A power supply is not a simple small box. It is the heart of an active device, providing energy to components continuously. The quality of the power supply directly affects the performance of components. The design, manufacturing, and quality management of power supplies require precise electronic instruments and equipment to simulate the various characteristics (that is, various specifications) of the power supply during actual operation, and can only be put into use after verification. Engineers must consider the following factors when designing or evaluating power supplies:
1. Describe the influence of input voltage on output voltage in several indicators
1. Absolute voltage regulation coefficient
A. Absolute voltage regulation coefficient: It indicates the ratio of the DC change △U0 of the voltage-regulated power supply output to the change △Ui of the input power grid when the load remains unchanged. That is: K=△U0/△Ui.
B. Relative voltage regulation coefficient: It indicates the ratio of the relative change of the DC voltage △Uo output by the voltage regulator to the relative change of the output power grid Ui when the load remains unchanged. That is: S=△Uo/Uo/△Ui/Ui.
2. Grid regulation rate
It indicates the relative change in the output voltage of the regulated power supply when the input grid voltage changes by ±10% from the rated value, and is sometimes expressed as an absolute value.
3. Voltage stability
The relative change in output voltage (△Uo/Uo percentage) caused by the load current being maintained at any value within the rated range and the input voltage changing within the specified range is called the voltage stability of the voltage regulator.
2. Several indicators of the impact of load on output voltage
1. Load regulation (also called current regulation)
Under rated grid voltage, when the load current changes from zero to maximum, the maximum relative change of output voltage is usually expressed as a percentage, and sometimes as an absolute change.
2. Output resistance (also called equivalent internal resistance or internal resistance)
Under rated grid voltage, the output voltage changes △Uo due to the load current change △IL, so the output resistance is Ro=|△Uo/△IL| ohms.
3. Several indicators of ripple voltage
1. Maximum ripple voltage
The absolute value of the output voltage ripple (including noise) at rated output voltage and load current, usually expressed as peak-to-peak value or effective value.
2. Ripple factor Y (%)
Under rated load current, the ratio of the effective value of the output ripple voltage Urms to the output DC voltage Uo, that is, y=Umrs/Uo x100%
3. Ripple voltage suppression ratio
At the specified ripple frequency (for example 50Hz), the ratio of the ripple voltage Ui~ in the output voltage to the ripple voltage Uo~ in the output voltage, that is: ripple voltage suppression ratio = Ui~/Uo~.
Here is a statement: noise is different from ripple. Ripple is a component that appears between the output terminals and is synchronized with the input frequency and the switching frequency. It is expressed as a peak-to-peak value and is generally less than 0.5% of the output voltage. Noise is a high-frequency component other than ripple that appears between the output terminals. It is also expressed as a peak-to-peak value and is generally around 1% of the output voltage. Ripple noise is a combination of the two, expressed as a peak-to-peak value, and is generally less than 2% of the output voltage.
4. Inrush Current
Inrush current refers to the maximum instantaneous current that flows before the input current reaches a stable state when the input voltage is connected or disconnected at a specified time interval. It is usually 20A-30A.
5. Overcurrent protection
Overcurrent protection is a power supply load protection function to prevent damage to the power supply and load caused by overload output current, including short circuit on the output terminal. The given value of overcurrent is generally 110%-130% of the rated current.
6. Overvoltage protection
Overvoltage protection is a function that protects the load from excessive voltage between terminals. It is generally specified as 130%-150% of the output voltage.
7. Output undervoltage protection
When the output voltage is below the standard value, the output voltage drop is detected or the power supply is stopped and an alarm signal is issued to protect the load and prevent misoperation. The value is usually around 80%-30% of the output voltage.
8. Overheat protection
When an abnormality occurs inside the power supply or the power supply temperature rises beyond the standard due to improper use, the power supply will stop working and an alarm signal will be issued.
9. Temperature Drift and Temperature Coefficient
Temperature drift: Changes in ambient temperature affect the parameters of components, thus causing changes in the output voltage of the regulator. The temperature coefficient is commonly used to indicate the magnitude of temperature drift.
