Should T8 LED lamps be subjected to a withstand voltage test before they are aged after manufacturing? Some manufacturers skip this step and ship them directly after aging. Why? The answer is that the withstand voltage test will kill the lamp beads. Expanding the concept, a considerable number of people in the entire LED industry believe that the withstand voltage test will kill the lamp beads. Therefore, a considerable number of lamps on the market have not undergone the withstand voltage test, and there are certain hidden dangers in their use safety. Most of these lamps cannot pass export inspections or CE tests, and the product quality has dropped a level. There is another problem: lamps assembled with a 3.75KV withstand voltage driver power supply cannot even pass 3KV when subjected to withstand voltage. What is going on? This article attempts to talk about my personal views through analysis.
The following is an analysis of the mechanism of T8 voltage withstand test dead lamp beads.
There are two reasons for LED damage. One is voltage overshoot, and the other is current overshoot. The leakage current of the withstand voltage test is set at about 10mA, which generally does not exceed the current value allowed by the LED. The most likely cause of LED damage is voltage overshoot.
How did the voltage exceed the limit?
The lamp is composed of three parts: the driver power supply, LED and heat sink. The withstand voltage test is generally to test the withstand voltage between the driver power input terminal and the lamp housing that can be touched by the human body. Withstand voltage is achieved by insulation. The insulation from the input terminal to the housing consists of two parts, one is the insulation between the primary and secondary of the power supply (except for non-isolated power supplies), and the other is the insulation between the lamp bead and the heat sink (generally integrated with the housing). AC-powered lamps are tested for withstand voltage with AC high voltage. See the figure below.
In the figure, CY is the Y capacitor of the driving power supply, and CY1 and CY2 are the partial capacitors between the positive and negative copper foils of the aluminum substrate and the aluminum plate. The high voltage during the withstand voltage test is directly applied between CY and CY1/CY2. The equivalent figure is shown below.
Assume that the applied AC high voltage is VC, the voltage distributed on the Y capacitor of the power supply is VCY, and the voltage distributed on the distributed capacitance of the aluminum substrate is VCY1/2, then VC=VCY+VCY1/2. We know that the capacitive reactance Xc=1/(2πfC). The larger the capacitance, the smaller the capacitive reactance, and the smaller the voltage distributed in the series circuit, and the opposite is also true. In this example, the Y capacitance of the power supply is a constant value, between 1000p and 2200P. Assuming that the distributed capacitance value of the aluminum substrate is equal to the Y capacitance value of the power supply, the voltage distributed on the aluminum substrate is equal to the power distributed on the Y capacitor of the power supply, both of which are 1/2 VC. If CY1/2 is less than CY, then VCY1/2 will be greater than VCY, that is, the voltage applied to the aluminum substrate is higher than half of the high voltage value of the withstand voltage test. The smaller the distributed capacitance, the higher this voltage. This is one of them. Secondly, the copper foil of the aluminum substrate has positive and negative electrodes. These two copper foils are not connected together. The light-emitting diodes after series and parallel connection are connected between these two electrodes, and the distributed capacitance of the two copper foils is discrete. The different shapes of the copper foils make the distributed capacitance different, and the high voltages distributed are also different. If the voltage of the negative electrode is higher than that of the positive electrode, the secondary transformer winding and the rectifier tube of the power supply are turned on, and the voltage is forcibly pulled to the positive electrode voltage. This situation will not cause the LED to die due to overvoltage. If the positive electrode voltage is higher than the negative electrode voltage, then there will be current (this current is different from the leakage current) flowing through the LED, which is why the LED will flash during the withstand voltage test. The higher this voltage, the brighter the LED. When it is larger than the LED withstand voltage to a certain extent, the PN junction of the LED will be damaged. Another situation where the positive electrode voltage is higher than the negative electrode voltage is that the negative electrode is broken down and is at zero potential. At this time, as long as the positive electrode is distributed with an extremely low voltage, it is enough to cause the LED to be damaged. Therefore, the main reason for the damage of the LED is that the voltage difference between the positive and negative electrodes is too large, and this voltage difference is determined by the shape and position of the positive and negative copper foils on the aluminum substrate. Next, let’s take a look at the aluminum substrate.
Aluminum substrate is a metal-based copper-clad laminate with good heat dissipation function. Generally, a single-sided board consists of a three-layer structure, namely a circuit layer (copper foil), an insulating layer and a metal base layer.
Two parallel metal plates plus the dielectric in the middle form a capacitor. The larger the area of the plate and the smaller the distance between the plates, the larger the capacity. The insulating layer in the middle of the aluminum substrate is equivalent to the capacitor dielectric, and its thickness cannot be changed after the product is finished. The withstand voltage value of the insulating layer is about 2.5KV, which is commonly used, and 4KV, which is a higher level. After selecting the aluminum substrate according to the cost performance, it is necessary to comprehensively consider the matching design according to its performance. Generally speaking, if the withstand voltage value of the driving power supply is large enough (such as greater than 3KV), most of the high voltage value can be added to the power supply to make the high voltage that the aluminum substrate bears lower. The realization of this goal is to increase the copper foil area of the aluminum substrate to make the distributed capacitance as large as possible. The specific requirement is to make the total area of the positive copper foil as large as possible than the negative pole, and at the same time ensure sufficient creepage distance. Generally, for a 2.5KV aluminum substrate, the creepage distance of the entire board cannot be less than 2.5MM. This can ensure that there is no weak link in the aluminum substrate and it will not break down when the voltage is high. The picture below is a picture of the aluminum substrate of a mass-produced T8 LED lamp tube. With an isolated power supply with a withstand voltage of 3.75KV and a 5kv input line, the withstand voltage of the entire lamp reaches 4KV. The entire production process is tested to withstand a voltage of 1.5KV, and the lamp beads are almost never dead.
