Digitizing these basic sensor elements requires specialized analog circuit design, digital circuit design, and firmware development techniques. The LTC2983 integrates these specialized techniques into a single IC, solving each of the unique challenges associated with thermocouples, RTDs, thermistors, and diodes. The device integrates the analog circuitry and temperature measurement algorithms and linearization data necessary for each type of sensor to directly measure each sensor and output the measurement results in °C.
Thermocouple Overview
The voltage produced by a thermocouple is a function of the temperature difference between the thermocouple tip (thermocouple temperature) and the electrical connection point on the circuit board (cold junction temperature). To determine the thermocouple temperature, the cold junction temperature needs to be accurately measured, a method known as cold junction compensation. The cold junction temperature is usually determined by a separate temperature sensor (not a thermocouple) placed at the cold junction. The LTC2983 allows diodes, RTDs, and thermistors to be used as cold junction sensors. To convert the voltage output from the thermocouple to temperature, a high-order polynomial (up to 14th order) must be solved (using a table or mathematical function) to obtain the measured voltage and cold junction temperature. The LTC2983 has built-in polynomials for all 8 standard thermocouples (J, K, N, T, R, S, T, and B), as well as user-set table data for custom thermocouples. The LTC2983 measures the thermocouple output and cold junction temperature simultaneously, performs all necessary calculations, and then reports the thermocouple temperature in °C.
Thermocouples: What's the big deal?
The output voltage produced by the thermocouple is low (< 100 mV at full scale). Due to the offset and noise of the ADC, the voltage value measured must be low. In addition, the voltage is an absolute voltage reading, which requires an accurate/low drift reference voltage. The LTC2983 contains a low noise, continuously offset calibrated 24-bit delta-sigma ADC (offset and noise < 1μV) and has a maximum reference of 10ppm/°C.
The output voltage of the thermocouple can also drop below ground when the thermocouple tip is exposed to an environment below the cold junction temperature. This complicates the system by forcing the addition of a second negative supply or input level shifting circuitry. The LTC2983 incorporates a proprietary front end that can digitize the signal using a single supply referenced to ground.
In addition to providing high measurement accuracy, thermocouple circuits must also employ noise rejection, input protection, and anti-aliasing filtering. The LTC2983 has a high input impedance and a maximum input current of less than 1nA. The device can use external protection resistors and filter capacitors without introducing additional errors. The LTC2983 includes a built-in digital filter and 75dB rejection of 50Hz and 60Hz.
Fault detection is an important function in many thermocouple measurement systems. The most common fault is an open circuit (thermocouple is damaged or not inserted). In the past, current sources or pull-up resistors were added to the thermocouple inputs to detect this type of fault. The problem with this approach is that these induced signals cause errors and noise and interact with the input protection circuit. The LTC2983 includes a unique open circuit detection circuit that checks if the thermocouple is damaged immediately before the measurement cycle begins. In this case, the open circuit excitation current/resistor does not interfere with the measurement accuracy. The LTC2983 also reports faults related to cold junction sensors. The device also detects, reports, and recovers from electrostatic discharge (ESD) events, which can occur when long sensor wires are used in industrial environments. The LTC2983 also indicates through its fault reporting whether the measured temperature is above/below the expected temperature range for a specific thermocouple.
Diode Overview
Diodes are inexpensive semiconductor devices that can be used as temperature sensors. These devices are typically used as cold junction sensors in thermocouples. When an excitation current is applied to a diode, the voltage produced by the diode is a function of the temperature and the applied current. If two perfectly matched excitation current sources of known ratio are applied to the diode, the output is a voltage that is known to be proportional to temperature (PTAT).
Diodes: What's the big deal?
To generate a PTAT voltage with a known ratio, two highly matched, proportional current sources are required. The LTC2983 relies on a delta-sigma oversampling architecture to accurately generate this ratio. The diodes and leads connected to the ADC contain unknown parasitic diode effects. The LTC2983 provides 3 current measurement modes to eliminate parasitic lead resistance. Different diode manufacturers specify different diode non-ideal coefficients. The LTC2983 allows the non-ideal coefficient of each diode to be set individually. Because absolute voltages are measured, the value and drift of the ADC reference voltage are critical. The LTC2983 contains a reference that is trimmed at the factory to a maximum of 10ppm/°C.
The LTC2983 automatically generates a proportional current, measures the resulting diode voltage, calculates the temperature using the programmed non-idealities and outputs the result in °C. The device can also be used as a cold junction sensor for thermocouples. If the diode is damaged, shorted or inserted incorrectly, the LTC2983 will detect this fault if the cold junction temperature is measured by the LTC2983 and report it in the conversion result output word as well as the corresponding thermocouple measurement.
