introduction
In industrial applications such as test and measurement equipment or embedded computing, the system architecture of embedded DC-DC converters can be quite complex, with requirements on many different aspects such as output voltage and current, ripple, EMI, power-up sequencing, etc. This article focuses on the impact of converter power stage selection in DC-DC applications.
Requirements for Advanced Embedded DC-DC Converters
Many industrial systems, such as test and measurement equipment, require embedded DC-DC converters because the computing power required for these applications is increasing. This computing power is provided by DSPs, FPGAs, digital ASICs, and microcontrollers, which are constantly improving thanks to the shrinking process geometries. On the other hand, this also brings three major requirements: first, the supply voltage is getting lower and lower (of course, there is also the allowable voltage ripple and load variation); second, the supply current is gradually increasing; third, these ICs usually need to provide separate voltages for the core and I/O structure in an accurate sequence to avoid latch-up.
Embedded DC-DC converters must have excellent efficiency. The small space available for such converters makes thermal design particularly challenging, as embedded converters rely primarily on the copper area around the components on the PCB to improve the system thermal impedance. Since power dissipation is proportional to the square of the current, this situation worsens as the load current increases. Therefore, low on-resistance RDSON and low switching loss power switches are required. However, since the lower the on-resistance RDSON of the device, the higher the parasitic capacitance and therefore the switching losses, the higher the final power dissipation, so a certain trade-off must be made. Another major requirement for embedded DC-DC converters is that EMI must be low. The noise generated by these converters can interfere with surrounding circuits and must be as small as possible. However, high speed (to reduce switching losses) switching large currents (if required by the load) inevitably generates a lot of switching noise, including conducted noise and radiated noise (mainly magnetic fields). Therefore, special attention must be paid to the optimization of power stage component selection and layout, especially in terms of driver connections. In addition, the PWM control topology has a certain impact.
For example, a digital IC using 0.09μm technology may require a supply voltage of 1.2V ± 40mV. According to the data sheet of this DSP, its supply current can be as high as 952mA. Another example is a large-scale FPGA manufactured in 65nm process, which requires an idle supply current of 4.2A at 1.0V +/-50mV supply voltage and 85℃. In active mode, the current can increase to 18A, depending on the specific configuration, because the dynamic requirements are very high at high switching frequencies.
It is quite common for these applications to include multiple different ICs, for example, a smaller microcontroller (when the supply voltage is higher) to handle all the interface and host functions, with a larger DSP or dedicated hardware to perform the compute intensive functions. Many times, high-performance A/D converters with another set of voltage requirements are also used specifically to improve noise performance and really take advantage of the resolution and bandwidth of these converters. These trends have led to complex power management systems with many interdependencies.
Modular control lifting system design
One application recommendation is to place the DC-DC converter as close to the load as possible. This minimizes EMI, reduces the board space occupied by wide, high-current traces, and improves the converter's dynamic characteristics. This has led to the emergence of "distributed" power management systems in which all converters are ideally connected to each other. An example of a controller that can work in conjunction with other converters in a network is the FD2004, as shown in the block diagram of Figure 1.
FD2004 is a member of Digital-DC product family, integrating digital loop control and highly integrated power management functions. This controller and its peers can be connected to the host controller and other DC-DC converters through SMBus (System Management Bus), easily implementing many different functions, such as in-system configuration of converters, power-on sequence, margining, fault protection and system monitoring. All these functions help to shorten time to market and, more importantly, improve system reliability.
The FD2004 can work with an external gate driver (such as the FD1505) and discrete MOSFETs, or a single-package DrMOS product that integrates the driver and MOSFET. It can also be programmed by resistors in stand-alone applications—specifically, the maximum output voltage is set by resistors, and the maximum voltage set by software commands must not exceed 10% to protect the load. In applications that require higher currents, such as multi-phase converters, the selected architecture enables current sharing of up to 8 phases, and phase shedding can be achieved at low output power to maintain high efficiency. The controller is based on a digital control loop with adaptive performance algorithms and loop compensation, supporting switching frequencies up to 1.4MHz. Clock synchronization can help improve EMI performance. The FD2006 is also a good choice for applications that require both an integrated driver and a discrete external MOSFET.
Integrated DC-DC converters are recommended for system voltages with lower output currents, where PCB area and ease of use are the most important considerations. Digital converters, such as the FD2106 (6A max), have communication capabilities like other products in the Digital-DC family and can be used with discrete MOSFETs or converters based on DrMOS that can provide higher currents. For stand-alone applications, integrated converters (such as Fairchild Semiconductor's FAN2106) can also be used because they do not need to be connected to other converters in the system.
