Most cars use the same set of LEDs for their taillights and brake lights, which requires the LEDs to operate at two different brightness levels: full brightness when braking, and 10% to 25% full brightness (dimmable) when used as taillights and running lights. Pulse width modulation (PWM) is the best dimming method, which can maintain the LED color spectrum over the entire brightness range. In addition, using an LED driver with a built-in 200Hz oscillation circuit can eliminate the need for an external PWM signal generator, simplifying the design.
The taillight (adjustable LED brightness) and brakelight (full brightness) are controlled by the TAIL and STOP inputs of the LED driver. When a voltage is applied to the TAIL terminal, the taillight LED is driven to 10% to 25% of full brightness. When a voltage is applied to the STOP terminal (brake), the LED is driven to full brightness (regardless of the state of the TAIL terminal input).
Tail Light Driver Specifications
The input power supply voltage (between STOP or TAIL and ground) is nominally 6V to 16V and may reach 45V under load dump.
The output voltage (VLED) can reach up to (VIN-1.4V).
The output current (LED current) when braking is 350mA, 240mA or 140mA, depending on the J1 setting.
The taillight LED current is regulated at 20% of full brightness via a PWM signal.
enter
STOP: A 6V~16V input voltage is applied between STOP(+) and GND(-) to drive the LED with a continuous current of 350mA, 240mA or 140mA, which is set by J1.
TAIL: A 6V~16V input voltage is applied between TAIL(+) and GND(-), driving the LED at 350mA, 240mA or 140mA with a 10% duty cycle. The current is set by J1.
Output
LED+: Connect to LED anode.
LED-: Connect to LED cathode.
Circuit Description
The LED driver for the car taillight (STOP and TAIL mode) can be simply implemented using a linear LED driver IC (e.g. MAX16804) with minimal external components. Figure 1 shows the corresponding circuit schematic, and Figure 2 shows the PCB layout. The maximum current flowing through the LED is set by R3 or R4, which is controlled by the connection method of J1. The brightness is controlled by a PWM signal, which is implemented inside the IC. The driver IC generates a 200Hz LED current regulation signal, and the duty cycle depends on the voltage at the DIM terminal. For example, when the DIM terminal voltage is 0.78V, the taillight brightness is set at 20% of the full brightness.
Figure 1: MAX16804 high-brightness LED driver schematic
The STOP and TAIL inputs are connected to the IN pin through diodes D1 and D2. The IC can be powered from either input without affecting each other. D1 and D2 also provide reverse voltage protection from voltage spikes on the automotive power bus. Capacitors C4 and C3 bypass any noise on the STOP power line and provide protection for the DIM pin.
Tail light driving lighting working mode
A fixed 0.78V voltage is generated from the TAIL input to the DIM terminal (generated from the +5V regulated output), and the driver converts this voltage into a 20% PWM duty cycle to regulate the LED current. The PWM duty cycle in TAIL mode is independent of the input voltage at the TAIL terminal, and the DIM voltage in TAIL mode is set by the resistor divider R1/R2. If the duty cycle setting is required to be different from 20%, the corresponding DIM voltage (VDIM) can be calculated according to the following formula.
Where D is the required duty cycle.
Select R1 and R2 according to formula 2 to meet the DIM voltage requirements.
In the formula, 0.6V is the forward voltage of the diode, 5V is the regulator output, and VDIM is the required DIM pin voltage to meet the PWM duty cycle requirements. In order to avoid the DIM voltage being affected by the change of the DIM input bias current, R2 is selected to be around 20kΩ.
Figure 2: PCB layout of the MAX16804 circuit
Braking mode
In order to obtain a 100% duty cycle, the DIM voltage needs to be set above 3.1V. When the STOP terminal is input with voltage, the DIM terminal obtains sufficient drive voltage through D3 to ensure a 100% PWM duty cycle. At this time, no matter what voltage is input to the TAIL terminal, the LED will be driven with a continuous current of 350mA.
LED Current Setting
The MAX16804 circuit shown in Figure 1 can set three different currents (140mA, 240mA, or 350mA) through jumper J1. As shown in Table 1:
Table 1: Jumper J1 sets three different current connection methods.
If a different current setting is required, the current-sense resistor (R3 or R4) can be calculated as follows.
Where 0.198V is the current-sense voltage and IOUT is the required LED current in A.
Power consumption
The device (MAX16804) is capable of dissipating 2.758W of power. In this application, the maximum power consumption is in STOP mode. The maximum power consumption is calculated as follows:
VIN is the input voltage of the IN pin, VLED is the forward voltage of the LED string, and 350mA is the maximum LED current set by jumper J1. Most of the device power dissipates through the exposed pad. In order to improve heat dissipation, the exposed pad should be soldered to a circuit board pad of the same area, and multiple vias should be used to connect the exposed pad to the copper-clad area of the ground layer.
The MAX16804 can dissipate the maximum rated power at 25°C room temperature, and the power dissipated is reduced when the ambient temperature is higher. To prevent the IC from entering thermal shutdown, the power consumption should be appropriately reduced at high temperatures.
Circuit Connection
LED+ is connected to the anode of the LED, and LED- is connected to the cathode of the LED.
