Summary
In applications such as wireless transceivers, the system is often located in remote locations and is often battery powered. Since few people can visit the site to intervene, such applications must run continuously. After a period of continued inactivity or hang, the system needs to be reset to resume operation. To achieve a system reset, cut the supply voltage, disconnect power from the system, and then connect power again to restart the system.
This article will explore what methods and techniques can be used to monitor the active low output of a circuit to drive a high-side input switch to perform a system power cycle.
Introduction
To improve the reliability and robustness of electronic systems, one approach is to implement protection mechanisms that can detect faults and respond promptly. These mechanisms act like safety barriers, mitigating potential damage and ensuring the system operates properly. Power cycling ensures proper system operation and provides protection, often working when a system is unresponsive and inactive so that it can continue to function. Power cycling is accomplished with a power switch that opens and closes the path between the power input and the downstream electronic system to restart the system. Once the system's microcontroller unit (MCU) becomes unresponsive and continues to be inactive, the system enters reset mode and begins power cycling.
A more common method for implementing high-side power paths or input switches is to use MOSFETs. Either N-channel or P-channel MOSFETs can be used as input switches, each with different drive requirements. Driving an N-channel MOSFET as a high-side switch is a bit complicated, so a P-channel MOSFET is usually chosen.
Supervisory circuitry can easily detect when a system is inactive by monitoring the supply voltage and/or using a watchdog timer to detect the presence of pulses. The watchdog timer feature enhances the supervisory circuit's capabilities as a comprehensive protection solution. Once inactivity is detected, the watchdog timer asserts the reset output, which is typically an active-low signal. This signal can be used to place the microcontroller into reset mode or trigger a non-maskable interrupt, prompting the system to take corrective action. Although the active-low output is primarily used to reset the microcontroller, it is also necessary to perform a power cycle in situations such as when the system is unresponsive for an extended period of time. To this end, several techniques can be used to drive the high-side P-channel MOSFET input switch from the active low output of the supervisory circuit, resulting in better system reliability.
Use MOSFET as high side input switch
Figure 1 shows an application circuit that uses a high-side input switch to protect downstream electronic systems from power-down faults. MOSFETs enable easy selection of the appropriate voltage and current ratings based on application needs, making them ideal for high-end switching designs in systems.
Figure 1. Example of a high-side input switch implementation to protect the system from brownout faults
The high-side input switch can be an N-channel or P-channel MOSFET. When the gate voltage is low, the N-channel MOSFET switch opens and the supply voltage connection is disconnected. For an N-channel MOSFET to fully close and connect power to downstream electronic systems, the gate voltage must be higher than the supply voltage by at least equal to the MOSFET threshold voltage. Therefore, if an N-channel MOSFET is used as a high-side input switch, additional configuration circuitry, such as a charge pump, will be required. Some protection circuits also integrate comparators and charge pumps to drive high-side N-channel MOSFETs while keeping the solution simple. Using a P-channel MOSFET as the high-side input switch does not require a charge pump, but reverses the polarity. This method is simpler and therefore a common method for many applications.
Monitoring circuit output drives input switch
When using P-channel MOSFETs in a circuit, it is important to first establish proper bias conditions for the gate, source, and drain terminals. Gate-source voltage (VGS) plays a key role in controlling MOSFET conduction. For P-channel MOSFETs, the gate voltage must be lower than the source voltage, and the difference must be at least equal to the MOSFET threshold voltage. This negative bias ensures that the P-channel MOSFET is biased into its active region so that current can flow from source to drain. Additionally, the gate-source threshold voltage (VGS(th)) determines the minimum voltage required to establish a conductive path between the gate and source terminals. For P-channel MOSFETs, VGS(th) is usually specified as a negative value, indicating that the gate voltage needs to be low enough relative to the source to conduct. Another important consideration is the drain-source voltage (VDS), which is the voltage applied to the drain and source terminals. MOSFETs must operate within specified VDS limits to prevent damage to the device.
A voltage monitor or supervisory circuit can provide two options for its logic level output: active-low and active-high output signals. The former "active low level" means that when the input condition is true and is met, the output is set to low level; and when the input condition is false, the output is set to high level. The latter "active high" means that when the input condition is true, the output is set to high level; when the input condition is false and not met, the output is set to low level. Supervisory circuits are often used to reset microcontrollers, so an active-low output is used to pull the microcontroller's reset pin low during a fault. Driving a P-channel MOSFET with an active-high output is very simple, especially for an open-drain topology.