RTD Overview
An RTD is a resistor whose resistance value changes with temperature. To measure an RTD, an accurately known low drift sense resistor is connected in series with the RTD. An excitation current is applied to the network and a ratiometric measurement is made. The resistance value of the RTD in ohms is determined from this ratio. This resistance value is then used to determine the temperature of the sensor element by looking up a table. The LTC2983 automatically generates the excitation current, measures the sense resistor and RTD voltage simultaneously, calculates the sensor resistance, and reports the result in °C. RTDs can measure temperature over a wide temperature range, from as low as 200°C to as high as 850°C. The LTC2983 can digitize most types of RTDs (PT-10, PT-50, PT-100, PT-200, PT-500, PT-1000, and NI-120), has built-in coefficients for many standards (U.S., European, Japanese, and ITS-90 standards), and provides user-defined table data for custom RTDs.
RTD: What is important?
The resistance value of a typical PT100 RTD changes less than 0.04Ω for every 1/10°C change in temperature, which corresponds to a 4μV signal level at 100μA current excitation. Low ADC offset and noise are critical for accurate measurements. The measurement is ratiometric with respect to the sense resistor, but the absolute values of the excitation current and reference voltage are not as important when calculating temperature.
Previously, ratiometric measurements between the RTD and sense resistor were performed with a single ADC. The voltage drop across the sense resistor was used as the reference input to the ADC that measured the voltage drop across the RTD. This architecture requires a sense resistor of 10 kΩ or greater, so buffering is required to prevent voltage drops caused by dynamic current at the ADC reference input. Since the value of the sense resistor is critical, the buffer must be low offset, low drift, and low noise. This architecture makes it difficult to cycle the current source to eliminate parasitic thermocouple effects. The reference input to the delta-sigma ADC is more susceptible to noise than the input, and low reference voltage values can cause instability. The multi-ADC architecture of the LTC2983 solves all of these problems (see Figure 1). The LTC2983 uses two highly matched, buffered, and auto-calibrated ADCs, one for the RTD and the other for the sense resistor. These ADCs simultaneously measure the RTD and Rsense, calculate the RTD resistance, and use this data to look up a ROM-based table to ultimately output the RTD temperature in °C.
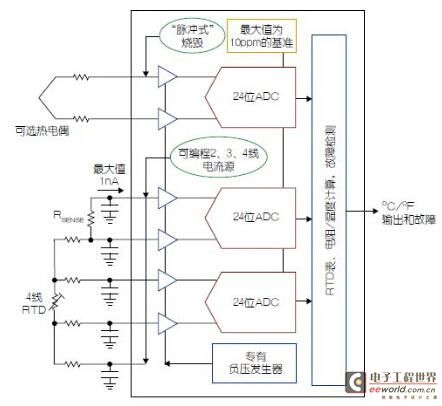
Figure 1. Measuring RTD temperature using LTC2983
RTDs are available in many configurations: 2-wire, 3-wire, and 4-wire. The LTC2983 offers all 3 configurations in a single, configurable hardware solution. The device can share a single sense resistor between multiple RTDs. Its high impedance input allows external protection circuits to be placed between the RTD and ADC inputs without introducing errors. The device can also automatically rotate current excitation to eliminate external thermal errors (parasitic thermocouples). In situations where parasitic lead resistance of the sense resistor degrades performance, the LTC2983 allows Kelvin sensing with Rsense.
The LTC2983 includes fault detection circuitry. The device can determine if the sense resistor or RTD is damaged or shorted. If the measured temperature is higher or lower than the maximum or minimum temperature specified for the RTD, the LTC2983 issues a warning. When the RTD is used as a cold junction sensor for a thermocouple, three ADCs measure the thermocouple, sense resistor, and RTD simultaneously. RTD fault information is passed to the thermocouple measurement, and the RTD temperature is automatically used to compensate for the cold junction temperature.
Thermistor Overview
Thermistors are resistors whose resistance value changes with temperature. Unlike RTDs, the resistance value of a thermistor can change by multiple orders of magnitude over its temperature range. To measure a thermistor, a sense resistor is connected in series with the sensor. An excitation current is applied to the network and a ratiometric measurement is performed. The resistance value of the thermistor is measured in ohms and can be determined from this ratio. This resistance value is used to determine the temperature of the sensor and solve the Steinhart-Hart equation or lookup table data. The LTC2983 automatically generates the excitation current, measures the sense resistor and thermistor voltages simultaneously, calculates the thermistor resistance, and reports the result in °C. Thermistors generally operate from -40°C to 150°C. The LTC2983 contains the coefficients required to calculate the temperature of standard thermistors of 2.252kΩ, 3kΩ, 5kΩ, 10kΩ, and 30kΩ. Because thermistors are available in a variety of types and resistance values, the LTC2983 can be programmed using custom thermistor table data (R and T) or Steinhart-Hart coefficients. Thermistors: What's Important?
