1 Introduction
Motors are commonly used in industrial production processes, and motor failures often bring serious consequences and losses. The stator winding is the main component of the three-phase asynchronous motor, and it is also the part of the motor that is most easily damaged and causes failures. During the production process of the asynchronous motor, due to the mistakes of the production workers, the stator winding may be reversed, making it difficult to start the motor, and the three-phase current is seriously unbalanced and the current rises sharply. The current in the winding group with the reversed components is larger, and the motor makes abnormal noises and vibrates violently. If the power is not turned off and the machine is not stopped in time, the motor speed will drop, and the stator winding of the machine will soon burn out. In order to avoid greater losses, timely detection is required.
In actual applications, existing detection methods often require the motor to be removed during production applications, or the winding error can only be discovered when the motor fails. The detection method mainly involves removing the motor stator after the motor fails, connecting it to a DC power supply, and using a magnetic needle to determine whether there is reverse winding embedding.
The effect of the magnetic needle test method is also limited, requiring a large voltage and a magnetic needle with strong magnetism. In actual application and production, the effectiveness and timeliness of the test are poor, which greatly reduces efficiency.
This study uses the principle that when a permanent magnet rotates at an appropriate speed for more than one revolution at the rotor position, a corresponding voltage signal will be induced on the stator winding, and uses a detection device combining chips and circuits to replace the original manual detection method. The accuracy and feasibility of the proposed comprehensive detection method are proved through experimental research.
2. Design of reverse-embed winding detection device
When the permanent magnet rotates more than one circle at the rotor position of the asynchronous motor, a corresponding voltage signal will be induced on the stator winding. If the permanent magnet is narrow enough, it can be considered that it only cuts one coil edge each time it rotates. When the measured phase winding is not reversed, the two opposite coil edges cut by the permanent magnet will induce electric potentials of the same magnitude and opposite direction, which cancel each other out, making the output voltage of this phase close to 0; when there is a winding reverse embedding in the phase winding, electric potentials of the same magnitude and direction will be induced on the two opposite coils, and the electric potentials are superimposed on each other, making the output voltage of this phase have peaks and valleys. It is easy to find from theoretical analysis that if there is winding reverse embedding, the peak and valley values appear regularly, which is also reflected in the actual waveform detection. Therefore, the position of the reverse embedded winding can be further specified.
Due to the uneven air gap when the permanent magnet rotates in the asynchronous motor, the output induced voltage will have strong fluctuations, that is, sharp pulses, which will seriously affect the accuracy of the microcontroller voltage reading, so filtering is necessary. A low-pass filter is needed. In order to improve the performance, a Butterworth second-order low-pass filter is used to filter out high-order pulses.
But at the same time, the amplitude of the output induced voltage is attenuated. In order to obtain a voltage amplitude that is conducive to identification, the voltage needs to be amplified. Since the input voltage of the microcontroller can only be positive, the voltage signal needs to be biased. Combining the two, the voltage signal is biased and amplified, and an inverting proportional amplifier with bias is used.
Due to the advantages of the STM32 single-chip computer system that can quickly detect and process signals and is inexpensive, the parameters are first set according to the asynchronous motor model, and then the DAC port outputs the signal that drives the asynchronous motor to rotate one circle through the stepper motor driver. At the same time, the ADC cyclically inputs the acquisition and detection, and generates a judgment on whether there is an anti-embedded winding based on the signal input, and makes corresponding operation outputs. The asynchronous motor is controlled by the stepper motor driver. If there is an anti-embedded winding, it points to the position of the anti-embedded winding within one circle. If there is no anti-embedded winding, the asynchronous motor rotates another circle based on the original rotation, and the stm32 marquee indicates it.
3. Example verification
Before using the STM32 microcontroller in the device to read the filtered voltage signal, adjust the amplifier and bias potentiometer so that the microcontroller can read the peak and valley values of the voltage signal and perform AD conversion. Calculate and analyze based on the peak and valley values combined with the direction of the permanent magnet. First, rotate the permanent magnet for one circle. If the difference between the peak and valley values of the voltage signal read by the ADC is outside a range, there is winding reverse embedding in the motor, and further control the stepper motor to rotate to the reverse embedding winding position; if the difference between the peak and valley values is within a range, there is no winding reverse embedding in the motor, and the device flashes the indicator light to explain.
In the actual measurement of this project, the number of motor poles is 4, the number of coils per phase is 4, the rated power of the asynchronous motor is 200-500W, the PWM wave frequency controlled by the single-chip microcomputer is 1.6kHz, and the asynchronous motor needs 400 pulses to rotate one circle, so the frequency of the induced voltage is 4Hz.
Figure 2 is an example detection diagram, Figure 2-1 is the forward connection diagram of the winding, and Figure 2-2 is the reverse connection diagram of the winding, where max_a and min_a are the locations of the maximum and minimum values.
