This paper discusses the IGBT gate drive characteristics, gate series resistance and its drive circuit, and proposes an effective method of slow gate voltage drop overcurrent protection and overvoltage absorption.
introduction
IGBT is a composite device of MOSFET and bipolar transistor. It has the characteristics of easy driving of MOSFET and large voltage and current capacity of power transistor. Its frequency characteristics are between MOSFET and power transistor, and it can work normally in the frequency range of tens of kHz, so it occupies a dominant position in high-frequency and medium-power applications.
IGBT is a voltage-controlled device. When a DC voltage of more than ten V is applied between its gate and emitter, only a leakage current of μA level flows through it, and basically no power is consumed. However, there is a large parasitic capacitance (several thousand to tens of thousands of pF) between the gate and emitter of IGBT. During the rising and falling edges of the driving pulse voltage, several A of charging and discharging current needs to be provided to meet the dynamic requirements of opening and closing. This requires its driving circuit to output a certain peak current.
As a high-power composite device, IGBT may be locked and damaged when overcurrent occurs. If the gate voltage is locked at a normal speed when overcurrent occurs, the excessive current change rate will cause overvoltage. Therefore, soft shutdown technology is required. Therefore, it is very necessary to master the driving and protection characteristics of IGBT.
Gate characteristics
The gate of the IGBT is electrically isolated from the emitter by a layer of oxide film. Since this oxide film is very thin, its breakdown voltage can generally only reach 20~30V, so gate breakdown is one of the common causes of IGBT failure. In applications, although the gate drive voltage is sometimes guaranteed not to exceed the maximum rated gate voltage, the parasitic inductance of the gate connection and the capacitive coupling between the gate and the collector can also generate an oscillating voltage that damages the oxide layer. For this reason. Twisted wires are usually used to transmit drive signals to reduce parasitic inductance. A small resistor in series in the gate connection can also suppress the oscillating voltage.
Due to the distributed capacitance Cge and Cgc between the gate-emitter and gate-collector of the IGBT, and the distributed inductance Le in the emitter drive circuit, the influence of these distributed parameters makes the actual drive waveform of the IGBT not completely the same as the ideal drive waveform, and produces factors that are not conducive to the opening and closing of the IGBT. This can be verified by using an inductive load circuit with a freewheeling diode (see Figure 1).
At t0, the gate drive voltage starts to rise. At this time, the main factors affecting the rising slope of the gate voltage uge are only Rg and Cge, and the gate voltage rises faster. At t1, the gate threshold value of the IGBT is reached and the collector current starts to rise. From this point on, there are two reasons that cause the uge waveform to deviate from the original trajectory.
First, the induced voltage on the distributed inductance Le in the emitter circuit increases with the increase of the collector current ic, thereby weakening the gate drive voltage and reducing the rising rate of the gate-emitter uge, slowing down the growth of the collector current.
Secondly, another factor that affects the voltage of the gate drive circuit is the Miller effect of the gate-collector capacitance Cgc. At t2, the collector current reaches its maximum value, and then the gate-collector capacitance Cgc begins to discharge, increasing the capacitive current of Cgc in the drive circuit, increasing the voltage drop on the impedance in the drive circuit, and also weakening the gate drive voltage. Obviously, the lower the impedance of the gate drive circuit, the weaker this effect is, and this effect lasts until t3, when uce drops to zero. Its influence also slows down the turn-on process of the IGBT. After t3, ic reaches a steady-state value, and after the factors affecting the gate voltage uge disappear, uge reaches its maximum value at a faster rate of increase.
(a) Equivalent circuit (b) Turn-on waveform
Figure 1 IGBT switch equivalent circuit and turn-on waveform
As can be seen from the waveform in Figure 1, due to the existence of Le and Cgc, the rising rate of uge slows down a lot in the actual operation of IGBT. This effect of hindering the rise of driving voltage is manifested as an obstacle to the rise of collector current and the turn-on process. In order to mitigate this effect, the internal resistance of Le and Cgc of the IGBT module and the gate drive circuit should be as small as possible to obtain a faster turn-on speed.
