LED driver technical indicators
● Input power supply voltage: 10V to 15V
● LED drive current: 10A
● LED forward bias voltage: 4.5V to 6V
● LED current rise/fall time: < 1us
● LED current ripple: 10% peak-to-peak, maximum
enter
● VIN (J4): Power input
● PWMR, PWMB, PWMG (pins 1, 3 and 4 of J8): RGB PWM input signals, the amplitude should be 3.3V to 5V. When the rise/fall time of the output is kept within 1?s, any PWM period exceeding 2?s can be used. Only one of the above three signals is high at a time.
● PWMN (Pin 4 of J8): PWMR, PWMG, and PWMB are logically NORed. PWMN is high only when all three PWM signals are low.
● ON/OFF (J1): Leave open or drive to +5V to enable the driver, connect to GND to disable the board operation.
Output
● LEDR, LEDG, LEDB (J5, J6, and J7): 10A RGB LED output. Connect LED+ to pins 3, 4, and 5; connect LED- to pins 6, 7, and 8.
● OUTV (J2): Provides a signal proportional to the LED current. The voltage on OUTV is 135 times the voltage across R12||R16.
● VIN_OUT (J3): Input supply voltage for connecting to other boards. Pins 1 and 2 are VIN+; pins 3 and 4 are GND.
Figure 1. LED driver circuit board (top layer)
Figure 2. LED driver circuit board (bottom layer)
Figure 3. Schematic diagram of an LED driver based on the MAX16821.
Circuit Description
Low-power projectors use a single-chip DLP to process RGB colors. Only one color DLP is lit at any given time. This approach enables the use of a high-current driver with a few additional switches to switch between LEDs, resulting in a compact and economical projector design.
The LED driver reference design provided in this article uses a single buck converter to sequentially drive RGB LEDs with 10A current. MOSFETS Q8, Q9, and Q10 select and switch the regulated inductor current to drive one of the RGB LEDs based on the PWM signal.
The core circuit of the MAX16821B buck converter operates in average current mode control, stepping down the 10V to 15V input supply voltage to a 4.5V to 6V LED forward bias voltage. The buck converter operating frequency is set by an external resistor to ground. The MODE pin is connected to GND to select the IC to operate in buck driver mode. The converter switches at 300kHz, which optimizes the device to provide very high efficiency with a small inductor size.
The design requires that the LED current rise/fall time is less than 1?s. To achieve this indicator, a very small output filter capacitor must be selected, which increases the load ripple current. In addition, if an inductor larger than the conventional value is selected, the inductor ripple current will remain within the load ripple current. The output end is limited to 10A/?s by a 1?F capacitor (C11) to prevent any overshoot caused by parasitic components.
The LED driver controls and maintains a 10A current through the inductor. According to the LED that needs to be driven at any moment, Q8, Q9 or Q10 is turned on respectively to switch the inductor current to the corresponding LED. When all three LEDs are turned off, the inductor current forms a local loop through Q4.
The MAX16821 device has two control loops: an inner loop that controls the inductor current and an outer loop that determines the inductor current required to drive the LED. In a step-down converter, the inductor current is the same as the LED current. Therefore, the control circuit is simplified to a single inductor current monitoring loop. In this design, R5 limits the current error amplifier gain to 11.5V/V to prevent subharmonic oscillations of the inductor current. The current loop compensation has no zero-pole pairs, which increases the low-frequency gain and allows the inductor current to be accurately stabilized at the value set by the voltage loop. The voltage error amplifier compares the LED current-sense voltage across R11||R17 with the internal 100mV reference and provides a 70dB error gain. The amplified output drives the inner current loop. Even with the lower gain of the inner current loop, the high gain of the voltage error amplifier can stabilize the LED current at 10A.
The inductor current switches between the local loop formed by the RGB LED and Q4, and the voltage error amplifier output requires 4 different levels. Because the output voltage under these 4 conditions is different, 4 levels are required. 4 different compensation capacitors (C7, C10, C13 and C14) are used to store the voltage error amplifier output, corresponding to 4 different load conditions. The compensation capacitors are connected to the circuit through analog switches (Q2, Q5, Q6 and Q7), and one is turned on at a time. Once the LED is turned on, the corresponding compensation capacitor immediately adjusts the error amplifier output to the last stored voltage, so that the LED current quickly rises to 10A.
The pole formed by the internal current loop absorption inductance and the output pole formed by the LED dynamic impedance and output capacitor C11 generate a pole frequency much higher than the switching frequency. The voltage loop has only one polarity, which is the pole of the voltage error amplifier. The compensation capacitors (C7, C10, C13 and C14) form a pole at the origin, making the voltage loop pass through 0dB in the 1/10 frequency range.
The MAX15025 dual-channel MOSFET driver (U2, U3) drives (Q2, Q5, Q6, and Q7) to quickly switch between LED loads with current slew rates up to 10A/1?s. The loss-reduction circuit formed by C9 and R10 slows down the switching edges at the LX node, helping to suppress any overshoot/undershoot ringing. If the output voltage exceeds *V, the overvoltage protection feedback provided by R3 and R4 will shut down U1. Once the output voltage drops below 5.4V, U1 resumes switching operation. Filter capacitor C1 prevents false triggering due to noise. The RC network provides a 3ms delay from the power-on edge, allowing U1 to start operating after the input power supply stabilizes.
