In direct-type backlight sources, the arrangement of LEDs must compromise the effect of color mixing and heat dissipation, as shown in Figure 1. The denser the LED configuration, the better the RGB color mixing effect, but the LED heat dissipation performance will decrease; if the LEDs are arranged more sparsely, the RGB color mixing effect will be reduced, while the LED heat dissipation performance will be improved. Therefore, how to design an LED arrangement with good color mixing effect and an easy-to-implement heat dissipation design is a problem that needs to be considered in the LED arrangement design.
Figure 1: LED arrangement in direct-type backlight source
1. LED backlighting system
LEDs are becoming the mainstream device for backlighting applications of small and medium-sized color displays. The choice of LED is a key factor in determining the best price/performance ratio for display subsystem design. When designing portable LED driver circuits, cost and performance factors are generally considered. One constraint of the system design is the available battery power and voltage, and other constraints include functional characteristics, such as adjusting for ambient light and building the architecture of the LED.
LEDs can be screened based on different parameters, including forward voltage and chromaticity and brightness at a specific forward current. For example, the forward voltage of white light LEDs is usually 3.5~4V, and the typical operating current is 15~20mA. When multiple LEDs are used in a backlighting device, these LEDs are usually matched to produce uniform brightness. Therefore, the "differentially screened" or matched LEDs provided by LED manufacturers are matched in VF or other parameters within a certain voltage range. These VF differences are usually 3.5V~3.65V, 3.65~3.8V, and 3.8~4.0V, and the forward voltage of the latest LED products is 3V. LEDs with low VF values are suitable for small displays, while larger color displays usually require higher brightness and generally use medium or high VF value LEDs.
Generally speaking, the VF value of LED is an important parameter in system design. This is because portable products powered by ordinary batteries (such as mobile phones) use a single lithium-ion battery with a voltage range of 2.7~4.2V. If the system's battery operating voltage requirement is designed to be no less than 3V, the design can directly use a battery voltage as low as 3V and without voltage regulation to drive the LED.
When multiple LEDs are connected together, both the forward voltage and current must be matched so that the entire assembly can produce consistent brightness. The simplest way to achieve constant current is to connect LEDs in series that have been screened for forward voltage. The levels of difference in LED matching include luminous intensity and chromaticity, where chromaticity determines the color displayed and is mostly related to the semiconductor process used in the design. Electrical operating conditions have little effect on chromaticity. For luminous intensity, the screening process measures the luminous intensity at a given forward operating current.
Currently, there are driver ICs on the market that can drive multiple LEDs. Their functions include voltage boosting and driving multiple LEDs in series to match current with arrays containing one or more LEDs in each column. Specific driver ICs can provide precise current matching independent of the LED forward voltage VF, and use LED brightness control functions to help provide more functions and improve power management.
2. White LED backlight power supply solution
Recently, with the development of wireless communication products, colorful LCD displays have been gradually introduced into mobile phones and PDAs, and white LEDs provide a perfect backlight solution for such applications. However, since the typical voltage of a single lithium-ion battery is 3.6V and the maximum voltage is 4.2V, and the forward voltage of a white LED is typically 3.5V and the maximum is 4V at 20mA, a single lithium-ion battery cannot directly drive a white LED. Therefore, many mobile phone and PDA manufacturers have been looking for economical and efficient white LED boost backlight power supply solutions.
Figure 2 shows how to power three white LEDs using the MAX1848 DC/DC boost converter. The MAX1848 uses a constant current to drive two or three white LEDs, making it suitable for portable devices such as mobile phones and PDAs. The boost converter includes a high-voltage, low-on-resistance N-channel MOSFET switch to achieve high conversion efficiency and maximize battery life. The analog voltage dual-mode input provides a simple way to adjust the brightness and switch control. The input can also be controlled by inputting a PWM waveform and adding an RC filter. The 1.2MHz current-mode PWM control technology allows the use of very small input and output capacitors and small inductors outside the controller, and minimizes input voltage ripple. The programmable soft-start function eliminates input surge current during startup. The MAX1848 is available in a volume-saving SOT-23 package or an ultra-small UCSP package.