From the above analysis, it can be seen that if a small capacitor is added between the positive electrode of the aluminum substrate and the aluminum plate (shell), the dead lamp phenomenon of the LED can be significantly improved.
Summary: This article discusses the main reasons for the damage of the lamp beads of T8 LED lamps assembled with isolated power supply during the withstand voltage test: 1. The voltage difference between the positive and negative electrodes of the aluminum substrate is large, exceeding the withstand voltage value of the LED; 2. The negative electrode of the aluminum substrate has a weak link and breaks down to zero potential, and the positive electrode is connected to high voltage, causing damage to the LED. The countermeasures are: 1. Select a high-voltage drive power supply; 2. The copper foil of the aluminum substrate should be as large as possible, and the positive electrode should be larger than the negative electrode; 3. Control the minimum creepage distance of the copper foil to the aluminum plate: 2.5KV is not less than 2.5MM. 4. Do not miss any weak links, such as the input line (it is best to use wire with a withstand voltage of more than 5KV), the exposed metal parts of the plug and socket on the aluminum substrate, etc.
For non-isolated power supplies, all high voltages are applied to the aluminum substrate. The description of the positive and negative electrodes of the aluminum substrate in this article also applies.
Previous article:Seven tips for LED driver power design
Next article:Apple iPhone 5S dual LED flash photos
Recommended ReadingLatest update time:2024-11-17 01:52
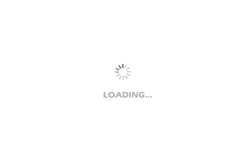
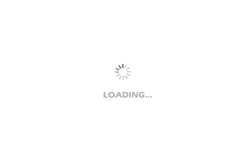
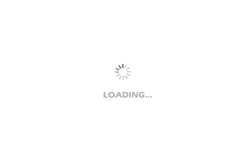
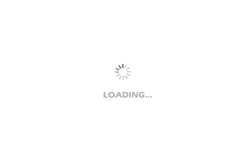
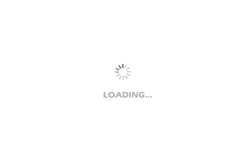
- MathWorks and NXP Collaborate to Launch Model-Based Design Toolbox for Battery Management Systems
- STMicroelectronics' advanced galvanically isolated gate driver STGAP3S provides flexible protection for IGBTs and SiC MOSFETs
- New diaphragm-free solid-state lithium battery technology is launched: the distance between the positive and negative electrodes is less than 0.000001 meters
- [“Source” Observe the Autumn Series] Application and testing of the next generation of semiconductor gallium oxide device photodetectors
- 采用自主设计封装,绝缘电阻显著提高!ROHM开发出更高电压xEV系统的SiC肖特基势垒二极管
- Will GaN replace SiC? PI's disruptive 1700V InnoMux2 is here to demonstrate
- From Isolation to the Third and a Half Generation: Understanding Naxinwei's Gate Driver IC in One Article
- The appeal of 48 V technology: importance, benefits and key factors in system-level applications
- Important breakthrough in recycling of used lithium-ion batteries
- Innolux's intelligent steer-by-wire solution makes cars smarter and safer
- 8051 MCU - Parity Check
- How to efficiently balance the sensitivity of tactile sensing interfaces
- What should I do if the servo motor shakes? What causes the servo motor to shake quickly?
- 【Brushless Motor】Analysis of three-phase BLDC motor and sharing of two popular development boards
- Midea Industrial Technology's subsidiaries Clou Electronics and Hekang New Energy jointly appeared at the Munich Battery Energy Storage Exhibition and Solar Energy Exhibition
- Guoxin Sichen | Application of ferroelectric memory PB85RS2MC in power battery management, with a capacity of 2M
- Analysis of common faults of frequency converter
- In a head-on competition with Qualcomm, what kind of cockpit products has Intel come up with?
- Dalian Rongke's all-vanadium liquid flow battery energy storage equipment industrialization project has entered the sprint stage before production
- Allegro MicroSystems Introduces Advanced Magnetic and Inductive Position Sensing Solutions at Electronica 2024
- Car key in the left hand, liveness detection radar in the right hand, UWB is imperative for cars!
- After a decade of rapid development, domestic CIS has entered the market
- Aegis Dagger Battery + Thor EM-i Super Hybrid, Geely New Energy has thrown out two "king bombs"
- A brief discussion on functional safety - fault, error, and failure
- In the smart car 2.0 cycle, these core industry chains are facing major opportunities!
- Rambus Launches Industry's First HBM 4 Controller IP: What Are the Technical Details Behind It?
- The United States and Japan are developing new batteries. CATL faces challenges? How should China's new energy battery industry respond?
- Murata launches high-precision 6-axis inertial sensor for automobiles
- Ford patents pre-charge alarm to help save costs and respond to emergencies
- Sell some IC chips
- stm32cubemx always fails to install the packages of various mcu
- [GD32L233C-START review] + DHT11 sensor usage [2]
- DIY an I2C level conversion board
- I hope this book "PCB Design Secrets" will be passed on to you!
- [National Technology Low Power Series N32L43x Evaluation] 3. Key Driver + SPI_LCD Screen Driver
- A comic book about CircuitPython and Mu
- Is there any ADR3433 chip that can be replaced by PINTOPIN?
- MSP430 Remote Upgrade Solution
- Calculate the frequency of the sinusoidal signal collected by msp430