As a rising star in the lighting field, LED lighting has a promising market prospect in the next five years and shows a strong growth momentum. According to the development trend of LED lighting prices continuously decreasing and performance continuously improving, the comprehensive cost of the entire life cycle of most LED lamps will be significantly lower than that of traditional lamps in the next 1-2 years, and they will become the mainstream lighting source.
As the shell of LED lamps , aluminum alloy and ceramic materials are traditionally used. However, in the past two years, a new material, thermal conductive plastic, has emerged and has been gradually accepted by the majority of manufacturers, becoming a highly anticipated shell material.
In summary, thermal conductive plastics have the following advantages:
1. Insulation and flame retardant, high safety.
2. Lightweight, density is about two-thirds of aluminum.
3. Easy to process and shape, good mass production.
4. No need for secondary processing, more environmentally friendly.
Faced with numerous thermal conductive plastic suppliers, how to more reasonably select cost-effective products, the following are some key points worth paying attention to:
1. Considerations for narrowing the screening scope
1. RoHS and UL certification of thermal conductive plastics
Whether or not a lamp factory has RoHS and UL certification is a critical factor for exporting to the European and North American markets. The issuing agency of RoHS and UL certificates actually does a preliminary screening of the materials. For many manufacturers, if they are not familiar with new materials such as thermal conductive plastics, they can learn more about thermal conductive plastics through the certification of the testing agency. It is worth noting that the UL certification number can be queried online, and its authenticity is relatively reliable.
2. Processing equipment required for materials
Thermal conductive plastics are divided into thermoplastic and thermosetting materials. Most thermal conductive plastics are thermoplastic raw materials. Such materials can be produced by traditional ordinary injection molding machines. If the original manufacturer of energy-saving lamps has a large number of injection molding machines, they can continue to use them. Another common practice is to outsource the injection molding process to a professional injection molding company. When the company's own production capacity is insufficient, it can easily expand production capacity through outsourcing factories.
On the contrary, if the thermal conductive plastic is a thermosetting material like phenolic resin, ordinary injection molding machines cannot be used, and special thermosetting plastic injection molding machines must be used. The additional equipment costs will greatly increase the cost. Moreover, once the own injection molding capacity is insufficient, it is difficult to find a suitable outsourced injection molding factory.
From a practical point of view, the molding cycle of thermoplastic materials is shorter than that of thermosetting materials, which also means that the processing cost will be reduced.
3. Color of the material
Usually, thermal conductive plastics are synthesized by adding additives to a certain base material (such as PC, PPS, PA). These thermal conductive additives are usually dark-colored materials, while the final customer demand is usually mainly white. If qualified white raw materials cannot be provided, it may lead to an additional painting process after injection molding, thereby increasing cost expenditure.
4. Production location of raw materials
For current LED whole lamp export orders, delivery time is an important clause. If the thermal conductive plastic is produced domestically, there should be enough time for delivery. If the origin is overseas, it is usually necessary to consider sea transportation and customs clearance import links, and the delivery time will be extended. At the same time, the sales cost of imported raw materials will also be higher than that of domestic production.
2. Comparison of material properties
1. Thermal conductivity
As a key technical indicator, thermal conductivity is the most concerned by users for materials from various manufacturers. However, the technical standards for testing thermal conductivity are different, including ASTM E 1530, ASTM E1461, and standards defined by certain companies, etc. Even under the same technical standards, the testing methods are different, such as the flat plate method and the laser method. Under different testing methods, the error range of the final test results is completely different. Generally, the accuracy of the laser method is higher than that of the flat plate method, and the equipment involved in the laser method is basically imported and expensive.
It is precisely because of the above reasons that users may be misled by only looking at the thermal conductivity. A more realistic approach is to use the same mold to injection mold thermal conductive plastics from different manufacturers, and then assemble the same lamp board and power supply. After power is turned on, test the pin temperature of the lamp bead or the temperature of the aluminum substrate close to the pin. The lower the temperature, the better the heat dissipation material.
