In recent years, with the increasing maturity of LED technology, LED light sources have been increasingly widely used due to their advantages of using low-voltage power supply, low energy consumption, strong applicability, high stability, short response time, and multi-color luminescence. Most LED power supplies use switching power supply technology, and the output is mostly a constant current source that can change the voltage as the forward voltage drop value of the LED changes, that is, a constant current drive. According to the volt-ampere characteristics of the LED, a small change in voltage can lead to a large change in current, which may damage the LED. In addition, the control circuit in the switching power supply is relatively complex, and the transistors and integrated devices have poor ability to withstand electrical and thermal shocks. Therefore, the reliability of the driving power supply affects the life of the LED application product. In order to protect the safety of the switching power supply itself and the load and extend the service life, a safe and reliable protection circuit must be designed.
1 Shoot-through protection circuit
Half-bridge and full-bridge are commonly used topologies for switching power supplies. "Shoot-through" poses a great threat to them. Shoot-through is the phenomenon that two transistors in the same bridge arm are turned on at the same time. During the commutation period, the switching power supply is susceptible to interference and causes shoot-through. Excessive shoot-through current will damage the power electronic devices used for inversion. Once the shoot-through phenomenon occurs, it must be detected as soon as possible and the drive must be turned off immediately to avoid the PN junction of the switching device accumulating too much heat and burning out. Here, a shoot-through detection and protection circuit for full-bridge and half-bridge is designed using the dual monostable integrated trigger CD4528.
CD4528 contains two monostable triggers, and its truth table is shown in Figure 1. Pins 3 and 13 of the chip are the Clear terminals of the two independent monostable circuits inside, pins 5 and 11 are the B input terminals of the monostable, and pins 4 and 12 are the A input terminals of the monostable. The B terminal is connected to a high level, and the rising edge trigger of the A terminal input will only be effective when the Clear terminal is at a high level.
PWM1 and PWM2 are two complementary pulse signals output by the PWM chip. The driving of Q1 and Q4 in the main circuit (see Figure 2) is synchronized with PWM1 in Figure 3, and the driving of Q2 and Q3 is synchronized with PWM2. The current rise rate is sampled at points A, B, C and D4 and then converted into a voltage signal, which is given to the through signal 1 and through signal 2 in Figure 3 respectively.
The left and right bridge arms in the main circuit are symmetrical, so the direct protection of the left bridge arm is analyzed. Under normal conditions, when Q1 and Q4 are turned on, PWM1 is high level, PWM2 is low level, the high level input of pin 3 is valid, no current flows through points A and D, and the monostable will not be triggered; although points B and C sample the rising edge signal of the normal output, the input is invalid when pin 13 is low level, so the monostable will not be triggered, and no protection signal is output; in direct pass, Q3 is misdirected for some reason, and point A will detect a large current rise rate and convert it into a voltage signal; at this time, PWM1 is high level, and the monostable on the left in Figure 3 is triggered to generate a protection signal sent to the shutdown terminal of the PWM chip, blocking the PWM pulse output.
2 Overcurrent protection circuit
When there are unexpected situations such as load short circuit, overload or control circuit failure, the current flowing through the switch tube will be too large, causing the tube to consume more power and generate heat. If there is no overcurrent protection device, the high-power switch tube may be damaged; failure of the regulation circuit may also cause overcurrent damage to the LED. Overcurrent protection is generally achieved through detection and comparison by sampling resistors or Hall sensors, but they all have the disadvantages of large size and high cost.
Here, the method shown in Figure 4 is used, and a thinner wire coil with the same number of turns is placed on the choke of the forward converter. The two windings are magnetically balanced, and there should be no voltage difference between them. However, the main winding has a DC resistance, and a small voltage difference is generated at high currents, which is determined by the load current. This small voltage difference is detected by the op amp, and the current limit can be set by adjusting Rx. The disadvantage of this circuit is that the current limit is not very precise, because the copper resistance increases by 4% for every 10°C increase in temperature. However, this circuit can still meet our design requirements.
3. Power on and power off current overshoot protection circuit
The current-stabilized switching power supply is prone to current overshoot when it is turned on and off. Loads such as LEDs do not allow current overshoots of the ms level. The instantaneous large current impact may damage the LED device, so current overshoot must be strictly prevented.