Figure 2 Waveform when IGBT is turned off
The waveform of IGBT when it is turned off is shown in Figure 2. At t0, the gate drive voltage begins to decrease, and at t1, it reaches a level that can just maintain the normal working current of the collector. The IGBT enters the linear working area, and uce begins to rise. At this time, the Miller effect of the gate-collector capacitance Cgc dominates the rise of uce. Due to the coupling charging effect of Cgc, uge remains basically unchanged during t1-t2. At t2, uge and ic begin to decrease at a speed determined by the inherent impedance between the gate and the emitter. At t3, uge and ic both drop to zero, and the shutdown ends.
As can be seen from Figure 2, the presence of capacitor Cgc prolongs the turn-off process of the IGBT. In order to reduce this effect, on the one hand, an IGBT device with a smaller Cgc should be selected; on the other hand, the internal impedance of the drive circuit should be reduced to increase the charging current flowing into Cgc and speed up the rise of uce.
In practical applications, the uge amplitude of IGBT also affects the saturation conduction voltage drop: as the uge increases, the saturation conduction voltage will decrease. Since the saturation conduction voltage is one of the main reasons for the heating of IGBT, it must be minimized. Usually the uge is 15~18V. If it is too high, it is easy to cause gate breakdown. Generally, 15V is taken. When the IGBT is turned off, adding a certain negative bias voltage to its gate-emitter is beneficial to improve the anti-interference ability of the IGBT, usually 5~10V.
Effect of Gate Series Resistance on Gate Drive Waveform
The rise and fall rates of the gate drive voltage have a great influence on the IGBT turn-on and turn-off process. The MOS channel of the IGBT is directly controlled by the gate voltage, and the drain current of the MOSFET part controls the gate current of the bipolar part, so that the turn-on characteristics of the IGBT are mainly determined by its MOSFET part, so the turn-on of the IGBT is greatly affected by the gate drive waveform. The turn-off characteristics of the IGBT mainly depend on the recombination rate of the internal minority carriers, and the recombination of the minority carriers is affected by the turn-off of the MOSFET, so the gate drive also affects the turn-off of the IGBT.
In high-frequency applications, the rise and fall rates of the driving voltage should be faster to increase the IGBT switching rate and reduce losses.
Under normal conditions, the faster the IGBT is turned on, the smaller the loss. However, if there is a reverse recovery current of the freewheeling diode and a discharge current of the absorption capacitor during the turn-on process, the faster the turn-on is, the greater the peak current the IGBT will bear, and the more likely it is to cause damage to the IGBT. At this time, the rising rate of the gate drive voltage should be reduced, that is, the resistance value of the gate series resistor should be increased to suppress the peak value of the current. The cost is a large turn-on loss. Using this technology, the current peak value of the turn-on process can be controlled at any value.
From the above analysis, we can know that the gate series resistance and the internal impedance of the driving circuit have a greater impact on the turn-on process of the IGBT, but a smaller impact on the turn-off process. A small series resistance is beneficial to speed up the turn-off rate and reduce the turn-off loss, but too small will cause excessive di/dt and generate a large collector voltage spike. Therefore, the series resistance should be comprehensively considered according to the specific design requirements.
The gate resistor also affects the waveform of the drive pulse. If the resistance value is too small, it will cause pulse oscillation. If it is too large, the leading and trailing edges of the pulse waveform will be delayed and slowed down. The gate input capacitance Cge of the IGBT increases with the increase of its rated current capacity. In order to maintain the same leading and trailing edge rate of the drive pulse, a larger leading and trailing edge charging current should be provided for IGBT devices with large current capacity. For this reason, the resistance value of the gate series resistor should decrease as the current capacity of the IGBT increases.
IGBT drive circuit
The IGBT drive circuit must have two functions: one is to achieve electrical isolation between the control circuit and the driven IGBT gate; the other is to provide appropriate gate drive pulses. Pulse transformers, differential transformers and photocouplers can be used to achieve electrical isolation.
Figure 3 IGBT drive circuit composed of discrete components
Figure 3 shows an IGBT drive circuit using discrete components such as optocouplers. When a control signal is input, the optocoupler VLC is turned on, the transistor V2 is turned off, and V3 is turned on to output a +15V drive voltage. When the input control signal is zero, VLC is turned off, V2 and V4 are turned on, and a -10V voltage is output. The +15V and -10V power supplies must be close to the drive circuit, and the leads from the output end of the drive circuit and the power ground end to the gate and emitter of the IGBT should be twisted pairs, and the length should preferably not exceed 0.5m.
