Fiber optic connectors are the most widely used optical passive devices in optical fiber communication networks, and their core components are fiber optic pins. An important process in the manufacturing process of fiber optic connectors is to use a fiber optic connector grinder to grind the end face of the ceramic pin. In order to make the end face of the fiber optic pin contact and grind with the grinding wheel as required. It involves repeated positioning motion control in the three axes of X, Y, and A on the grinder operating table. The servo control system is an important part of the fiber optic connector grinder.
The servo motor can convert the input electrical signal into angular displacement or angular velocity output. It has the characteristics of stable operation, no self-rotation and fast response, and is used as an actuator in the servo control system.
ED200 servo amplifier is an intelligent servo motor controller that can provide full digital control of speed, position and torque. The use of PLC can improve the stability of the servo control system and enhance the anti-interference ability of the system: the use of touch screen can provide a clear human-machine operation interface.
The grinding machine servo control system designed in this paper consists of four parts: servo motor, ED200 servo amplifier, PLC and touch screen. Combining their advantages greatly improves the grinding quality and yield rate of optical fiber connectors.
1. Composition structure and working principle of servo system
The servo system is an automatic control system used to control a certain state of the controlled object so that it can automatically, continuously and accurately reproduce the changing law of the input signal. Since the core diameter of the fiber optic connector pin is very thin, in order to grind a more ideal end face according to the chamfering requirements, the repeat positioning error of the three axes of the operating table X, Y, and A must be controlled within a certain range. The ED200 servo amplifier adopts high-response vector control and has high-precision current detection capability. It can achieve high-precision, high-speed and stable feeding, which can well meet the control requirements of the system. The fiber optic connector grinder servo control system is a closed-loop control system. Figure 1 is the block diagram of its closed-loop servo system. The system compares the output displacement with the setting, and automatically adjusts the position loop parameters, speed loop parameters, current loop parameters and excitation parameters to make the target position consistent with the actual position, thereby achieving the purpose of precise positioning.
2 Servo system design
2.1 System Hardware Design
The hardware used in this design is Kinco's S23 two-phase servo motor, ED200 servo amplifier, Mitsubishi's FX2N series PLC and GOTl000 touch screen.
The hardware structure of the fiber optic connector servo control system is shown in Figure 2. The grinding process involves three kinds of motion: horizontal, vertical and rotation, which are controlled by servo motors and servo amplifiers of the three axes X, Y and A. The connection and control methods of the three axes are similar. The figure shows the connection between the PLC and the servo amplifier of one axis.
ED200 servo amplifier is an intelligent all-digital servo driver. It integrates drive, control, bus, I/O and other functions. It can store 256 programs. Each program can store a motion curve, including acceleration, deceleration, maximum speed, target position and other important motion curve parameters. Through 8 I/O ports, up to 128 motion curves can be directly called. Using the communication function provided by ED200, the external controller PLC can call the 256 programs stored in ED200 and directly modify the internal system parameters of the driver through the data input window of the touch screen human-machine interface.
2.2 System software design
The software design of the grinding machine servo system includes the assignment of ED200 internal objects (target position, speed, acceleration, deceleration, origin search method, working mode, etc.) and PLC programming control.
ECO2WIN is a special programming software for ED200 servo amplifier. It uses the method of sequencer programming to assign values to the objects inside the amplifier. Since the grinding process involves positioning many times, the working mode is the position control mode (absolute/relative position mode). The objects to be defined in this mode are shown in Table 1.
Each program of the ED200 servo drive has a corresponding program segment number, and its list contains up to 8 objects with read-write (RW) attributes. After calling a program, all instructions in the program segment will be executed in order from top to bottom. This is the idea of sequential programming.
Figure 3 is the parameter setting window of the Y-axis servo amplifier controlling the servo motor to drive the operating table to enter the feeding point. The program segment number is 11, the working mode selects the absolute position movement mode in the position mode (the equipment status word 60400010 is set to 0X003F), and the maximum speed, acceleration, deceleration and target position values are set to 30,000, 160,000, 16,000 and 40,000 respectively.
The control events that trigger the program segment provided by ED200 servo include edge signal trigger of input port, expiration of timer time set by internal programming, true comparison result of two values, target position arrival, etc. Some events can be defined repeatedly, so a program segment can be executed once or multiple times. At the same time, another program segment can be called in a program segment.
In the digital input window of EC02WlN software, the program segment corresponding to the edge signal of ED200 digital input port DIN1~DIN8 can be set to realize the function of calling the internal program segment from the input port. In the design, the signal of ED200 digital input port is provided by PLC, so the servo motor can be indirectly controlled through PIC.
A complete single-cycle process of grinding the fiber optic connector pin body includes operations such as feeding, grinding, discharging, and servo positioning. Figure 4 is the software flow chart of the system. Among them, the positioning part is mainly controlled by the internal sequence programming of the ED200 servo amplifier, and the program segment is triggered by the PLC signal. The entire grinding machine system is controlled by PLC programming, and the PLC adopts the ladder diagram programming method.
ED200 supports two-wire (half-duplex) and four-wire (full-duplex) RS485 communication. The PLC communication expansion module FX2N-485-BD communicates with ED200 via RS485 to exchange data between them. The PLC program is written in ladder diagram, and the address and number of bytes of the transmitted data are set using RS serial communication instructions. After connecting to the touch screen, the target position value of the internal program segment of ED200 can be modified through the data input window of the touch screen.