Figure 2: Using the MAX1848 to power three white LEDs
In the circuit shown in Figure 2, the MAX1848 requires a small inductor, a diode, a current-sense resistor, and three capacitors. The total cost of this solution is slightly higher than the MAX684 charge pump solution, but its conversion efficiency is much higher. When driving three series-connected white LEDs, the required output power is
POUT=3.1×3×15=139.5mW
The conversion efficiency of MAX1848 is
η=POUT/(POUT+PMAX1848+PVD1) (1)
Where: PMAX1848 is the power consumed by the MAX1848; POUT is the output power; PVD1 is the power consumed by the Schottky diode VD1.
The data listed in Table 1 are actual data measured using the MAX1848 evaluation board. As can be seen from Table 1, the efficiency of the solution using the MAX1848 is 15%~25% higher than that of the MAX684. The specific data is related to the input voltage.
Therefore, when the input voltage is 3.6V, the input power required by the MAX1848 solution is
PIN=9.32×15/0.8529≈164(mW)
When the input voltage is 4.2V, the input power required by the MAX1848 solution is
PIN=9.32×15/0.8539≈163.7(mW)
The MAX684 charge pump power supply solution requires fewer external components and is low in cost; while the MAX1848 inductive boost solution requires much lower input power, maximizing battery life. In the circuit shown in Figure 2, the LEDs are allowed to be connected in series, ensuring that all LEDs have the same current and brightness, while also eliminating the current-limiting resistor in the parallel structure. Another important feature of the MAX1848 is output overvoltage protection, which prevents the LED from being damaged due to accidental factors when the output voltage is too high when the LED is not connected. The MAX1848 solution is also suitable for other portable products using small color LCD displays.
3. Methods for controlling LED brightness
The display screen that puts red and green LEDs together as a pixel is called a two-color screen or a color screen; the display screen that puts red, green, and blue LEDs together as a pixel is called a three-color screen or a full-color screen. The pixel size of indoor LED screens is generally 2~10mm, and several LED tube cores that can produce different primary colors are often packaged into one; the pixel size of outdoor LED screens is mostly 12~26mm, and each pixel is composed of several various single-color LEDs. The common finished product is called a pixel tube. The two-color pixel tube is generally composed of three red and two green, and the three-color pixel tube is composed of two red, one green, and one blue.
Whether using LED to make a single-color, two-color or three-color screen, if you want to display an image, the brightness of each LED that constitutes the pixel must be adjustable, and the degree of fineness of the adjustment is the brightness level of the display. The higher the brightness level, the more delicate the displayed image, the richer the color, and the more complex the corresponding display control system. Generally, for an image with 256 levels of brightness, the color transition is very soft, while for a color image with 16 levels of brightness, the color transition boundary is very obvious. Therefore, color LED screens are currently required to be made with 256 levels of brightness. There are two ways to control LED brightness:
Change the current flowing through the LED. Generally, the current allowed for continuous operation of LEDs is around 20mA. Except for the red LED, which has saturation, the brightness of other LEDs is basically proportional to the current flowing through.
Taking advantage of the visual inertia of the human eye, the pulse width modulation method is used to achieve brightness control, that is, the pulse width (i.e., duty cycle) is changed periodically. As long as the repeated lighting cycle is short enough (i.e., the refresh frequency is high enough), the human eye cannot feel the jitter of the light-emitting pixel. Since pulse width modulation is more suitable for digital control, the display screen that uses a microcomputer to provide LED display content uses pulse width modulation to control the brightness level.
The control system of LED usually consists of three parts: main control box, scanning board and display control device. The main control box obtains the brightness data of various colors of pixels on a screen from the computer's display card, and then redistributes it to several scanning boards. Each scanning board is responsible for controlling several rows (columns) on the LED screen, and the display control signal of the LED on each row (column) is transmitted in serial. There are currently two ways to transmit display control signals in serial. One method is to centrally control the brightness of each pixel on the scanning board. The scanning board decomposes the brightness value of each row of pixels from the control box (i.e. pulse width modulation), and then transmits the opening signal of each row of LED in the form of pulses (1 for lighting and 0 for non-lighting) to the corresponding LED in serial mode by row to control whether it is lit. This method uses fewer devices, but the amount of serially transmitted data is larger, because in a repeated lighting cycle, each pixel requires 16 pulses at 16 levels of brightness and 256 pulses at 256 levels of brightness. Due to the limitation of the operating frequency of the device, the LED screen can generally only achieve 16 levels of brightness.
