open a "Terminal" window to set a "C The control software of the winding machine has four tasks, among which task 7 is used for the motor motion control of the winding machine and the logic control of the machine tool, task 6 is used to manage the I/O signals and spindle speed control related to the machine tool and winding, task 2 completes the serial communication function, and task 1 realizes the glue feeding control. The task functions and execution time allocation of the control program are shown in Figure 2. Among them, tasks 7 and 6 have the highest priority, and each servo cycle (1 Ins) is allocated a time slice. Tasks 1, 2 and L have the same priority, and are allocated a time slice in turn in each servo cycle. The task functions and execution time allocation of the winding program are shown in Figure 2.

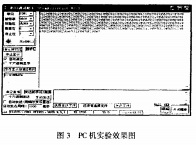
Conclusion
The CNC system of the winding machine combines the advantages of industrial PC and embedded motion controller, and makes full use of the electronic gear function of TRIO motion controller. The system can automatically wind according to the process requirements, and has the functions of system operation status display, remote communication, fault diagnosis and alarm, and reverse gap compensation. The yarn width of the winding machine can be adjusted arbitrarily between 80 and 220 mm, which can meet the winding requirements of pipes with different diameters. The maximum yarn output speed can reach mm/min, and the core mold rotation angle resolution is 0.018. The trolley trajectory control error is less than 0 mm, the whole machine has fast response speed, stable performance and simple operation. The system has been applied to Daqing Zhutian Composite Materials Co., Ltd. Practice has proved that the system plays a very important role in improving the technical level, automation level and pipeline quality of FRP pipe winding molding process, shortening the pipeline development cycle, reducing the labor intensity of staff, improving production efficiency and reducing production costs.
Previous article:Analysis of remote control technology of oscilloscope using computer labview
Next article:Application of Motor Soft Starter in Mining Engineering
- Popular Resources
- Popular amplifiers
- Molex leverages SAP solutions to drive smart supply chain collaboration
- Pickering Launches New Future-Proof PXIe Single-Slot Controller for High-Performance Test and Measurement Applications
- CGD and Qorvo to jointly revolutionize motor control solutions
- Advanced gameplay, Harting takes your PCB board connection to a new level!
- Nidec Intelligent Motion is the first to launch an electric clutch ECU for two-wheeled vehicles
- Bosch and Tsinghua University renew cooperation agreement on artificial intelligence research to jointly promote the development of artificial intelligence in the industrial field
- GigaDevice unveils new MCU products, deeply unlocking industrial application scenarios with diversified products and solutions
- Advantech: Investing in Edge AI Innovation to Drive an Intelligent Future
- CGD and QORVO will revolutionize motor control solutions
- Innolux's intelligent steer-by-wire solution makes cars smarter and safer
- 8051 MCU - Parity Check
- How to efficiently balance the sensitivity of tactile sensing interfaces
- What should I do if the servo motor shakes? What causes the servo motor to shake quickly?
- 【Brushless Motor】Analysis of three-phase BLDC motor and sharing of two popular development boards
- Midea Industrial Technology's subsidiaries Clou Electronics and Hekang New Energy jointly appeared at the Munich Battery Energy Storage Exhibition and Solar Energy Exhibition
- Guoxin Sichen | Application of ferroelectric memory PB85RS2MC in power battery management, with a capacity of 2M
- Analysis of common faults of frequency converter
- In a head-on competition with Qualcomm, what kind of cockpit products has Intel come up with?
- Dalian Rongke's all-vanadium liquid flow battery energy storage equipment industrialization project has entered the sprint stage before production
- Allegro MicroSystems Introduces Advanced Magnetic and Inductive Position Sensing Solutions at Electronica 2024
- Car key in the left hand, liveness detection radar in the right hand, UWB is imperative for cars!
- After a decade of rapid development, domestic CIS has entered the market
- Aegis Dagger Battery + Thor EM-i Super Hybrid, Geely New Energy has thrown out two "king bombs"
- A brief discussion on functional safety - fault, error, and failure
- In the smart car 2.0 cycle, these core industry chains are facing major opportunities!
- The United States and Japan are developing new batteries. CATL faces challenges? How should China's new energy battery industry respond?
- Murata launches high-precision 6-axis inertial sensor for automobiles
- Ford patents pre-charge alarm to help save costs and respond to emergencies
- New real-time microcontroller system from Texas Instruments enables smarter processing in automotive and industrial applications
- [RVB2601 Creative Application Development] Temperature and Humidity Monitoring System Based on Alibaba Cloud
- MPLAB X IDE compile error!!! Newbie asks for help from experts/(ㄒoㄒ)/~~
- Future Prospects of UWB Technology
- On the problem of value jump in PMT application
- Use of access/_access function in C language
- Some useful information: RVB2601 development board program download automatic operation and OLED screen protection
- To the netizens who entered the Pingtouge RVB2601 competition (reference materials, technical support, experience sharing, work submission and selection criteria)
- Summary: RCSN experience W806 Lianshengde 9.9 yuan development board
- Hardware Design: Circuit Design of DSP TMS320C5509A
- VaST's latest modeling tool enables comprehensive software development before tapeout