The load characteristics of LEDs themselves greatly affect the reliability of using a switching power supply to drive them. The load characteristics of LEDs, namely the volt-ampere characteristics, are diode characteristics. Within a certain range, the increase in voltage across the LEDs causes the current to grow exponentially and explosively. Therefore, many LED lamps driven by switching power supplies show many unstable characteristics. The reason is that the output of the switching power supply is not a very clean and smooth DC voltage (current) energy, but a very complex energy signal, which can be roughly regarded as stable.
LEDs are very sensitive to voltage changes. When LEDs work under a stable current, the voltage across them is generally between 3.0 and 3.6V (there are slight differences between high and low power LEDs). When the voltage across them fluctuates slightly, the current across them will change dramatically, and the output power of the power supply will also change dramatically. If the grid voltage suddenly increases, a small output voltage change will create a large output current increase, and the power will increase dramatically, causing accidents.
Practice has proved that adding various voltage suppression components, such as TVR and TVS, to the circuit does not have a very obvious effect. It will still be damaged when it should be damaged. The reliability of LED driver power supply is always not as good as other power supplies. This is an objective fact. Although many people say that there is no problem with the LED power supply they make, it is actually just a pale self-consolation because it does not solve the fundamental problem.
Reliability and efficiency are mutually constrained. A high-efficiency power supply will inevitably reduce reliability. To improve reliability, power efficiency must be sacrificed. Because in order to reduce the impact of input voltage on output voltage, electrical energy must undergo multiple layers of conversion. To give a simple example, the reliability of the BUCK circuit is usually not very high, but the reliability of the BUCK-BOOST circuit is better than that of the BUCK, which has been verified in practice. Because people who understand the principle of power supply know that when the switch tube of the BUCK circuit is turned on, the LED load and the inductor are connected in series in the 300V high voltage. At this time, the LED is directly powered by 300V, while the BUCK-BOOST circuit stores energy for the inductor alone. During the shutdown period, the BUCK circuit is the inductor that continues to flow to the load, while the BUCK-BOOST circuit is when the inductor is turned off, and the energy is transferred to the LED load. The difference between the two is that the BUCK circuit is directly powered by 300V for a period of time, while the latter first stores energy in the inductor and then transfers it from the inductor to the LED load. Therefore, the latter has high reliability because it has a long transfer path. The longer the transmission path, the lower the efficiency. Generally, the efficiency of the BUCK-BOOST circuit is 2-5 percentage points lower than that of the BUCK circuit.
Therefore, the current LED driver power supply generally has better reliability of isolation than non-isolation, and lower voltage reliability than high voltage. It is all subject to the constraints of this law, that is, improving efficiency means sacrificing reliability, and improving reliability means reducing efficiency.
In fact, all the problems are caused by the load characteristics of the LED. The fundamental method is to improve the load characteristics of the LED light string, but the method of improving the load characteristics is still to sacrifice efficiency. The simplest way to improve the load characteristics is to add a resistor in series to the LED light string. The larger the resistor string, the more stable the load characteristics. Of course, this will reduce efficiency. Another good way is to add a linear constant voltage device and use a transistor as an adjustment tube. The transistor is equivalent to a variable resistor. In this case, the reliability should be higher (I have come to this conclusion in theory, but I have no practical experience yet). Therefore, it can be basically concluded that the most reliable LED driving method is actually: ordinary constant voltage power supply plus linear constant current device. Of course, the efficiency will not be too high. Once the efficiency is high, the reliability will decrease.