Figure 4 Driver composed of integrated circuit TLP250
Figure 4 shows a driver composed of the integrated circuit TLP250. The isolation voltage of the built-in optocoupler of TLP250 can reach 2500V, the rise and fall time are both less than 0.5μs, the output current is 0.5A, and it can directly drive IGBTs within 50A/1200V. After adding a push-pull amplifier transistor, it can drive IGBTs with larger current capacity. The driver composed of TLP250 is small in size and cheap in price, and is an ideal choice for IGBT drivers without overcurrent protection. Overcurrent protection of IGBT
The overcurrent protection circuit of IGBT can be divided into two categories: one is low-multiple (1.2~1.5 times) overload protection; the other is high-multiple (up to 8~10 times) short-circuit protection.
For overload protection, it is not necessary to respond quickly. Centralized protection can be used, that is, to detect the total current of the input terminal or DC link. When this current exceeds the set value, the comparator flips, blocking the input pulses of all IGBT drivers and reducing the output current to zero. Once this overload current protection is activated, it must be reset to resume normal operation.
IGBT can withstand short-circuit current for a very short time. The time it can withstand short-circuit current is related to the on-state saturation voltage drop of the IGBT, and it will be extended as the saturation on-state voltage drop increases. For example, the short-circuit time allowed by an IGBT with a saturation voltage drop of less than 2V is less than 5μs, while the short-circuit time allowed by an IGBT with a saturation voltage drop of 3V can reach 15μs, and can reach more than 30μs at 4~5V. The above relationship exists because as the saturation on-state voltage drop decreases, the impedance of the IGBT also decreases, and the short-circuit current increases at the same time. The power consumption during short circuit increases with the square of the current, causing the short circuit time to decrease rapidly.
The commonly used protection measures are soft shutdown and gate voltage reduction. Soft shutdown refers to directly shutting down the IGBT when overcurrent and short circuit occur. However, soft shutdown has poor anti-interference ability. Once an overcurrent signal is detected, it will shut down, which is prone to malfunction. In order to increase the anti-interference ability of the protection circuit, a delay can be added between the fault signal and the start of the protection circuit. However, the fault current will rise sharply during this delay, greatly increasing the power loss and causing the di/dt of the device to increase. Therefore, the protection circuit is often activated, but the device is still broken.
The purpose of reducing the gate voltage is to reduce the gate voltage immediately when an overcurrent is detected in the device, but the device remains on. A fixed delay is set after the gate voltage is reduced, and the fault current is limited to a smaller value during this delay period, which reduces the power consumption of the device during the fault, prolongs the device's short-circuit resistance time, and can reduce the di/dt when the device is turned off, which is very beneficial to device protection. If the fault signal still exists after the delay, the device will be turned off. If the fault signal disappears, the drive circuit can automatically resume normal working state, thereby greatly enhancing the anti-interference ability.
The above-mentioned method of reducing gate voltage only considers the relationship between gate voltage and short-circuit current. In the actual process, the speed of reducing gate voltage is also an important factor, which directly determines the di/dt of the fault current drop. The slow gate voltage reduction technology controls the rate of decrease of the fault current by limiting the speed of reducing gate voltage, thereby suppressing the peak value of dv/dt and uce of the device. Figure 5 shows the specific circuit for realizing slow gate voltage reduction.
Figure 5 Circuit for achieving slow gate voltage drop
During normal operation, due to the conduction of the fault detection diode VD1, the voltage at point a is clamped below the breakdown voltage of the voltage stabilizing diode VZ1, and the transistor VT1 always remains in the off state. V1 is normally turned on and off through the driving resistor Rg. Capacitor C2 provides a very small delay for hard switching applications, so that when V1 is turned on, there is a certain amount of time for uce to drop from the high voltage to the on-state voltage drop without causing the protection circuit to operate.
