In the medical device market, product features such as miniaturization, low power consumption and high fluid compatibility have become a global development trend. However, material specifications, product requirements and cost issues vary from country to country. This requires sensor manufacturers to provide a flexible and scalable product line to meet the needs of global customers. In addition, sensor manufacturers must ensure product quality and supply quality.
Miniaturization affects product size, portability and weight
Designers are facing a series of challenges to develop smaller, lighter and more portable medical devices to save space in wards and facilitate the use of medical staff. For example, traditional infusion pumps and insulin pumps are large in size. After design optimization, the emergence of portable and mobile devices has brought great benefits to patients and medical staff. For example, smaller sensors can be easily integrated into infusion pumps with limited space. Due to its small size and low power consumption, the portability of infusion pumps is further improved, which helps to improve the convenience of patients' lives. In addition, more and more patients choose "home treatment" instead of "hospitalization" - this trend is particularly common in the United States and EU countries. The transformation of treatment patterns has also promoted the trend of miniaturization of medical devices (including respiratory devices and diagnostic equipment).
In some cases, miniaturization will consider building some diagnostic functions into networked medical devices to remotely monitor patient treatment and care. Therefore, it is necessary to select sensor products that integrate multiple detection functions (such as humidity and temperature detection) in a single package. This move can create possibilities for medical device manufacturers to reduce the size of the device or increase the functionality of the device. Respiratory devices used for respiratory therapy (including ventilators and sleep apnea machines) benefit from this design.
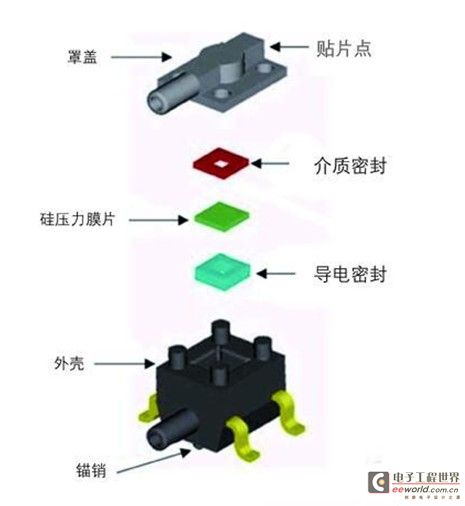
Figure 1: Modular design of Honeywell Sensing & Control’s TruStability board-mount pressure sensor
Another way for sensor manufacturers to meet the above requirements is to further develop sensor product lines that provide a variety of mechanical interfaces, mounting styles, packaging, and I/O options. In this way, medical device designers can choose the right interface to reduce space, reduce costs, and eliminate additional components. For example, pressure sensors should provide a variety of mounting options for installation in space-constrained applications, making it easier for designers to place the sensor in the right position for accurate detection. For applications that require precise measurement, the installation of the sensor is critical. For example, in dialysis treatment, the use of sensors to accurately measure the pressure of the dialysate and veins is directly related to the patient's life safety.
For portable applications, sensors need to meet the requirements of low voltage and low power consumption, which can extend the battery life. The sensor should also provide two modes: start/sleep mode, and the device will only consume power when in start mode. The sensor's sleep mode can extend the battery life, reduce the size of the power supply, and thus reduce the weight of the medical device.
Material/Specification Standards Impacting Global Manufacturers
For example, in the European Union, if there is even a little evidence that a material is harmful or dangerous, government regulators may list it as a prohibited material. Because EU countries have a well-developed medical insurance system and sufficient funds, their medical device market is very large. Therefore, global medical device manufacturers must ensure that their products meet EU standards before entering the EU market. Two regulations that affect the global electronics industry are the Directive on the Restriction of the Use of Certain Hazardous Substances in Electrical and Electronic Equipment (RoHS) and the Regulation on the Registration, Evaluation, Authorization and Restriction of Chemicals (REACH). The former aims to restrict six chemical substances previously used in the electronics manufacturing industry, while the latter provides the electronics industry with a framework for controlling the use of hazardous substances within the EU. RoHS and REACH affect the use of materials in end products and production processes. In order to sell products to EU countries, global manufacturers and distributors must comply with these regulations.
To ensure accurate measurement, the sensor must be as close to the fluid (blood, infectious substances, saline solution, etc.) as possible and frequently contact the patient's gas or liquid channels. Therefore, sensor manufacturers must ensure that the selected materials, supply chain and production process meet EU material specifications.
In addition, EU regulations also promote the use of RoHS-compliant liquid media compatible sensors in various medical devices (from chemical analyzers to ventilators). In order to help medical device manufacturers solve the "long-standing" problem of cost, sensor manufacturers must further develop product lines and provide a variety of output types, pressure types, pressure ranges, installation options and packaging types to meet the needs of EU countries.
The product platform should provide a variety of options and components to meet the specific needs of different countries, and should help medical device design engineers meet the pricing of products by manufacturers and distributors around the world. In addition, it should also allow engineers the flexibility to adjust the product according to the application and national requirements.
Figure 2: Honeywell HumidIcon digital temperature and humidity sensor integrates two functions in a single small package and can operate at a low voltage of 2.3Vdc
For example, the design of respiratory devices varies significantly from country to country, and the requirements for packaging types are also different. Flexible sensors should provide multiple packaging options, suitable for both integrated manifold designs in Western countries and traditional designs with multiple branches and interfaces common in developed countries.