Absolute temperature coefficient: The change in output voltage caused by a temperature change of 1 degree Celsius, △UoT, the unit is V/℃ or millivolt per degree Celsius.
Relative temperature coefficient: The relative change in output voltage caused by a temperature change of 1 degree Celsius is △UoT/Uo, the unit is V/℃.
10. Drift
When the input voltage, load current and ambient temperature of the voltage regulator remain constant, the stability of the component parameters will also cause changes in the output voltage. Slow changes are called drift, fast changes are called noise, and the changes in between are called fluctuations.
There are two ways to express drift:
1. The change in output voltage value △Uot within a specified time.
2. The relative change of output voltage within a specified time △Uot/Uo.
The drift time can be set to 1 minute, 10 minutes, 1 hour, 8 hours or longer. Only in the regulator with higher accuracy, there are two indicators: temperature coefficient and temperature drift.
11. Response Time
Response time refers to the time it takes for the output voltage of the regulator to adjust from the initial change to the new stable value when the load current changes suddenly. In DC regulators, this characteristic is represented by the output voltage waveform when the load current is a rectangular wave, which is called the transition characteristic.
12. Distortion
Distortion is unique to AC voltage stabilizers. It means that the output waveform is not a positive waveform, resulting in waveform distortion, which is called distortion.
13. Noise
According to the audible frequency regulation of 30Hz-18kHZ, this is not a problem for the conversion frequency of the switching power supply, but it needs to be regulated according to needs for the power supply with a fan.
14. Input Noise
In order to keep the switching power supply working normally, the input noise index should be formulated according to the rated input conditions and the pulse voltage (0-peak) superimposed on the industrial frequency by the allowable input. Generally, the external pulse width is 100-800us and the external voltage is 1000V.
15. Surge
This is to add a surge voltage to the input voltage at a specified number of times at intervals of more than 1 minute to avoid abnormal phenomena such as insulation damage, flashover, arcing, etc. The value specified for communication equipment is several thousand volts, generally 1200V.
16. Static Noise
Refers to a kind of repetitive pulse static electricity that can keep the whole output circuit in normal working state when it is applied to any part of the power supply frame under rated input conditions. It is generally guaranteed to be within 5-10KV.
17. Stability
Under the allowable operating conditions, the maximum relative change of output voltage is △Uo/Uo.
18. Electrical safety requirements (GB 4943-90)
1. Safety requirements for power supply structure
1) Space requirements
UL, CSA, and VDE safety regulations emphasize the distance requirements on the surface and space between live parts and between live parts and non-live metal parts. UL and CSA require that there should be a distance of 0.1 inches between high-voltage conductors with an inter-pole voltage greater than or equal to 250VAC, and between high-voltage conductors and non-live metal parts (not including wires), both on the surface and in space; VDE requires a 3mm creep or 2mm clear gap between AC lines; IEC requires a 3mm clear gap between AC lines and a 4mm clear gap between AC lines and grounding conductors. In addition, VDE and IEC require a minimum of 8mm of space between the output and input of the power supply.
2) Dielectric experimental test method (high voltage: input and output, input and ground, input AC between two levels)
3) Leakage current measurement
Leakage current is the current flowing through the input side ground wire. In the switching power supply, it is mainly the leakage current through the bypass capacitor of the noise filter. UL and CSA both require that the exposed non-charged metal parts should be connected to the ground. The leakage current is measured by connecting a 1.5K ohm resistor between these parts and the ground. The leakage current should not be greater than 5 mA. VDE allows: Use a 1.5K ohm resistor and a 150nP capacitor in parallel. And apply 1.06 times the rated operating voltage. For data processing equipment, the leakage current should not be greater than 3.5 mA. Generally, it is about 1 mA.
4) Insulation resistance test
VDE requirements: There should be a 7M ohm resistor between the input and the low voltage output circuit, and a 2M ohm resistor or a 500V DC voltage for 1 minute between the accessible metal part and the input.