Another method is that the content of the serial transmission of the scanning board is not the switch signal of each LED but an 8-bit binary brightness value. Each LED has its own pulse width modulator to control the lighting time. In this way, in a repeated lighting cycle, each pixel only needs 4 pulses at 16 levels of brightness and only 8 pulses at 256 levels of brightness, which greatly reduces the serial transmission frequency. This method of decentralized control of LED brightness can easily achieve 256 levels of brightness control.
In any computing device, the requirements for the display are relatively strict. Small (2-4 inch) color TFT displays are more common in handheld devices, and the display power supply may consume most of the battery energy. The use of TFT displays requires a large part of the energy to be used for backlighting. Compared with CCFL and EL backlight sources, white LEDs are widely used in small TFT display backlighting due to their excellent efficiency and simple driving circuits. White LEDs have a high forward voltage (3.0-4.0V) and often require a boost circuit. The boost circuit uses a charge pump structure or an inductor-based design. The backlight efficiency is determined by how frequently the display works. Figure 3 shows two options. The inductor-based design provides the best conversion efficiency and can maintain constant LED brightness when the battery is about to run out; the charge pump device is lower in cost, but also lower in efficiency.
Figure 3 Two common white light LED driving solutions
4. Solutions to reduce column driver power consumption and improve performance
The clarity and refresh rate of flat panel displays are constantly improving, which makes the refresh rate of scan lines higher and higher. This requirement is in direct conflict with the requirement of system design to save system power as much as possible. National Semiconductor's proprietary intelligent charge sharing technology can not only reduce power consumption, but also improve the output performance of column drivers. If used in the correct way, intelligent charge sharing technology can reduce the power consumption of column drivers by up to 40% and shorten the output stabilization time.
How Intelligent Charge Sharing Technology Works
Smart Charge Sharing works by redistributing the energy stored in the scan lines of a thin-film transistor (TFT) liquid crystal display (LCD) and driving each scan line to half of its final value without consuming power. This technology works because half of the scan lines have a voltage higher than VCOM and the other half have a voltage lower than VCOM during each phase.
Figures 4 and 5 show the basic operation of the intelligent charge sharing technique. In this example, each scan line of the flat panel display can be considered to be approximately equal to the sum of the RC circuit loads on the output amplifier of the column driver. For the convenience of quantitative analysis, each scan line should be treated as a distributed load. Since it is only used to explain the working principle of charge sharing, it can be treated as an additive load.
Figure 4 Scan line voltage immediately before charge sharing
Figure 5 Voltage of scan lines when sharing charge
Figure 4 shows the situation immediately before charge sharing begins. The voltage of each alternate scan line is above and below VCOM. A series of switches are included in the column driver to short-circuit all the scan lines. Before charge sharing, all switches are open.
Figure 5 shows the situation when the charge is shared. The output amplifier has been put into standby mode (hi-Z mode) and the switches are all closed. The current flows from the scan line with a voltage higher than VCOM to the scan line with a voltage lower than VCOM in the direction shown by the arrow. When the charge is shared, the output amplifier does not consume power. Although the switch is turned on again, the voltage of each scan line is the same as VCOM. The output amplifier enters the traditional driving state at this moment. One thing to note is that the output only needs to drive the scan line from VCOM to the voltage of the last stage, rather than driving it from the beginning to the end of the entire voltage range.
Connected together in a short circuit, the scan line voltage is changing its polarity and ensuring that its polarity is opposite to VCOM. For an n-line inverter circuit, not every scan line switches voltage. Using intelligent charge sharing technology helps improve the efficiency of the charge sharing function.
Differences between Intelligent Charge Sharing Technology and Conventional Drivers
The output waveform of the column driver using the intelligent charge sharing technology is different from the output waveform of the traditional column driver in appearance. Figure 6 shows these two different output waveforms. For these two output waveforms, VHXX is the output voltage in the upper half (voltage higher than VCOM), and VLXX is the output voltage in the lower half (voltage lower than VCOM). The waveform shown in Figure 6 (a) is the output waveform of the traditional driver. No matter where in the voltage range, the conversion rate can still remain relatively stable. The waveform shown in Figure 6 (b) is the output waveform of the column driver using the intelligent charge sharing technology. The waveform of the intelligent charge sharing technology can be divided into two parts. The first part is the part when the charge is shared. The conversion rate of this part is always very fast, and then it stabilizes and matches the VCOM voltage. After the charge sharing is completed, the output amplifier enters the traditional driving mode, and its output waveform (the second part of the waveform) is very similar to the waveform of the traditional driver.
