Overall design of portable B-ultrasound power supply
Figure 1 is the overall design block diagram of the portable B-ultrasound power supply. There are two types of input voltages for portable B-ultrasound power supply: one is the power adapter input with a voltage of 18V, and the other is the battery input with a voltage of 14.4V. It is required to realize hot switching between the two voltages, and the system operation is not affected when switching the voltage, that is, to provide hot switching function without delay between external power and battery power supply. It is necessary to output several voltages such as ±12V, 5V, 3.3V, ±48V, etc., and the specific indicators are 12V/2.5A, -12V/0.5A, 5V/4A, 3.3V/3A, +48V /80mA, -48V/80mA. It has a single-button power on/off function, that is, when there is no power, press the power button to turn on the power; when there is power, press the power button to send a shutdown signal to the control panel, and the host computer can also shut down through software (that is, it supports ATX shutdown instructions). The power output interface uses a standard computer ATX interface.
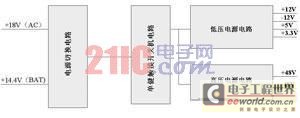
Figure 1 Overall design block diagram
of portable B-ultrasound power supply Design of power switching circuit
The portable B-ultrasound power switching circuit is shown in Figure 2. When the external power adapter is connected, the voltage input is AC 18V, which is added to the 3rd pin (non-inverting end) of the N100A (LM193) voltage comparator after passing through the VD100 and VD101 diodes and then divided by R100 and R107. The battery input voltage is 14.4V, which is added to the 2nd pin (inverting end) of the N100A (LM193) voltage comparator after being divided by R101 and R108. Since the voltage at pin 3 is higher than that at pin 2, pin 1 of N100A (LM193) outputs a high level, turning on transistor V100, turning off V101, and turning off field effect transistor V105. The POWER_IN+ terminal receives the 18V voltage of the external power adapter. When there is no external power adapter, or when the portable B-ultrasound machine is in use and the external AC power suddenly fails and the external power adapter cannot be used, the voltage at pin 3 of N100A (LM193) is lower than that at pin 2, and pin 1 of N100A (LM193) outputs a low level, turning off transistor V100, turning on V101, and turning on field effect transistor V105. The battery voltage passes through the source and drain of the turned-on field effect transistor V105, and the POWER_IN+ terminal receives the 14.4V voltage of the battery, realizing hot switching between the two voltages. VD102 and VD103 act as an isolation in the circuit, isolating the external power adapter from the battery.
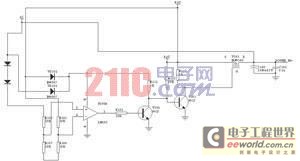
Figure 2 Power switching circuit
Design of single-touch switch circuit
The portable B-ultrasound single-touch switch circuit is shown in Figure 3. The POWER_IN+ voltage from the external adapter or battery is sent to the field effect tube Q100 to prepare for power on, and the other is sent to one end of the touch button POWER-KEY2 through R104 and VD104. The other end of the touch button POWER-KEY2 is grounded. When the touch button POWER-KEY2 is pressed, the base of the transistor N106 is clamped at a low level, N106 is turned on, and then N102 is also turned on, and the field effect tube Q100 is turned on. The POWER_IN+ voltage from the external adapter or battery passes through the source and drain of the turned-on Q100 to obtain the POWER+ voltage, which powers the high and low voltage circuits and turns on the machine. When the machine is turned on, the POWER+ voltage passes through the 6V voltage regulator diode to turn on transistor N104. The collector of N104 is at a low level, which keeps N106 turned on and keeps the machine turned on.
Figure 3 Single-touch switch circuit
When the portable B-mode ultrasound machine is in the power-on state, when the button POWER-KEY2 is pressed again, the optocoupler B101 is turned on, the optocoupler secondary is turned on, and the 4th pin of the inverter D101 outputs a low level to the control panel. The control panel issues a low-level shutdown command POWER-OFF1, which turns on the optocoupler B100, and then turns on the transistor N103, N104 is turned off, and the high level of the collector of N104 turns off N106, causing the field effect tube Q100 to turn off, and the machine is turned off.
