With the continuous evolution of LED materials and packaging technology, the brightness of LED products has continued to increase, and the application of LED has become more and more extensive. Using LED as a backlight source for displays has become a hot topic recently. This is mainly because different types of LED backlight technology have more advantages than traditional cold cathode fluorescent lamps (CCFL) in terms of color, brightness, life, power consumption and environmental protection, thus attracting industry players to actively invest.
The original single-chip LED had low power, limited heat generation, and little heat problem, so its packaging method was relatively simple. However, with the continuous breakthroughs in LED material technology in recent years, LED packaging technology has also changed, from the early single-chip cannonball-shaped packaging to a flat, large-area multi-chip packaging module; its operating current has evolved from the early low-power LED of about 20mA to the current high-power LED of about 1/3 to 1A, and the input power of a single LED is as high as 1W or more, and even to 3W and 5W. The packaging method has evolved.
Since the heat issues derived from high-brightness and high-power LED systems will be the key to the quality of product functions, in order to quickly discharge the heat generated by LED components to the surrounding environment, we must first start with the thermal management of the packaging level (L1 & L2). The current industry practice is to connect the LED chip to a heat spreader with solder or thermal paste, and reduce the thermal impedance of the packaging module through the heat spreader. This is also the most common LED packaging module on the market, and the main sources are internationally renowned LED manufacturers such as Lumileds, OSRAM, Cree and Nicha.
Many terminal application products, such as mini projectors, automotive and lighting sources, require more than a thousand or tens of thousands of lumens in a specific area. Single-chip packaging modules alone are obviously not enough to cope with this. Moving towards multi-chip LED packaging and direct chip bonding to substrates is the future development trend.
Heat dissipation is the main obstacle in the development of LEDs for lighting purposes. Using ceramics or heat pipes is an effective way to prevent overheating, but heat management solutions increase the cost of materials. The purpose of high-power LED heat management design is to effectively reduce the thermal resistance between chip heat dissipation and the final product. R junction-to-case is one of the solutions using materials that provide low thermal resistance but high conductivity, and heat is directly transferred from the chip to the outside of the package shell through chip attachment or thermal metal methods.
Of course, the heat dissipation components of LED are similar to those of CPU, which are mainly air-cooled modules composed of heat sinks, heat pipes, fans and thermal interface materials. Of course, water cooling is also a heat countermeasure. For the most popular large-size LED TV backlight modules, the input power of 40-inch and 46-inch LED backlight sources is 470W and 550W respectively. If 80% of it is converted into heat, the required heat dissipation is about 360W and 440W.
So how to take away the heat? Currently, the industry uses water cooling, but there are concerns about high unit price and reliability. There are also heat pipes combined with heat sinks and fans for cooling, such as the 46-inch LED backlight LCD TV from Japanese giant Sony, but problems such as fan power consumption and noise still exist. Therefore, how to design a fanless heat dissipation method may be the key to determining who will win in the future.
Here we will introduce several heat dissipation methods and materials.
Cooling method
Generally speaking, according to the way of taking away heat from the radiator, the radiator can be divided into active cooling and passive cooling. The so-called passive cooling refers to the natural dissipation of heat from the heat source LED light source into the air through the heat sink. The heat dissipation effect is proportional to the size of the heat sink, but because it is a natural heat dissipation, the effect is of course greatly reduced. It is often used in devices that do not require space, or for cooling components that do not generate much heat. For example, some popular motherboards also use passive cooling on the north bridge. Most of them use active cooling. Active cooling is to forcibly take away the heat generated by the heat sink through cooling devices such as fans. Its characteristics are high heat dissipation efficiency and small device size.
Active cooling can be divided into air cooling, liquid cooling, heat pipe cooling, semiconductor cooling, chemical cooling, etc. based on the cooling method.
Air cooling is the most common way of cooling, and it is also a relatively cheap way. Air cooling is essentially the use of a fan to remove the heat absorbed by the radiator. It has the advantages of relatively low price and easy installation. However, it is highly dependent on the environment. For example, its cooling performance will be greatly affected when the temperature rises or when overclocking. Liquid cooling
Liquid cooling is a method of removing heat from the radiator by forced circulation of liquid driven by a pump. Compared with air cooling, it has the advantages of being quiet, stable in cooling, and less dependent on the environment. The price of liquid cooling is relatively high, and the installation is relatively troublesome. At the same time, try to install it according to the instructions in the manual to achieve the best heat dissipation effect. For cost and ease of use considerations, liquid cooling usually uses water as the heat transfer liquid, so liquid cooling radiators are often also called water-cooled radiators.
