At present, most of the long-delay thermal tripping test schemes adopted in China are to directly apply a voltage to the circuit breaker through a transformer to obtain the test current. During the test, due to the fluctuation of the grid voltage, the change of the lead resistance in the current-carrying circuit, and the change of the load resistance heating, the test current changes accordingly, which makes it difficult to meet the requirements of national standards. This article introduces a power-stabilized inverter power supply, which has the advantages of stable and reliable operation, high input power factor, high output accuracy, small waveform distortion and high efficiency.
The inverter power supply with a nominal power of 300W can be used for household electric fans, televisions, and daily lighting without any problems. The 300W inverter uses a 12V/60AH battery to power the above household appliances. After a full charge, it can be used for nearly 5 hours. However, even if the battery voltage is sufficient, it is still difficult to start a 180-liter refrigerator because the output voltage drops to less than 180V at the moment of startup and fails. The nominal power of the refrigerator compressor is mostly around 100W, and the actual instantaneous current of startup can reach more than 2A. If the voltage drop at the moment of startup is not very obvious, the output power must be increased to 600VA. If a PWM voltage stabilization system is used while increasing the output power, the voltage drop at the moment of startup can be significantly reduced. Whether it is an electric fan or a refrigerator, when using an inverter power supply, an LC filter as shown in Figure 1 should be added to the output end of the inverter to improve the waveform and avoid the pulse rising edge peak from breaking through the motor winding.
Inverters using bipolar switching tubes have a base drive current that is basically 1/β of the switch current. Therefore, high-current switching circuits must use multi-stage amplification, which not only complicates the circuit but also deteriorates reliability. Moreover, as the output power increases, the switch tube drive current must be greater than 1/β of the collector current, making it impossible for ordinary driver ICs to drive directly. Although multi-stage amplification can achieve the goal, the waveform distortion increases significantly, which leads to an increase in the on/off loss of the switch tube. At present, most of the drive solutions for high-power inverters and UPS use MOS FET tubes as switch devices.
Application of MOSFET
In recent years, the manufacturing process of metal oxide insulated gate field effect transistors has developed rapidly, making it common for the drain-source withstand voltage (VDS) to reach more than kV and the drain-source current (IDS) to reach 50A. Therefore, it is widely used in high-frequency power amplification and switching circuits.
In addition, there are hybrid products of bipolar transistors and MOS FETs, namely the so-called IGBT insulated gate bipolar transistors. As the name implies, it is a combination device with MOS FET as the front stage and bipolar transistor as the output. Therefore, IGBT has both the voltage driving characteristics of insulated gate field effect tubes and the output characteristics of small saturation voltage drop and high withstand voltage of bipolar transistors. Its turn-off time is less than 0.4μs, VCEO reaches 1.8kV, and ICM reaches 100A. It is currently commonly used in circuits such as motor variable frequency speed regulation, high-power inverters and switching power supplies.
Generally, the parallel push-pull circuit of MOS FET is commonly used in medium-power switching power inverter. The on-resistance between the drain and source of MOS FET has the current-sharing characteristic of resistance. When used in parallel, no external current-sharing resistor is required, and the drain and source can be directly used in parallel. When the gate and source are used in parallel, each MOS FET tube must use a separate gate isolation resistor to avoid the increase of the total capacitance formed by the parallel connection of the gate capacitance of each switch tube, which leads to an increase in charging current, delays the process of establishing the driving voltage, and increases the conduction loss of the switch tube.
MOSFET Driving
In recent years, with the improvement of MOSFET production technology, various switching power supplies and converters have widely adopted MOS FET tubes as high-frequency and high-voltage switching circuits. However, integrated circuits dedicated to driving MOS FET tubes are extremely rare in China. The requirements for driving MOSFET tubes are low output impedance and built-in current sinking drive circuits. Therefore, ordinary driver ICs used for bipolar switch tubes cannot be directly used to drive field effect tubes.
At present, there are still few IC varieties that can directly drive MOSFET tubes worldwide. The single-ended driver is commonly used in the UC3842 series, and the double-ended drivers used for push-pull circuits are SG3525A (driving N-channel field effect tubes), SG3527A (driving P-channel field effect tubes) and SG3526N (driving N-channel field effect tubes). However, in the nearly 40 years of rapid development of switching power supplies, there are a large number of excellent and fully functional double-ended output driver ICs. At the same time, with the popularization of MOSFET tubes, many new circuits have been developed, which can be used to drive MOSFET tubes. Solving the MOSFET drive includes two contents: one is to reduce the output impedance of the driver IC; the other is to add a current injection path for the MOSFET tube. For this reason, it is worth reviewing the driver stages of SG3525A, SG3527A, SG3526N and the single-ended driver UC3842 series.