When the circuit has overcurrent and short circuit faults, the uce on V1 rises, and the voltage at point a rises accordingly. When it reaches a certain value, VZ1 breaks down, VT1 turns on, the voltage at point b drops, and the capacitor C1 is charged through the resistor R1. The capacitor voltage starts to rise from zero. When the capacitor voltage rises to about 1.4V, the transistor VT2 turns on, and the gate voltage uge drops as the capacitor voltage rises. By adjusting the value of C1, the charging speed of the capacitor can be controlled, and then the drop speed of uge can be controlled; when the capacitor voltage rises to the breakdown voltage of the voltage-stabilizing diode VZ2, VZ2 breaks down, uge is clamped at a fixed value, and the process of slowly reducing the gate voltage ends. At the same time, the drive circuit outputs an overcurrent signal through the optocoupler. If the fault signal disappears during the delay process, the voltage at point a decreases, VT1 resumes cutoff, C1 discharges through R2, the voltage at point d increases, VT2 also resumes cutoff, uge rises, and the circuit resumes normal working state.
Overvoltage during IGBT switching
When the IGBT is turned off, its collector current has a high rate of decrease, especially in the case of a short-circuit fault. If no soft-off measures are taken, its critical current decrease rate will reach several kA/μs. The extremely high current decrease rate will induce a high overvoltage on the distributed inductance of the main circuit, causing the current and voltage running trajectory of the IGBT to exceed its safe operating area and be damaged when it is turned off. Therefore, from the perspective of shutdown, it is hoped that the inductance and current decrease rate of the main circuit are as small as possible. However, for the opening of the IGBT, the inductance of the collector circuit is conducive to suppressing the reverse recovery current of the freewheeling diode and the peak current caused by the charging and discharging of the capacitor, which can reduce the opening loss and withstand a higher opening current rise rate. In general, the collector of the IGBT switching circuit does not need a series inductor, and its opening loss can be controlled by improving the gate drive conditions.
IGBT turn-off snubber circuit
In order to effectively suppress the IGBT turn-off overvoltage and reduce the turn-off loss, it is usually necessary to set a turn-off buffer absorption circuit for the IGBT main circuit. The IGBT turn-off buffer absorption circuit is divided into a charge-discharge type and a discharge prevention type.
(a) RC type (b) RCD type
Figure 6 Charge and discharge type IGBT snubber circuit
There are two types of charge and discharge types: RC absorption and RCD absorption. As shown in Figure 6. The RC absorption circuit generates a voltage drop on the resistor R due to the charging current of the capacitor C, which also causes an overshoot voltage. The RCD circuit bypasses the charging current on the resistor with a diode, thus overcoming the overshoot voltage.
(a) LC type (b) RLCD type (c) RLCD type
Figure 7 Three types of discharge-blocking absorption circuits
Figure 7 shows three types of discharge-blocking type absorption circuits. The discharge voltage of the absorption capacitor Cs in the discharge-blocking type snubber circuit is the power supply voltage. Before each shutdown, Cs only feeds back the overshoot energy of the last shutdown voltage to the power supply, reducing the power consumption of the absorption circuit. Because the capacitor voltage starts to rise from the power supply voltage when the IGBT is turned off, its overvoltage absorption capacity is not as good as that of the RCD type charge-discharge type. In terms of the ability to absorb overvoltage, the discharge-blocking type has a slightly worse absorption effect, but the energy loss is smaller.
The requirements for the buffer absorption circuit are:
1) Try to reduce the wiring inductance La of the main circuit;
2) The absorption capacitor should use a low-inductance absorption capacitor, and its lead should be as short as possible, preferably directly connected to the terminal of the IGBT;
3) The absorption diode should be a fast turn-on and fast soft recovery diode to avoid the generation of turn-on overvoltage and reverse recovery causing large oscillation overvoltage.
Conclusion
This article analyzes the driving and protection technology of IGBT in detail and draws several points that should be paid attention to during design:
1. Due to the Miller effect of collector-gate parasitic capacitance, IGBT can cause unexpected voltage spike damage, so the impedance of the gate circuit should be low enough during design to minimize its negative impact.
2. The gate series resistance and the internal impedance of the driving circuit have a great influence on the IGBT turn-on process and the waveform of the driving pulse. Therefore, they should be considered comprehensively during design.
3. Slow gate voltage drop technology should be used to control the rate of decrease of fault current, thereby suppressing the peak value of dv/dt and uce of the device to achieve the purpose of short circuit protection.
4. When the working current is large, in order to reduce the shutdown overvoltage, the wiring inductance of the main circuit should be reduced as much as possible, and the absorption capacitor should use a low-inductance type.