3.1 Power-on current overshoot protection
When the power is turned on, due to the large power filter capacitor and the delay links, the current sampling feedback value is different from the given value at the regulator input, which will cause the load current to overshoot. The measured overshoot waveform is shown in Figure 5. In order to solve this problem, the value of the regulator given end RC can be appropriately increased. After adjustment, the startup current does not overshoot, and the waveform is shown in Figure 6.
3.2 Shutdown current overshoot protection
In the 30A/20V switching current-stabilized power supply we designed, the control circuit is used for separate power supply. The filter capacitor of the main circuit stores a large amount of electrical energy during operation. After the main power supply is cut off, the stored charge will take several seconds to be discharged. Therefore, after shutdown, the sampling circuit with separate power supply is turned off first and the main circuit is turned off later. The given input of the regulator is powered by the main circuit, that is, after shutdown, the sampling input of the regulator is reduced first, and the given end is reduced slowly, so its output error voltage increases, and the control chip increases the duty cycle of PWM, which leads to severe overshoot of the load current during shutdown. The current waveform during overshoot is shown in Figure 7.
FIG8 is a shutdown current overshoot protection circuit. The circuit can quickly detect whether the AC power is turned off within 3ms, and forcefully lower the voltage at the given input terminal of the regulator after the power is turned off to prevent current overshoot. The specific operation process is as follows.
Optocouplers U1 and U2 conduct alternately with the positive and negative half cycles of the power supply under test. When the AC voltage at point A is greater than the conduction voltage Von of the light-emitting diode in the optocoupler, the optocoupler turns on, and C3 discharges through the triode in the optocoupler, so that the voltage at point B does not reach the turn-on voltage of the field effect tube; when the AC voltage is less than Von, the optocoupler does not conduct, C3 charges, and the voltage at point B increases. At this time, the time for the voltage of C3 to rise to the threshold of the field effect tube should be greater than the time for the optocoupler to turn off, so as to ensure that Q2 does not conduct. At t1, the AC power supply is disconnected, the output of the optocoupler is in a high-impedance state, and the charge stored in C2 charges C3 through R1. The voltage on C3 increases rapidly. When the voltage at point B is greater than the turn-on voltage of the field effect tube, the field effect tube Q2 conducts, and after conducting, Vs can be quickly pulled down. In Figure 8, Vs is the given input voltage of the regulator. The load current at the moment of shutdown and the waveform at point B in Figure 8 are shown in Figure 9. Changing the parameters of R1 and R4 can change the time for charging C3. If R4 is selected with a larger resistance value, the voltage on C3 can be increased and the discharge time of C3 can be extended. The size of C2 can determine the time for the circuit to maintain operation after the AC power is cut off. In summary, setting reasonable parameters can ensure that Q2 is always turned on when the main circuit power is not completely turned off, that is, the given input terminal of the error amplifier is always zero, avoiding current overshoot.
4 Overvoltage protection circuit
If the load of a current-stabilized power supply is disconnected, the voltage across the current detection resistor drops to zero. Once the given value is not zero, the regulator will cause the output voltage to soar to the maximum value, which is very dangerous when the load connection is poor. For loads such as LEDs and semiconductor refrigeration, when overvoltage occurs, the first task is to protect the load, followed by protecting the switching power tube.
To solve the above problems, two protection methods are used simultaneously. One is to place a bidirectional TVS to protect against transient impulse voltage.
TVS is a high-efficiency protection device in the form of a diode. When the two poles of the TVS diode are subjected to a reverse transient high-energy impact, it can change the high impedance between the two poles into a low impedance at a speed of nanoseconds, absorb up to several kilowatts of surge power, and clamp the voltage between the two poles at a predetermined value, effectively protecting the components in the electronic circuit from damage by various surge pulses. The resistor can also be connected in series with the TVS. When the TVS is not broken down, there is no current on the resistor. If an overvoltage occurs, the TVS is broken down, and current flows through the resistor, generating a voltage drop, which is used as a protection signal and sent to the shutdown terminal of the PWM chip to block the PWM pulse output. Another method is to stop the power supply immediately when the load is disconnected, as shown in Figure 10, where R24 and R27 provide a fixed small voltage U+ to the op amp's in-phase input terminal. R26 is the sampled load current input. When the load is disconnected, the voltage at the op amp's inverting input terminal U-=0, so U+>U-, the op amp output voltage is high, and a no-load protection signal is given. At the same time, the time constant R30×C15 is adjusted in coordination with the time constant given by the power supply so that the no-load protection does not malfunction.