Figure 2a is the drive output circuit of the above IC (taking one of the outputs as an example). The output pulse of the oscillator passes through the NOR gate, and the rising and falling edges of the pulse are output as two drive pulses with different timings. During the positive pulse period, Q1 is turned on and Q2 is turned off. The positive pulse output by the emitter of Q1 charges the gate capacitance of the switch tube, so that the drain-source quickly reaches the conduction threshold. After the positive pulse, if the charge between the gate and source of the switch tube cannot be quickly discharged, the drain-source drive pulse will not be cut off immediately. For this reason, after Q1 is cut off, the NOR gate immediately turns on Q2 to provide a path for the gate-source capacitance to discharge. In this drive mode, Q1 provides drive current and Q2 provides injection current (i.e., discharge current). Q1 is an emitter follower, which itself has a very low output impedance.
In order to meet the above requirements, the common bipolar switch drive output is connected to the peripheral drive circuit of Figure 2b, which can also meet the drive requirements of MOS FET tubes. The integrated circuit designed to drive the bipolar switch tube often uses a double-ended totem pole to output two pulses, that is, the polarity of the two output pulses is the same, to drive the two push-pull NPN transistors. In order to allow the push-pull two tubes to be turned on in turn, the time sequence of the two drive pulses is different. If the first output is a positive pulse, after being cut off, after a dead time, the second output begins. The two-way drive stage uses a bipolar transistor collector-emitter open output to obtain different pulse polarities for driving NPN or PNP switch tubes.
In FIG. 2b , a PNP transistor Q and a diode D are connected, and their functions are to shunt the driving current and the sinking current respectively.
The emitter of the buffer inside the pre-driver IC establishes a non-inverted positive polarity drive pulse on the load resistor R1 to cut off the transistor Q. At the beginning of the rising edge of the drive pulse, the positive polarity pulse is added to the gate-source of the MOS FET switch tube through the diode D to charge the gate-source capacitor CGS. When the charging voltage reaches the gate voltage threshold of the switch tube, its drain-source is turned on. After the positive pulse duration, the emitter level of the buffer amplifier inside the IC is zero, and the output end will have a certain period of dead zone. At this time, the emitter of Q carries the CGS charging voltage, so Q is turned on, CGS discharges through the ec pole of Q, and the collector current of Q is the current injection path. R2 is the gate resistor of the switch tube, the purpose is to prevent the gate of the switch tube from being suspended during the Q and D conversion process, otherwise its nearly infinite high input impedance is very easy to be broken down by the interference level. Using this method to drive the MOS FET switch tube using an ordinary double-terminal output integrated circuit can achieve a relatively ideal effect. In order to reduce the conduction/cutoff loss, D should use a fast switching diode. The collector current of Q should be determined according to the switch tube. If multiple MOS FET tubes are used in parallel for each output in order to increase the output power, a perfusion transistor with a sufficiently large ICM and a high-speed switching diode should be selected.
TL494 Applications
Among all the dual-end output driver ICs currently available, the TL494 developed by Texas Instruments has the most complete functions and the strongest driving capability. The total current of its two outputs with different timings is twice that of the SG3525, reaching 400mA. This alone makes the switching power supplies, DC/DC converters, and inverters with output power of kilowatts and above almost all use TL494. Although TL494 is designed to drive bipolar switch tubes, most of the equipment using MOS FET switch tubes currently also widely uses TL494 using peripheral perfusion circuits. For this reason, this section will introduce its functions and application circuits in detail. Its internal block diagram is shown in Figure 3. Its internal circuit functions, characteristics, and application methods are as follows:
A. An independent sawtooth oscillator with built-in RC timing circuit setting frequency has an oscillation frequency of fo (kHz) = 1.2/R (kΩ). C (μF), and its maximum oscillation frequency can reach 300kHz. It can drive bipolar switch tubes and, after adding a current injection path, can also drive MOS FET switch tubes.
B. There is a dead time control circuit composed of a comparator inside. The output level of the comparator is controlled by an external voltage. The trigger is flipped through its output level to control the dead time between the two outputs. When the level of the 4th pin increases, the dead time increases.