The controller and converter chain of the digital power management system can be controlled through a graphical user interface, which makes it easy to modify all parameters and monitor system performance. The software runs on a PC and is connected to the controller via a USB interface. When the parameters are all good, they are stored in the non-volatile memory of the controller, so that the PC is no longer required to run the system.
The DC-DC power stage shown in Figure 2 can be designed in different ways to achieve the best electrical and thermal performance at the same time.
1. Discrete solutions with drivers and MOSFETs are still commonly used. To meet all design requirements, Fairchild Semiconductor now offers products in small-size thermally enhanced MLP (QFN) packages to achieve high system performance. MOSFET was first packaged in MLP (see Figure 3). Its Power56 and Power33 product families use the latest PowerTrench technology, which can provide ultra-low RDSon and low Qg at the same time, making them suitable for high switching frequency applications. Bonding technology can reduce the inductance of the package and improve the limited ID of the package, making it suitable for high current applications. Its low-end FET product portfolio uses SyncFET with integrated Schottky diodes to achieve high switching performance while reducing heat dissipation.
The FDMS9600S integrates a high-side FET and a low-side SyncFET in an asymmetrical Power56 package, further improving thermal performance and enabling compact PCB designs with small footprints (Figure 4).
2. The above discrete solutions with drivers and MOSFETs are also available in MCM (multi-chip modules) in 8x8mm or 6x6mm MLP packages. These DrMOS (DriverMOS) product lines include 8x8mm products FDMD87xx and 6x6mm products FDMF67xx to meet different design requirements. The evaluation board can help designers become familiar with the application and test the performance for comparison with discrete solutions (Figure 5).
A discrete solution with Power56 MOSFETs and SO-8 drivers has a board footprint of around 120mm2, while an MCM requires only 64mm2 or 36mm2. The individual components in the latter module are carefully selected and fully optimized, resulting in higher performance and better thermal performance than discrete solutions (Figures 6 and 7). Driven by the computer industry, this solution can handle currents up to 30A and is optimized for switching frequencies up to 1MHz. Even in high-current designs, even with thermal design rules in mind, a heat sink is not required because the air flow in the system is sufficient to dissipate the heat of the chip.
3. The final fully integrated switch will make the power stage design faster and easier. In addition to the FD2106 in the Digital-DC series, the FAN210x TinyBuck series also provides fully integrated synchronous buck functions for 3A FAN2103 and 6A FAN2106 applications (Figure 8).
The entire IC is packaged in an MLP package measuring only 5x6mm, which helps in compactness of the design while achieving optimal thermal performance and high efficiency.
At first glance, higher integration may seem to result in higher bill of materials (BOM) costs, but considering all the advantages, such as space savings, better thermal performance, fewer passive components, etc., it actually reduces the final system cost. Such a fully integrated solution also supports high system reliability, because fewer components means less risk of failure, and lower system temperature is also very important considering thermal design rules.
Thermal design is a very important part of the design task. With today's MOSFETs, DrMOS or gate drivers, you can generally get a pretty good junction-to-case thermal impedance, but the thermal impedance from case to ambient depends on the design and is usually much higher. In most systems, using only the PCB, the thermal impedance (case to ambient) is around 40K/W, with the best designs being able to reach 25K/W. This is still much higher than the junction-to-case thermal impedance, which is typically 2K/W for MOSFETs. Therefore, the thermal design of the PCB is very important, because both thermal impedances are in series and affect the maximum temperature of the PCB, which is usually the limiting factor (if the junction-to-case thermal impedance is low, the junction temperature cannot be much higher than the PCB).
For higher currents, a multi-phase discrete solution (e.g., 2-3 DrMOS devices) is preferred to spread the heat over a larger surface. Another trade-off is switching frequency—if it is not predetermined by EMI requirements or space constraints (using higher switching frequencies to reduce the size of passive components), lower switching frequencies can help reduce switching losses and ultimately reduce temperatures.
As for layout, more metal obviously helps. A thicker top layer helps keep temperatures down, but may not be appropriate for the rest of the PCB because of the added cost and the impossibility of finer spacing required for other components. Larger copper areas are helpful but consume PCB space. These should be covered with solder whenever possible, as metal surfaces dissipate heat better than painted surfaces. In multi-layer PCBs, inner layers are sometimes used to assist with heat dissipation. Thermal vias (filled with solder) are sometimes used to spread heat to the other side of the PCB (Figure 9).