Heat pipe
Heat pipe is a kind of heat transfer element, which makes full use of the principle of heat conduction and the rapid heat transfer property of the refrigerant, and transfers heat by evaporation and condensation of liquid in a fully enclosed vacuum tube. It has a series of advantages such as extremely high thermal conductivity, good isothermal property, arbitrary change of heat transfer area on both sides of the hot and cold sides, long-distance heat transfer, and temperature control. In addition, the heat exchanger composed of heat pipe has the advantages of high heat transfer efficiency, compact structure, and low fluid resistance. Its thermal conductivity has far exceeded that of any known metal.
Semiconductor Refrigeration
Semiconductor refrigeration is the use of a special semiconductor refrigeration sheet to generate a temperature difference when powered on to cool down. As long as the heat at the high temperature end can be effectively dissipated, the low temperature end will be continuously cooled. A temperature difference is generated on each semiconductor particle. A refrigeration sheet is composed of dozens of such particles in series, thus forming a temperature difference on the two surfaces of the refrigeration sheet. By using this temperature difference phenomenon and combining air cooling/water cooling to cool down the high temperature end, an excellent heat dissipation effect can be obtained. Semiconductor refrigeration has the advantages of low cooling temperature and high reliability. The cold surface temperature can reach below -10°C, but the cost is too high, and it may cause a short circuit due to the low temperature. In addition, the technology of semiconductor refrigeration sheets is not mature and not practical enough.
Chemical Refrigeration
The so-called chemical refrigeration is to use some ultra-low temperature chemicals to absorb a lot of heat when they melt to lower the temperature. In this regard, the use of dry ice and liquid nitrogen is more common. For example, the use of dry ice can reduce the temperature to below -20℃, and some more "abnormal" players use liquid nitrogen to reduce the CPU temperature to below -100℃ (theoretically). Of course, due to the high price and short duration, this method is mostly used in laboratories or extreme overclocking enthusiasts.
Material selection
Thermal conductivity (unit: W/mK)
Silver 429
Copper 401
Gold 317
Aluminum 237
Iron 80
Lead 34.8
1070 Aluminum Alloy 226
1050 aluminum alloy 209
6063 Aluminum Alloy 201
6061 Aluminum Alloy 155
Generally speaking, ordinary air-cooled radiators naturally choose metal as the material of the radiator. For the selected material, it is hoped that it has both high specific heat and high thermal conductivity. As can be seen from the above, silver and copper are the best thermal conductive materials, followed by gold and aluminum. However, gold and silver are too expensive, so the heat sink is currently mainly made of aluminum and copper. In comparison, copper and aluminum alloy both have their own advantages and disadvantages: copper has good thermal conductivity, but it is more expensive, more difficult to process, too heavy, and the copper radiator has a small heat capacity and is easy to oxidize. On the other hand, pure aluminum is too soft and cannot be used directly. Aluminum alloys are used to provide sufficient hardness. The advantages of aluminum alloys are low price and light weight, but the thermal conductivity is much worse than copper. Therefore, in the history of the development of radiators, the following materials have also appeared:
Pure aluminum radiator
Pure aluminum radiators were the most common radiators in the early days. They have a simple manufacturing process and low cost. So far, pure aluminum radiators still occupy a considerable part of the market. In order to increase the heat dissipation area of its fins, the most commonly used processing method for pure aluminum radiators is aluminum extrusion technology, and the main indicators for evaluating a pure aluminum radiator are the thickness of the radiator base and the Pin-Fin ratio. Pin refers to the height of the fins of the heat sink, and Fin refers to the distance between two adjacent fins. The Pin-Fin ratio is the height of the Pin (excluding the thickness of the base) divided by the Fin. The larger the Pin-Fin ratio, the larger the effective heat dissipation area of the radiator, which means the more advanced the aluminum extrusion technology. Pure copper radiator
The thermal conductivity of copper is 1.69 times that of aluminum, so under the premise of other conditions being the same, pure copper radiators can take heat away from the heat source faster. However, the texture of copper is a problem. Many "pure copper radiators" are not actually 100% copper. In the list of copper, copper content of more than 99% is called acid-free copper, and the next level of copper is red copper with a copper content of less than 85%. At present, the copper content of most pure copper radiators on the market is between the two. Some inferior pure copper radiators contain less than 85% copper. Although the cost is very low, their thermal conductivity is greatly reduced, affecting the heat dissipation. In addition, copper also has obvious disadvantages. The high cost, difficult processing, and the large mass of the radiator have hindered the application of all-copper heat sinks. The hardness of red copper is not as good as that of aluminum alloy AL6063, and the performance of some mechanical processing (such as grooving, etc.) is not as good as that of aluminum; the melting point of copper is much higher than that of aluminum, which is not conducive to extrusion (Extrusion) and other problems.
