The biggest advantage of LED technology is that it can produce pure color light with an extremely narrow spectrum in the form of electromagnetic radiation, with high efficiency and no heat radiation. It is good if the color produced is exactly the desired color, but in general lighting applications, what we really want is "white" light. In other words, we need to mix multiple colors in precise proportions, similar to the spectrum of sunlight when it reaches the human eye after being filtered through the earth's atmosphere.
Although white light is obtained from LED sources by coating a layer of phosphorous material on top of a blue or UV emitter, similar to fluorescent lamps, the actual composition of the phosphorous material and its thickness and coating location are still widely discussed by all major LED manufacturers, and this is reflected in the manufacturers announcing new and more efficient research results every month. Moreover, the quality of the light produced is also constantly improving, and the quality perceived by the human eye is actually measured by measuring the correlated color temperature, which is the black body temperature (CCT) that is very close to the perceived color of the lamp. This is a very important issue because the light produced by early fluorescent lamps was somewhat harsh, which led to the "cold reception" of early compact fluorescent lamps.
Another way to get white light from an LED is to precisely mix the red, green, and blue (RGB) light from three color emitters in the correct proportions, which not only produces white light, but also the desired correlated color temperature. Figure 1 shows a simple application circuit that uses an 8-bit microcontroller in an eight-pin package to control a three-color LED. By controlling the relative brightness of the three emitters through simple software techniques, each emitter can achieve approximately 6 bits of resolution (providing sixty-four brightness levels), which is sufficient for precise control of the color output (white light) and selection of the desired CCT.
The PIC12HV615 Flash microcontroller in the figure integrates a shunt regulator, an oscillator providing an 8MHz clock, a reset circuit, and an analog-to-digital converter to provide a complete and flexible single-chip solution. The in-circuit programmable function of this Flash component also allows the color calibration process to be performed during production, providing a method to compensate for performance differences between various light emitters and differences between components.
LEDs have a long service life but are prone to color drift
The solution in Figure 1 has many applications, such as in automotive dashboard lighting where the color output of each module is required to match the color of the adjacent modules. Increasingly, so-called mood lighting applications are emerging, but of course, there are some obvious drawbacks.
Figure 1. Example of a simple white light LED system
First, this solution is less efficient because it is a linear solution and some power is dissipated in the current limiting resistor in series with each emitter. Further problems can arise over the life of the application.
Indeed, one of the main advantages of LED technology is its extremely long operating life, but this also leads to the problem of chromaticity drift. After 50,000 hours of operation or more, the light output of LEDs gradually decreases to 70% of their nominal value. Compared to incandescent bulbs that suddenly fail after 1,500 hours of use, their service life is indeed very long. Unfortunately, during these 50,000 hours, the CCT of white LEDs will change, warming up and moving closer to blue as the phosphor ages. Even RGB LED solutions have similar problems, with CCT chromaticity drift as the three color emitters slowly age at different rates and according to different curves.
By using the intelligence of the microcontroller, a variety of techniques can be designed to compensate for the aging of components using predictive algorithms or by implementing a closed loop control system. Many manufacturers use components that are sensitive to the color of the light, which can solve the color drift problem at once when used with a simple PID algorithm, of course, this will increase the cost of the solution. Because the changes are extremely slow over thousands of hours, high computing performance is not required, and even the lowest cost 8-bit microcontroller can be used to implement this control mechanism. This mechanism can not only compensate for the aging of the LED, but also the aging of the driver circuit, which is very important for such a long application life.
Temperature management is a challenge for lighting applications
Another challenge for general lighting applications is temperature management. As mentioned above, high-power LEDs do not consume excess energy when they generate electromagnetic radiation within a narrow spectrum range (in the visible spectrum), but they still generate heat as a byproduct. The difference from light sources such as incandescent bulbs is that this heat can only be transferred by direct contact (conduction) rather than radiation. In order to be compatible with incandescent bulb lighting systems, some important restrictions are imposed on the design of general lighting systems such as supporting equipment. In other words, a lighting system designed for an incandescent bulb of a given rated power is difficult to adapt to an LED lamp of the same power because the heat conduction path may be very limited. High thermal resistance paths can cause the LED emitter to overheat quickly, destroying the phosphor-containing material (for white LEDs) and quickly damaging the LED junction.