Previous article:256-level grayscale display - FPGA-based OLED true color display design
Next article:Application of digital power technology in LED lighting
Recommended ReadingLatest update time:2024-11-17 03:57
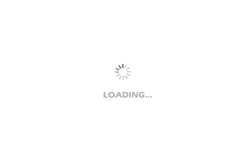
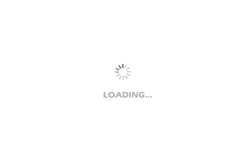
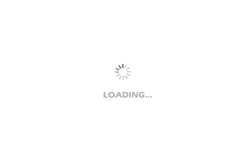
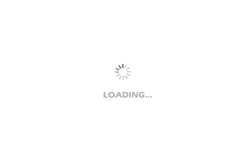
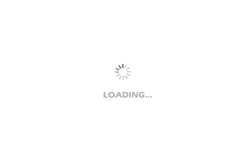
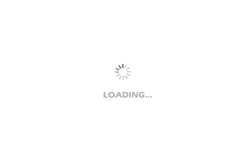
- Popular Resources
- Popular amplifiers
- MathWorks and NXP Collaborate to Launch Model-Based Design Toolbox for Battery Management Systems
- STMicroelectronics' advanced galvanically isolated gate driver STGAP3S provides flexible protection for IGBTs and SiC MOSFETs
- New diaphragm-free solid-state lithium battery technology is launched: the distance between the positive and negative electrodes is less than 0.000001 meters
- [“Source” Observe the Autumn Series] Application and testing of the next generation of semiconductor gallium oxide device photodetectors
- 采用自主设计封装,绝缘电阻显著提高!ROHM开发出更高电压xEV系统的SiC肖特基势垒二极管
- Will GaN replace SiC? PI's disruptive 1700V InnoMux2 is here to demonstrate
- From Isolation to the Third and a Half Generation: Understanding Naxinwei's Gate Driver IC in One Article
- The appeal of 48 V technology: importance, benefits and key factors in system-level applications
- Important breakthrough in recycling of used lithium-ion batteries
- Innolux's intelligent steer-by-wire solution makes cars smarter and safer
- 8051 MCU - Parity Check
- How to efficiently balance the sensitivity of tactile sensing interfaces
- What should I do if the servo motor shakes? What causes the servo motor to shake quickly?
- 【Brushless Motor】Analysis of three-phase BLDC motor and sharing of two popular development boards
- Midea Industrial Technology's subsidiaries Clou Electronics and Hekang New Energy jointly appeared at the Munich Battery Energy Storage Exhibition and Solar Energy Exhibition
- Guoxin Sichen | Application of ferroelectric memory PB85RS2MC in power battery management, with a capacity of 2M
- Analysis of common faults of frequency converter
- In a head-on competition with Qualcomm, what kind of cockpit products has Intel come up with?
- Dalian Rongke's all-vanadium liquid flow battery energy storage equipment industrialization project has entered the sprint stage before production
- Allegro MicroSystems Introduces Advanced Magnetic and Inductive Position Sensing Solutions at Electronica 2024
- Car key in the left hand, liveness detection radar in the right hand, UWB is imperative for cars!
- After a decade of rapid development, domestic CIS has entered the market
- Aegis Dagger Battery + Thor EM-i Super Hybrid, Geely New Energy has thrown out two "king bombs"
- A brief discussion on functional safety - fault, error, and failure
- In the smart car 2.0 cycle, these core industry chains are facing major opportunities!
- Rambus Launches Industry's First HBM 4 Controller IP: What Are the Technical Details Behind It?
- The United States and Japan are developing new batteries. CATL faces challenges? How should China's new energy battery industry respond?
- Murata launches high-precision 6-axis inertial sensor for automobiles
- Ford patents pre-charge alarm to help save costs and respond to emergencies
- Getting Started with CircuitPython for the Raspberry Pi Pico
- Switching Power Supply Interest Group Task 06
- AT32F4xx Standard Library BSP&Pack Application Guide
- Use of resolver decoding chip AD2S1200
- GaN goes mobile?
- Is there any MEMS or sensor expert?
- Leakage current and withstand voltage test of low voltage battery products
- i.MX6ULL Embedded Linux Development 1-Preliminary Study on Uboot Transplantation
- 【Synopsys IP Resources】 Comprehensive IP Solutions to Help HPC Chip Development
- GPIO Features of TMS320C6748