Starting from practical applications, this paper analyzes and discusses the design and debugging methods of embedded system power supplies in welding machine control systems based on some problems encountered during the design and debugging of embedded system power supplies.
1 System Hardware Structure
In the design of welding machine control system based on embedded system, AT91RM9200 is used as the core microprocessor of the system. SDRAM, SRAM and Flash are expanded according to the requirements of the control system. The keyboard and LCD display circuit can adjust and display parameters in real time and alarm when errors occur. RS485 serial interface completes data transmission and communication, and infrared remote control operation can be performed. The hardware structure of the system is shown in Figure 1.
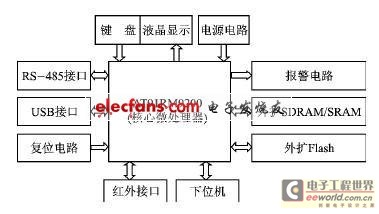
Figure 1 System hardware structure diagram
2 System Power Design
2.1 System Power Supply Working Principle
The AT91RM9200 is a system chip built entirely around the ARM920T processor. It has a rich set of system and application peripherals and standard interfaces, making it a low-power, low-cost embedded industrial-grade product. The AT91RM9200 provides a full-featured power management controller (PMC) that optimizes the power consumption of the entire system and supports normal, idle, slow clock and standby operating modes, providing different power consumption levels and event response delay times [1]. In idle mode, the ARM processor clock is disabled and waits for the next interrupt (or master reset); slow clock mode is the mode selected after reset, in which the main oscillator
The oscillator is the basic circuit of the transceiver. Its function is to generate an AC signal of a certain frequency. It is an energy conversion device that converts DC power into AC power with a certain frequency. The PLL is turned off to reduce power consumption; the Standby mode is a combination of the slow clock mode and the idle mode. It enables the processor to respond quickly to wake-up events and maintain low power consumption. When the system is working normally, it is powered by an external DC power supply and charges the battery. When the external power supply is disconnected, it automatically switches to the internal backup battery for power supply.
2.2 Power Circuit Design
AT91RM9200 has 5 types of power pins: VDDCORE pin is used to power the core, usually 1.8 V; VDDPLL and VDDOSC are used to power the PLL or oscillator, usually 1.8 V; VDDIOP and VDDIOM are used to power the peripheral I/O port line, USB transceiver and external bus interface I/O port line, usually 3.3 V. In addition, the power supply voltage of the keyboard and display circuit of the system requires a +5 V power supply. Therefore, this control system needs to use 3 sets of power supplies. By analyzing the control requirements and performance of the entire control system, it is determined that the load current of this system is about 3 A. Therefore, the voltage regulator chip of the system power supply uses ON's LM2576 series regulator to stabilize the external DC power supply into the +3.3 V and +5 V power supplies required by the system. Since the system core power supply requires 1.8 V, the system should use a secondary power conversion circuit. This article uses TI's micro-power, ultra-low voltage dropout PMOS regulator (LDO chip) TPS72518 as the core power conversion chip to stabilize +3.3 V to +1.8 V to provide working power for the processor core. The system power supply circuit is shown in Figure 2. Figure 2 shows PCB design methods such as embedded system power decoupling. C3 and C6 are electrolytic bypass capacitors of the voltage regulator chip. Connecting them to the circuit can make the circuit work stably; C2, C5, and C8 are output stabilizing capacitors, which have a good effect on reducing output ripple, output noise, and the impact of load current changes. According to the working requirements of the regulator itself, the capacitors are 10 μF and 100 μF electrolytic capacitors respectively.
An electrolytic capacitor is a capacitor made of two parallel metal plates and an electrolyte placed between the two metal plates. The name of the capacitor is given according to the type of electrode material and electrolyte used. The dielectric has an electrolyte coating and has polarity, which can be connected in positive and negative directions and cannot be connected incorrectly.