When the host computer issues a high-level shutdown command POWER-OFF, it will also turn on the optocoupler B100, and the remaining process is the same as the control panel shutdown process.
Design of low-voltage power supply circuit
The portable B-mode ultrasound low-voltage power supply circuit is shown in Figure 4, which mainly consists of 6 TPS5430s from TI and 1 LM2576 from National Semiconductor. Six TPS5430s provide two groups of +12V, +5V, and +3.3V voltages, one of which is used to power the main control board of the portable B-ultrasound machine, and the other is used to power the computer in the portable B-ultrasound machine. These two groups are exactly the same, so we only give the power supply schematic diagram of one group. LM2576 is responsible for generating -12V voltage for the computer in the portable B-ultrasound machine.
Figure 4 Low-voltage power supply circuit
TPS5430 has a wide voltage input range of 5.5 to 36V, a continuous current output capacity of 3A (peak value of 4A), and a conversion efficiency of 95%. 8-pin small SMD package, the back of the chip is a metal heat sink, which must be soldered to the ground when used, and the heat sink is regarded as the 9th pin when making PCB packaging. There is no need to connect a heat sink, and the heat dissipation of the circuit board itself can achieve good results, which is particularly suitable for the design and use of portable products. Pin 1 of TPS5430 is the BOOT terminal, and a low ESR capacitor of 0.01μF is required between BOOT and pin 8 PH. Pins 2 and 3 are empty terminals. Pin 4 VSENSE is the feedback voltage terminal of the regulator. It is connected to the voltage divider resistor of the output voltage to obtain the feedback of the output voltage. Pin 5 ENA is the power ON/OFF control terminal. When the voltage of this pin is lower than 0.5V, the chip will shut down the power conversion and the supply current will be reduced to 18μA. When it is suspended, it is enabled and the chip works normally. We have no control over this pin, so it is suspended. Pin 6 is grounded. Pin 7 VIN is the power supply terminal, connected to POWER+. A high-quality, low-ESR ceramic capacitor is connected between the power supply and the ground. Pin 8 PH is the source of the internal power field effect tube, and the freewheeling diode and inductor are connected externally. The PowerPad terminal of pin 9 is the heat dissipation metal sheet on the back of the chip, which must be connected to the ground (GND).
The output voltage value of TPS5430 is determined by the voltage divider voltage value of its pin 4. The output voltage Vout = (1.221 + (R1×1.221)/R2) V. Among them, R1 is the upper resistor of the voltage divider, and R2 is the lower resistor of the voltage divider. For the design of TPS5430, R1 can be 10kΩ, and R2 can be calculated according to the output voltage to be obtained. According to R206 (1.11K), R208 (3.07K), and R210 (5.36K) given in Figure 4, we can calculate that the output voltage is 12.2V, 5.2V, and 3.5V respectively, which is slightly higher than the design value by 0.2V. The load is relatively heavy, and the voltage is just right when loaded.
N208 (LM2576-12) is a product of National Semiconductor. Pin 1 is the power supply terminal, connected to POWER+; Pin 2 is the output terminal, connected to a freewheeling diode and an inductor; Pin 3 is the ground terminal, and Pin 5 is the power ON/OFF control terminal. Since a negative voltage is to be output, Pins 3 and 5 are not grounded but connected to a -12V power supply; Pin 4 is the voltage feedback terminal. We use the LM2576-12 with a fixed 12V output, so Pin 4 is grounded and does not need to be connected to a feedback resistor for voltage division.
Design of high-voltage power supply circuit
The portable B-mode high-voltage power supply circuit is shown in Figure 5, using a DC/DC converter. UA3843 is a high-performance, fixed-frequency, current-mode controller specifically designed for DC/DC converter applications, providing designers with a cost-effective solution using minimal external components. It is divided into PWM control, frequency current limiting, voltage control, and other parts.