The resistance of a thermistor can vary by many orders of magnitude over its temperature range. For example, a thermistor that is 10kΩ at room temperature may be as low as 100Ω at the highest temperature and >300kΩ at the lowest temperature, while other thermistor standards may reach over 1MΩ.
Typically, to accommodate large value resistors, very low excitation current sources and larger sense resistors are used. This results in very low signal levels at the low end of the thermistor resistance range. Input buffers and reference buffers are needed to isolate the ADC’s dynamic input current from these larger resistors. But buffers don’t work very well close to ground without separate supplies, and offset/noise errors need to be minimized. The LTC2983 solves all of these problems (see Figure 2). The device combines a continuously calibrated proprietary buffer that can digitize signals at or below ground with a multi-ADC architecture. Two matched buffered ADCs simultaneously measure the thermistor and sense resistor, calculate (based on a standard) the thermistor’s temperature, and report the result in °C. Large value sense resistors are not required, allowing multiple RTDs and different types of thermistors to share a single sense resistor. The LTC2983 also automatically sets different excitation current ranges depending on the thermistor output resistance.
Typically, to accommodate large value resistors, very low excitation current sources and larger sense resistors are used. This results in very low signal levels at the low end of the thermistor resistance range. Input buffers and reference buffers are needed to isolate the ADC’s dynamic input current from these larger resistors. But buffers don’t work very well close to ground without separate supplies, and offset/noise errors need to be minimized. The LTC2983 solves all of these problems (see Figure 2). The device combines a continuously calibrated proprietary buffer that can digitize signals at or below ground with a multi-ADC architecture. Two matched buffered ADCs simultaneously measure the thermistor and sense resistor, calculate (based on a standard) the thermistor’s temperature, and report the result in °C. Large value sense resistors are not required, allowing multiple RTDs and different types of thermistors to share a single sense resistor. The LTC2983 also automatically sets different excitation current ranges depending on the thermistor output resistance.
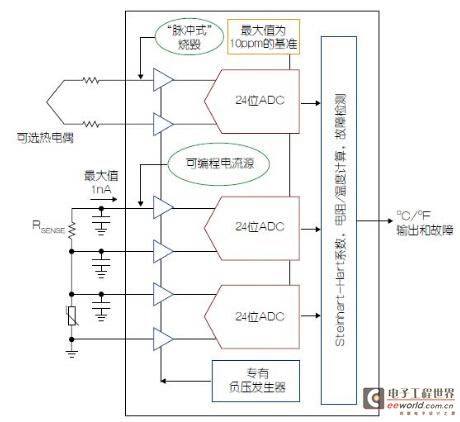
Figure 2 Measuring thermistor temperature using LTC2983
The LTC2983 includes fault detection circuitry. The device determines if the sense resistor or thermistor is damaged/shorted. If the measured temperature is above or below the maximum or minimum value specified for the thermistor, the LTC2983 issues an alarm. Thermistors can be used as cold junction sensors for thermocouples. In this case, 3 ADCs measure the thermocouple, sense resistor, and thermistor simultaneously. Thermistor fault information is passed to the thermocouple measurement, and the thermistor temperature is automatically used to compensate for the cold junction temperature.
Universal measuring system
The LTC2983 can be configured as a universal temperature measurement circuit (see Figure 3). Up to four sets of universal inputs can be added to a single LTC2983. Each set of inputs can be used directly to digitize a 3-wire RTD, 4-wire RTD, thermistor, or thermocouple without changing any built-in hardware. Each sensor can use the same four ADC inputs and protection/filtering circuits and can be configured by software. All four sets of sensors can share a sense resistor and measure cold junction compensation with a diode. The input structure of the LTC2983 allows any sensor to be connected to any channel. Any combination of RTDs, sense resistors, thermistors, thermocouples, diodes, and cold junction compensation can be added to any and all 21 analog inputs of the LTC2983.