Supplier quality assurance is key
Sensor manufacturers must not only comply with various material regulations and global electronic standards such as the US UL, Canadian cUL or CSA, European ENEC and Chinese CQC, but also develop a quality assurance system to ensure effective implementation of regulatory links and control of product quality.
The supplier's production process should comply with Six Sigma quality standards to ensure the production of high-quality products. Medical device products are related to the life safety of patients, and product quality is crucial to manufacturers.
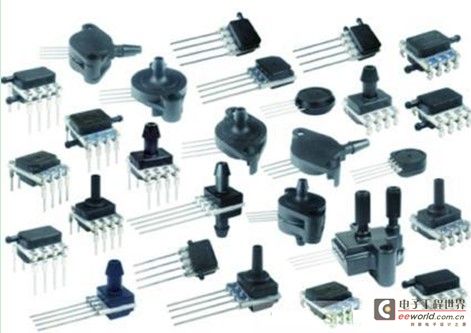
Figure 3: Honeywell's 20PC series of fluid-compatible pressure sensors offer a variety of pressure ranges, package types, and digital/analog outputs.
The reliability of suppliers is also important to designers. Sensor manufacturers should select suppliers worldwide to support product design and production needs. For example, when European designers develop new products, they usually outsource certain modules or components to electronic manufacturing services (EMS) companies around the world, and finally assemble them at European manufacturers.
Emerging Technology Trends
Medical device engineers also need suppliers to provide products that support emerging technology trends, such as digital interface options and disposable sensors. Sensor manufacturers provide digital interfaces (especially I2C output) for several reasons: With digital I2C output, designers can remove signal conditioning circuits on the printed circuit board (PCB), thereby saving board space and cost. In addition, digital I2C output can also reduce the number of copper wires and wires, further reducing costs. The reduction in parts helps the miniaturization of circuit boards.
Signal conditioning on the circuit board enables sensor compensation, calibration and amplification, thereby improving measurement accuracy and reliability. This helps improve the quality of care and patient comfort, and reduces the total cost of purchasing equipment in hospitals or clinics. Manufacturers of medical devices (from dialysis machines, infusion pumps to incubators and respiratory equipment) will benefit from this.
In order to save the cleaning work of the areas that come into direct contact with the liquid medicine or the patient's body fluids, more and more medical devices (such as infusion pumps) are using disposable sensors. Since the sensor plays a decisive role in the performance of medical devices, medical staff must consider the reliability of disposable sensors.
Cross-contamination is a major concern for single-use sensors if they are not replaced when they are needed. This is especially true when the sensors are used to treat HIV/AIDS, avian influenza, and Legionnaires’ disease, which can be transmitted through body fluids. Although medical device manufacturers recommend that single-use sensors be used on a single patient, some clinics do not follow this advice due to budget constraints and lack of regulation.
Previous article:Wireless Charging of Medical Devices
Next article:Complete broadband driver and receiver solution for video over UTP
- Popular Resources
- Popular amplifiers
- Bourns Launches Two Thick Film Resistor Series with High Power Dissipation Capabilities in Compact TO-220 and DPAK Package Designs
- Bourns Launches New High-Pulse Brake Resistor Series with Superior Energy Dissipation Capabilities
- Nexperia launches new 120 V/4 A half-bridge gate driver to further improve robustness and efficiency in industrial and automotive applications
- Vishay's New 150 V MOSFETs Offer Industry-Leading Power Loss Performance
- The first generation of SGT MOSFET series from Qiangmao: innovative trench technology, automotive-grade 60 VN channel, breakthrough in high-efficiency performance of automotive electronics
- DC/DC Power Supplies for Automotive Applications
- MathWorks and NXP Collaborate to Launch Model-Based Design Toolbox for Battery Management Systems
- STMicroelectronics' advanced galvanically isolated gate driver STGAP3S provides flexible protection for IGBTs and SiC MOSFETs
- New diaphragm-free solid-state lithium battery technology is launched: the distance between the positive and negative electrodes is less than 0.000001 meters
- Europe's three largest chip giants re-examine their supply chains
- Breaking through the intelligent competition, Changan Automobile opens the "God's perspective"
- The world's first fully digital chassis, looking forward to the debut of the U7 PHEV and EV versions
- Design of automotive LIN communication simulator based on Renesas MCU
- When will solid-state batteries become popular?
- Adding solid-state batteries, CATL wants to continue to be the "King of Ning"
- The agency predicts that my country's public electric vehicle charging piles will reach 3.6 million this year, accounting for nearly 70% of the world
- U.S. senators urge NHTSA to issue new vehicle safety rules
- Giants step up investment, accelerating the application of solid-state batteries
- Guangzhou Auto Show: End-to-end competition accelerates, autonomous driving fully impacts luxury...
- How to read optical encoding information via DSP2812 SPI
- Communication System Simulation Using Ansoft Serenade
- The four major sins of malware
- I would like to ask, the output waveform of the power amplifier is more than 180 degrees out of phase with the input waveform. What is going on?
- Let's take a look at the cheap lithium battery charging circuit made by foreigners!
- AD+FPGA+asynchronous FIFO+CMI+SPI code
- Using FSMC bus for inter-chip communication
- PADS9.5 graphic tutorial
- Silkscreen
- I'm a newbie. I don't understand. I'm asking for help on the problem I encountered when making a spi receiving module in Verilog.