Copper-aluminum bonding technology
After considering the shortcomings of copper and aluminum, some high-end heat sinks on the market often use a copper-aluminum combination manufacturing process. These heat sinks usually use a copper metal base, while the heat sink fins use aluminum alloy. Of course, in addition to the copper base, there are also heat sinks that use copper columns and other methods, which are also based on the same principle. With a higher thermal conductivity, the copper bottom surface can quickly absorb the heat released by the CPU; the aluminum fins can be made into the shape that is most conducive to heat dissipation with the help of complex process methods, and provide a larger heat storage space and release it quickly. This has found a balance point in all aspects.
Previous article:Four rules for mastering LED design
Next article:How much do you know about the special terms for LED driver power supply for lighting?
Recommended ReadingLatest update time:2024-11-16 14:43
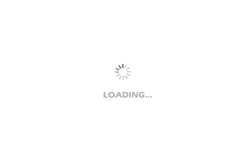
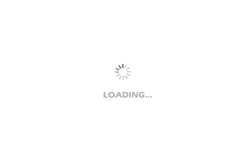
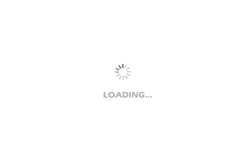
- Popular Resources
- Popular amplifiers
- MathWorks and NXP Collaborate to Launch Model-Based Design Toolbox for Battery Management Systems
- STMicroelectronics' advanced galvanically isolated gate driver STGAP3S provides flexible protection for IGBTs and SiC MOSFETs
- New diaphragm-free solid-state lithium battery technology is launched: the distance between the positive and negative electrodes is less than 0.000001 meters
- [“Source” Observe the Autumn Series] Application and testing of the next generation of semiconductor gallium oxide device photodetectors
- 采用自主设计封装,绝缘电阻显著提高!ROHM开发出更高电压xEV系统的SiC肖特基势垒二极管
- Will GaN replace SiC? PI's disruptive 1700V InnoMux2 is here to demonstrate
- From Isolation to the Third and a Half Generation: Understanding Naxinwei's Gate Driver IC in One Article
- The appeal of 48 V technology: importance, benefits and key factors in system-level applications
- Important breakthrough in recycling of used lithium-ion batteries
- Innolux's intelligent steer-by-wire solution makes cars smarter and safer
- 8051 MCU - Parity Check
- How to efficiently balance the sensitivity of tactile sensing interfaces
- What should I do if the servo motor shakes? What causes the servo motor to shake quickly?
- 【Brushless Motor】Analysis of three-phase BLDC motor and sharing of two popular development boards
- Midea Industrial Technology's subsidiaries Clou Electronics and Hekang New Energy jointly appeared at the Munich Battery Energy Storage Exhibition and Solar Energy Exhibition
- Guoxin Sichen | Application of ferroelectric memory PB85RS2MC in power battery management, with a capacity of 2M
- Analysis of common faults of frequency converter
- In a head-on competition with Qualcomm, what kind of cockpit products has Intel come up with?
- Dalian Rongke's all-vanadium liquid flow battery energy storage equipment industrialization project has entered the sprint stage before production
- Allegro MicroSystems Introduces Advanced Magnetic and Inductive Position Sensing Solutions at Electronica 2024
- Car key in the left hand, liveness detection radar in the right hand, UWB is imperative for cars!
- After a decade of rapid development, domestic CIS has entered the market
- Aegis Dagger Battery + Thor EM-i Super Hybrid, Geely New Energy has thrown out two "king bombs"
- A brief discussion on functional safety - fault, error, and failure
- In the smart car 2.0 cycle, these core industry chains are facing major opportunities!
- The United States and Japan are developing new batteries. CATL faces challenges? How should China's new energy battery industry respond?
- Murata launches high-precision 6-axis inertial sensor for automobiles
- Ford patents pre-charge alarm to help save costs and respond to emergencies
- New real-time microcontroller system from Texas Instruments enables smarter processing in automotive and industrial applications
- A simple pull-up and pull-down circuit causes the control chip to heat up!
- I would like some advice on how to import .brd files into DXP
- [RT-Thread reading notes] Part 2: Implementing multithreading
- VGA Display Circle - Simple Design and Application FPGA
- [NXP Rapid IoT Review] Rapid IoT Studio Simple Programming Step 2 Counter plus Bluetooth
- What does this PCB package marking mean?
- Problems found during PCB rule checking
- Study and use of DSP6678 chip
- Simple and fast design of LC filter
- 【ST NUCLEO-G071RB Review】TIM-PWM