Another approach is that thermally conductive plastic suppliers usually provide standard public mold products, and the heat dissipation effect of the public mold can be compared with heat sinks of the same specifications and dimensions (such as A19 bulbs) to roughly judge the performance of the material.
2. Material fluidity
It is usually expressed by melt index. Thermally conductive materials with good fluidity are easier to mold and produce more smoothly. Based on thermally conductive plastics with high fluidity, the wall thickness of the radiator can be designed to be relatively thin, usually 1-1.2mm. The thin wall thickness will shorten the heat dissipation path, thereby improving the heat dissipation effect. At the same time, the thinner wall thickness will reduce the weight of the material and reduce the material cost. If the material is poor in fluidity, it is usually not easy to injection mold, and it will easily damage the mold, increasing the mold maintenance cost.
3. Molding shrinkage
Generally, under the condition of 3mm thickness, the qualified molding shrinkage should be below 0.5%. If it is greater than 0.8%, it will have an adverse effect on the dimensional accuracy of the radiator. The molding shrinkage should be as small as possible. If a material with a higher molding shrinkage is selected, the wall thickness will have to be increased to compensate.
4. Mechanical properties
The mechanical strength of the thermal conductive plastic heat sink depends on several key indicators: cantilever beam notch impact strength, tensile strength, bending strength, usually the indicators of different materials can be compared, the larger the indicator value, the better. Thermal conductive plastics with excellent mechanical properties can add a snap-on design to the heat sink structure, so that the interface between the PC cover or lens and the heat sink is realized by snap-on, thus avoiding complete reliance on adhesive for fixing. The problem with adhesive is that it takes time to cure, which prolongs the delivery time, and the glue is easy to atomize at high temperature, affecting the light output effect.
5. Flame retardant properties
There are two key points. First, whether it meets the UL94 V0 flame retardant rating, which is critical for exporting to the US market. Second, whether it is halogen-free flame retardant. Simply put, the flame retardant should not contain halogen, otherwise the environmental protection level of the material will be reduced, and it will be difficult to pass the European RoHS and REACH directives.
6. Insulation properties
One benefit of thermally conductive plastics is insulation safety. If the molded heat dissipation housing can withstand a high voltage of more than 3500V, it should be easy to pass the safety test. To match such an insulating housing, the light board and power supply solutions that can be selected can be more flexible, including: high-voltage linear lamp beads + high-voltage linear power supply, non-isolated power supply + medium-power lamp beads. For specific parameters, please refer to the dielectric strength.
7. Thermal Expansion Coefficient
If a plastic-coated aluminum structure is used in the radiator structure, the difference in expansion coefficients between the outer layer of thermally conductive plastic and the inner layer of aluminum alloy should be considered. The thermal expansion coefficient of aluminum alloy is: 0.000024 mm/mm*k, and the expansion coefficient of thermally conductive plastic should be at the same order of magnitude, otherwise it will cause asynchronous thermal expansion and contraction, resulting in cracking of the radiator shell.
3. Price
As a category of plastics, thermal conductive plastics first follow the rule of quantity-based pricing. At the same time, it should be noted that the factors affecting the price are also closely related to the material density. Materials with lower density actually reduce unit costs. In addition, whether the rod part of the injection molding can be crushed and reused for injection molding actually has a certain impact on the price.
IV. Value-added Services
As a supplier of thermal conductive materials, whether we can provide customers with thermal simulation testing services will provide a reference for judging whether the customized heat sink of the customer has qualified heat dissipation. This will avoid modifying the mold after the mold is completed and finding that the heat dissipation is unreasonable, and thus avoid the risk of blind mold opening.