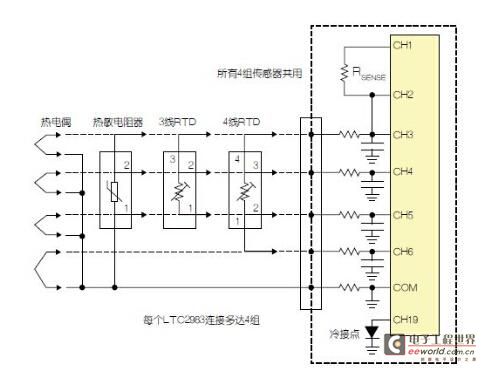
Figure 3 General temperature measurement system
in conclusion
The LTC2983 is a groundbreaking high-performance temperature measurement system. The device can directly digitize thermocouples, RTDs, thermistors, and diodes with laboratory-grade accuracy. The LTC2983 integrates three 24-bit delta-sigma ADCs and a proprietary front end to solve many typical problems associated with temperature measurement. High input impedance and zero input range allow direct digitization of all temperature sensors and easy input prediction. 20 flexible analog inputs enable the device to be reprogrammed through a simple SPI interface, so any sensor can be measured with the same hardware design. The LTC2983 automatically performs cold junction compensation, can measure cold junctions with any sensor, and provides fault reporting. The device can directly measure 2, 3, or 4-wire RTDs, and can easily share sense resistors to save cost, while easily rotating current sources to eliminate parasitic thermal effects. The LTC2983 can automatically set the current source range to improve accuracy and reduce noise associated with thermistor measurements. The LTC2983 allows the use of user-programmable custom sensors. Custom table-based RTDs, thermocouples and thermistors can be programmed into the device. The LTC2983 combines high accuracy, an easy-to-use sensor interface and high flexibility in a complete single-chip temperature measurement system.
Previous article:Design of a Class E power amplifier chip performance test circuit
Next article:Design Tips for 10W Wireless Power System
- Popular Resources
- Popular amplifiers
-
Virtualization Technology Practice Guide - High-efficiency and low-cost solutions for small and medium-sized enterprises (Wang Chunhai)
-
Improve Your Automotive ECU Design with a Low-IQ Buck Converter
-
Three-Phase 11 kW PFC + LLC Electric Vehicle On-Board Charging (OBC) Platform User Manual (ONSEMI Semiconductor)
-
CMOS Mixed Signal Circuit Design
- MathWorks and NXP Collaborate to Launch Model-Based Design Toolbox for Battery Management Systems
- STMicroelectronics' advanced galvanically isolated gate driver STGAP3S provides flexible protection for IGBTs and SiC MOSFETs
- New diaphragm-free solid-state lithium battery technology is launched: the distance between the positive and negative electrodes is less than 0.000001 meters
- [“Source” Observe the Autumn Series] Application and testing of the next generation of semiconductor gallium oxide device photodetectors
- 采用自主设计封装,绝缘电阻显著提高!ROHM开发出更高电压xEV系统的SiC肖特基势垒二极管
- Will GaN replace SiC? PI's disruptive 1700V InnoMux2 is here to demonstrate
- From Isolation to the Third and a Half Generation: Understanding Naxinwei's Gate Driver IC in One Article
- The appeal of 48 V technology: importance, benefits and key factors in system-level applications
- Important breakthrough in recycling of used lithium-ion batteries
- Innolux's intelligent steer-by-wire solution makes cars smarter and safer
- 8051 MCU - Parity Check
- How to efficiently balance the sensitivity of tactile sensing interfaces
- What should I do if the servo motor shakes? What causes the servo motor to shake quickly?
- 【Brushless Motor】Analysis of three-phase BLDC motor and sharing of two popular development boards
- Midea Industrial Technology's subsidiaries Clou Electronics and Hekang New Energy jointly appeared at the Munich Battery Energy Storage Exhibition and Solar Energy Exhibition
- Guoxin Sichen | Application of ferroelectric memory PB85RS2MC in power battery management, with a capacity of 2M
- Analysis of common faults of frequency converter
- In a head-on competition with Qualcomm, what kind of cockpit products has Intel come up with?
- Dalian Rongke's all-vanadium liquid flow battery energy storage equipment industrialization project has entered the sprint stage before production
- Allegro MicroSystems Introduces Advanced Magnetic and Inductive Position Sensing Solutions at Electronica 2024
- Car key in the left hand, liveness detection radar in the right hand, UWB is imperative for cars!
- After a decade of rapid development, domestic CIS has entered the market
- Aegis Dagger Battery + Thor EM-i Super Hybrid, Geely New Energy has thrown out two "king bombs"
- A brief discussion on functional safety - fault, error, and failure
- In the smart car 2.0 cycle, these core industry chains are facing major opportunities!
- The United States and Japan are developing new batteries. CATL faces challenges? How should China's new energy battery industry respond?
- Murata launches high-precision 6-axis inertial sensor for automobiles
- Ford patents pre-charge alarm to help save costs and respond to emergencies
- New real-time microcontroller system from Texas Instruments enables smarter processing in automotive and industrial applications
- An Engineer's Guide to EMI - Noise Propagation and Filtering
- Detailed explanation of Bluetooth GattCallback usage and BLE data transmission
- Why are most PCBs green? Are black PCBs more advanced?
- Zero-knowledge ESP8266 tutorial: SmartConfig one-click network configuration
- Op amp power supply
- EEWORLD University ----TI EV/HEV 48V and Motor Drive Solutions
- Can RTthread be ported to nrf51822?
- I want to control the on and off of NMOS through a 3.3V microcontroller
- Components Science Popularization: Pressure Sensor
- What wattage is this resistor?