5) Printed circuit board requirements
Requires UL certified 94V-2 material or better.
2. Safety requirements for power transformer structure
1) Insulation of transformer
The copper wire used in the transformer winding should be enameled wire, and other metal parts should be coated with insulating materials such as porcelain and lacquer.
2) Dielectric strength of transformer
There should be no insulation rupture and arcing during the experiment.
3) Insulation resistance of transformer
The insulation resistance between transformer windings shall be at least 10M ohms. A 500V DC voltage shall be applied between the winding and the core, frame and shielding layer for 1 minute. No breakdown or arcing shall occur.
4) Transformer humidity resistance
The transformer must be placed in a humid environment and immediately undergo insulation resistance and dielectric strength tests, and meet the requirements. A humid environment is generally: relative humidity is 92% (with a tolerance of 2%), the temperature is stable between 20 and 30 degrees Celsius, and the error is allowed to be 1%. The above tests must be carried out immediately after being placed in the humid environment for at least 48 hours. At this time, the temperature of the transformer itself should not be 4 degrees Celsius higher than the test before entering the humid environment.
5) VDE requirements for transformer temperature characteristics
6) UL and CSA requirements on transformer temperature characteristics.
Note: IEC——International Electrotechnical Commission
VDE——Verbandes Deutcher ElectrotechnICer
UL——Underwriters' Laboratories
CSA——CANadian Standards Association
FCC——Federal Communications Commission
19. Radio disturbance (tested in accordance with GB 9254-1998)
1. Power terminal disturbance voltage limit
2. Radiated disturbance limit
20. Electromagnetic compatibility test
ElectromagnetIC compatibility test (EMC)
Electromagnetic compatibility refers to the ability of a device or system to work normally in a common electromagnetic environment without causing unbearable electromagnetic interference to anything in that environment.
There are generally two propagation paths for electromagnetic interference waves, and each path should be evaluated. One is to propagate to the power line with a long wavelength band, which interferes with the emission area, generally below 30MHz. This long wavelength frequency is less than 1 wavelength within the length range of the power line attached to the electronic equipment, and the amount of radiation into space is also very small. From this, the voltage occurring on the power line can be grasped, and the size of the interference can be fully evaluated. This noise is called conducted noise.
When the frequency reaches 30MHz or more, the wavelength will also become shorter. At this time, if only the noise source voltage generated in the power line is evaluated, it will not match the actual interference. Therefore, a method of evaluating the noise level by directly measuring the interference wave propagating into the space is adopted. This noise is called radiation noise. The methods for measuring radiation noise include the above-mentioned method of directly measuring the interference wave propagating into the space according to the electric field strength and the method of measuring the power leaked to the power line.
Electromagnetic compatibility tests include the following tests:
① Magnetic field sensitivity: (Immunity) The degree of unwanted response of a device, subsystem or system when exposed to electromagnetic radiation. The lower the sensitivity level, the higher the sensitivity and the worse the immunity. Fixed frequency, peak-to-peak magnetic field
② Electrostatic discharge sensitivity: The charge transfer caused by objects with different electrostatic potentials approaching or directly contacting each other. A 300PF capacitor is charged to -15000V and discharged through a 500 ohm resistor. It can be out of tolerance, but it must be normal after discharge. Data transmission and storage cannot be lost.
③ Power supply transient sensitivity: including spike signal sensitivity (0.5us 10us twice), voltage transient sensitivity (10%-30%, 30S recovery), frequency transient sensitivity (5%-10%, 30S recovery).
④ Radiated sensitivity: A measure of the radiated interference field that causes equipment degradation. (14K-1GHz, electric field strength is 1V/M)
⑤ Conducted sensitivity: A measure of interference signals or voltages on power, control or signal lines that cause unwanted responses or performance degradation in equipment. (30Hz-50KHZ 3V, 50K-400M 1V)
⑥ Magnetic field interference in non-working state: The magnetic flux density of the packaging box at 4.6m is less than 0.525uT, and at 0.9m it is 0.525Ut.