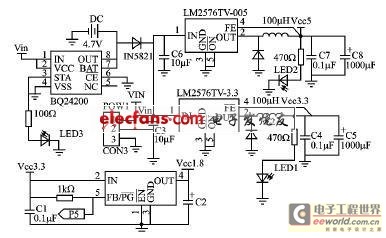
Figure 2 System power circuit diagram
The performance of embedded systems based on 32-bit microprocessors depends largely on the stability and reliability of the clock circuit, while the stability of the clock circuit mainly depends on the stability of the system phase-locked loop (PLL). Therefore, a filter circuit should be used in the power supply of the PLL analog part to ensure the stability of the power supply [2]. The parameters of key components such as the clock, power supply and reset control inside the microprocessor play an important or even decisive role in various operating modes of the system. Therefore, in order to ensure that the set parameters remain unchanged under various operating modes, a backup battery power supply circuit is usually provided in the embedded system design. As shown in Figure 2, TI's battery charger BQ24200 is used as the backup battery for the system power supply. When the system is working normally, the external power supply charges it. When the external power supply is cut off, it provides system power supply so that the system can save important parameters.
3 System power supply debugging
3.1 Debugging content and steps
A relatively large embedded system hardware circuit should be welded and debugged in modules to avoid being unable to check when encountering problems. Since each circuit module in the system needs to be connected to the input power, if the power input is improper, the output result will be incorrect or even burn out the integrated circuit.
Integrated circuits are made by semiconductor manufacturing technology. Many transistors, resistors, capacitors and other components are made on a small single-crystal silicon wafer, and the components are combined into a complete electronic circuit by multi-layer wiring or tunnel wiring. It is represented by the letter "IC" (also with the text symbol "N", etc.) in the circuit. Therefore, the system power module should be installed and debugged first. The successful debugging of the system power circuit module is the key to the successful debugging of the entire hardware circuit.
After soldering the components according to the circuit diagram, carefully check whether the components are soldered correctly, whether there is a cold solder joint or welding slag short circuit on the circuit board, and then power on and debug.
An electronic device that can provide a stable DC power supply to the load. The power supply of a DC stabilized power supply is mostly an AC power supply. When the voltage of the AC power supply or the load resistance changes, the DC output voltage of the regulator will remain stable. As electronic equipment develops towards high precision, high stability and high reliability, DC stabilized power supplies have put forward high requirements for the power supply of electronic equipment.
The generator output power supply is connected to the input port (POW1) of the system power module, and the input power Vin is adjusted to +6 V. The 1.8 V, 3.3 V, and 5 V output ports of the system power supply are checked with an oscilloscope, and there is no voltage output. After the power is turned off and the circuit is checked again, it is found that the electrolytic capacitor C6 has been burned black because the positive and negative polarities of C6 are connected in reverse. After the new capacitor is replaced and welded correctly, it is powered on for debugging. The 1.8 V and 5 V voltage output terminals are normal, while the voltage of the 3.3 V voltage output terminal is less than 3 V. After checking the data sheet of the voltage regulator chip LM2576, the input power Vin is adjusted, and the voltage values of the three sets of system power supplies are detected at the same time. When the three sets of power outputs are correct, the value of the input voltage Vin is about 6.7 V. Since the load current of this control system is about 3 A, a load resistor with a load current of 3 A is added to the circuit to test the stability of the system power supply. After debugging, the components such as capacitors and inductors heat up normally, and the output voltage value is correct. At this point, the system power module is successfully debugged.
Next, we gradually installed and debugged other module circuits. Each time a module was installed, it was powered on for testing, mainly to test whether the system power supply voltage and the input voltage and output results of the module were correct. After the entire system hardware circuit was installed and powered on for debugging, it was found that the system power supply was unstable, that is, the DC regulated input power supply often lost power, causing the system power supply to work abnormally. Since there were many system circuits, it was difficult to check, and the problem had not been solved. After multiple power-on tests and debugging, it was found that a voltage (boost) converter in the circuit was smoking - the chip was burnt. After carefully checking the data sheet of the chip, it was found that the chip model was wrong and the positive and negative feedback voltage pins were connected in reverse. After removing the chip, the system power supply worked normally.
3.2 Analysis of debugging results
The system power debugging and the installation and debugging process of the entire system hardware circuit are analyzed. Combined with the problems encountered during the installation and debugging process, the following conclusions are drawn:
① Chip resistor
Chip fixed resistor, directly translated from Chip Fixed Resistor, commonly known as SMD Resistor, is a type of metal glass uranium resistor. It is a resistor made by mixing metal powder and glass uranium powder and printing it on a substrate using screen printing. It is resistant to moisture, high temperature, and has a small temperature coefficient.
The substrates of capacitors are mostly made of ceramic materials that are easily broken by collision, while the number of pins of surface-mount integrated circuits is large, the spacing is narrow, and the hardness is low, which can easily cause pin solder short circuits, cold solder joints and other faults. Therefore, skills such as temperature control, preheating, and light touch should be mastered during disassembly and welding.