Figure 2. P-channel MOSFET is used as a high-side input switch to provide overvoltage protection.
The active-high output of the supervisory circuit is connected to the gate of the P-channel MOSFET. When the monitored voltage falls below the specified threshold, the OUT pin pulls the gate low, turning on the P-channel MOSFET. The load is therefore connected to the supply voltage. When the monitored voltage exceeds the threshold, the OUT pin goes high, the P-channel MOSFET turns off, and the load is disconnected from the supply voltage.
In Figure 2, the high-voltage adjustable timing control and monitoring circuit MAX16052 is used as an overvoltage protection circuit. The OUT pin of the device is connected directly to the gate of the P-channel MOSFET. The source of the P-channel MOSFET is connected to the input voltage and the drain is connected to the load. An external pull-up resistor is connected between VCC and the P-channel MOSFET gate to keep the gate high when the OUT pin is low.
When the monitored voltage falls below the fixed threshold specified by the MAX16052, the OUT pin pulls the gate pin low, causing the P-channel MOSFET switch to be in a short-circuit or conductive state. When the monitored voltage exceeds the threshold, the OUT pin goes high, the P-channel MOSFET turns off, and the load is disconnected from the supply voltage.
In some applications, the desired monitoring requirements may only apply to active-low outputs. This means that when the monitoring conditions are met, the output signal is low. In these cases, we must resort to techniques to control the input switches with active-low outputs. For example, if the microcontroller needs to be reset after 32 seconds of system inactivity and the system needs to enable a power cycle after 128 seconds of continuous inactivity, the watchdog timer's Watchdog Input (WDI) pin can be used to detect the inactivity. When no pulse or change is detected for a period of time (watchdog timeout period tWD), the watchdog output (WDO) goes low. The MAX16155 nanopower power supply monitor with watchdog timer is available in multiple models to meet the required watchdog timeout lengths of 32 s and 128 s. To achieve the required functionality, we need two watchdog timers, one to reset the microcontroller and another to initiate the power cycle routine shown in Figure 3. A major challenge was determining how to use the low-level outputs of different watchdog timer models to enable power cycling by opening the input switch during periods of inactivity or system unresponsiveness.
Figure 3. Using two MAX16155 watchdog timers with different watchdog timeouts, one for soft reset and one for power cycle.
NPN bipolar junction transistor used as driver circuit
One way to drive a P-channel high-side switch is to use an NPN bipolar junction transistor (BJT), as shown in Figure 4. This circuit forms an inverter that converts the active low signal from the watchdog output into the high logic signal required for P-channel MOSFET switching.
When the system is active, the watchdog output on the MAX16155 WDO pin is idle and usually high. This is then connected to the base pin of the driver transistor through a network of current limiting resistors. The normal high output of the WDO pin provides the necessary base-emitter voltage as the control input to the NPN bipolar junction transistor. It builds up enough voltage across the base-emitter junction to bring the transistor into a conducting state.
Resistor dividers are connected to the gate and source pins of the high-side MOSFET switch to control its gate-source voltage (VGS). This gate-to-source voltage determines whether the MOSFET remains on or off. When the WDO pin activates the NPN bipolar junction transistor, current flows through the transistor. This pulls the resistor divider down to GND, changing the voltage at the resistor divider junction. This voltage is then applied to the gate pin of the high side MOSFET. This creates a potential difference, with the gate pin having a lower potential than the source pin, causing the MOSFET to turn on. When the MOSFET is in the on state, power is provided to the system microprocessor or load. Figure 5 shows the current flow from the power supply through switch Q2 when the system is active.
