1 Features and Pin Functions MAX6870/MAX6871 pdf,MAX6870/MAX6871 datasheet
1.1 Features
●6 (MAX6870) or 4 (MAX6871) programmable input voltage detectors:
1 high-voltage input (+1.25 V to +7.625 V or +2.5 V to +13.2 V thresholds); 1
bipolar voltage input (±1.25 V to ±7.625 V or ±2.5 V to ±15.25 V thresholds);
4 (MAX6870) or 2 (MAX6871) positive voltage inputs (+0.5 V to +3.05 V or +1 V to +5.5 V thresholds);
●4 general-purpose logic inputs;
●2 programmable watchdog timers;
●8 (MAX6870) or 5 (MAX6871) programmable outputs: active-high, active-low, open-drain, weak pullup, push-pull, charge pump with timing delays ranging from 25 μs to 1600 ms;
●10-bit internal ADC monitors input voltages, detectors, and two auxiliary inputs;
●State control and manual reset control;
●Internal 1.25 V reference or external reference input;
●4 KB internal user EEPROM;
●I2C/SMBus compatible serial programming/communication interface;
●±l% threshold accuracy.
1.2 Pin Function
The MAX6870/MAX6871 are available in a 32-pin thin QFN leadless package. The functions of the individual pins are shown in Table 1.
2 Internal structure and working principle
The MAX6870 and MAX6871 have six inputs. The circuit starts to work as long as the voltage at any one of the inputs IN3-IN6 exceeds the minimum operating voltage of 2.7 V, or the voltage on IN1 exceeds 4 V. There are two threshold levels to choose from for each of the six inputs. They can be set to either two undervoltage detection states or one overvoltage detection state and one undervoltage detection state (i.e., window detector). The threshold levels can be set via I2C and saved in the configuration EEPROM. The threshold level range for IN3-IN6 is 0.5 V to 5.5 V, and the step size can be 10 mV or 20 mV depending on the selected threshold level. IN1 can detect voltages up to 13.2 V, so it is directly used to detect 12 V (or slightly lower) system bus voltages.
The second input IN2 is used to detect another higher voltage or negative voltage.
The MAX6870 internal multiplexer switches the 6 detector inputs and 2 auxiliary inputs to a 10-bit ADC with 1% accuracy. The ADC then digitizes the 8 input voltages and writes them to the internal registers, which can be called up through the I2C interface. The 2 auxiliary inputs can be used to change the voltage values of the 2 additional inputs, such as the input voltage of the current sensing amplifier or the input voltage of the temperature sensor, to change the output state when the current or temperature is above a certain value.
The 6 detector inputs and 4 common inputs (GPI) determine the state of the 8 outputs by changing the connection settings of the programming logic array according to the programming of the internal EEPROM. Similarly, by mixing the inputs and outputs, some outputs can be controlled by other outputs of the device. The delay of each output can be set independently and saved in the EEPROM inside the circuit.
The output of the device can be set to an internal pull-up open-drain structure or an external pull-up open-drain structure, or it can be set to a push-pull structure, and the output terminal can be directly connected to any power supply voltage to be detected internally. All outputs can be set to either high level active or low level active. As mentioned above, the programmable logic array of the MAX6870 can be connected in many ways, and different combinations of inputs and outputs can be used to drive each output.
MAX6870 also has a charge pump inside, allowing OUT1~OUT4 to be directly connected to an external N-channel switch device without other power supplies. The device also has two watchdog timers, and the watchdog timeout and start delay can be set by yourself. The watchdog generates a long start delay after the reset operation, so that the system can initialize, upload memory data and perform routine software testing during this period.
The manual reset input allows manual control of all outputs while testing the circuit. The MAX6870 also has configuration registers and a configuration EEPROM. During the development phase, the system configuration is changed immediately by writing the data to be modified into the configuration registers. If the changes need to be saved, they can be written to the configuration EEPROM later. If the data from the configuration EEPROM needs to be loaded back in, the system can be restarted by soft or hard restart. During the startup process, the system downloads the data from the EEPROM into the configuration registers.
4 Applications of MAX6870 and MAX6871
The flexibility of the MAX6870/MAX6871 lies in its programmable internal registers, and the register contents depend on the contents of the EEPROM. After the system is powered on or soft-started, the configuration register information is downloaded from the EEPROM. Before powering up each input, the configuration signal should first be written to the EEPROM through the I2C master. The correct operation should be to quickly configure the registers using the write block protocol, then read the data to verify its correctness, and finally write the data to the EEPROM through the write word protocol. The register map address is shown in Figure 1. The 512-byte EEPROM from 8100h to 82ffh is available for users to save software or board information.
The typical application circuit of MAX6870 is shown in Figure 2. The outputs monitor 12 V, 5 V, 3.3 V, 2.5 V, and 0.7 V respectively. Outputs 1 and 4 drive n-channel switching devices. The internal reference voltage is used. The auxiliary input is used as temperature detection. It communicates with the microprocessor through the I2C bus to realize the reading and writing of the internal EEPROM.