C. The two outputs of the trigger are equipped with control circuits, so that Q1 and Q2 can output driving pulses with different double-ended timings to drive push-pull switching circuits and half-bridge switching circuits, and can also output single-ended driving pulses with the same phase sequence to drive single-ended switching circuits.
D. The two internal groups of identical error amplifiers have their common-mode input terminals led out of the chip, so their reference voltage can be freely set to facilitate voltage stabilization sampling, or one of them can be used as over-voltage, over-current and over-threshold protection.
E. The output drive current reaches 400mA on a single end, which can directly drive a switch circuit with a peak current of 5A. The peak value of the double-ended output pulse is 2×200mA, and adding a drive stage can drive nearly 1000W push-pull and bridge circuits.
The functions and parameters of each pin of TL494 are as follows: Pins 1 and 16 are the non-inverting inputs of error amplifiers A1 and A2. The maximum input voltage does not exceed VCC+0.3V. Pins 2 and 15 are the inverting inputs of error amplifiers A1 and A2. The reference voltage for error detection can be connected. Pin 3 is the output of error amplifiers A1 and A2. It is used to control the non-inverting input of the PWM comparator inside the integrated circuit. When the output voltage of either A1 or A2 increases, the output pulse width of the PWM comparator is controlled to decrease. At the same time, the output terminal is also led out to connect the RC frequency correction circuit and the direct negative feedback circuit between pins 2 and 15, which can stabilize the gain of the error amplifier and prevent its high-frequency self-excitation. In addition, the voltage of pin 3 is inversely proportional to the output pulse width, and this terminal function can also be used to achieve high-level protection. Pin 4 is the dead time control terminal. When a voltage below 1V is applied, the dead time is proportional to the applied voltage. If the voltage exceeds 1V, the internal comparator will turn off the output pulse of the trigger. Pin 5 is the external timing capacitor terminal of the sawtooth oscillator, and pin 6 is the external timing resistor terminal of the sawtooth oscillator. It is generally used to limit the oscillation frequency to less than 40kHz when driving bipolar transistors. Pin 7 is the ground terminal. Pins 8 and 11 are the collector open-circuit output terminals of the two-way driver amplifier NPN tube. When pins 8 and 11 are connected to Vcc, and pins 9 and 10 are connected to the emitter load resistor to the ground, the two channels are positive polarity totem pole outputs, which are used to drive various push-pull switch circuits. When pins 8 and 11 are grounded, the two channels are in-phase drive pulse outputs. Pins 8, 11 and pins 9 and 10 can be directly connected in parallel. The maximum drive current is 2×200mA when the two-end output is used, and the maximum drive current is 400mA when used in parallel. Pin 14 is the internal reference voltage precision voltage regulator circuit terminal. Output 5V±0.25V reference voltage, the maximum load current is 10mA. Used for error detection reference voltage and control voltage of control mode. The extreme parameters of TL494: maximum instantaneous operating voltage (pin 12) 42V, maximum output current 250mA, maximum error input voltage Vcc+0.3V, test/ambient temperature ≤45℃, maximum allowable power consumption 1W, maximum junction temperature 150℃, operating temperature range 0~70℃, storage temperature -65~+150℃.
Standard application parameters of TL494: Vcc (pin 12) is 7~40V, Vcc1 (pin 8) and Vcc2 (pin 11) are 40V, Ic1 and Ic2 are 200mA, RT range is 1.8~500kΩ, CT range is 4700pF~10μF, and the maximum oscillation frequency (fOSC) is ≤300kHz.