Previous article:Dalian Daquanding Group launches 1KW DC/DC power module solution based on Innoscience products
Next article:STMicroelectronics smart actuator STSPIN reference design integrates motor control, sensors and edge AI
Recommended ReadingLatest update time:2024-11-16 09:35
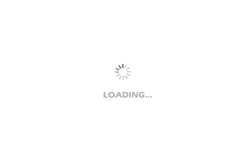
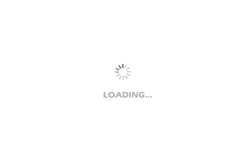
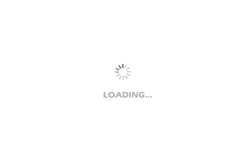
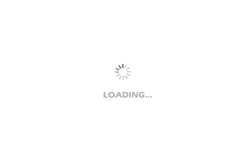
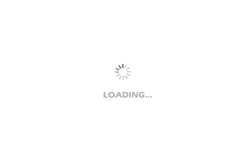
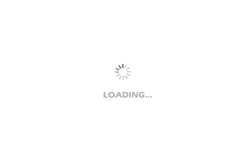
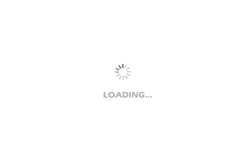
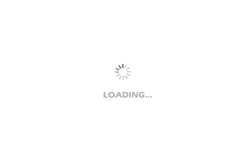
- Popular Resources
- Popular amplifiers
-
Siemens Motion Control Technology and Engineering Applications (Tongxue, edited by Wu Xiaojun)
-
Modern Product Design Guide
-
Modern arc welding power supply and its control
-
Small AC Servo Motor Control Circuit Design (by Masaru Ishijima; translated by Xue Liang and Zhu Jianjun, by Masaru Ishijima, Xue Liang, and Zhu Jianjun)
- MathWorks and NXP Collaborate to Launch Model-Based Design Toolbox for Battery Management Systems
- STMicroelectronics' advanced galvanically isolated gate driver STGAP3S provides flexible protection for IGBTs and SiC MOSFETs
- New diaphragm-free solid-state lithium battery technology is launched: the distance between the positive and negative electrodes is less than 0.000001 meters
- [“Source” Observe the Autumn Series] Application and testing of the next generation of semiconductor gallium oxide device photodetectors
- 采用自主设计封装,绝缘电阻显著提高!ROHM开发出更高电压xEV系统的SiC肖特基势垒二极管
- Will GaN replace SiC? PI's disruptive 1700V InnoMux2 is here to demonstrate
- From Isolation to the Third and a Half Generation: Understanding Naxinwei's Gate Driver IC in One Article
- The appeal of 48 V technology: importance, benefits and key factors in system-level applications
- Important breakthrough in recycling of used lithium-ion batteries
- Innolux's intelligent steer-by-wire solution makes cars smarter and safer
- 8051 MCU - Parity Check
- How to efficiently balance the sensitivity of tactile sensing interfaces
- What should I do if the servo motor shakes? What causes the servo motor to shake quickly?
- 【Brushless Motor】Analysis of three-phase BLDC motor and sharing of two popular development boards
- Midea Industrial Technology's subsidiaries Clou Electronics and Hekang New Energy jointly appeared at the Munich Battery Energy Storage Exhibition and Solar Energy Exhibition
- Guoxin Sichen | Application of ferroelectric memory PB85RS2MC in power battery management, with a capacity of 2M
- Analysis of common faults of frequency converter
- In a head-on competition with Qualcomm, what kind of cockpit products has Intel come up with?
- Dalian Rongke's all-vanadium liquid flow battery energy storage equipment industrialization project has entered the sprint stage before production
- Allegro MicroSystems Introduces Advanced Magnetic and Inductive Position Sensing Solutions at Electronica 2024
- Car key in the left hand, liveness detection radar in the right hand, UWB is imperative for cars!
- After a decade of rapid development, domestic CIS has entered the market
- Aegis Dagger Battery + Thor EM-i Super Hybrid, Geely New Energy has thrown out two "king bombs"
- A brief discussion on functional safety - fault, error, and failure
- In the smart car 2.0 cycle, these core industry chains are facing major opportunities!
- The United States and Japan are developing new batteries. CATL faces challenges? How should China's new energy battery industry respond?
- Murata launches high-precision 6-axis inertial sensor for automobiles
- Ford patents pre-charge alarm to help save costs and respond to emergencies
- New real-time microcontroller system from Texas Instruments enables smarter processing in automotive and industrial applications
- Altium Designer 18 Schematic
- I am designing a transformer for a flyback switching power supply. Is my estimate of the maximum duty cycle correct?
- Connected sports devices, desktop toys and medical wearables face new security challenges
- FAQ_ How to test the frequency deviation of low-speed clock in BlueNRG-X
- Start the Allwinner V853 platform GUI "Hello World!" journey in 5 minutes
- How to detect idle in input capture mode of STM32
- Design of DSP Embedded TCP/IP Network Communication System
- Is the chip industry about to change? Nvidia launches its first CPU, which achieves ten times the performance of x86
- Importance and necessity of wiring harness tester in new energy vehicle wiring harness production
- PADS9.5 usage help, cancel drilling frame format