Power Conversion/Control for LED Focus
All the focus of LED is on obtaining the maximum luminous efficiency (lm/W), so the efficiency of the drive/control circuit must also be given equal attention. LED is a relatively low-voltage component (Vf ~ 3-4 volts), which is completely incompatible with the high voltage 110-220 volts provided by the mains. In addition, in order to operate at the best efficiency level and maintain constant light output, the current of the LED needs to be precisely controlled. Only switching power supplies can provide the high efficiency required for this conversion.
Using multiple constant current drive topologies to perform the required power conversion, isolation, power factor correction and/or simply improving existing solutions may require the use of two-stage processing. The input voltage is first reduced to an intermediate voltage, where traditional techniques are used to meet power factor correction (PFC) and high voltage isolation requirements, while the second stage is responsible for meeting LED current and temperature control requirements. Figure 2 shows a smart LED solution that uses a boost converter MCP1630 in a constant current configuration. A small 8-bit microcontroller provides a flexible clock source, programmable current set point (to make the drive circuit meet different LED module specifications) for further power saving dimming functions, and also provides closed-loop temperature control using a remote temperature sensor (integrated temperature sensor such as MCP9700 or thermistor).
Figure 2 Schematic diagram of smart LED solution
Like many switching power supply controllers, the MCP1630 already provides an over-temperature detection function. However, due to the large difference between the temperature of the drive circuit and the temperature of the actual LED module, the over-temperature detection function of the MCP1630 and the closed-loop temperature control function can complement each other. The microcontroller-based intelligent solution can provide great flexibility, and the power output to the LED module is gradually reduced as its temperature approaches the critical threshold until a balance is reached, rather than suddenly shutting down the system or just sounding an alarm. This function is very important for component manufacturers, especially when LED lamps are designed and commercially operated independently of the lighting system and the system temperature design cannot be guaranteed to be correct.
Perhaps the biggest advantage of using an intelligent drive design, that is, using a small microcontroller to monitor the LED drive circuit, is that adding more intelligence and functionality to the solution only requires adding a few lines of program code. The communication interface is easy to implement using the microcontroller's built-in serial communication interface to implement simple digital protocols such as DMX-512 or DALI. Ethernet can be used for more advanced system integration, or ZigBee protocol can be used for wireless communication.
And, after connecting each lighting point, a new energy management system can be designed to further improve the efficiency of the entire home or office building system through energy-saving strategies and a more holistic approach.
In general, if new solid-state lighting, especially power LED solutions, are to make an impact and realize their potential in general lighting, it is best to have smart solutions - small-scale intelligence implemented by inexpensive microcontrollers, which can be added to lighting solutions to remove many of the obstacles that have hindered the introduction of previous technologies. Smart solutions can help calibrate color, dim light, manage heat and communicate, making solid-state lighting a cost-effective alternative in general lighting today that is consistent with the energy-efficient concept.