In order to reduce the impact of interference, a 0.1 μF capacitor is used to bypass high-frequency noise between the monitoring voltage and ground, and a 1 μF capacitor is used to bypass between ABP, DBP and ground. ABP and DBP are internally generated voltages and should not be used to power external circuits.
Previous article:Application circuit of MAX1917 to realize 2.5V power output
Next article:Design of power grid current meter based on CS5460A chip
Recommended ReadingLatest update time:2024-11-16 22:48
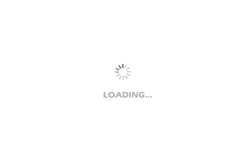
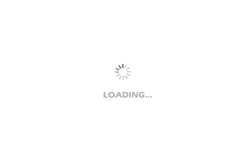
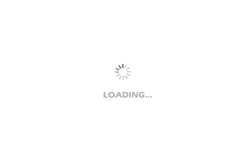
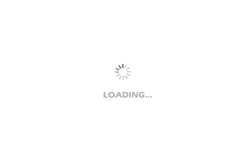
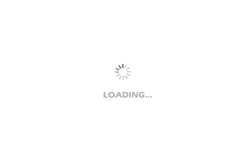
- Popular Resources
- Popular amplifiers
-
Microgrid Stability Analysis and Control Microgrid Modeling Stability Analysis and Control to Improve Power Distribution and Power Flow Control (
-
Modern Electronic Technology Training Course (Edited by Yao Youfeng)
-
New Energy Vehicle Control System Inspection and Maintenance (Edited by Bao Pili)
-
Intelligent Control Technology of Permanent Magnet Synchronous Motor (Written by Wang Jun)
- MathWorks and NXP Collaborate to Launch Model-Based Design Toolbox for Battery Management Systems
- STMicroelectronics' advanced galvanically isolated gate driver STGAP3S provides flexible protection for IGBTs and SiC MOSFETs
- New diaphragm-free solid-state lithium battery technology is launched: the distance between the positive and negative electrodes is less than 0.000001 meters
- [“Source” Observe the Autumn Series] Application and testing of the next generation of semiconductor gallium oxide device photodetectors
- 采用自主设计封装,绝缘电阻显著提高!ROHM开发出更高电压xEV系统的SiC肖特基势垒二极管
- Will GaN replace SiC? PI's disruptive 1700V InnoMux2 is here to demonstrate
- From Isolation to the Third and a Half Generation: Understanding Naxinwei's Gate Driver IC in One Article
- The appeal of 48 V technology: importance, benefits and key factors in system-level applications
- Important breakthrough in recycling of used lithium-ion batteries
- Innolux's intelligent steer-by-wire solution makes cars smarter and safer
- 8051 MCU - Parity Check
- How to efficiently balance the sensitivity of tactile sensing interfaces
- What should I do if the servo motor shakes? What causes the servo motor to shake quickly?
- 【Brushless Motor】Analysis of three-phase BLDC motor and sharing of two popular development boards
- Midea Industrial Technology's subsidiaries Clou Electronics and Hekang New Energy jointly appeared at the Munich Battery Energy Storage Exhibition and Solar Energy Exhibition
- Guoxin Sichen | Application of ferroelectric memory PB85RS2MC in power battery management, with a capacity of 2M
- Analysis of common faults of frequency converter
- In a head-on competition with Qualcomm, what kind of cockpit products has Intel come up with?
- Dalian Rongke's all-vanadium liquid flow battery energy storage equipment industrialization project has entered the sprint stage before production
- Allegro MicroSystems Introduces Advanced Magnetic and Inductive Position Sensing Solutions at Electronica 2024
- Car key in the left hand, liveness detection radar in the right hand, UWB is imperative for cars!
- After a decade of rapid development, domestic CIS has entered the market
- Aegis Dagger Battery + Thor EM-i Super Hybrid, Geely New Energy has thrown out two "king bombs"
- A brief discussion on functional safety - fault, error, and failure
- In the smart car 2.0 cycle, these core industry chains are facing major opportunities!
- The United States and Japan are developing new batteries. CATL faces challenges? How should China's new energy battery industry respond?
- Murata launches high-precision 6-axis inertial sensor for automobiles
- Ford patents pre-charge alarm to help save costs and respond to emergencies
- New real-time microcontroller system from Texas Instruments enables smarter processing in automotive and industrial applications
- Your evaluation information has been sent, please check it!
- The legendary Starlink
- EEWORLD University: How to use GaN to design reliable, high-density power solutions
- [Sipeed LicheeRV 86 Panel Review] Four Debian Python+Tk Calculators
- The relationship between LoraWAN, LPWAN and Lora
- Looking for PD Sink controller solution
- How to edit old posts?
- Failed to add serial port devices uart3-uart5 to the kernel
- EEWORLD University - Basic Knowledge of Welding
- micropython update: 2020.4