MiR Autonomous Mobile Robots Releases White Paper on "Automation of Internal Transportation in the Automotive Industry" to Enable a New Ecosystem of Cross-Border Car Manufacturing
March 24, 2022, Shanghai – Mobile Industrial Robots (MiR), a global leader in the mobile robot market, today released the white paper "Automation of Internal Transportation in the Automotive Industry" (link: shorturl.at/rsQT9), empowering the new cross-border car manufacturing ecosystem with intelligent logistics.
From the delivery of the AITO M5 smart electric car jointly built by Huawei and Seres Automotive, to Sony's announcement of a joint venture with Honda to establish a new company to develop pure electric vehicles, the first quarter of 2022 has witnessed the entry of many new car-making forces. The "2022 China Automobile Market Trend Analysis Report" recently released by the China Association of Automobile Manufacturers also shows that China's total automobile sales in 2022 are expected to reach 27.5 million, of which new energy vehicles will reach 5 million, a year-on-year increase of 42%. As established automakers and upstarts have entered the arena, new energy vehicles are blooming everywhere in China, and a new car-making ecosystem is accelerating.
Behind the cross-border car manufacturing trend is a series of favorable policies. New energy vehicles are a major strategic focus of the "14th Five-Year Plan". The country has successively adopted various special measures such as the "New Energy Vehicle Industry Development Plan (2021-2035)" to stipulate specific paths, encourage cross-border collaboration among enterprises in the fields of new energy vehicles, energy, transportation, information and communications, and strive to make pure electric vehicles the mainstream of new sales vehicles by 2035.
Faced with vast market potential and fierce competition, traditional automakers and new car manufacturers are hoping to build moats around core aspects such as battery technology upgrades, chip research and development, and charging infrastructure. However, to gain a competitive advantage in a rapidly changing market, a full-link intelligent upgrade from head to toe is needed.
Zhang Yu, Sales Director of MiR China, said: "Automobile manufacturing is a systematic project with a particularly long chain. It is not only the core skills such as chips that are the bottleneck. In order to make the manufacturing process keep up with the strong demand, it is also a top priority to improve the level of intelligence of the entire automotive chain, which involves not only R&D and production and manufacturing, but also warehousing and logistics. Among them, the optimization of internal logistics of car manufacturing plants is an indispensable part of the factory's intelligent upgrade. However, although robots are ubiquitous in the automotive parts industry, autonomous mobile robots are still a relatively new thing in the industry, indicating that the industry still has a lot of room for optimization in internal transportation automation."
Internal transportation in car factories faces multiple pain points
First, the massive demand has put tremendous pressure on the production, warehousing and logistics systems. The manufacturing of an average car involves about 10,000 independent parts that cannot be disassembled, and cars with more complex structures and functions may have more than 20,000 parts. After all the parts enter the factory, they need to be efficiently loaded, sorted, monitored, transported and stored, which poses a great challenge to any factory.
Secondly, from the perspective of talent development, during the vehicle manufacturing and assembly process, traditional internal logistics and transportation mainly rely on manpower. This is not only inefficient and difficult to meet delivery needs in a timely manner, but also long-term repetitive labor also prevents employees from focusing their precious time on higher-value work.
What's more, the manufacturing environment of most car factories is a mixture of people and vehicles. Many companies use manual forklifts to transport materials within the factory, but the weight of a forklift is three times that of a car. Once an accident occurs, it is very likely to cause serious harm to the staff.
To meet the above challenges, many companies hope to use robots to assist manual work. However, traditional AGV robots require laying wires or magnetic strips as "tracks", which limit them to fixed routes. Expanding/changing the working area is expensive and time-consuming. This not only fails to meet the needs of flexible production, but also brings high deployment costs, which makes many companies hesitate.
AMR robots help automate internal transportation in car factories
Unlike AGV robots, autonomous mobile robots (AMRs) are flexible in deployment, safe and reliable, have autonomous navigation, and are easy to use. They do not require laying tracks or making any physical changes to the factory environment, and are easy to expand and change work areas. By allowing AMRs to automatically unpack, disassemble, move, and store materials as needed, and undertake high-risk and repetitive tasks, the risk of personal injury can be greatly reduced while improving vehicle manufacturing efficiency, and employees can devote more time to higher value-added work. Specifically, AMR robots can bring the following benefits.
Intelligence: MiR continuously optimizes the intelligence of AMR through "visual technology" and "motion control technology". The robot can autonomously plan and adjust routes, avoid obstacles, stop at designated locations for autonomous charging, automatically call elevators, open and close doors, and transport materials across floors. The highly intelligent autonomous navigation function enables it to flexibly adapt to the complex factory environment of the car workshop. In addition, MiR's independently developed MiRFleet scheduling system can achieve the mutual coordination of multiple robots, carry out 7x24 hours of multi-site delivery, and solve irregular and non-fixed-point delivery tasks on demand.
Safety: MiR AMR can operate smoothly in a noisy and crowded dynamic environment, automatically avoid obstacles, and safely and stably shuttle between warehouses and manufacturing areas. All MiR AMRs are equipped with dual laser scanners with a 360-degree field of view, which can always sense the surrounding environment in advance while moving forward and re-plan the route at any time. In addition, MiR AMR's sensor vision is not affected by light and dust, has high scanning accuracy, and its overall safety has passed high-level certification.
Open and flexible: As an open composite robot, MiR AMR uses the MiRGo platform with more than dozens of ready-to-use top modules to quickly meet the segmented needs of various specific scenarios in car factories. In addition, if the autonomous navigation capability of the AMR chassis replaces the walking function of human legs and feet, then the collaborative robot arm replaces the function of human arms. The combination of the two greatly expands the application scenarios of robots.