5 Conclusion
This article mainly discusses several protection methods for LED power supplies and introduces some specific circuits. For a given DC switching power supply, whether the protection circuit is complete and works according to the preset settings is crucial to the safety and reliability of the power supply device. The reliability of the power supply will affect the life of the LED product, so it is usually necessary to combine several protection methods to form a complete protection system to ensure the normal operation of the DC switching power supply. We actually use these measures to drive LED loads, which works safely and reliably.
Previous article:Brief analysis of the thermal characteristics of LED lighting in practical applications
Next article:Interpretation of the development history of LED lighting and LED display
Recommended ReadingLatest update time:2024-11-17 00:02
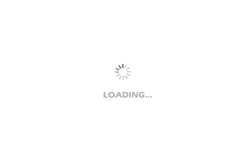
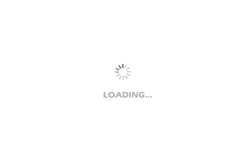
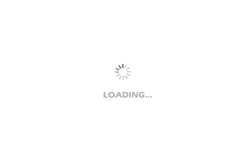
- Popular Resources
- Popular amplifiers
- MathWorks and NXP Collaborate to Launch Model-Based Design Toolbox for Battery Management Systems
- STMicroelectronics' advanced galvanically isolated gate driver STGAP3S provides flexible protection for IGBTs and SiC MOSFETs
- New diaphragm-free solid-state lithium battery technology is launched: the distance between the positive and negative electrodes is less than 0.000001 meters
- [“Source” Observe the Autumn Series] Application and testing of the next generation of semiconductor gallium oxide device photodetectors
- 采用自主设计封装,绝缘电阻显著提高!ROHM开发出更高电压xEV系统的SiC肖特基势垒二极管
- Will GaN replace SiC? PI's disruptive 1700V InnoMux2 is here to demonstrate
- From Isolation to the Third and a Half Generation: Understanding Naxinwei's Gate Driver IC in One Article
- The appeal of 48 V technology: importance, benefits and key factors in system-level applications
- Important breakthrough in recycling of used lithium-ion batteries
- Innolux's intelligent steer-by-wire solution makes cars smarter and safer
- 8051 MCU - Parity Check
- How to efficiently balance the sensitivity of tactile sensing interfaces
- What should I do if the servo motor shakes? What causes the servo motor to shake quickly?
- 【Brushless Motor】Analysis of three-phase BLDC motor and sharing of two popular development boards
- Midea Industrial Technology's subsidiaries Clou Electronics and Hekang New Energy jointly appeared at the Munich Battery Energy Storage Exhibition and Solar Energy Exhibition
- Guoxin Sichen | Application of ferroelectric memory PB85RS2MC in power battery management, with a capacity of 2M
- Analysis of common faults of frequency converter
- In a head-on competition with Qualcomm, what kind of cockpit products has Intel come up with?
- Dalian Rongke's all-vanadium liquid flow battery energy storage equipment industrialization project has entered the sprint stage before production
- Allegro MicroSystems Introduces Advanced Magnetic and Inductive Position Sensing Solutions at Electronica 2024
- Car key in the left hand, liveness detection radar in the right hand, UWB is imperative for cars!
- After a decade of rapid development, domestic CIS has entered the market
- Aegis Dagger Battery + Thor EM-i Super Hybrid, Geely New Energy has thrown out two "king bombs"
- A brief discussion on functional safety - fault, error, and failure
- In the smart car 2.0 cycle, these core industry chains are facing major opportunities!
- The United States and Japan are developing new batteries. CATL faces challenges? How should China's new energy battery industry respond?
- Murata launches high-precision 6-axis inertial sensor for automobiles
- Ford patents pre-charge alarm to help save costs and respond to emergencies
- New real-time microcontroller system from Texas Instruments enables smarter processing in automotive and industrial applications
- Commonly used algorithms for drones - Kalman filter (XII)
- Application of Torque Sensors in the Automotive Industry
- Vayo-CAM365 Function Detailed Explanation (I)
- Apply for DCM evaluation samples for free!
- ESP32 Arduino 2.0.3 has been released
- What is your understanding of Article 82 of the Labor Contract Law of the People’s Republic of China?
- [Synopsys IP Resources] Automotive SoCs will be reshaped, and IP will usher in new changes
- Technical Article: What is Switch Mode Power Supply Current Sensing?
- 1. When it comes to the conduction condition of NMOS, VGS>0 is sufficient. But after conduction, won't VS be greater than VG? 2. We...
- How to measure intermittent current?