② Before debugging the power module, you must carefully check whether the components are installed correctly, and use a voltmeter to detect whether there are cold soldering or welding slag short circuits in the circuit to ensure the correctness of the circuit and avoid burning out the components.
③ If you are not sure when powering on, you can consider using an adjustable regulated power supply with a current limiting function, slowly increase the voltage value of the regulated power supply, and detect the input current (voltage) and output voltage until the output voltage meets the requirements.
④ When debugging a relatively large system circuit, you should first install and debug the system power supply, and then gradually install and debug other modules after successful debugging. Each time a module is installed, power it on for testing, and then debug another module after ensuring that it is correct.
Conclusion
This article takes the embedded control system based on AT91RM9200 as an example, focusing on the design ideas and methods of the system power circuit and the installation and debugging process of the system power supply. Combined with the problems encountered during the debugging process, the debugging methods and precautions of the embedded system circuit are analyzed. With the widespread application of embedded systems, the design and debugging of power circuits are particularly important, and the design and debugging ideas of this article are worth learning from.
Previous article:Design of Windows Universal Driver Program for PCI Devices
Next article:Application of SOPC in the Design of Embedded Gateway of Jamming System
- Popular Resources
- Popular amplifiers
- Molex leverages SAP solutions to drive smart supply chain collaboration
- Pickering Launches New Future-Proof PXIe Single-Slot Controller for High-Performance Test and Measurement Applications
- CGD and Qorvo to jointly revolutionize motor control solutions
- Advanced gameplay, Harting takes your PCB board connection to a new level!
- Nidec Intelligent Motion is the first to launch an electric clutch ECU for two-wheeled vehicles
- Bosch and Tsinghua University renew cooperation agreement on artificial intelligence research to jointly promote the development of artificial intelligence in the industrial field
- GigaDevice unveils new MCU products, deeply unlocking industrial application scenarios with diversified products and solutions
- Advantech: Investing in Edge AI Innovation to Drive an Intelligent Future
- CGD and QORVO will revolutionize motor control solutions
- Innolux's intelligent steer-by-wire solution makes cars smarter and safer
- 8051 MCU - Parity Check
- How to efficiently balance the sensitivity of tactile sensing interfaces
- What should I do if the servo motor shakes? What causes the servo motor to shake quickly?
- 【Brushless Motor】Analysis of three-phase BLDC motor and sharing of two popular development boards
- Midea Industrial Technology's subsidiaries Clou Electronics and Hekang New Energy jointly appeared at the Munich Battery Energy Storage Exhibition and Solar Energy Exhibition
- Guoxin Sichen | Application of ferroelectric memory PB85RS2MC in power battery management, with a capacity of 2M
- Analysis of common faults of frequency converter
- In a head-on competition with Qualcomm, what kind of cockpit products has Intel come up with?
- Dalian Rongke's all-vanadium liquid flow battery energy storage equipment industrialization project has entered the sprint stage before production
- Allegro MicroSystems Introduces Advanced Magnetic and Inductive Position Sensing Solutions at Electronica 2024
- Car key in the left hand, liveness detection radar in the right hand, UWB is imperative for cars!
- After a decade of rapid development, domestic CIS has entered the market
- Aegis Dagger Battery + Thor EM-i Super Hybrid, Geely New Energy has thrown out two "king bombs"
- A brief discussion on functional safety - fault, error, and failure
- In the smart car 2.0 cycle, these core industry chains are facing major opportunities!
- Rambus Launches Industry's First HBM 4 Controller IP: What Are the Technical Details Behind It?
- The United States and Japan are developing new batteries. CATL faces challenges? How should China's new energy battery industry respond?
- Murata launches high-precision 6-axis inertial sensor for automobiles
- Ford patents pre-charge alarm to help save costs and respond to emergencies
- Why signal isolation is important in 48V HEV/EV systems
- 【Silicon Labs Development Kit Review】+ Unboxing Experience
- IIC Timing Diagram
- Please recommend a 5V to positive and negative 15V op amp power supply circuit or chip to share
- [ESP32 Learning] Reading Hall Sensor
- Lock-in Amplifier Design
- EEWORLD University ----RISC-V 5th workshop
- What is transparent transmission and point-to-multipoint transmission? What are their classic applications and advantages?
- How to build an undervoltage protection circuit using discrete components
- Is there any AMS1117 with 12V output?