To obtain a 350mA LED current, select pins 1 and 2 of J1.
In STOP mode, the power supply voltage is connected between STOP (+) and GND (-), and the minimum voltage is 6V, which is at least 1.4V higher than the forward voltage of the LED.
In TAIL mode, remove the STOP power supply and connect the power supply voltage between TAIL (+) and GND (-).
Test Results
During the test, the maximum LED current was set at 350mA and 240mA. In STOP mode, the LED is at full brightness. After the power supply voltage is applied between STOP and ground, the LED current will quickly rise to the set value (350mA or 240mA). The LED is driven with continuous current and there is no overshoot.
In TAIL mode, the 200Hz, 20% duty cycle PWM control signal only allows current to flow through the LED within 1/5 of the cycle, thereby reducing the LED brightness. In STOP and TAIL modes, the LED current amplitude is the same, and the limited rise and fall time helps improve EMI indicators.
Previous article:High Current LED Driver Design for Automotive/HDTV Backlighting
Next article:Design Analysis and Examples of High-Power LED Constant-Current Driving Circuit
Recommended ReadingLatest update time:2024-11-16 18:00
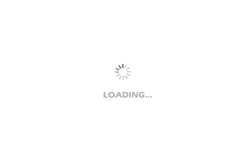
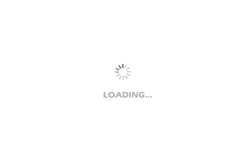
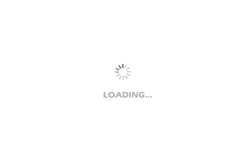
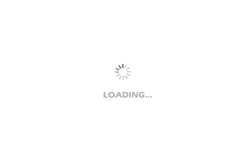
- MathWorks and NXP Collaborate to Launch Model-Based Design Toolbox for Battery Management Systems
- STMicroelectronics' advanced galvanically isolated gate driver STGAP3S provides flexible protection for IGBTs and SiC MOSFETs
- New diaphragm-free solid-state lithium battery technology is launched: the distance between the positive and negative electrodes is less than 0.000001 meters
- [“Source” Observe the Autumn Series] Application and testing of the next generation of semiconductor gallium oxide device photodetectors
- 采用自主设计封装,绝缘电阻显著提高!ROHM开发出更高电压xEV系统的SiC肖特基势垒二极管
- Will GaN replace SiC? PI's disruptive 1700V InnoMux2 is here to demonstrate
- From Isolation to the Third and a Half Generation: Understanding Naxinwei's Gate Driver IC in One Article
- The appeal of 48 V technology: importance, benefits and key factors in system-level applications
- Important breakthrough in recycling of used lithium-ion batteries
- Innolux's intelligent steer-by-wire solution makes cars smarter and safer
- 8051 MCU - Parity Check
- How to efficiently balance the sensitivity of tactile sensing interfaces
- What should I do if the servo motor shakes? What causes the servo motor to shake quickly?
- 【Brushless Motor】Analysis of three-phase BLDC motor and sharing of two popular development boards
- Midea Industrial Technology's subsidiaries Clou Electronics and Hekang New Energy jointly appeared at the Munich Battery Energy Storage Exhibition and Solar Energy Exhibition
- Guoxin Sichen | Application of ferroelectric memory PB85RS2MC in power battery management, with a capacity of 2M
- Analysis of common faults of frequency converter
- In a head-on competition with Qualcomm, what kind of cockpit products has Intel come up with?
- Dalian Rongke's all-vanadium liquid flow battery energy storage equipment industrialization project has entered the sprint stage before production
- Allegro MicroSystems Introduces Advanced Magnetic and Inductive Position Sensing Solutions at Electronica 2024
- Car key in the left hand, liveness detection radar in the right hand, UWB is imperative for cars!
- After a decade of rapid development, domestic CIS has entered the market
- Aegis Dagger Battery + Thor EM-i Super Hybrid, Geely New Energy has thrown out two "king bombs"
- A brief discussion on functional safety - fault, error, and failure
- In the smart car 2.0 cycle, these core industry chains are facing major opportunities!
- The United States and Japan are developing new batteries. CATL faces challenges? How should China's new energy battery industry respond?
- Murata launches high-precision 6-axis inertial sensor for automobiles
- Ford patents pre-charge alarm to help save costs and respond to emergencies
- New real-time microcontroller system from Texas Instruments enables smarter processing in automotive and industrial applications
- What factors need to be considered in the practical application of RFID?
- [AT-START-F403A Review] Part 6: On-chip Flash performance test
- Why can't the microcontroller receive data during Proteus simulation? The digital tube does not change
- nRF51802/nRF51822/nRF52832 Core Comparison
- [2022 Digi-Key Innovation Design Competition] + K210 & STM32F429-DK
- Regarding the problem of op amp, ask online
- Free application for VICOR "Bidirectional 48V/12V Converter Module" evaluation board
- The FFT function and application of digital oscilloscope
- TI DSP TMS320C66x SPI Nor Flash multi-core program burning
- AD2S1200, a resolver with 2 pairs of poles, but each pair of poles has 4 groups of 0-4096 outputs.