Figure 5 ±48V power supply circuit
1 PWM control
POWER+ provides voltage to the 7th pin of N1 (UA3843) through resistor R34, and the sawtooth oscillator formed by the external R36, C33 and the internal circuit of N1 at the 4th pin starts to work. The PWM pulse is output from the 6th pin of N1 to control the conduction time of MOSFET V9 and determine the level of the output voltage. R37 is used to suppress parasitic oscillation and is usually connected in series near the gate of MOSFET. The gate resistor R37 cannot be too large, which directly affects the charging and discharging of the MOSFET input capacitance by the PWM drive signal, that is, affects the switching speed of MOSFET. The induced electromotive force output from the 9th and 10th pins of the secondary of the switching transformer is rectified by VD14 and filtered by C35, L7, and C36 to form a +48V DC output voltage to power the B-ultrasound probe. The induced electromotive force output from the 7th and 6th pins of the secondary of the switching transformer is rectified by VD13 and filtered by C39, L8, and C37 to form a -48V DC output voltage to power the B-ultrasound probe. VD12, C34, and R38 form a spike pulse absorption circuit, which is used to suppress the extremely high-amplitude spike pulse generated by the drain of V9 at the moment when the switch tube changes from on to off. The principle is: at the moment when V9 is cut off, the spike pulse generated by its drain forms a charging circuit through VD12 and C34. The charging current suppresses the spike pulse within a certain range, avoiding V9 from being broken down by the spike pulse. When C34 is charged, C34 discharges through R38 to prepare for absorbing the spike pulse again in the next cycle.
2 Cyclic current limit
2 pin FEED BACK is the feedback voltage input terminal. This pin is compared with the reference voltage (usually +2.5V) of the in-phase input terminal of the internal error amplifier to generate a control voltage to control the width of the pulse. This circuit is grounded and controlled by the output terminal 1 of the internal error amplifier. The cyclic current limit signal at pin 3 determines the width of the PWM pulse, that is, determines the level of the output voltage. The R47, R48, R14, and C32 connected to the 3rd pin of N1 (UA3843) form a cyclic current limiting circuit. In each oscillation cycle, when the peak value of the inductance current of the primary windings 3 to 5 of the switching power supply pulse transformer L6 reaches the set value, the PWM pulse is turned off. The set value is determined by the voltage of the COMP terminal of the 1st pin of N1 (UA3843) (COMP of the 1st pin is the output terminal of the internal error amplifier). Usually, a feedback network is connected between this pin and the 2nd pin to determine the gain and frequency response of the error amplifier. The cyclic current limiting control process is as follows: the switch tube is turned on, the inductance current rises, and the sampling voltage V3 rises. When the voltage of the 3rd pin is greater than 1V, the internal current detection comparator flips, the internal PWM latch is reset, and the PWM pulse is turned off to prepare for the next cycle. In order to eliminate the spike pulse interference of the current limiting circuit, a spike filter circuit is formed by R14 and C32 to ensure that the cyclic current limiting function is effective in each oscillation cycle. R47 and R48 are current limiting sampling resistors, which determine the maximum output current value of the entire switching converter. Changing their resistance values can adjust the maximum output current.
3 Voltage Control
N1 (UA3843) is a current-type pulse width modulator with two closed-loop controls. The current sampling signal is sent to the non-inverting input terminal 3 of the current detection comparator to form a current closed-loop control, and the error voltage is sent to the output terminal 1 of the internal error amplifier. Its output is sent to the inverting input terminal of the current detection comparator as a comparison reference to form a voltage closed-loop control. It can be seen from this that the voltage closed loop and the current closed loop interact with each other. Both of them finally control the PWM latch through the current detection comparator, that is, control the width of the PWM pulse. The voltage closed-loop control circuit consists of components such as voltage reference N2 (TL431A), photocoupler B4 (TLP521), and resistors R31, VR7, R12, and R32. The current signal output by the photocoupler B4 (TLP521) is converted into a voltage signal and sent to the output terminal 1 of the internal error amplifier. The internal comparison reference of the N2 (TL431A) error amplifier is 2.5V. The voltage closed-loop voltage regulation control process is: the output voltage rises, the reference end VR of TL431A rises, the TL431 turns on and rises, the optocoupler B4 (TLP521) turns on and rises, the voltage of pin 1 drops, the internal current detection comparator flips in advance, the internal PWM latch resets in advance, the PWM pulse becomes narrower, and the output voltage becomes lower, thereby stabilizing the output voltage. The high-voltage output voltage value VOUT=(1+R31/(R12+VR7))Vref, by adjusting the value of potentiometer VR7, the output can be adjusted to ±48V, and the adjustment range is 31×2.5=77.5V~(1+15)×2.5=32V.