It can be seen from actual measurements that when there is a reverse-embedded winding, the difference between the maximum and minimum values is only 2000, while when there is no reverse-embedded winding, the difference is only 5. This can be used to distinguish them and further find the location of the reverse-embedded winding.
4 Conclusion
This research device uses STM32 as the development platform, applies modern signal processing technology to motor detection, uses a detection device combined with chips and circuits to replace the original manual detection method, and provides an asynchronous motor winding reverse embedding detection device based on STM32. This research device uses the principle that the permanent magnet will induce a corresponding voltage signal on the stator winding when it rotates at an appropriate speed for one or more cycles at the rotor position. On the premise of maintaining the integrity of the original motor stator and rotor, it can quickly detect whether the motor has reverse embedding of windings, and can clearly indicate the results, and can quickly point out the reverse-embedded windings. It has a fast response speed, accurate detection, and can intuitively reflect the faults of the motor, which brings great convenience to the control and detection of the motor.
Previous article:MOSFET selection strategy explained
Next article:ESD Solutions for NFC Antennas
Recommended ReadingLatest update time:2024-11-16 14:58
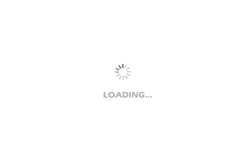
- Popular Resources
- Popular amplifiers
- MathWorks and NXP Collaborate to Launch Model-Based Design Toolbox for Battery Management Systems
- STMicroelectronics' advanced galvanically isolated gate driver STGAP3S provides flexible protection for IGBTs and SiC MOSFETs
- New diaphragm-free solid-state lithium battery technology is launched: the distance between the positive and negative electrodes is less than 0.000001 meters
- [“Source” Observe the Autumn Series] Application and testing of the next generation of semiconductor gallium oxide device photodetectors
- 采用自主设计封装,绝缘电阻显著提高!ROHM开发出更高电压xEV系统的SiC肖特基势垒二极管
- Will GaN replace SiC? PI's disruptive 1700V InnoMux2 is here to demonstrate
- From Isolation to the Third and a Half Generation: Understanding Naxinwei's Gate Driver IC in One Article
- The appeal of 48 V technology: importance, benefits and key factors in system-level applications
- Important breakthrough in recycling of used lithium-ion batteries
- Innolux's intelligent steer-by-wire solution makes cars smarter and safer
- 8051 MCU - Parity Check
- How to efficiently balance the sensitivity of tactile sensing interfaces
- What should I do if the servo motor shakes? What causes the servo motor to shake quickly?
- 【Brushless Motor】Analysis of three-phase BLDC motor and sharing of two popular development boards
- Midea Industrial Technology's subsidiaries Clou Electronics and Hekang New Energy jointly appeared at the Munich Battery Energy Storage Exhibition and Solar Energy Exhibition
- Guoxin Sichen | Application of ferroelectric memory PB85RS2MC in power battery management, with a capacity of 2M
- Analysis of common faults of frequency converter
- In a head-on competition with Qualcomm, what kind of cockpit products has Intel come up with?
- Dalian Rongke's all-vanadium liquid flow battery energy storage equipment industrialization project has entered the sprint stage before production
- Allegro MicroSystems Introduces Advanced Magnetic and Inductive Position Sensing Solutions at Electronica 2024
- Car key in the left hand, liveness detection radar in the right hand, UWB is imperative for cars!
- After a decade of rapid development, domestic CIS has entered the market
- Aegis Dagger Battery + Thor EM-i Super Hybrid, Geely New Energy has thrown out two "king bombs"
- A brief discussion on functional safety - fault, error, and failure
- In the smart car 2.0 cycle, these core industry chains are facing major opportunities!
- The United States and Japan are developing new batteries. CATL faces challenges? How should China's new energy battery industry respond?
- Murata launches high-precision 6-axis inertial sensor for automobiles
- Ford patents pre-charge alarm to help save costs and respond to emergencies
- New real-time microcontroller system from Texas Instruments enables smarter processing in automotive and industrial applications
- .DSN file is garbled when opened.
- Live Q&A Summary: ADI MEMS Sensors Open a New Era of Conditional State Monitoring
- Security Technology System of Wireless WLAN
- It is found that the OPAMP of STM32G474 cannot be internally connected to ADC4
- In-depth understanding of C language function parameters as pointers
- EEWORLD University Hall ---- The first stop of the ADI Road theme tour of Shijian: Industrial Automation
- AD20 Installation Issues
- Are there any commonly used solutions recommended for converting 0-10V to PWM?
- Looking for C8051F58x/F59x IDE?
- 9. [Learning LPC1768 library functions] Clkout experiment