Figure 4 is a 400W high-power voltage-stabilizing inverter circuit using TL494 introduced in a foreign publication. The excitation conversion part uses TL494, VT1, VT2, VD3, and VD4 to form a current-injection drive circuit to drive two 60V/30A MOS FET switch tubes in each of the two channels. If the output power needs to be increased, 3 to 4 switch tubes can be used in parallel for each channel, and the circuit remains unchanged. The application method of TL494 in this inverter is as follows:
Pins 1 and 2 form a voltage-stabilizing sampling and error amplification system. The positive input pin 1 inputs the 15V DC voltage output by the inverter secondary sampling winding rectification. After R1 and R2 divide the voltage, the pin 1 has a sampling voltage of nearly 4.7~5.6V when the inverter is working normally. The negative input pin 2 inputs a 5V reference voltage (output from pin 14). When the output voltage decreases, the voltage of pin 1 decreases, the error amplifier outputs a low level, and the output voltage is increased through the PWM circuit. Normally, the voltage value of pin 1 is 5.4V, the voltage value of pin 2 is 5V, and the voltage value of pin 3 is 0.06V. At this time, the output AC voltage is 235V (square wave voltage). Pin 4 is connected to R6, R4, and C2 to set the dead time. The normal voltage value is 0.01V. Pins 5 and 6 are connected to CT and RT to set the oscillator triangle wave frequency to 100Hz. Normally, the voltage value of pin 5 is 1.75V, and the voltage value of pin 6 is 3.73V. Pin 7 is the common ground. Pins 8 and 11 are the collectors of the internal drive output transistors, and pin 12 is the front-stage power supply terminal of TL494. These three terminals control the start/stop of TL494 through switch S, and serve as the control switch of the inverter. When S1 is turned off, TL494 has no output pulse, so the switch tubes VT4~VT6 have no current. When S1 is turned on, the voltage value of these three pins is the positive voltage of the battery. Pins 9 and 10 are the emitters of the internal drive-stage transistors, which output two positive pulses with different timings. The voltage value is 1.8V under normal circumstances. Among the pins 13, 14, and 15, pin 14 outputs a 5V reference voltage, so that pin 13 has a 5V high level, controls the gate circuit, and the trigger outputs two drive pulses for the push-pull switch circuit. Pin 15 is connected to an external 5V voltage to form the inverting input reference voltage of the error amplifier, so that the in-phase input pin 16 constitutes a high-level protection input terminal. In this connection, when the input of pin 16 is higher than 5V, the output voltage can be reduced by voltage stabilization, or the drive pulse can be turned off to achieve protection. There is almost no possibility of output overvoltage in the self-excited inverter, so pin 16 is not used in this circuit and is grounded by resistor R8.
The inverter uses a 400VA power frequency transformer, and the core uses 45×60mm2 silicon steel sheet. The primary winding uses 1.2mm diameter enameled wire, two wires are wound in parallel for 2×20 turns. The secondary sampling winding uses 0.41mm enameled wire for 36 turns, with a center tap. The secondary winding is calculated at 230V, and 0.8mm enameled wire is used for 400 turns. Switching tubes VT4~VT6 can be replaced by any type of 60V/30A N-channel MOS FET tube. VD7 can use 1N400X series ordinary diodes. The circuit can work normally almost without debugging. When the positive terminal voltage of C9 is 12V, R1 can be selected between 3.6~4.7kΩ, or adjusted with a 10kΩ potentiometer to make the output voltage the rated value. If the output power of this inverter is increased to nearly 600W, in order to avoid excessive primary current and increase resistive loss, it is advisable to change the battery to 24V, and the switch tube can use a high-current MOS FET tube with a VDS of 100V. It should be noted that it is better to use multiple tubes in parallel rather than a single switch tube with an IDS greater than 50A. The reasons are: first, the price is higher, and second, it is too difficult to drive. It is recommended to use 100V/32A 2SK564, or three 2SK906s in parallel. At the same time, the cross-section of the transformer core must reach 50cm2, and the number of turns and wire diameter should be calculated according to the calculation method of ordinary power transformers, or a waste UPS-600 transformer can be used as a substitute. If it is used to power refrigerators and electric fans, don't forget to add LC low-pass filters.
Since the AC current source in this article is essentially a voltage-type current source, that is, the output current is stabilized by quickly adjusting the output voltage. When the output is open, the output voltage will rise rapidly to near the DC bus voltage, and will not rise very high like the current source. Nevertheless, when the load is open, the output voltage will still rise rapidly and cause the output voltage to oscillate at the LC resonant frequency, both of which will cause serious distortion of the output waveform; in addition, when the output load is reconnected, it will cause output transient overcurrent. Therefore, the described AC current inverter power supply is used in the long-delay thermal trip test of low-voltage electrical appliances, and is suitable for the calibration and testing of the long-delay characteristics of low-voltage electrical appliances such as circuit breakers and thermal relays.