Cost-effectiveness: In addition to considering the initial cost of purchasing automation technology, companies are increasingly considering return on investment from the perspective of total cost of ownership, which means taking into account factors such as cost savings from improved safety and man-hours saved due to flexible solutions. MiR AMR has a short deployment time and does not require changes to the physical environment of the production line, so the deployment efficiency is very high and downtime is avoided, which brings excellent cost-effectiveness to the company.
The automotive industry’s embrace of AMRs is beginning to bear fruit
Currently, MiR AMR has been adopted by many global leading automobile companies and automotive parts suppliers in the field of automotive parts, such as Ford, Visteon, and Faurecia, and is widely used in the entire process of parts/raw materials transportation, warehousing logistics, and waste disposal.
In Spain, for example, Ford's Valencia plant produces 2,000 vehicles a day, with three MiR AMRs transporting industrial materials of various sizes and weights between the body and stamping shops. This is the first time Ford has used collaborative autonomous mobile robots in its European plants. Tests have shown that each robot can free up an average of 40 hours of work per day for Ford, allowing workers to engage in other more complex tasks.
In Slovakia, Visteon's factory in Namestovo needs to produce 10,000 driving consoles every day and provide a specific amount of materials to the production line at a specific time, which places extremely high demands on the accuracy and flexibility of the internal transportation system, which the original AGV robots cannot meet. Therefore, Visteon deployed four MiR 200 robots to supply PCB circuit boards to the SMT production line, collect waste materials, and transport finished plastic components on demand around the clock every working day. The robot's operating interface is very user-friendly, and employees can operate it without programming knowledge to expand its functions, so that it can be quickly deployed to various new tasks. The flexible and easy-to-use MiR AMR enabled Visteon to recover its investment costs in less than a year.
In Germany, workers at Faurecia's plant in Stadthagen used to spend 8-10 hours a day transporting products from the welding workshop to the paint shop and then to the assembly workshop, which was very tedious and time-consuming. Faurecia then deployed a fleet of MiR 500 and MiR 200 hook robots to transport frame components between different sites, and integrated MiR AMR with the company's own ERP system, enabling the robots to automatically receive orders. This has enabled Faurecia to fully automate the internal transportation of frames.
Previous article:RTI Appoints Y-Mobility CEO David Fidalgo to Advisory Board
Next article:Create stable and efficient automatic testing equipment from multiple dimensions
Recommended ReadingLatest update time:2024-11-16 21:23
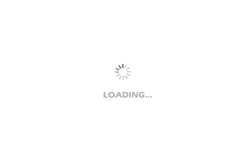
- Popular Resources
- Popular amplifiers
- Molex leverages SAP solutions to drive smart supply chain collaboration
- Pickering Launches New Future-Proof PXIe Single-Slot Controller for High-Performance Test and Measurement Applications
- CGD and Qorvo to jointly revolutionize motor control solutions
- Advanced gameplay, Harting takes your PCB board connection to a new level!
- Nidec Intelligent Motion is the first to launch an electric clutch ECU for two-wheeled vehicles
- Bosch and Tsinghua University renew cooperation agreement on artificial intelligence research to jointly promote the development of artificial intelligence in the industrial field
- GigaDevice unveils new MCU products, deeply unlocking industrial application scenarios with diversified products and solutions
- Advantech: Investing in Edge AI Innovation to Drive an Intelligent Future
- CGD and QORVO will revolutionize motor control solutions
- Innolux's intelligent steer-by-wire solution makes cars smarter and safer
- 8051 MCU - Parity Check
- How to efficiently balance the sensitivity of tactile sensing interfaces
- What should I do if the servo motor shakes? What causes the servo motor to shake quickly?
- 【Brushless Motor】Analysis of three-phase BLDC motor and sharing of two popular development boards
- Midea Industrial Technology's subsidiaries Clou Electronics and Hekang New Energy jointly appeared at the Munich Battery Energy Storage Exhibition and Solar Energy Exhibition
- Guoxin Sichen | Application of ferroelectric memory PB85RS2MC in power battery management, with a capacity of 2M
- Analysis of common faults of frequency converter
- In a head-on competition with Qualcomm, what kind of cockpit products has Intel come up with?
- Dalian Rongke's all-vanadium liquid flow battery energy storage equipment industrialization project has entered the sprint stage before production
- Allegro MicroSystems Introduces Advanced Magnetic and Inductive Position Sensing Solutions at Electronica 2024
- Car key in the left hand, liveness detection radar in the right hand, UWB is imperative for cars!
- After a decade of rapid development, domestic CIS has entered the market
- Aegis Dagger Battery + Thor EM-i Super Hybrid, Geely New Energy has thrown out two "king bombs"
- A brief discussion on functional safety - fault, error, and failure
- In the smart car 2.0 cycle, these core industry chains are facing major opportunities!
- The United States and Japan are developing new batteries. CATL faces challenges? How should China's new energy battery industry respond?
- Murata launches high-precision 6-axis inertial sensor for automobiles
- Ford patents pre-charge alarm to help save costs and respond to emergencies
- New real-time microcontroller system from Texas Instruments enables smarter processing in automotive and industrial applications
- [Project source code] Audio acquisition + FFT spectrum analysis + VGA display spectrum value based on FPGA
- EPLAN
- Download to get gifts | TE outdoor monitoring, an important guarantee and trend choice for creating a safe and stable society!
- How to process the signal of BLDC feedback speed measuring motor
- Seeking agent chip GD32F405
- "Play Board" + STM32F407 core board voice-controlled colored lights
- There may be a cure for the bald self! Tencent AI analyzes the cause of male baldness for the first time
- [TI recommended course] #Boost and buck-boost DCDC converters help wireless charging design#
- Arduino online simulation website wokwi
- [NXP Rapid IoT Review] Classic Snake purely hand-typed