Figure 6 Driver output waveform
Smart charge sharing is fundamentally different from the energy-saving techniques commonly used in column drivers on the market today. Many column drivers on the market today have a low-power mode available. For most applications, this mode reduces the bias current flowing into the output amplifier to save energy. However, this always reduces the average conversion rate of the output. For small flat-panel displays with small loads and low resolution, this solution is quite good. However, once the conversion rate is slowed down, the performance will also be reduced. For the new generation of high-resolution, high-load flat-panel displays, this is far from meeting the requirements.
Intelligent charge sharing technology can not only save energy, but also improve the average conversion rate of flat panel displays at the same time, because the energy stored in each row of scanning lines can instantly provide a larger current, which is impossible for traditional amplifiers. Because National Semiconductor's column driver has this advantage, it can support a higher actual conversion rate on the one hand, and reduce power on the other hand.
Application of Intelligent Charge Sharing Technology of FPD33584 and FPD33620
In order to fully utilize the advantages of charge sharing technology, the length of the charge sharing time should be set according to the load size of the flat panel display. Even if a flat panel display with a smaller RC circuit load requires less shared charge, it can save more energy than a flat panel display with a larger RC circuit load. National Semiconductor has fully considered the length of the charge sharing time when designing the two column drivers FPD33584 and FPD33620, ensuring that the length of time can be controlled without adding external circuits or input pins.
For most flat panel display loads, National Semiconductor Corporation generally recommends that the charge sharing time be set at 500ns~1ms. For example, for a flat panel display with a load equivalent to 50kΩ and 150pF, due to the larger load, a longer charge sharing time may be required to save more power and achieve better performance.
When using FPD33584 and FPD33620, two methods can be used to control the length of the charge sharing time. The three pins CLK-SEL, TIME0 and TIME1 can be used to determine which control method to use. All pins can be disconnected within the TCP or COF package.
The first method is to control the charge sharing time by changing the pulse width of CLK1. This is the most ideal method for applications that require accurate control of the charge sharing time. In this configuration, the charge starts sharing at the rising edge of CLK1 and ends sharing at the falling edge of CLK1. When using this configuration, the potential of the CLK1-SEL pin must be pulled high using the TCP or COF connection. When using this configuration, the TIME0 and TIME1 pins should be in a floating state. Figure 7 shows the typical output waveform when the charge sharing time is controlled by the CLK1 pulse.
Figure 7 Using CLK1 pulse to control charge sharing time
The second method is to control the charge sharing time using a specified number of RSDSTM clock pulses. The control function can be activated by placing the CLK1-SEL pin in a floating state or connecting it to a lower potential to control the charge sharing time. The two pins TIME0 and TIME1 provide four different lengths of charge sharing time for selection. As shown in Table 2, different values of TIME0 and TIME1 have different charge sharing times. For most applications, National Semiconductor recommends that the value [TIME1, TIME0] = [1, 0] can also be used for flat-panel displays with smaller loads or applications with lower RSDSTM clock frequencies. 128 RSDSTM clock cycles can only be used for flat-panel displays with extremely large loads. In this configuration, charge sharing begins at the falling edge of CLK1 and continues for the RSDSTM clock cycles listed in Table 2. Figure 8 shows a typical output waveform, where tCS is the product of the number of clock cycles listed in Table 2 and the PWRSDS value.
Figure 8 Using clock cycles to control charge sharing time
When using intelligent charge sharing technology to share charge, the conversion rate is generally much faster than the displayed rate. National Semiconductor's proprietary intelligent charge sharing technology not only improves the performance of the column driver, but also helps reduce the overall power consumption of the system. In addition to achieving higher performance, this technology is also pin-compatible with many RSDS column drivers on the market.