Previous article:Buy an LED Driver or Design Your Own
Next article:Misunderstandings to Avoid When Purchasing High-Power LED Lamps
Recommended ReadingLatest update time:2024-11-16 16:53
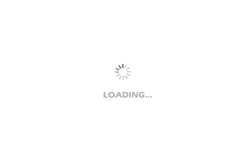
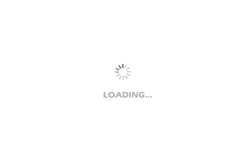
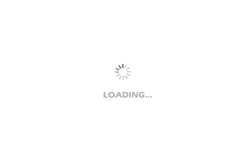
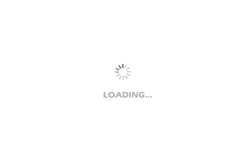
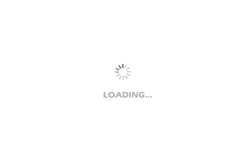
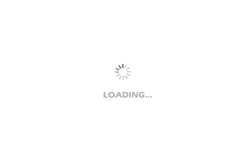
- Popular Resources
- Popular amplifiers
- MathWorks and NXP Collaborate to Launch Model-Based Design Toolbox for Battery Management Systems
- STMicroelectronics' advanced galvanically isolated gate driver STGAP3S provides flexible protection for IGBTs and SiC MOSFETs
- New diaphragm-free solid-state lithium battery technology is launched: the distance between the positive and negative electrodes is less than 0.000001 meters
- [“Source” Observe the Autumn Series] Application and testing of the next generation of semiconductor gallium oxide device photodetectors
- 采用自主设计封装,绝缘电阻显著提高!ROHM开发出更高电压xEV系统的SiC肖特基势垒二极管
- Will GaN replace SiC? PI's disruptive 1700V InnoMux2 is here to demonstrate
- From Isolation to the Third and a Half Generation: Understanding Naxinwei's Gate Driver IC in One Article
- The appeal of 48 V technology: importance, benefits and key factors in system-level applications
- Important breakthrough in recycling of used lithium-ion batteries
- Innolux's intelligent steer-by-wire solution makes cars smarter and safer
- 8051 MCU - Parity Check
- How to efficiently balance the sensitivity of tactile sensing interfaces
- What should I do if the servo motor shakes? What causes the servo motor to shake quickly?
- 【Brushless Motor】Analysis of three-phase BLDC motor and sharing of two popular development boards
- Midea Industrial Technology's subsidiaries Clou Electronics and Hekang New Energy jointly appeared at the Munich Battery Energy Storage Exhibition and Solar Energy Exhibition
- Guoxin Sichen | Application of ferroelectric memory PB85RS2MC in power battery management, with a capacity of 2M
- Analysis of common faults of frequency converter
- In a head-on competition with Qualcomm, what kind of cockpit products has Intel come up with?
- Dalian Rongke's all-vanadium liquid flow battery energy storage equipment industrialization project has entered the sprint stage before production
- Allegro MicroSystems Introduces Advanced Magnetic and Inductive Position Sensing Solutions at Electronica 2024
- Car key in the left hand, liveness detection radar in the right hand, UWB is imperative for cars!
- After a decade of rapid development, domestic CIS has entered the market
- Aegis Dagger Battery + Thor EM-i Super Hybrid, Geely New Energy has thrown out two "king bombs"
- A brief discussion on functional safety - fault, error, and failure
- In the smart car 2.0 cycle, these core industry chains are facing major opportunities!
- The United States and Japan are developing new batteries. CATL faces challenges? How should China's new energy battery industry respond?
- Murata launches high-precision 6-axis inertial sensor for automobiles
- Ford patents pre-charge alarm to help save costs and respond to emergencies
- New real-time microcontroller system from Texas Instruments enables smarter processing in automotive and industrial applications
- Has anyone used a PIC microcontroller to play songs with a buzzer? Please share, thank you
- Comment and download the information, participate in the lucky draw, and let us take the first step in technical exchange and sharing! !
- "Power Amplifier Experiment Case" Application of Power Amplifier in Capacitive Coupling Wireless Power Transfer System
- PCB design principles of high frequency wiring
- Dry cell boost 3V, dry cell boost 3.3V chip output current test, maximum 500MA
- Its predecessor is Fairchild's motor product line. Come to the forum solo. Do you want to catch it for testing?
- [CH563L Review] Part 2 Based on uCos, using FIFO algorithm to implement UART queue
- [National Technology N32 MCU Development Package] --N32G032 Series
- [STM32WB55 Review] + Registers can be avoided, but RTOS cannot be avoided
- EEWORLD University ---- Linux Embedded Development