Circuit waveform
Figure 4. Oscilloscope screenshot showing the current in one of the LEDs (CH3).
The voltage at the OUTV pin (CH1) represents the magnitude of the inductor current; the voltage at the CLP pin (CH2) represents the PWM duty cycle. The inductor current is the same throughout the cycle. The PWM duty cycle for the blue and green LEDs is almost the same, but smaller for the red LED. The LED current rises and stabilizes to its final value within 1?s.
Temperature measurement:
● VIN: 12V
● IOUT: 10A to RGB LED, 20% PWM per color
● Cooling: The circuit board is forced to cool by air
● Circuit board temperature: +53°C
● Q1, Q3 housing: +60°C
● Q4, Q8, Q9 and Q10 housing: +58°C
● U1 top: +53°C
● L1 coil temperature: +70°C
Power-on steps
● Connect 10A RGB LED to J5, J6 and J7.
● Keep PWMR, PWMG, PWMB and PWMN signals at low level.
● Gradually increase the power supply voltage to 10V and observe the current, which should be less than 0.3A.
● Apply PWM signals PWMR, PWMG and PWMB with a PWM duty cycle of 15% to 20% (position each PWM pulse so that only one PWM signal is high at the same time). The PWMN signal should be the digital OR of PWMR, PWMG and PWMB. All three LEDs are alternately driven with a 10A current at the set duty cycle.
Previous article:High Power LED Camera Flash Driver Architecture
Next article:Main parameters and applications of LED driver chip DD212
Recommended ReadingLatest update time:2024-11-16 17:42
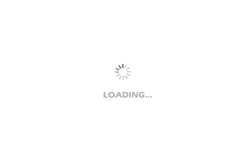
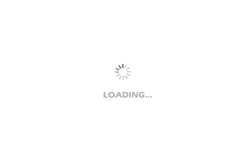
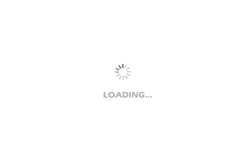
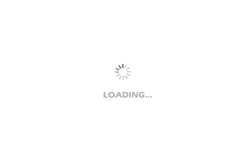
- MathWorks and NXP Collaborate to Launch Model-Based Design Toolbox for Battery Management Systems
- STMicroelectronics' advanced galvanically isolated gate driver STGAP3S provides flexible protection for IGBTs and SiC MOSFETs
- New diaphragm-free solid-state lithium battery technology is launched: the distance between the positive and negative electrodes is less than 0.000001 meters
- [“Source” Observe the Autumn Series] Application and testing of the next generation of semiconductor gallium oxide device photodetectors
- 采用自主设计封装,绝缘电阻显著提高!ROHM开发出更高电压xEV系统的SiC肖特基势垒二极管
- Will GaN replace SiC? PI's disruptive 1700V InnoMux2 is here to demonstrate
- From Isolation to the Third and a Half Generation: Understanding Naxinwei's Gate Driver IC in One Article
- The appeal of 48 V technology: importance, benefits and key factors in system-level applications
- Important breakthrough in recycling of used lithium-ion batteries
- Innolux's intelligent steer-by-wire solution makes cars smarter and safer
- 8051 MCU - Parity Check
- How to efficiently balance the sensitivity of tactile sensing interfaces
- What should I do if the servo motor shakes? What causes the servo motor to shake quickly?
- 【Brushless Motor】Analysis of three-phase BLDC motor and sharing of two popular development boards
- Midea Industrial Technology's subsidiaries Clou Electronics and Hekang New Energy jointly appeared at the Munich Battery Energy Storage Exhibition and Solar Energy Exhibition
- Guoxin Sichen | Application of ferroelectric memory PB85RS2MC in power battery management, with a capacity of 2M
- Analysis of common faults of frequency converter
- In a head-on competition with Qualcomm, what kind of cockpit products has Intel come up with?
- Dalian Rongke's all-vanadium liquid flow battery energy storage equipment industrialization project has entered the sprint stage before production
- Allegro MicroSystems Introduces Advanced Magnetic and Inductive Position Sensing Solutions at Electronica 2024
- Car key in the left hand, liveness detection radar in the right hand, UWB is imperative for cars!
- After a decade of rapid development, domestic CIS has entered the market
- Aegis Dagger Battery + Thor EM-i Super Hybrid, Geely New Energy has thrown out two "king bombs"
- A brief discussion on functional safety - fault, error, and failure
- In the smart car 2.0 cycle, these core industry chains are facing major opportunities!
- The United States and Japan are developing new batteries. CATL faces challenges? How should China's new energy battery industry respond?
- Murata launches high-precision 6-axis inertial sensor for automobiles
- Ford patents pre-charge alarm to help save costs and respond to emergencies
- New real-time microcontroller system from Texas Instruments enables smarter processing in automotive and industrial applications