Previous article:Research on light distribution and heat dissipation technology based on high-power LED lamps
Next article:LED aluminum substrate professional knowledge introduction
Recommended ReadingLatest update time:2024-11-16 17:58
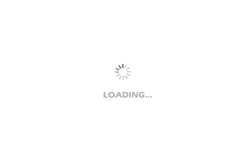
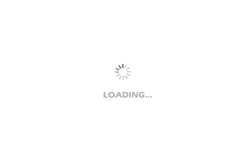
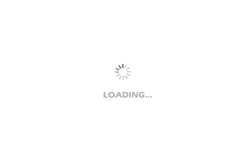
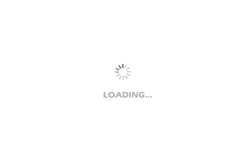
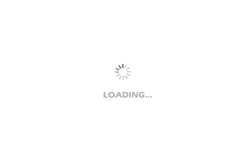
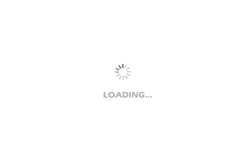
- Popular Resources
- Popular amplifiers
- MathWorks and NXP Collaborate to Launch Model-Based Design Toolbox for Battery Management Systems
- STMicroelectronics' advanced galvanically isolated gate driver STGAP3S provides flexible protection for IGBTs and SiC MOSFETs
- New diaphragm-free solid-state lithium battery technology is launched: the distance between the positive and negative electrodes is less than 0.000001 meters
- [“Source” Observe the Autumn Series] Application and testing of the next generation of semiconductor gallium oxide device photodetectors
- 采用自主设计封装,绝缘电阻显著提高!ROHM开发出更高电压xEV系统的SiC肖特基势垒二极管
- Will GaN replace SiC? PI's disruptive 1700V InnoMux2 is here to demonstrate
- From Isolation to the Third and a Half Generation: Understanding Naxinwei's Gate Driver IC in One Article
- The appeal of 48 V technology: importance, benefits and key factors in system-level applications
- Important breakthrough in recycling of used lithium-ion batteries
- Innolux's intelligent steer-by-wire solution makes cars smarter and safer
- 8051 MCU - Parity Check
- How to efficiently balance the sensitivity of tactile sensing interfaces
- What should I do if the servo motor shakes? What causes the servo motor to shake quickly?
- 【Brushless Motor】Analysis of three-phase BLDC motor and sharing of two popular development boards
- Midea Industrial Technology's subsidiaries Clou Electronics and Hekang New Energy jointly appeared at the Munich Battery Energy Storage Exhibition and Solar Energy Exhibition
- Guoxin Sichen | Application of ferroelectric memory PB85RS2MC in power battery management, with a capacity of 2M
- Analysis of common faults of frequency converter
- In a head-on competition with Qualcomm, what kind of cockpit products has Intel come up with?
- Dalian Rongke's all-vanadium liquid flow battery energy storage equipment industrialization project has entered the sprint stage before production
- Allegro MicroSystems Introduces Advanced Magnetic and Inductive Position Sensing Solutions at Electronica 2024
- Car key in the left hand, liveness detection radar in the right hand, UWB is imperative for cars!
- After a decade of rapid development, domestic CIS has entered the market
- Aegis Dagger Battery + Thor EM-i Super Hybrid, Geely New Energy has thrown out two "king bombs"
- A brief discussion on functional safety - fault, error, and failure
- In the smart car 2.0 cycle, these core industry chains are facing major opportunities!
- The United States and Japan are developing new batteries. CATL faces challenges? How should China's new energy battery industry respond?
- Murata launches high-precision 6-axis inertial sensor for automobiles
- Ford patents pre-charge alarm to help save costs and respond to emergencies
- New real-time microcontroller system from Texas Instruments enables smarter processing in automotive and industrial applications
- [Xianji HPM6750 Review] GPIO lighting and button control
- RTL8382M/RTL8380M Industrial-grade managed embedded full Gigabit switch core module
- 05 Serial port experience and receiving variable-length data
- IC card swiping technology under the screen
- AC detector
- Selection and application of freewheeling diode
- ESP32 CAM Development with MicroPython
- Division circuit
- Android smart wearable device development from entry to mastery pdf download
- Why can't we develop industry software like Matlab?