Previous article:Analysis of the main power circuit design of three-phase PWM inverter
Next article:Design and implementation of a multifunctional inverter power supply
Recommended ReadingLatest update time:2024-11-16 21:03
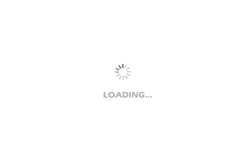
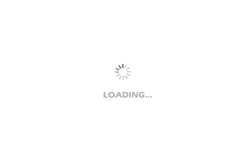
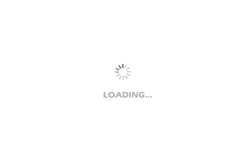
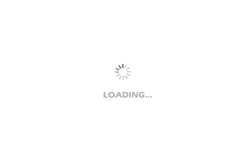
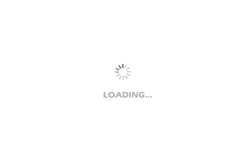
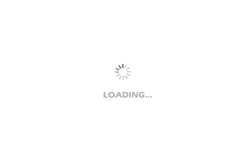
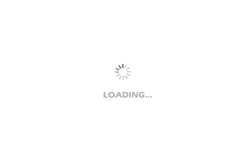
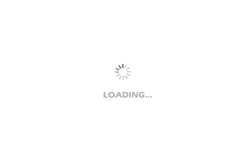
- Popular Resources
- Popular amplifiers
-
Optimization design of SGT_MOSFET peak oscillation in synchronous rectification circuit
-
Study on the Behavioral Model of Silicon Carbide MOSFET Power Module and EMI Prediction of Low-Voltage Auxiliary Power Supply
-
Theory and practice of small-size MOS device models for VLSI simulation
-
Power Electronics Technology 2nd Edition (Li Jie, Chao Xiaojie, Jia Weijuan, Yang Jiayi, Lai Wei)
- MathWorks and NXP Collaborate to Launch Model-Based Design Toolbox for Battery Management Systems
- STMicroelectronics' advanced galvanically isolated gate driver STGAP3S provides flexible protection for IGBTs and SiC MOSFETs
- New diaphragm-free solid-state lithium battery technology is launched: the distance between the positive and negative electrodes is less than 0.000001 meters
- [“Source” Observe the Autumn Series] Application and testing of the next generation of semiconductor gallium oxide device photodetectors
- 采用自主设计封装,绝缘电阻显著提高!ROHM开发出更高电压xEV系统的SiC肖特基势垒二极管
- Will GaN replace SiC? PI's disruptive 1700V InnoMux2 is here to demonstrate
- From Isolation to the Third and a Half Generation: Understanding Naxinwei's Gate Driver IC in One Article
- The appeal of 48 V technology: importance, benefits and key factors in system-level applications
- Important breakthrough in recycling of used lithium-ion batteries
- Innolux's intelligent steer-by-wire solution makes cars smarter and safer
- 8051 MCU - Parity Check
- How to efficiently balance the sensitivity of tactile sensing interfaces
- What should I do if the servo motor shakes? What causes the servo motor to shake quickly?
- 【Brushless Motor】Analysis of three-phase BLDC motor and sharing of two popular development boards
- Midea Industrial Technology's subsidiaries Clou Electronics and Hekang New Energy jointly appeared at the Munich Battery Energy Storage Exhibition and Solar Energy Exhibition
- Guoxin Sichen | Application of ferroelectric memory PB85RS2MC in power battery management, with a capacity of 2M
- Analysis of common faults of frequency converter
- In a head-on competition with Qualcomm, what kind of cockpit products has Intel come up with?
- Dalian Rongke's all-vanadium liquid flow battery energy storage equipment industrialization project has entered the sprint stage before production
- Allegro MicroSystems Introduces Advanced Magnetic and Inductive Position Sensing Solutions at Electronica 2024
- Car key in the left hand, liveness detection radar in the right hand, UWB is imperative for cars!
- After a decade of rapid development, domestic CIS has entered the market
- Aegis Dagger Battery + Thor EM-i Super Hybrid, Geely New Energy has thrown out two "king bombs"
- A brief discussion on functional safety - fault, error, and failure
- In the smart car 2.0 cycle, these core industry chains are facing major opportunities!
- The United States and Japan are developing new batteries. CATL faces challenges? How should China's new energy battery industry respond?
- Murata launches high-precision 6-axis inertial sensor for automobiles
- Ford patents pre-charge alarm to help save costs and respond to emergencies
- New real-time microcontroller system from Texas Instruments enables smarter processing in automotive and industrial applications
- Allegro Issues
- 【National Technology N32G430】1: Preliminary Study
- How to draw large areas of PCB
- How to tell whether a component is genuine or fake?
- How to layout the PCB of photovoltaic power supply?
- Questions and Answers about bq24650 and BQ25601
- A Beginner's Guide to PCB Design
- Ultrasonic utility knife (cutting knife) 2999RMB ???
- 【Two-player fighting game machine】+ Fighting game based on custom GUI
- High salary recruitment of visual software engineers