Conclusion
This article introduces the design of a portable B-mode ultrasound power supply, including the design of a power switching circuit, a single-touch switch circuit, a low-voltage power supply circuit, and a high-voltage power supply circuit. The design index requirements are well met in our portable devices and can be applied to other portable devices.
Previous article:Design and application of "healthy" technical archive system for medical equipment
Next article:Application of Low Voltage Operational Amplifiers in Medical Electronics
- Popular Resources
- Popular amplifiers
- Molex leverages SAP solutions to drive smart supply chain collaboration
- Pickering Launches New Future-Proof PXIe Single-Slot Controller for High-Performance Test and Measurement Applications
- CGD and Qorvo to jointly revolutionize motor control solutions
- Advanced gameplay, Harting takes your PCB board connection to a new level!
- Nidec Intelligent Motion is the first to launch an electric clutch ECU for two-wheeled vehicles
- Bosch and Tsinghua University renew cooperation agreement on artificial intelligence research to jointly promote the development of artificial intelligence in the industrial field
- GigaDevice unveils new MCU products, deeply unlocking industrial application scenarios with diversified products and solutions
- Advantech: Investing in Edge AI Innovation to Drive an Intelligent Future
- CGD and QORVO will revolutionize motor control solutions
- Innolux's intelligent steer-by-wire solution makes cars smarter and safer
- 8051 MCU - Parity Check
- How to efficiently balance the sensitivity of tactile sensing interfaces
- What should I do if the servo motor shakes? What causes the servo motor to shake quickly?
- 【Brushless Motor】Analysis of three-phase BLDC motor and sharing of two popular development boards
- Midea Industrial Technology's subsidiaries Clou Electronics and Hekang New Energy jointly appeared at the Munich Battery Energy Storage Exhibition and Solar Energy Exhibition
- Guoxin Sichen | Application of ferroelectric memory PB85RS2MC in power battery management, with a capacity of 2M
- Analysis of common faults of frequency converter
- In a head-on competition with Qualcomm, what kind of cockpit products has Intel come up with?
- Dalian Rongke's all-vanadium liquid flow battery energy storage equipment industrialization project has entered the sprint stage before production
- Allegro MicroSystems Introduces Advanced Magnetic and Inductive Position Sensing Solutions at Electronica 2024
- Car key in the left hand, liveness detection radar in the right hand, UWB is imperative for cars!
- After a decade of rapid development, domestic CIS has entered the market
- Aegis Dagger Battery + Thor EM-i Super Hybrid, Geely New Energy has thrown out two "king bombs"
- A brief discussion on functional safety - fault, error, and failure
- In the smart car 2.0 cycle, these core industry chains are facing major opportunities!
- Rambus Launches Industry's First HBM 4 Controller IP: What Are the Technical Details Behind It?
- The United States and Japan are developing new batteries. CATL faces challenges? How should China's new energy battery industry respond?
- Murata launches high-precision 6-axis inertial sensor for automobiles
- Ford patents pre-charge alarm to help save costs and respond to emergencies
- "TGF4042 Signal Generator" Synchronous Trigger Measurement
- The main characteristics of the antenna (reposted)
- It’s almost the end of the year, do you have any new plans for the New Year?
- Huawei Ethernet Clock Synchronization Technology_Clock Transmission Technology White Paper
- How to use MRS IDE
- ADI Live Show starts at 10:00 this morning | Multi-parameter optical water quality analysis platform
- Qorvo Online Design Conference丨5G Solutions Supporting NAD and Telematics Unit Applications
- How to enable ADC group and DMA in STM32F030
- Talk about ARM architecture and programming model
- The problem of the transistor emitter voltage in the figure