3 Software Debugging
ECO2WIN has an oscilloscope function, which is used to monitor operating parameters (such as speed, position, and current) in a dynamic curve. The oscilloscope plays a very important role in judging the motor's motion state and regulation performance. It can visually observe the motor's overshoot, overload, and speed stability. Figure 5 is the monitoring curve of the A-axis motor speed and position. As can be seen from Figure 5, the maximum speed of the A-axis motor is 10,000 inc/s, the maximum displacement is 4,000 inc, the working mode is -1, and channel 1 is set to "Actual position
4 Conclusion
The end face processing of the optical fiber connector pin body belongs to high-precision grinding, which places extremely high demands on the positioning accuracy of the grinding machine servo control system. This design applies the ED200 servo driver, PLC and touch screen to the servo control system of the optical fiber connector grinder, greatly improving the grinding efficiency of the optical fiber connector. The design uses the ED200 servo amplifier, which is simple to program and convenient for PLC control. In addition, the RS485 communication between the PLC and ED200 is established using the communication expansion module, and the system control parameters can be modified through the touch screen, which is flexible and convenient. The actual results show that after the system is applied to the optical fiber connector grinder, the performance of the whole system is more stable, the positioning accuracy is high, and it is easy to operate, which improves the production efficiency.
Previous article:PLC communication based on PROFIBUS-DP
Next article:Application of OMRON PLC in the Control System of Chemical Wastewater Incineration Plant
Recommended ReadingLatest update time:2024-11-16 16:42
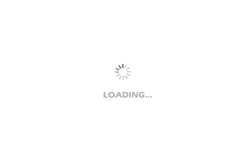
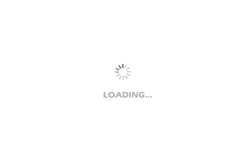
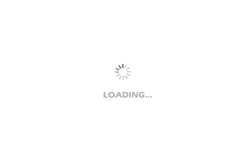
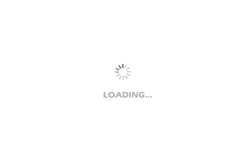
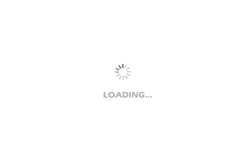
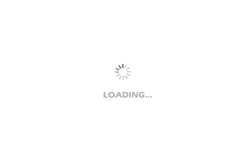
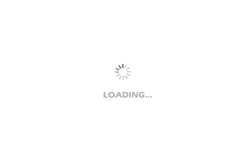
- Popular Resources
- Popular amplifiers
- Molex leverages SAP solutions to drive smart supply chain collaboration
- Pickering Launches New Future-Proof PXIe Single-Slot Controller for High-Performance Test and Measurement Applications
- CGD and Qorvo to jointly revolutionize motor control solutions
- Advanced gameplay, Harting takes your PCB board connection to a new level!
- Nidec Intelligent Motion is the first to launch an electric clutch ECU for two-wheeled vehicles
- Bosch and Tsinghua University renew cooperation agreement on artificial intelligence research to jointly promote the development of artificial intelligence in the industrial field
- GigaDevice unveils new MCU products, deeply unlocking industrial application scenarios with diversified products and solutions
- Advantech: Investing in Edge AI Innovation to Drive an Intelligent Future
- CGD and QORVO will revolutionize motor control solutions
- Innolux's intelligent steer-by-wire solution makes cars smarter and safer
- 8051 MCU - Parity Check
- How to efficiently balance the sensitivity of tactile sensing interfaces
- What should I do if the servo motor shakes? What causes the servo motor to shake quickly?
- 【Brushless Motor】Analysis of three-phase BLDC motor and sharing of two popular development boards
- Midea Industrial Technology's subsidiaries Clou Electronics and Hekang New Energy jointly appeared at the Munich Battery Energy Storage Exhibition and Solar Energy Exhibition
- Guoxin Sichen | Application of ferroelectric memory PB85RS2MC in power battery management, with a capacity of 2M
- Analysis of common faults of frequency converter
- In a head-on competition with Qualcomm, what kind of cockpit products has Intel come up with?
- Dalian Rongke's all-vanadium liquid flow battery energy storage equipment industrialization project has entered the sprint stage before production
- Allegro MicroSystems Introduces Advanced Magnetic and Inductive Position Sensing Solutions at Electronica 2024
- Car key in the left hand, liveness detection radar in the right hand, UWB is imperative for cars!
- After a decade of rapid development, domestic CIS has entered the market
- Aegis Dagger Battery + Thor EM-i Super Hybrid, Geely New Energy has thrown out two "king bombs"
- A brief discussion on functional safety - fault, error, and failure
- In the smart car 2.0 cycle, these core industry chains are facing major opportunities!
- The United States and Japan are developing new batteries. CATL faces challenges? How should China's new energy battery industry respond?
- Murata launches high-precision 6-axis inertial sensor for automobiles
- Ford patents pre-charge alarm to help save costs and respond to emergencies
- New real-time microcontroller system from Texas Instruments enables smarter processing in automotive and industrial applications
- protues arm2124 simulation snake program
- BlueNRG-1 chip
- Bluetooth 5 New Features and Applications
- GD32F130 will immediately enter the serial port interrupt after the serial port idle interrupt is turned on
- LIS2MDL array PCB board for magnetic nail navigation AGV car
- Filter Design——FilterSolutions
- Android driver learning 1-driver development process (Android.mk)
- MSP430 clock problem
- 【Repost】Master these five methods to make your MCU easily low power
- Asking for advice: Question about TMS320C5509A low power mode