⑦ Magnetic field interference in working state: the AC magnetic flux density of up, down, left and right is less than 0.5mT.
⑧ Conducted interference: interference propagating along the conductor. 10KHz-30MHz 60 (48) dBuV.
⑨ Radiated interference: Electromagnetic interference propagating through space in the form of electromagnetic waves. 10KHz-1000MHz 30 Shielded room 60 (54) uV/m.
21. Environmental Experiment
Environmental testing is to expose products or materials to natural or artificial environments, so as to evaluate their performance under storage, transportation and use conditions that they may actually encounter. Including low temperature, high temperature, constant humidity and heat, alternating humidity and heat, impact (impact and collision), vibration, constant acceleration, storage, mildew, corrosive atmosphere (such as salt spray), sand and dust, air pressure (high or low pressure), temperature change, flammability, sealing, water, radiation (sun or nuclear), soldering, terminal strength, noise (micro-beating 65DB), etc.
Previous article:Focus on testing to make power supply design more convenient
Next article:Design of current protection system based on GSM
Recommended ReadingLatest update time:2024-11-15 10:42
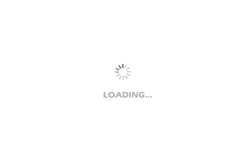
- MathWorks and NXP Collaborate to Launch Model-Based Design Toolbox for Battery Management Systems
- STMicroelectronics' advanced galvanically isolated gate driver STGAP3S provides flexible protection for IGBTs and SiC MOSFETs
- New diaphragm-free solid-state lithium battery technology is launched: the distance between the positive and negative electrodes is less than 0.000001 meters
- [“Source” Observe the Autumn Series] Application and testing of the next generation of semiconductor gallium oxide device photodetectors
- 采用自主设计封装,绝缘电阻显著提高!ROHM开发出更高电压xEV系统的SiC肖特基势垒二极管
- Will GaN replace SiC? PI's disruptive 1700V InnoMux2 is here to demonstrate
- From Isolation to the Third and a Half Generation: Understanding Naxinwei's Gate Driver IC in One Article
- The appeal of 48 V technology: importance, benefits and key factors in system-level applications
- Important breakthrough in recycling of used lithium-ion batteries
- LED chemical incompatibility test to see which chemicals LEDs can be used with
- Application of ARM9 hardware coprocessor on WinCE embedded motherboard
- What are the key points for selecting rotor flowmeter?
- LM317 high power charger circuit
- A brief analysis of Embest's application and development of embedded medical devices
- Single-phase RC protection circuit
- stm32 PVD programmable voltage monitor
- Introduction and measurement of edge trigger and level trigger of 51 single chip microcomputer
- Improved design of Linux system software shell protection technology
- What to do if the ABB robot protection device stops
- ASML predicts that its revenue in 2030 will exceed 457 billion yuan! Gross profit margin 56-60%
- Detailed explanation of intelligent car body perception system
- How to solve the problem that the servo drive is not enabled
- Why does the servo drive not power on?
- What point should I connect to when the servo is turned on?
- How to turn on the internal enable of Panasonic servo drive?
- What is the rigidity setting of Panasonic servo drive?
- How to change the inertia ratio of Panasonic servo drive
- What is the inertia ratio of the servo motor?
- Is it better for the motor to have a large or small moment of inertia?
- Does lighttpd support PHP?
- TI Designs – Precision file question about Bode plots
- Does the boost topology circuit limit the duty cycle?
- Op amp differential amplification problem
- FAQ_How to fill in the BQB certification application form
- HC6800 EM3 V2.0 CD-ROM
- Share the temperature and humidity monitoring of LoRa communication technology
- [TI star product limited time purchase] + AWR6843 purchase experience and unboxing
- EEWORLD University ---- VLSI Testing
- How to test the withstand voltage characteristics of general ceramic capacitors