Previous article:Advantages of LED light sources compared to incandescent lamps
Next article:Control technology of ultra-high brightness LED in lighting applications
Recommended ReadingLatest update time:2024-11-16 15:28
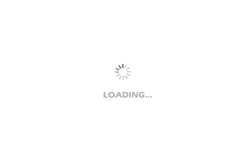
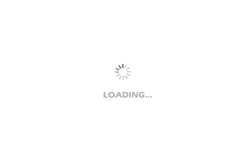
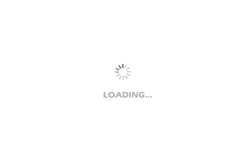
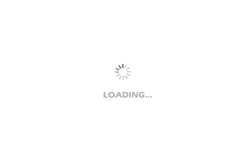
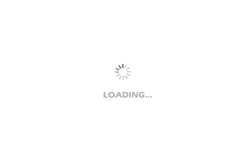
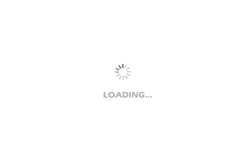
- Popular Resources
- Popular amplifiers
- MathWorks and NXP Collaborate to Launch Model-Based Design Toolbox for Battery Management Systems
- STMicroelectronics' advanced galvanically isolated gate driver STGAP3S provides flexible protection for IGBTs and SiC MOSFETs
- New diaphragm-free solid-state lithium battery technology is launched: the distance between the positive and negative electrodes is less than 0.000001 meters
- [“Source” Observe the Autumn Series] Application and testing of the next generation of semiconductor gallium oxide device photodetectors
- 采用自主设计封装,绝缘电阻显著提高!ROHM开发出更高电压xEV系统的SiC肖特基势垒二极管
- Will GaN replace SiC? PI's disruptive 1700V InnoMux2 is here to demonstrate
- From Isolation to the Third and a Half Generation: Understanding Naxinwei's Gate Driver IC in One Article
- The appeal of 48 V technology: importance, benefits and key factors in system-level applications
- Important breakthrough in recycling of used lithium-ion batteries
- Innolux's intelligent steer-by-wire solution makes cars smarter and safer
- 8051 MCU - Parity Check
- How to efficiently balance the sensitivity of tactile sensing interfaces
- What should I do if the servo motor shakes? What causes the servo motor to shake quickly?
- 【Brushless Motor】Analysis of three-phase BLDC motor and sharing of two popular development boards
- Midea Industrial Technology's subsidiaries Clou Electronics and Hekang New Energy jointly appeared at the Munich Battery Energy Storage Exhibition and Solar Energy Exhibition
- Guoxin Sichen | Application of ferroelectric memory PB85RS2MC in power battery management, with a capacity of 2M
- Analysis of common faults of frequency converter
- In a head-on competition with Qualcomm, what kind of cockpit products has Intel come up with?
- Dalian Rongke's all-vanadium liquid flow battery energy storage equipment industrialization project has entered the sprint stage before production
- Allegro MicroSystems Introduces Advanced Magnetic and Inductive Position Sensing Solutions at Electronica 2024
- Car key in the left hand, liveness detection radar in the right hand, UWB is imperative for cars!
- After a decade of rapid development, domestic CIS has entered the market
- Aegis Dagger Battery + Thor EM-i Super Hybrid, Geely New Energy has thrown out two "king bombs"
- A brief discussion on functional safety - fault, error, and failure
- In the smart car 2.0 cycle, these core industry chains are facing major opportunities!
- The United States and Japan are developing new batteries. CATL faces challenges? How should China's new energy battery industry respond?
- Murata launches high-precision 6-axis inertial sensor for automobiles
- Ford patents pre-charge alarm to help save costs and respond to emergencies
- New real-time microcontroller system from Texas Instruments enables smarter processing in automotive and industrial applications
- Recommended solutions to reduce Wi-Fi interference
- The MCU cannot run in DC-DC mode of BLUENRG-1
- Update the image
- Vote: Which of these TI star products do you like?
- Temperature detection [What is the device sensor you are most comfortable using]?
- ReSpeaker Core V2.0 builds Bluetooth speakers
- How to modify the default value of protel99sePCB toolbar?
- XMC4800 Relax ECAT Kit Review 3 - Testing the EtherCAT Slave
- TMS320VC5509A cannot connect to the emulator problem search and summary
- Let’s talk about digital filtering algorithms. Reply to get points!