For forced air convection systems, care should be taken when placing components to avoid placing the converter in the "wind shadow" of other larger components. It is recommended to place the controller upstream of the MOSFET, which will not increase power consumption much and will operate more reliably at a lower case temperature.
summary
Modern embedded DC-DC converters benefit from many different technical solutions that can improve system performance and reliability and reduce costs. The interdependencies on the control side between stand-alone converters or interconnected digital converters, and on the power stage side between integrated or discrete solutions show that DC-DC converters operating in the network can be optimized and have the lowest power consumption.
Previous article:Research on dual-output dual-closed-loop current-controlled DC/DC converter
Next article:Design of high efficiency and ultra-wide input voltage range DC-DC converter
Recommended ReadingLatest update time:2024-11-16 16:21
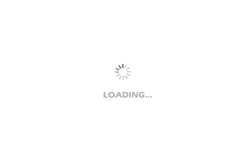
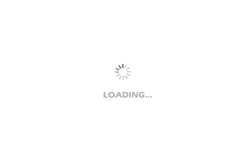
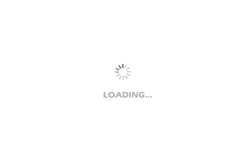
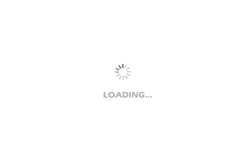
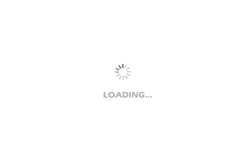
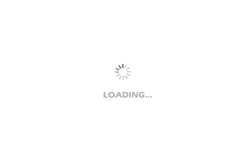
- Popular Resources
- Popular amplifiers
-
Study on the Behavioral Model of Silicon Carbide MOSFET Power Module and EMI Prediction of Low-Voltage Auxiliary Power Supply
-
Cable radiated EMI modeling considering mutual coupling effects_Junpeng Ji
-
Design of broadband hybrid active EMI filter for switching power supply_Liao Yuehong
-
Switching power supply conducted EMI simulation and filter circuit design_Jiang Yunfu
- MathWorks and NXP Collaborate to Launch Model-Based Design Toolbox for Battery Management Systems
- STMicroelectronics' advanced galvanically isolated gate driver STGAP3S provides flexible protection for IGBTs and SiC MOSFETs
- New diaphragm-free solid-state lithium battery technology is launched: the distance between the positive and negative electrodes is less than 0.000001 meters
- [“Source” Observe the Autumn Series] Application and testing of the next generation of semiconductor gallium oxide device photodetectors
- 采用自主设计封装,绝缘电阻显著提高!ROHM开发出更高电压xEV系统的SiC肖特基势垒二极管
- Will GaN replace SiC? PI's disruptive 1700V InnoMux2 is here to demonstrate
- From Isolation to the Third and a Half Generation: Understanding Naxinwei's Gate Driver IC in One Article
- The appeal of 48 V technology: importance, benefits and key factors in system-level applications
- Important breakthrough in recycling of used lithium-ion batteries
- Innolux's intelligent steer-by-wire solution makes cars smarter and safer
- 8051 MCU - Parity Check
- How to efficiently balance the sensitivity of tactile sensing interfaces
- What should I do if the servo motor shakes? What causes the servo motor to shake quickly?
- 【Brushless Motor】Analysis of three-phase BLDC motor and sharing of two popular development boards
- Midea Industrial Technology's subsidiaries Clou Electronics and Hekang New Energy jointly appeared at the Munich Battery Energy Storage Exhibition and Solar Energy Exhibition
- Guoxin Sichen | Application of ferroelectric memory PB85RS2MC in power battery management, with a capacity of 2M
- Analysis of common faults of frequency converter
- In a head-on competition with Qualcomm, what kind of cockpit products has Intel come up with?
- Dalian Rongke's all-vanadium liquid flow battery energy storage equipment industrialization project has entered the sprint stage before production
- Allegro MicroSystems Introduces Advanced Magnetic and Inductive Position Sensing Solutions at Electronica 2024
- Car key in the left hand, liveness detection radar in the right hand, UWB is imperative for cars!
- After a decade of rapid development, domestic CIS has entered the market
- Aegis Dagger Battery + Thor EM-i Super Hybrid, Geely New Energy has thrown out two "king bombs"
- A brief discussion on functional safety - fault, error, and failure
- In the smart car 2.0 cycle, these core industry chains are facing major opportunities!
- The United States and Japan are developing new batteries. CATL faces challenges? How should China's new energy battery industry respond?
- Murata launches high-precision 6-axis inertial sensor for automobiles
- Ford patents pre-charge alarm to help save costs and respond to emergencies
- New real-time microcontroller system from Texas Instruments enables smarter processing in automotive and industrial applications