Previous article:Engineers recommend a nine-speed adjustable DC power supply circuit design implementation
Next article:The H-bridge transformer driver converts the 3.3V input into a 12V isolated output power supply
Recommended ReadingLatest update time:2024-11-16 14:41
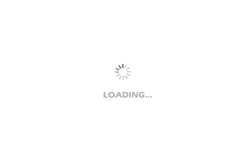
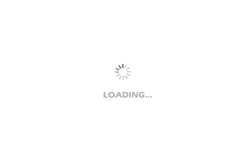
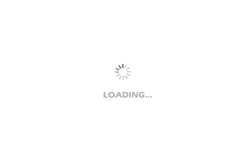
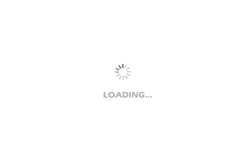
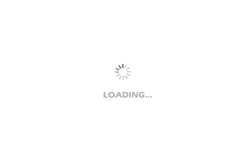
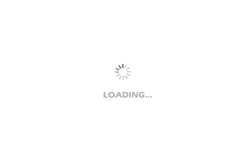
- Popular Resources
- Popular amplifiers
- MathWorks and NXP Collaborate to Launch Model-Based Design Toolbox for Battery Management Systems
- STMicroelectronics' advanced galvanically isolated gate driver STGAP3S provides flexible protection for IGBTs and SiC MOSFETs
- New diaphragm-free solid-state lithium battery technology is launched: the distance between the positive and negative electrodes is less than 0.000001 meters
- [“Source” Observe the Autumn Series] Application and testing of the next generation of semiconductor gallium oxide device photodetectors
- 采用自主设计封装,绝缘电阻显著提高!ROHM开发出更高电压xEV系统的SiC肖特基势垒二极管
- Will GaN replace SiC? PI's disruptive 1700V InnoMux2 is here to demonstrate
- From Isolation to the Third and a Half Generation: Understanding Naxinwei's Gate Driver IC in One Article
- The appeal of 48 V technology: importance, benefits and key factors in system-level applications
- Important breakthrough in recycling of used lithium-ion batteries
- Innolux's intelligent steer-by-wire solution makes cars smarter and safer
- 8051 MCU - Parity Check
- How to efficiently balance the sensitivity of tactile sensing interfaces
- What should I do if the servo motor shakes? What causes the servo motor to shake quickly?
- 【Brushless Motor】Analysis of three-phase BLDC motor and sharing of two popular development boards
- Midea Industrial Technology's subsidiaries Clou Electronics and Hekang New Energy jointly appeared at the Munich Battery Energy Storage Exhibition and Solar Energy Exhibition
- Guoxin Sichen | Application of ferroelectric memory PB85RS2MC in power battery management, with a capacity of 2M
- Analysis of common faults of frequency converter
- In a head-on competition with Qualcomm, what kind of cockpit products has Intel come up with?
- Dalian Rongke's all-vanadium liquid flow battery energy storage equipment industrialization project has entered the sprint stage before production
- Allegro MicroSystems Introduces Advanced Magnetic and Inductive Position Sensing Solutions at Electronica 2024
- Car key in the left hand, liveness detection radar in the right hand, UWB is imperative for cars!
- After a decade of rapid development, domestic CIS has entered the market
- Aegis Dagger Battery + Thor EM-i Super Hybrid, Geely New Energy has thrown out two "king bombs"
- A brief discussion on functional safety - fault, error, and failure
- In the smart car 2.0 cycle, these core industry chains are facing major opportunities!
- The United States and Japan are developing new batteries. CATL faces challenges? How should China's new energy battery industry respond?
- Murata launches high-precision 6-axis inertial sensor for automobiles
- Ford patents pre-charge alarm to help save costs and respond to emergencies
- New real-time microcontroller system from Texas Instruments enables smarter processing in automotive and industrial applications
- Is it useful for people who work with microcontrollers to read "Introduction to Algorithms" and "Data Structures"?
- Design of electronic piano based on LPC2000 series ARM chip
- How do analog switches ensure bandwidth without distortion?
- How to use a multimeter from entry level to mastery
- Looking for lmk04826B5 routine
- PCB panelization methods and precautions
- mpy adds math.isclose() function
- Low power mode of msp430f149
- Android's past and present
- How should the DC component in the signal be extracted?